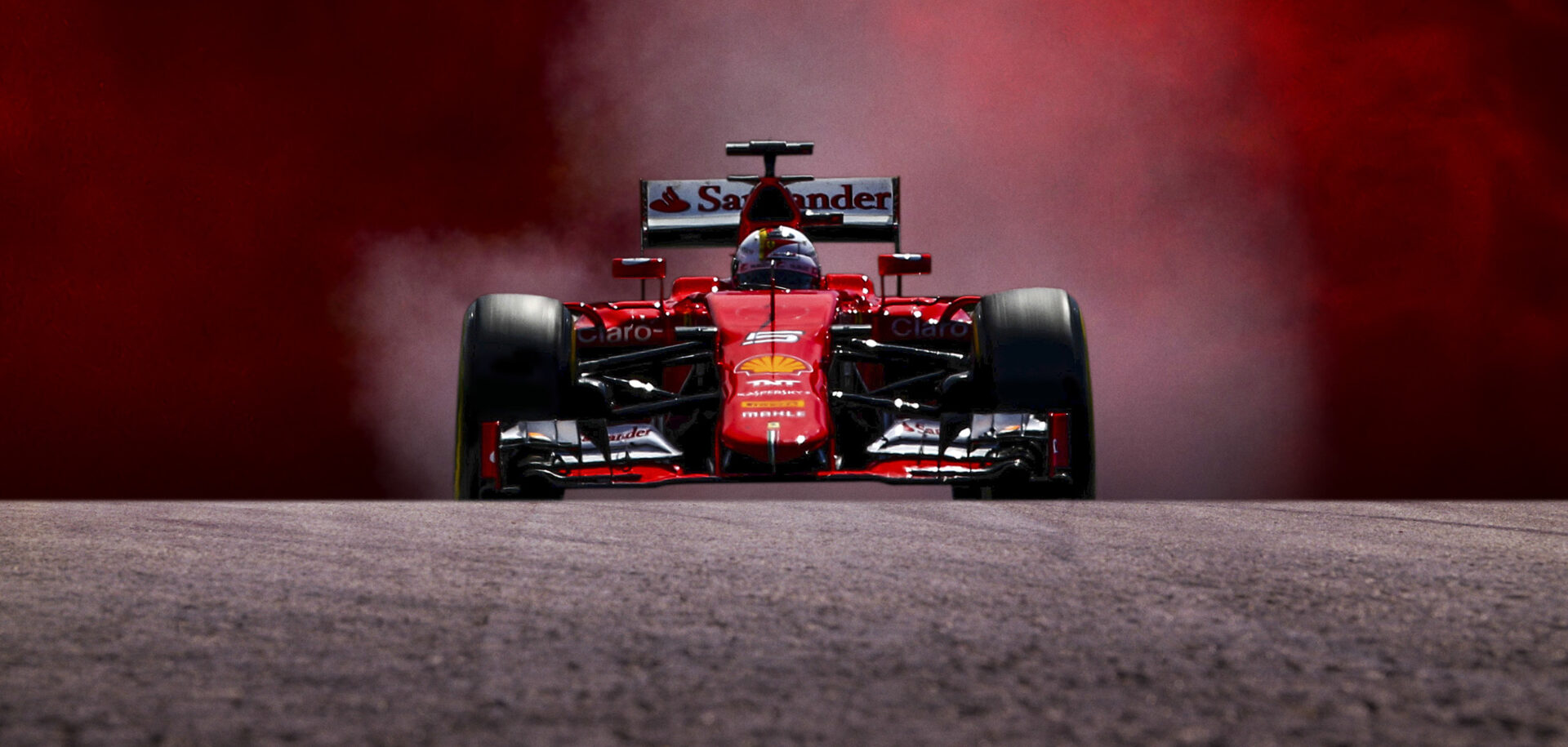
Soluzioni virtuali
Una soluzione integrata hardware e software permette agli ingegneri della Ferrari di vedere in tempo reale, in modalità wireless, cosa succede nelle celle di prova delle power unit.
Fatti
Ferrari in breve
Fondazione: 1929 (storica), 1947 (produzione auto)
Persone chiave: Sergio Marchionne, presidente; Amedeo Felisa, amministratore delegato
Sede: Maranello (Modena)
Proprietà: Fiat Chrysler Automobiles 90 percento, Piero Ferrari 10 percento
Linee di prodotto: corse e automobili sportive
Produzione: >7.000 unità
Fatturato: 2,5 miliardi di euro
Link correlati
Contatto vendite
Laura Baracco, Laura.Baracco@skf.com
Un purosangue può strappare la vittoria per un pelo, ma il cavallino rampante della Scuderia Ferrari deve fare di meglio, soprattutto oggi. Dalla stagione 2014, le direttive tecniche della Formula 1 sono drasticamente cambiate e anche una frazione di secondo di vantaggio può fare la differenza ai fini della vittoria.
I cambiamenti sostanziali introdotti nel 2014 hanno spinto l’azienda di Maranello a sviluppare celle di prova delle power unit di nuova generazione. In passato, non tutti gli impianti di questo tipo erano dotati di sistemi per il monitoraggio continuo delle vibrazioni degli organi di trasmissione, né questi erano integrati in un’unica piattaforma software. Il sistema di telemetria della Ferrari rendeva disponibili on line solo i dati in bassa frequenza e la capacità di post-processing in tempo reale era limitata.
“Per capire cosa succedeva, bisognava esaminare ogni cella”, spiega Mario Kuluridis, capo del Mechanical and Hydraulic Development Team nel settore Power-Unit Testing delle Testing Facilities della Scuderia Ferrari. “Non era possibile controllare on line i dati in alta frequenza in tempo reale. La ricerca dei guasti era troppo lenta e non si potevano fare previsioni sulla durata dei componenti sulla base delle linee di tendenza rilevate”.
Queste inefficienze, in particolare la mancanza di integrazione, nel 2011 indussero Kuluridis e il suo team a cercare sistemi di monitoraggio alternativi. La SKF fu interpellata in virtù della partnership consolidata, la più lunga nella storia della Formula 1, che lega le due aziende dal 1947.
Dopo aver preso in considerazione sia le soluzioni disponibili sul mercato sia quelle all’interno dell’azienda, la Ferrari decise che la piattaforma SKF IMx – compreso il software correlato SKF
@ptitude Observer– rappresentava un ottimo punto di partenza. L’SKF IMx offre funzioni di condition monitoring, protezione degli asset e programmazione della manutenzione preventiva in tempo reale, in pratica le caratteristiche necessarie agli ingegneri di Maranello.
Per rispondere alle esigenze specifiche del team, il sistema è stato altamente personalizzato. Dice Kuluridis: “Il fatto che la SKF fosse un partner tecnico, oltre che uno sponsor ufficiale, ci ha garantito il supporto necessario per adattare il sistema ai nostri requisiti”.
L’idea della Ferrari era quella di avere un sistema wireless integrato per il monitoraggio di singoli elementi durante i test di vibrazione in alta frequenza dell’unità. L’adozione dell’SKF IMx-T per il raggiungimento di questi obiettivi era in corso quando arrivò l’annuncio dei cambiamenti al regolamento tecnico del 2014, i quali accelerarono l’esigenza di migliorare le celle di prova e incrementarne la funzionalità. Le nuove regole hanno trasformato i motori in power unit pluricomponenti e hanno accentuato l’importanza della tecnologia per il recupero dell’energia, ERS, e dell’affidabilità a livello di prestazioni complessive.
La piattaforma SKF IMx standard era stata studiata per rispondere ai requisiti di industrie come quella eolica. Non era concepita per gestire quantità di dati, numeri di canali e volumi di calcoli alla velocità richiesta dalla Ferrari. Occorreva sviluppare una nuova soluzione, comprensiva di hardware e software. Una soluzione “virtuale” che non sarebbe stata autonoma, bensì complementare all’IMx-T e interamente integrata nel software SKF @ptitude Observer.
Attualmente la piattaforma installata gestisce fino a 100.000 controlli al secondo. È in grado di gestire analisi complesse e di inviare i risultati al sistema di telemetria, permettendo agli ingegneri dello sviluppo di controllare on line lo stato delle unità monitorate. Considerato il volume di dati, anche la velocità di calcolo e trasferimento è fondamentale. Il software SKF @ptitude Observer elabora le osservazioni 10-20 volte al secondo e le trasforma in risultati utili. Questo soddisfa l’esigenza espressa dal team di Kuluridis di avere “risultati e non dati”.
La piattaforma è in uso presso le celle di prova delle power unit della Ferrari dal 2013 e, a detta dei tecnici, i vantaggi sono evidenti. L’integrazione permette loro di vedere in tempo reale e in modalità wireless cosa succede in ciascuna cella. Attraverso la creazione di apposite procedure di analisi e diagnosi, la piattaforma ha permesso di identificare e risolvere tempestivamente i problemi prima che questi degenerassero in costosi guasti, riducendo così i tempi di fermo.
Dato che i danneggiamenti si ripercuotono sui componenti della trasmissione o, nel peggiore dei casi, sull’unità sottoposta al test, prevenire i problemi migliora l’efficienza. “Possiamo intervenire prima che si verifichi un danneggiamento”, dichiara Kuluridis. “Occorre semplicemente sostituire il componente problematico e si può subito riprendere, riducendo così i tempi di fermo e i guasti. Abbiamo migliorato la nostra efficienza in modo quantitativamente valutabile”.
@ptitude è un marchio registrato del Gruppo SKF.
Norme 2014 in Formula 1
Andrew Benson, giornalista sportivo della BBC, ha dichiarato che il 2014 ha segnato “un cambiamento epocale nelle norme che regolano la Formula 1”. La trasformazione riguarda le corse, la progettazione e alcune disposizioni tecniche, tra cui la sostituzione dei motori V8 aspirati da 2,4 litri (in uso dal 2006) con i turbo V6 da 1,6 litri. Come scrive Benson, “la potenza del motore torna ad essere un fattore di differenziazione”.
Il motore si chiama ora power unit. Ogni team ne può sostituire fino a cinque per stagione, ognuna delle quali deve avere avuto una percorrenza di almeno 4.000 chilometri. Le vetture non possono imbarcare più di 100 chilogrammi di carburante per gara (circa 130 litri) e il flusso massimo di carburante verso il motore è di 100 litri/h a oltre 12.000 giri/min. Nel 2013, invece, quando i limiti non erano ancora in vigore, i consumi per gara potevano arrivare a circa 150 kg.
Tali limiti sono ampiamente compensati dalla tecnologia ERS (Energy Recovery System).
L’ERS non è una novità, in quanto da anni il sistema KERS provvedeva a recuperare l’energia cinetica prodotta in fase di frenata dall’asse posteriore. Immagazzinata in un pacco batteria, l’energia può essere riutilizzata durante l’accelerazione e può ora erogare una potenza di 120 kW per 30 secondi a giro, più del doppio di quella prevista ante 2014, di 60 kW per fino a 6,7 secondi a giro.
Le norme del 2014 prevedono l’utilizzo di un secondo motore elettrico collegato direttamente al turbo, per utilizzare l’energia che sarebbe dissipata sotto forma di calore. La quantità è illimitata e può essere sia inviata alla batteria sia impiegata in fase di accelerazione.
La soluzione “virtuale” della SKF
Per ottimizzare la velocità e la quantità di dati gestiti dalla piattaforma SKF IMx alla Scuderia Ferrari, la SKF ha realizzato una soluzione “virtuale”. (La definizione “virtuale” è impropria, poiché la soluzione comprende sia l’hardware sia il software). La Ferrari desiderava incrementare e integrare l’hardware della piattaforma esistente, gestendone il controllo attraverso lo stesso software.
Cos’è che rende “virtuale” questa soluzione? Il fatto che per impostare le misurazioni e visualizzarne i risultati, l’operatore non deve aprire una seconda applicazione software né controllare un secondo componente hardware. Proprio quel genere di complicazione che gli ingegneri volevano evitare.
La piattaforma SKF IMx standard ha 16 sensori e algoritmi basati su cicli da sei o dodici mesi. La Ferrari voleva un sistema espandibile, con aggiornamenti bisettimanali o settimanali. Con 30 sensori aggiuntivi e la capacità di gestire i calcoli di routine in tempi molto brevi, il sistema virtuale soddisfa questi requisiti.
Le informazioni permettono alla Ferrari di intervenire in caso di problemi incipienti, modificando un componente prima che si verifichi un danneggiamento.