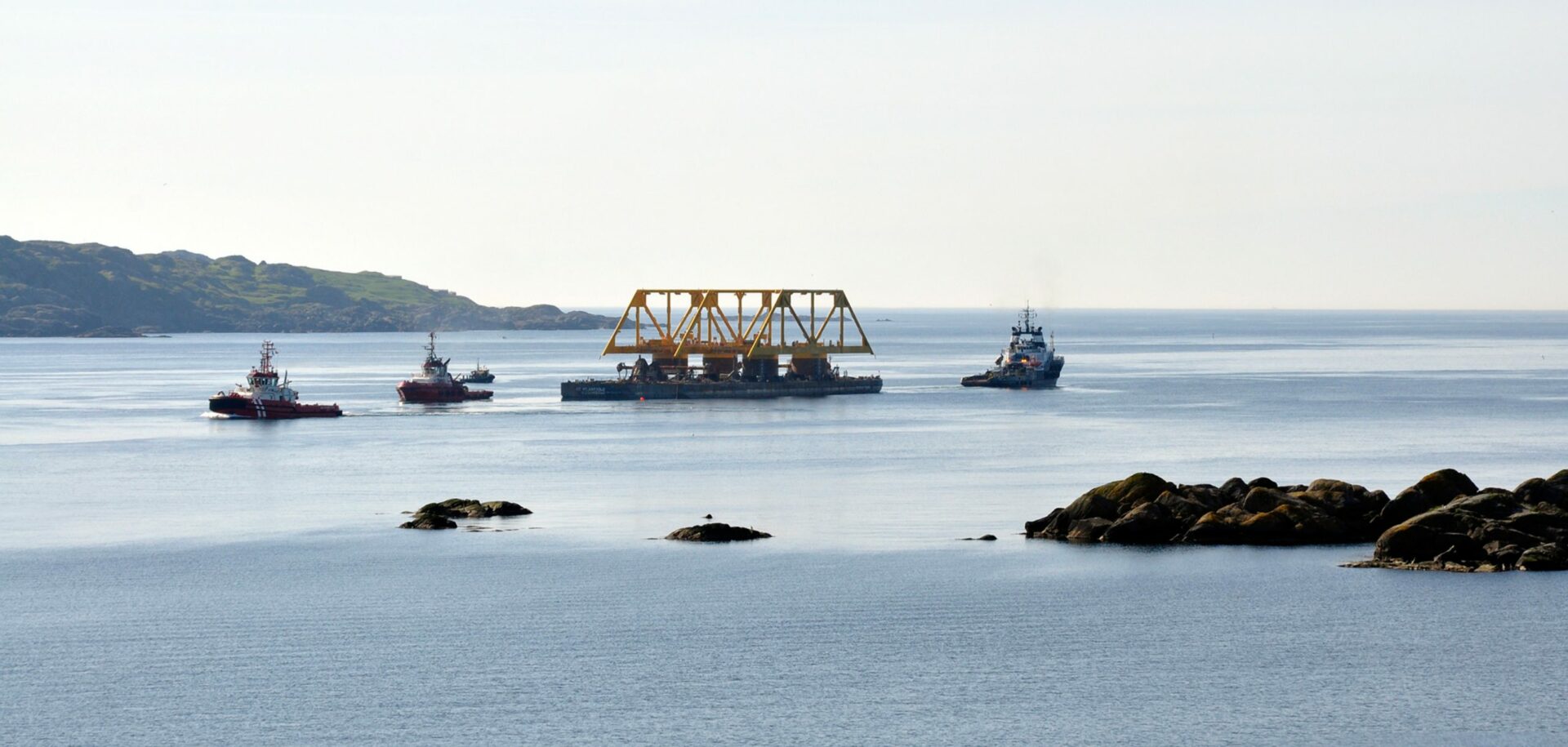
Soluzione profondamente innovativa
I primi impianti di compressione sottomarina del gas aiutano la Statoil a migliorare il tasso di recupero, i costi e l’impatto ambientale, sfruttando al massimo il giacimento.
Fatti
A 300 metri di profondità
Nel settembre 2015 la società energetica internazionale Statoil ha messo in funzione il primo treno di compressione sottomarino del mondo nel giacimento di Åsgard, nel Mare di Norvegia. Attualmente ne è in produzione un secondo che sarà installato nella stessa ubicazione. Questa tecnologia rivoluzionaria permette di recuperare volumi di gas aggiuntivi dai bacini di Midgard e Mikkel, prolungando la durata estrattiva dei giacimenti e, di conseguenza, il tasso di recupero.
Statoil
Sede a Stavanger, Norvegia
Stabilimenti in oltre 30 paesi
22.000 dipendenti in tutto il mondo
Le principali attività sono sulla piattaforma continentale norvegese
Quotata alle Borse di New York e Oslo
www.statoil.com
Massimizzare l’estrazione di petrolio e gas dai giacimenti sottomarini è sempre stato un tema delicato per l’industria del settore. Quando le sfide diventavano troppo grandi, le compagnie tendevano ad abbandonare. Ora non è più così. Grazie al nuovo sistema di compressione sottomarina del gas della Statoil, è possibile aumentare in modo economicamente vantaggioso il tasso di recupero dei giacimenti.
I nuovi impianti della compagnia energetica norvegese sono i primi al mondo. Appoggiati sul fondo sottomarino, a 300 metri di profondità, nel giacimento di Åsgard, questi provvedono a ottimizzare il tasso recupero del gas e a prolungare notevolmente la durata estrattiva dei bacini di Midgard e Mikkel.
Abbiamo scelto la SKF per la sua competenza nei cuscinetti. È l’unica azienda ad avere un prodotto così qualificato.
Torstein Vinterstø, direttore progetto Åsgard della Statoil
Si stima un incremento del tasso di recupero in questi due bacini nel Mare di Norvegia pari almeno al 20 percento, che equivale a oltre 300 milioni di barili di petrolio recuperati in più. Senza la nuova soluzione, i giacimenti sarebbero stati dismessi prematuramente.
La compressione del gas viene per tradizione effettuata su piattaforme o sulla terra ferma, lontano dai pozzi. Posizionare un compressore in prossimità della bocca di pozzo è invece una soluzione ad alto rendimento energetico, poiché presenta minore ingombro e minori esigenze di manutenzione. Essendo automatica, può essere gestita in remoto, eliminando la necessità di personale e sorveglianza continua.
L’ambiente, inoltre, beneficia di notevoli vantaggi. Rispetto alle soluzioni tradizionali, il compressore sottomarino offre una riduzione del consumo energetico del 40 percento, che si traduce in una notevole riduzione delle emissioni di CO2.
Con la nuova soluzione, l’apparecchiatura di compressione è resistente all’acqua – racchiusa in contenitori ermetici, che offrono un ambiente molto più protetto che in passato, come afferma Torstein Vinterstø, direttore del progetto Åsgard della Statoil. “Sulla terraferma o sulla piattaforma, l’apparecchiatura è esposta agli elementi, alla polvere, all’umidità e alle variazioni di temperatura, mentre il fondo marino offre un ambiente più stabile, con temperature costanti intorno ai 4 °C”.
Ci è voluto un grande sforzo per far quadrare tutto nei tempi previsti e nel rispetto dei costi, ma la SKF ci ha supportati facendo il massimo per soddisfare le esigenze.
Torstein Vinterstø, direttore progetto Åsgard della Statoil
Per realizzare il progetto dell’impianto di compressione sottomarina di Åsgard ci sono voluti circa 10 anni e 11 milioni di ore di lavoro. Ma, come dice Vinterstø, la Statoil voleva fare un investimento a lungo termine. “Essere tecnologicamente all’avanguardia, sia in termini di riduzione costi che ambientali, è importante tanto per la Statoil quanto per i nostri partner. Abbiamo capito che la tecnologia andava concepita diversamente e abbiamo fatto di tutto per ridurre i costi e le emissioni di CO2”.
Vinterstø sostiene che il sistema sottomarino non avrebbe mai potuto avere successo senza il contributo di fornitori come la SKF. “Abbiamo scelto la SKF per la sua competenza nei cuscinetti. È l’unica azienda ad avere un prodotto così qualificato”.
Le due aziende hanno collaborato alla messa a punto della complessa tecnologia dei cuscinetti magnetici, che è integrata nel carter del compressore (v. riquadro). Gli ingegneri della SKF e della Statoil hanno lavorato spesso fianco a fianco in quello che Vinterstø definisce un processo “molto efficiente”: “La SKF forniva le idee e suggeriva come ottenere una qualità adeguata”.
“Il confronto frequente ci ha permesso di far capire loro le nostre esigenze e raggiungere un risultato più efficace”.
Rendere la tecnologia conforme a una lunga serie di norme è stato un processo molto dispersivo, che ha visto la SKF impegnata in un’enorme sfida. Dice Vinterstø: “Penso sinceramente che la SKF sia stata coraggiosa a continuare con noi. Ci è voluto un grande sforzo per far quadrare tutto nei tempi previsti e nel rispetto dei costi, ma la SKF ci ha supportati facendo il massimo per soddisfare le esigenze”.
Per Vinterstø questo è il momento di valorizzare il successo della tecnologia sottomarina, condividendola con altri e adottandola in nuovi giacimenti.
Cuscinetti magnetici di lunga durata
Quando la Statoil decise di realizzare il primo impianto di compressione sottomarina del gas, si rivolse a vari fornitori, tra i quali la SKF.
Dopo cinque anni di intenso lavoro di sviluppo e collaudo, compresa la simulazione delle condizioni sottomarine con 6.000 ore di funzionamento continuo, la soluzione con i cuscinetti magnetici SKF era finalmente pronta per le profondità del Mare di Norvegia.
La scelta di integrare i cuscinetti magnetici nel carter del compressore ha di fatto eliminato l’esigenza di olio lubrificante, tenute e riduttori. I cuscinetti senza attrito offrono maggiore velocità di rotazione, consentendo l’uso di moduli e infrastrutture del compressore più leggeri. Jérémy Lepelley, responsabile vendite, Subsea and Oil & Gas Developments, della SKF Magnetic Mechatronics, ha dichiarato: “Abbiamo imparato molto dal progetto Statoil, che è tecnologicamente all’avanguardia e ci pone in vantaggio rispetto alla concorrenza”.