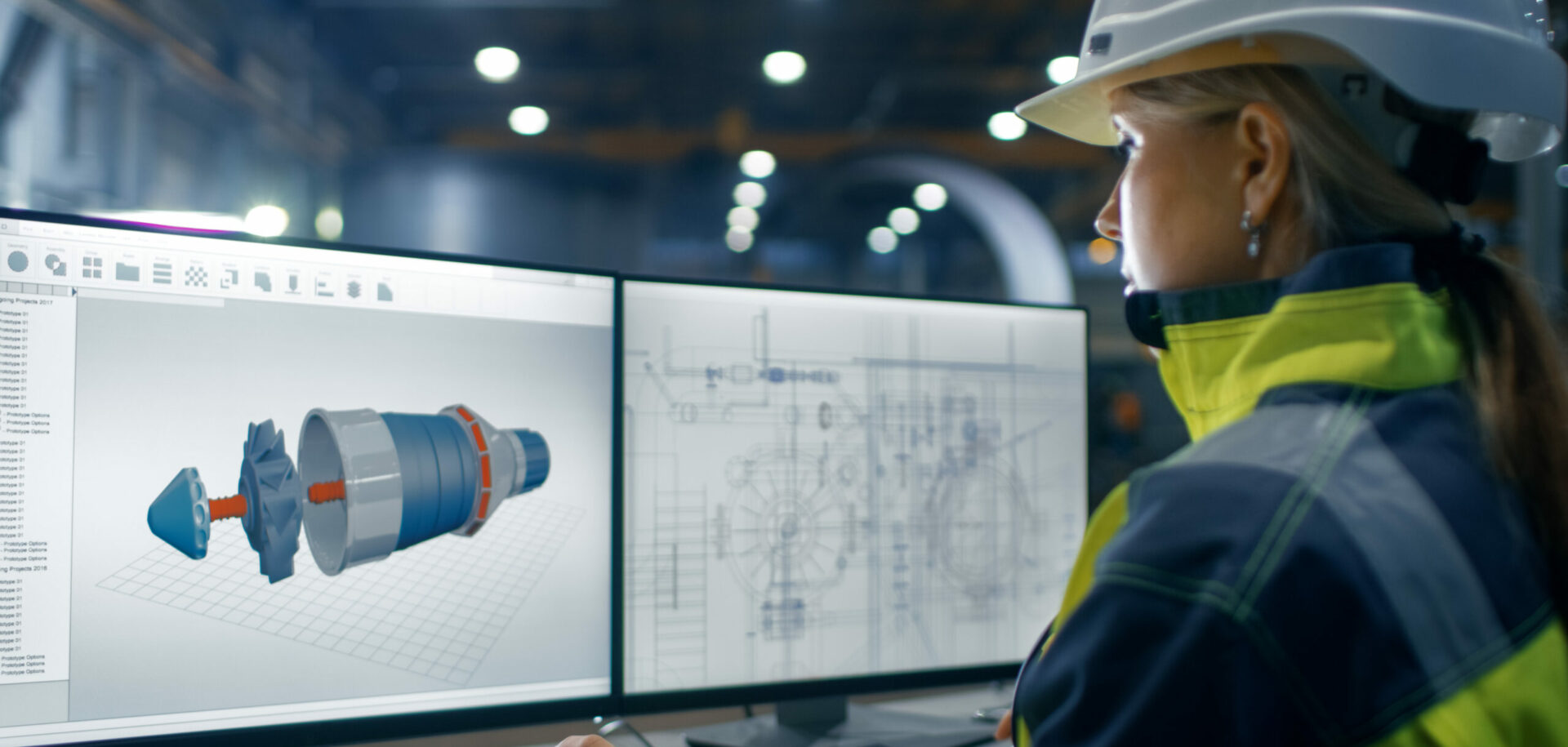
Rilavorare i cuscinetti conviene
Con la rilavorazione dei cuscinetti le aziende possono ridurre fermi macchina e costi e favorire la sostenibilità.
Sintesi
Da decenni è pratica comune nell’industria, e in particolare in quella aeronautica, smontare i cuscinetti volventi in occasione dei lavori di manutenzione o di revisione per rilavorarli e rimetterli in esercizio e, visto che gli interventi sui vari componenti recano molti vantaggi in termini di costo, vale la pena considerarli. A seconda delle condizioni in cui si trovano i cuscinetti, delle loro dimensioni, ecc. si possono avere risparmi tra il 50 e l’80 %. Inoltre la rilavorazione ha un forte impatto sulla sostenibilità ambientale: il ripristino di 100 kg di cuscinetti fa risparmiare circa 350 kg di CO2. Per determinare la durata L10 delle piste dei cuscinetti sottoposte a parziale asportazione del volume sollecitato durante la rilavorazione o a ripristino, si può definire una relazione di tipo algebrico in funzione della profondità z. A seconda dell’entità dell’intervento il fattore di durata LF di un cuscinetto rilavorato può valere da 0,87 a 0,99 volte la durata di un cuscinetto nuovo.
Contatto vendite
Heike Sengstschmid, heike.sengstschmid@skf.com
In tutti i tipi di macchinario i cuscinetti sono componenti fondamentali e la loro sostituzione può essere un problema. In genere li si sostituisce nel corso di una manutenzione programmata – quando si sta avvicinando il termine del loro ciclo di vita – oppure a seguito di un guasto imprevisto. A seconda del tipo, la sostituzione di un cuscinetto può comportare costi elevati e lunghi periodi di fermo macchina, mentre la sua eventuale eliminazione al termine della durata operativa può avere un impatto negativo sotto il profilo della sostenibilità – un aspetto che per investitori e clienti sta assumendo un’importanza crescente. Come fare per prolungare la durata di esercizio dei cuscinetti diminuendo fermi macchina, costi e scarti? La risposta sta nella rilavorazione (figg.1 e 2).
Le analisi costi-benefici indicano che con la rilavorazione si possono avere risparmi che vanno dal 50 all’80 % del costo di un cuscinetto nuovo – a seconda delle dimensioni e della complessità della forma del cuscinetto stesso, delle condizioni in cui questo si trova, del prezzo, ecc. Rilavorare i cuscinetti usati consente inoltre di ridurre le emissioni di CO2. A 100 kg di cuscinetti usati rilavorati può corrispondere una riduzione di circa 350 kg di CO2.
Nell’industria aeronautica, ma non solo, è pratica comune smontare i cuscinetti in occasione della manutenzione o delle revisioni per rilavorarli e rimetterli successivamente in esercizio [1], [2], [3].
Per essere certi che si seguano procedure bene definite e che si abbiamo termini di riferimento attendibili occorrerebbe una norma ISO internazionale. Attualmente esiste solo una norma austriaca [4], pubblicata nel 2011.
Per la rilavorazione dei cuscinetti volventi usati sono state fissate cinque classi.
È possibile descrivere la durata dei cuscinetti rilavorati considerando sia la geometria modificata sia la sollecitazione di taglio τ (τ0, τu) successiva all’asportazione del volume sollecitato e all’effetto dell’inserimento di un nuovo set di corpi volventi.
Durata e affidabilità dei cuscinetti
In genere non si può far funzionare un cuscinetto all’infinito, a meno che le condizioni di lavoro siano ideali e non si raggiunga il carico limite di fatica, altrimenti prima o poi sopraggiunge un affaticamento del materiale [5].
Fatica con inizio sotto-superficiale
Si considera come durata di un cuscinetto il periodo di tempo che precede la comparsa dei primi segni di affaticamento ed è funzione del numero di giri compiuti e dell’entità del carico applicato [6 ÷ 9]. La fatica trae origine dalle sollecitazioni cicliche di taglio presenti immediatamente al di sotto della superficie degli anelli e dei corpi volventi che si trova sottoposta al carico (fig. 3 e formula 1).
S probabilità di sopravvivenza [%]
N numero dei cicli di carico
τ0 sollecitazione massima ortogonale di taglio [Pa]
τᵤ sollecitazione limite di fatica di taglio [Pa]
z0 profondità della sollecitazione massima ortogonale di taglio [m]
a semiasse di contatto in senso trasversale [m]
l lunghezza del contatto sulla pista [m]
e esponente di Weibull
c, h esponente nella formula sollecitazione-durata
Dopo un certo tempo queste sollecitazioni provocano la comparsa di cricche al di sotto della superficie, le quali si estendono gradualmente in superficie. Quando i corpi volventi rotolano sulle cricche si staccano frammenti di materiale, dando luogo al fenomeno del cosiddetto “spalling” (erosione)
Altre modalità di cedimento
Sono note molte altre modalità di cedimento, causate da condizioni di lavoro o installazioni non corrette e protratte nel tempo. La norma ISO 15243, relativa ai danneggiamenti e ai guasti dei cuscinetti volventi [5], ne offre una buona panoramica, anche se, viste le recenti esperienze, andrebbe riveduta.
A metà degli anni ’50 un affermato teorico dei cuscinetti, Arvid Palmgren, esprimeva già l’idea che i cuscinetti potessero essere riparati anziché sostituiti, quando diceva: “La durata di esercizio media è molto più lunga di quella calcolata e quei cuscinetti che presentano brevi durate in realtà richiedono solo la sostituzione di quelle parti che si sono danneggiate per prime”.
Questo non vuol dire che un cuscinetto non possa essere usato una volta che sia comparsa un’erosione o un altro tipo di danneggiamento (fig. 4), rivelati da un aumento di rumorosità e vibrazione. Nel corso degli anni si sono sviluppate tecniche di riparazione dei cuscinetti che hanno consentito di ripristinarne la durata e l’affidabilità previste
Conseguenze
Le analisi e le esperienze circa le tecniche moderne di rilavorazione mostrano come con i cuscinetti riparati si possa raggiungere la durata e l’affidabilità dei cuscinetti nuovi. A seconda dell’entità del lavoro da eseguire, i risultati dei metodi di misurazione delle sollecitazioni, quali la diffrazione ai raggi X (XRD) [10] (fig. 5) e quelli con test non distruttivi (NDT), quali il metodo Barkhausen [11], il Micromagnetic Testing (3M), la spettroscopia a onda elastica non lineare (Non-Elastic Wave Spectroscopy, NEWS) [12], la spettroscopia di risonanza a ultrasuoni delle onde acustiche superficiali (Resonant Ultrasound Spectroscopy of Surface Acoustic Waves, RUSSAW) e l’analisi phased array a ultrasuoni consentono di determinare il fattore rappresentativo della durata LF, il cui valore può andare da 0,87 a 0,99 volte la durata di un cuscinetto nuovo (fig. 6).
Rilavorazione: classificazione
Qui di seguito diamo una spiegazione dei termini e delle definizioni relativi ai cuscinetti volventi che hanno funzionato.
A seconda della tipologia di lavoro e dell’entità di usura del cuscinetto, la rilavorazione si può suddividere in cinque classi (fig. 7).
Sebbene nelle singole classi le operazioni abbiano un numero, l’effettiva sequenza degli interventi non è direttamente connessa con il numero stesso. Si deve infatti tenere conto degli eventuali accordi stipulati tra le compagnie di manutenzione e gli operatori.
Nelle singole operazioni può essere necessario adottare delle cautele. Per esempio, quando un cuscinetto presenta un affaticamento sulla pista che ha avuto inizio sotto la superficie – ved. [5], non va considerato adatto per una rilavorazione nella Classe III, mentre quando presenta un affaticamento della pista con inizio superficiale, provocato da sporcizia o detriti, la pista stessa può spesso essere ripristinata con operazioni di lucidatura o rettifica.
Ulteriori interventi
Nelle operazioni di ricondizionamento (Classe II) o di rilavorazione di livello 1 (Classe III), i cuscinetti che si possono riparare vengono scomposti, ispezionandone visivamente i componenti e misurando la durezza degli anelli. Poi si esegue una verifica dimensionale di quei componenti che si ritiene si possano restaurare. Se necessario, si rettificano o si lucidano le facciate, il diametro del foro e quello esterno, purché le tolleranze lo permettano. Per permettere tali operazioni al fine di ripristinare le dimensioni a disegno, si può ricorrere alla preventiva nichelatura o cromatura delle superfici.
Negli interventi di ricondizionamento (Classe II) si asporta parecchio materiale per togliere i danneggiamenti superficiali e ridurre il volume di materiale sollecitato. La finitura delle superfici va riportata entro le specifiche a disegno o anche migliorata. Successivamente i cuscinetti vengono muniti di nuovi corpi volventi di diametro pari a quello degli originali, più due volte la profondità dal materiale asportato, in funzione delle specifiche del gioco interno del cuscinetto. I nuovi corpi volventi devono avere lo stesso diametro nominale, ma devono avere tolleranze che tengano conto del gioco stesso.
Le gabbie si verificano controllando l’esistenza di cricche e si ricorre a un rivestimento se necessario. Se è il caso le si sostituisce. Generalmente si inseriscono nelle gabbie nuovi corpi volventi e poi si ricompone il cuscinetto.
Nella rilavorazione di livello 1 (Classe III) dei cuscinetti di grandi dimensioni è ammessa una rettifica più profonda delle piste dell’anello interno e di quello esterno. Si possono inoltre seguire altri metodi di lavorazione meccanica (ad es. una tornitura dura). I danneggiamenti superficiali vanno rimossi e si riduce il volume del materiale sollecitato; la finitura delle superfici va riportata in accordo alle specifiche di disegno o anche migliorata. I cuscinetti vengono quindi muniti di nuovi corpi volventi di diametro pari a quello degli originali, più due volte la profondità di rettifica adottata sugli anelli. Nei cuscinetti a rulli cilindrici si impiegano rulli più lunghi e di diametro nominale maggiore di quello degli originali e questo può comportare la rilavorazione degli alveoli della gabbia o la sostituzione di questa.
Con procedimenti e classificazioni chiaramente definiti è possibile fare in modo che la rilavorazione dei cuscinetti soddisfi contemporaneamente sia le norme sia le esigenze dei vari fornitori di servizi.
Classe 0 – Ispezione
La Classe 0 prevede l’ispezione dei cuscinetti usati (o di quelli che sono rimasti a lungo in magazzino) e il confronto con quanto richiesto nei disegni o nelle specifiche. Il processo prevede:
NB: generalmente si consigliano un trattamento appropriato e un’adeguata rilavorazione.
Classe I – Riclassificazione (riqualificazione, bonifica)
La riclassificazione prevede tutte le operazioni di ispezione della Classe 0 e inoltre:
Classe II – Ricondizionamento
Con il ricondizionamento dei cuscinetti si prevedono tutte le operazioni di ispezione (Classe 0) e riclassificazione:(Classe I) e inoltre una o più di quelle seguenti:
Classe III – Rilavorazione di livello 1
La rilavorazione di livello 1 prevede tutte le precedenti operazioni di ispezione (Classe 0) e riclassificazione (Classe I) e, quando è il caso, il ricondizionamento (Classe II) e inoltre una o più delle seguenti operazioni:
19) inserimento di corpi volventi di diametro nominale maggiorato (ved. operazione 13)
20) montaggio della gabbia originaria riparata o di una nuova (ved. operazione 14)
Classe IV – Rilavorazione di livello 2
La rilavorazione di livello 2 prevede le operazioni delle Classi da I a III e l’ulteriore operazione:
Accessibilità globale
La SKF possiede una rete internazionale di centri di servizio a cui i clienti possono accedere per sfruttare tutta una serie di moderne strutture dedicate alla rilavorazione dei cuscinetti. L’azienda è uno dei maggiori fornitori mondiali di cuscinetti e, dal canto suo, la SKF Remanufacturing Services ha a disposizione più di 100 anni di conoscenze ed esperienze nel settore degli organi rotanti.
Nella rilavorazione dei cuscinetti la SKF impiega metodi e macchinari della stessa alta qualità che caratterizza la produzione dei cuscinetti nuovi, offrendo ai clienti la certezza che i loro cuscinetti e i relativi accessori (ad es. i sopporti) vengono trattati in ogni parte del mondo con la stessa cura, la stessa competenza e gli stessi processi di lavorazione. Ecco i vantaggi offerti dalla SKF Remanufacturing Services:
- estensione della durata operativa dei cuscinetti
- riduzione dei costi totali di esercizio
- riduzione dell’impatto sull’ambiente grazie al riciclo dei cuscinetti
- mantenimento delle scorte nel magazzino ricambi
- miglioramento dell’affidabilità del macchinario
- possibilità di ricevere suggerimenti per migliorare l’affidabilità delle applicazioni
I benefici ottenibili con un programma di rilavorazione possono essere incrementati sfruttando l’esperienza SKF nel settore della manutenzione predittiva.
Bibliografia
[1] Zaretsky, E.V.; Branzai, E.V.: NASA TM-2005-212966; “Effect of rolling bearing refurbishment and restoration on bearing life and reliability”. (2005)
[2] Zaretsky, E.V.; Branzai, E.V.: NASA TP-2007-214463, “Model specification for rework of aircraft engine, poser transmission, and accessory/auxillary ball and roller bearings”. (2007)
[3] “Optimize your assets with SKF Remanufacturing Services”. SKF Publication 6697 EN, July 2008
[4] ÖNORM M 6328 :2011 “Rolling bearings – Reworking of used rolling bearings (Wälzlager – Überarbeitung gebrauchter Wälzlager)“
[5] ISO 15243:2004, “Rolling bearings – Damage and failures – Terms, characteristics and causes” (“Cuscinetti volventi – Danneggiamenti e guasti – Terminologia, caratteristiche e cause”)
[6] Lundberg, G.; Palmgren, A.: “Dynamic capacity of rolling bearings”. Acta Politecnica. Mechanical Engineering Series. Royal Swedish Academy of Engineering Sciences, Vol.1, No3, 7, (1947)
[7] Lundberg, G.; Palmgren A.: “Dynamic capacity of roller bearings”. Acta Politecnica. Mechanical Engineering Series. Royal Swedish Academy of Engineering Sciences, Vol.2, No4, 96, (1952)
[8] Ioannides, E.; Bergling, G.; Gabelli, A.: “An analytical formulation for the life of rolling bearings”. Acta Polytechnica Scandinavica. Mechanical Engineering Series No. 137. Espoo 1999
[9] ISO 281:2007, “Rolling bearings – Dynamic load ratings and rating life” (“Cuscinetti volventi – Coefficienti di carico dinamico e durata teorica”)
[10] Voskamp, A.P.: “Material response to rolling contact loading”. Trans. Am. Soc. Mech. Engineers, J.Tribology 107 (1985) 359
[11] Zika, T.; Schimpelsberger, B.; Kern, A.: “Barkhausen-Noise – A possibility for non-destructive grinding burns (TROOSTITE) and residual stress testing”. Science Report 2006-2007, SKF Österreich AG, AT 0802 EN. (2008)
[12] Andersson, B.E.; Griffa, M.; Le Bas, P-Y.; Ulrich, T.J. ; Johnson, P.A. : “Experimental implementation of reverse time”