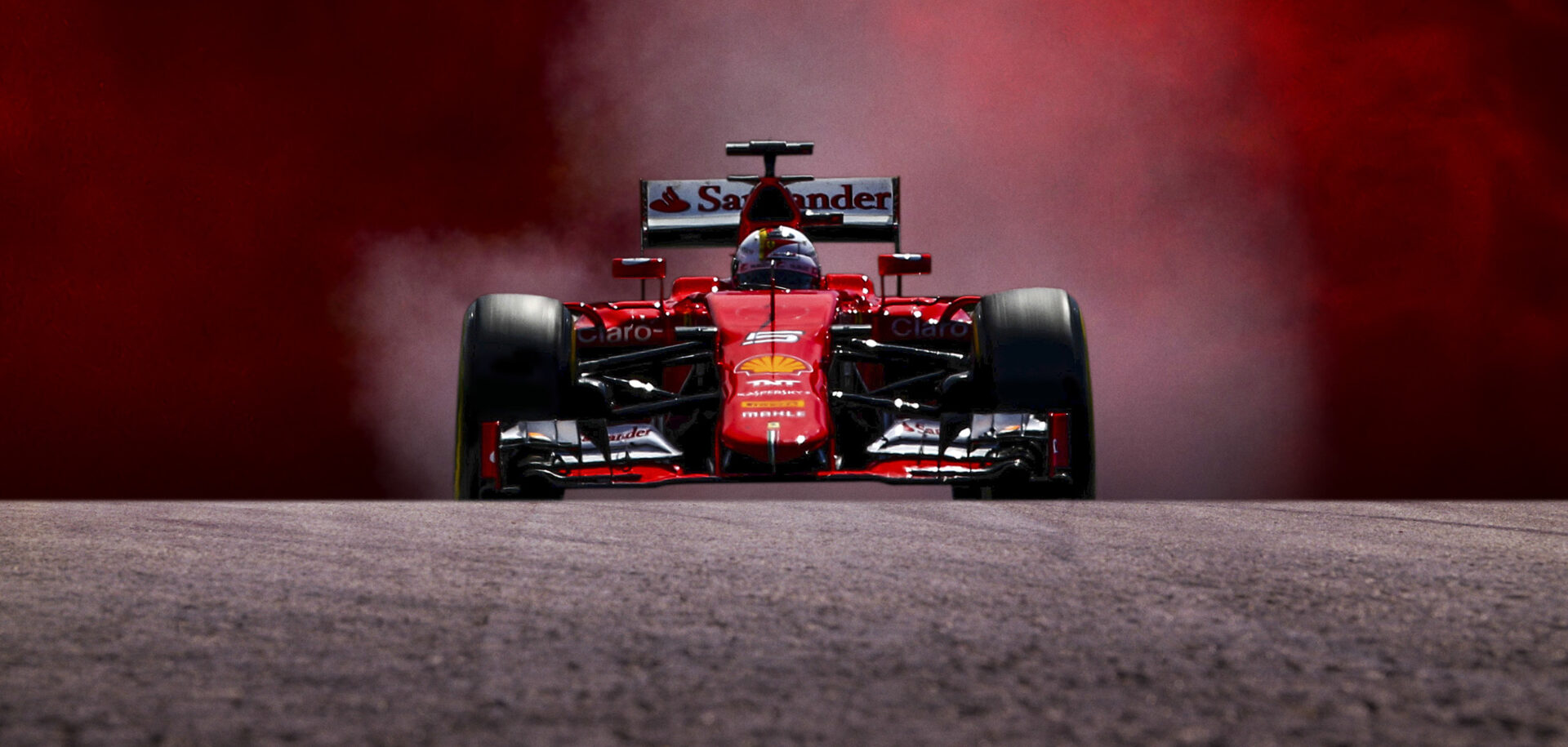
Virtual solutions
A solution that is both hardware and software enables test engineers at Scuderia Ferrari in Italy to wirelessly see what’s happening in every power unit test cell in real time.
A thoroughbred racehorse can eke out a win by a nose, but the prancing horses of Scuderia Ferrari (the Ferrari stable) have to do better than that, especially these days. The technical rules for Formula 1 car racing changed dramatically ahead of the 2014 racing season, and split seconds of advantage have become more decisive than ever in determining victory. The significant changes called for in 2014 were a catalyst for both revamping and building new generations of the company’s power unit test cells in Maranello, Italy. Previously, not all of these test cells had dedicated systems to monitor the vibration behaviour of drivelines on a continuous basis, nor were they integrated in a single software platform. Only low-frequency data were available online on the Ferrari telemetry system, and real-time post-processing capability was limited. “You had to go to each cell to see what was happening,” explains Mario Kuluridis, team leader for test facilities, mechanical and hydraulic development, in Scuderia Ferrari’s power unit testing department. “You couldn’t check high-frequency data online in real time. The troubleshooting was too slow, and you couldn’t make predictions about the life of components based on trends in measurement.” In 2011 these shortcomings, especially the lack of integration, prompted Kuluridis and his team to begin researching alternative monitoring systems. SKF was part of the discussion because the two companies have a close relationship; they have been partners since 1947, one of the longest partnerships in Formula 1 history. Scuderia Ferrari considered both market-available solutions and solutions developed in-house and decided that the SKF IMx platform – including its SKF @ptitude Observer software – represented a very good point of departure. SKF IMx provides condition monitoring, asset protection and preventive maintenance planning in real time, all features sought by the engineers in Maranello. However, it had to be customized to the team’s particular needs. “The fact that SKF was a partner and an official sponsor was a guarantee of tech-nical support in tailoring the system to our requirements,” Kuluridis says. Scuderia Ferrari’s vision was to have an integrated and wireless system with monitoring of individual elements during unit testing for vibration at high frequency. The introduction of SKF IMx-T towards this goal was under way when the 2014 technical changes were announced, accelerating the need for updating the test cells and adding to their complexity. Engines were now multi-component power units, ERS technology was becoming a major factor, and reliability was extremely important in overall performance. The standard SKF IMx platform was geared to industries such as wind farms. It wasn’t designed to handle the amount of data, number of channels and volume of calculation at the speed desired by Scuderia Ferrari. A new solution had to be developed, incorporating both hardware and software. This “virtual” solution would not be a stand-alone, but rather an addition to the IMx-T, fully integrated on the SKF @ptitude Observer software. Today, the installed platform handles up to 100,000 observations a second. It is capable of managing complex analyses and sending their results to the telemetry system, enabling development engineers to check online the status of units being tested. Because of the volume of data, the speed of calculation and data transfer is also vital. SKF @ptitude Observer software synthesizes the observations into manageable results 10 to 20 times per second. This supports the team’s emphasis on “results, not data”, Kuluridis says. The platform has been used in Scuderia Ferrari’s power unit test cells since 2013, and the advantages are obvious, say the test engineers. Integration means that an engineer can see what is happening wirelessly in every cell in real time. By developing dedicated analysis routines and diagnoses, the platform has been able to identify and address potential problems before they degenerate into expensive breakdowns. Downtime has been reduced. Because damage could result in losses on the driveline components or, in the worst case, on the unit under test, anticipating problems improves efficiency. “We can intervene before something is damaged,” Kuluridis says. “We only have to change the problematic part and can begin again immediately, reducing downtime as well as damage, so our efficiency has improved quantifiably.” @ptitude is a registered trademark of the SKF Group. BBC sportswriter Andrew Benson states that 2014 marked “the biggest set of rule changes in Formula 1 history”. They encompass ra-cing, design and technical changes, with the latter including the replacement of the naturally aspirated 2.4-litre V8 engine (used since 2006) with a 1.6-litre V6 turbocharger. “Engine power will be a performance differentiator again,” writes Benson. The engine is now called a power unit. Each team is restricted to just five per car and season, and each has to last 4,000 kilometres. Drivers are limited to 100 kilograms of fuel per race (about 130 litres), and fuel flow is restricted to 100 litres per hour at more than 12,000 r/min. By contrast, teams were consuming about 150 kilograms per race in 2013, when there were no consumption or flow limits. These limitations are more than compensated by ERS (energy recovery system) technology. ERS is not new. For years the KERS system has been harnessing kinetic energy from the rear axle during braking. Stored in a battery pack, it can be reused during acceleration and can produce 120 kilowatts during 30 seconds per lap. This is more than double its pre-2014 allocation of 60 kW for up to 6.7 seconds a lap. New as of 2014 is a second electric motor fitted to the turbo. It uses energy that would otherwise be dissipated as heat. The amount is unlimited and can either be battery-stored or used for acceleration. To handle the speed and volume of data flowing through the SKF IMx platform at Scuderia Ferrari, SKF developed a “virtual” solution. (The “virtual” moniker is not quite accurate, since the solution includes hardware as well as software.) Scuderia Ferrari wanted additional hardware that would be integrated with the platform’s existing hardware and controlled by the same software. What makes it “virtual” is that the operator doesn’t have to open a second software application or control a second piece of hardware to set the measurements and display the results. That was a complication the test team engineers wanted to avoid. The standard SKF IMx platform has 16 sensors and algorithms based on six-month or one-year cycles. Scuderia Ferrari wanted an expandable system and biweekly or weekly updates, which the virtual system delivers, with up to 30 additional sensors and the ability to handle routine calculations with very short turnarounds. This information enables Scuderia Ferrari to intervene in case of anticipated problems and to modify a component before damage occurs.
Formula 1 technical changes for 2014
SKF’s “virtual” solution