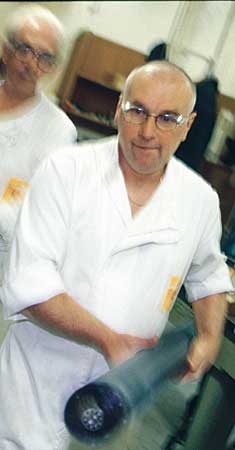
Sulla strada giusta
Fermate impreviste dimezzate alla Kodak grazie alla collaborazione con la SKF, con conseguente maggiore affidabilità della macchina per carta fotografica sensibile denominata Track Five.
L’enorme macchina per carta EKTAcolor della Kodak è collocata in uno dei più grandi edifici di mattoni d’Europa, che si erge maestoso sull’esteso quartiere di Harrow, a nordovest di Londra. Conosciuta anche come «Track Five», questo capolavoro di velocità e precisione applica il rivestimento fotosensibile alla carta fotografica. La Kodak Ltd, è la più antica consociata dell’americana Eastman Kodak Company. La produzione in Gran Bretagna inizia nel 1891, a tre anni dalla presentazione della prima fotocamera portatile ad opera di George Eastman, che si poteva acquistare con 25 dollari.
«La Track Five è il cuore di questo impianto» dichiara Paul Byatt, che ha lavorato 12 anni su questo macchinario. Byatt è attualmente direttore della seccheria, la persona responsabile della gestione dell’intero percorso della carta attraverso la macchina.
La carta passa a ciclo continuo nelle due linee di produzione della Track Five, che si snoda per cinque piani all’interno dell’edificio. Gli enormi rotoli di carta da caricare misurano 1,5 metri di larghezza per 4.000 metri di lunghezza. Il rotolo percorre circa 1.500 metri di impianto e, durante i vari processi, passa attraverso 2.000 rulli. Le operazioni comprendono il rivestimento, il raffreddamento e l’essiccazione del prodotto. Dalle parole di Byatt traspare un evidente attaccamento a questa macchina ma, come afferma, a volte la dedizione non è sufficiente.
Come spiega Byatt, attraversando un labirinto di corridoi dal soffitto basso, lo sbobinatore è la parte meno affidabile a causa dell’età. La macchina ha 35 anni, e per soddisfare i carichi di lavoro ha sempre funzionato a una velocità superiore del 25% rispetto a quella di progettazione. Si sono dunque verificati problemi di affidabilità, molto costosi in termini economici. Nel 2000 ci sono state ben 290 fermate ed è stato difficile far fronte agli impegni lavorativi.
Un’ottima collaborazione
È a quel punto che Chris Moon e Gerald Rolfe della SKF Reliability Systems UK entrano in scena. Nel novembre 2001 compiono una prima valutazione. «All’inizio ci proposero varie apparecchiature e cercarono di convincerci a partecipare subito a un progetto di razionalizzazione», ricorda Byatt, spostandosi per lasciar passare un camion che trasporta rotoli di carta grandi come una persona. «Non volevo più saperne. Pensavo si trattasse delle solite vendite, quindi stavo per allontanarli».
Per fortuna, non l’ha fatto. Nelle settimane successive, si instaura un’ottima collaborazione, frutto di una conoscenza graduale, molto più che un semplice rapporto venditore-cliente.
Nell’aprile 2002 Moon e Rolfe comunicano le conclusioni dei loro studi e i relativi suggerimenti. Byatt, ancora scettico, rimane piacevolmente sorpreso nel constatare che non gli viene proposto l’acquisto di numerose apparecchiature, ma gli viene presentata un’analisi che individua 13 punti chiave da prendere in considerazione.
I due tecnici SKF consigliano a Kodak un esame dei componenti più costosi dal punto di vista dei tempi passivi. L’analisi rivela che le interruzioni causate dalla sezione giunzioni, ritenuta la più problematica a causa delle frequenti rotture, sono in realtà meno costose di quelle causate dai rulli di pressione che si guastano meno, ma richiedono 500 minuti per ogni riparazione.
L’esame SKF interessa anche le operazioni di montaggio dei cuscinetti, il magazzino e la manutenzione generale. Fare qualsiasi intervento non è facile perché, durante la produzione, la carta diventa sensibile alla luce e la macchina funziona per circa due terzi in condizioni di oscurità. Ogni due settimane le luci vengono accese per i controlli tecnici, ma queste interruzioni possono essere molto costose.
Manutenzione predittiva
«I 2.000 rulli contengono 4.000 cuscinetti. Se cede anche solo uno di questi, rischiamo di graffiare il prodotto. Oggi facciamo una manutenzione predittiva anziché reattiva, ossia non aspettiamo che avvengano le rotture, e in questo la SKF ci ha aiutato», commenta Byatt, in piedi in una stanza illuminata, dove una fila di rulli alimenta la carta grezza portandola al buio, verso gli sbobinatori. Sono stati fatti investimenti in tecnologie quali il sistema SKF Marlin, il software di analisi dei macchinari, nonché nella formazione.
Sam Smith, 21 anni, è uno studente di ingegneria della Loughborough University, nel Leicestershire. Il giovane ha frequentato uno stage di due giorni sulla lubrificazione presso il Business and Technology Park SKF di Utrecht, Olanda, dove ha appreso la grande importanza della corretta lubrificazione dei cuscinetti.
Durante lo stage, gli specialisti Ron James e Ray Monk puliscono e riparano i rulli della Track Five. James preleva uno speciale martello da uno scaffale.»Questo – spiega roteandolo in aria – è uno degli attrezzi che la SKF ha saputo migliorare. Una volta usavamo i martelli classici, ma questo ha la particolarità di ammortizzare l’impatto. Un’altra importante novità è che i cuscinetti difettosi, invece che finire nel cestino, vengono inviati alla SKF per un’analisi».
L’insistenza di Byatt, che ha voluto adottare un approccio graduale con i tecnici SKF, ha convinto tutti. Grazie a questa collaborazione, i costi dovuti a guasti improvvisi sono diminuiti di 1,5 milioni di euro. La SKF, dal canto suo, prevede un volume di 150.000 euro in lavori di progetto per il 2004.
Obiettivi del programma di intervento della SKF Reliability Systems:
- Riduzione dei tempi di inattività dovuti a guasti improvvisi
- Rielaborazione delle strategie di manutenzione
- Affidamento alla SKF per tutte le forniture.
Dove intervenire:
- La sostituzione di 500 rulli di trasporto all’anno si rivela eccessiva. Questa situazione sembra collegata agli elevati sforzi che si producono e alle zone in cui i cuscinetti si possono sporcare. Il problema può essere risolto ristudiando la manutenzione, in modo da aumentare il grado di affidabilità.
- Esistono margini per prevedere altri punti di verifica delle prestazioni, utilizzando accelerometri su trasmissioni, riduttori e motori dalle condizioni più critiche. Questi strumenti possono essere combinati con dati ottenuti con ispezioni di altro tipo, in un processo automatizzato che sfrutta un efficace software di manutenzione predittiva.
Suggerimenti:
- Considerare un più ampio utilizzo della tecnologia Operator Drive Reliability, nella registrazione degli eventi e nell’acquisizione dei dati di feedback.
- Migliorare anche la registrazione e applicare l’analisi di Pareto, incorporando i costi e i tempi totali di inattività. I vantaggi finanziari derivanti confermeranno la validità delle soluzioni adottate al fine di migliorare l’affidabilità.
- Revisione dei metodi di calcolo dei tempi inattivi non previsti. Questi dovranno riflettere il tempo impiegato per le riparazioni (e il tempo di fermo totale) oltre a quello intercorso tra i guasti.