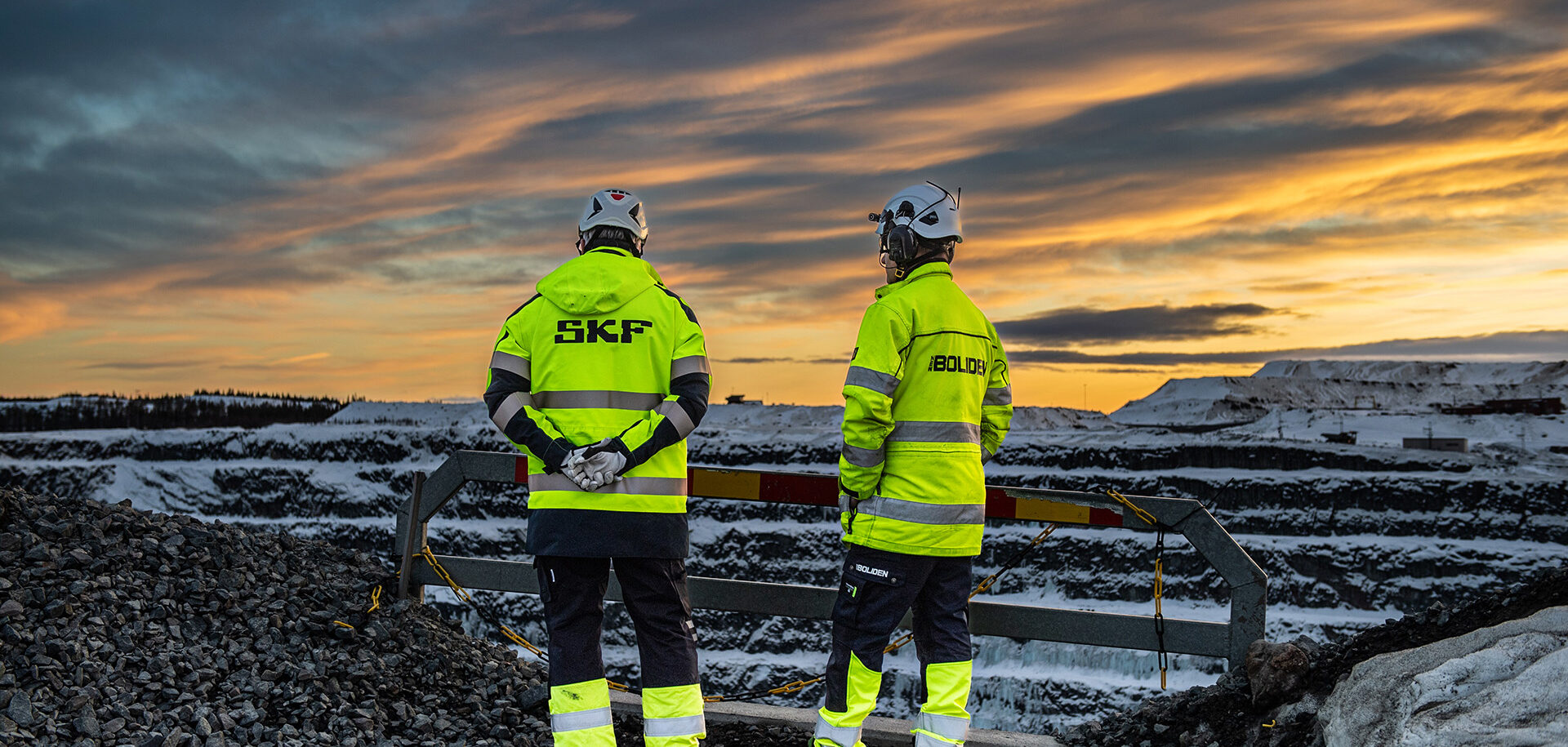
Una nuova collaborazione accresce l’affidabilità dei nastri trasportatori
Guasti e conseguenti fermi di produzione affliggevano i lunghi nastri trasportatori nella miniera di rame di Aitik, di proprietà di Boliden. La soluzione è stata un nuovo sistema di monitoraggio delle vibrazioni e la partnership con SKF.
“Prima avevamo fermate non programmate della produzione per rotture improvvise, ogni settimana, ma oggi i fermi produzione sono quasi esclusivamente programmati”, dichiara Stefan Johansson, supervisor for preventive maintenance presso il Crushing & Conveying department di Boliden Aitik, fuori dalla città di Gällivare.
Oggi i fermi produzione sono quasi esclusivamente programmati
Stefan Johansson, supervisor for preventive maintenance presso il Crushing & Conveying department di Boliden Aitik.
Il trasporto rappresenta un’attività critica per la miniera di rame. Per estrarre un contenuto di minerale pari a circa lo 0,2 percento occorre scavare enormi volumi di roccia e trasportarli dapprima con gli autocarri verso i frantumatori e poi con i nastri trasportatori al concentratore. Fin dall’inizio delle attività, nel 2010, il sistema di nastri trasportatori lungo sette chilometri è stato l’anello debole della catena.
“Abbiamo avuto un bel po’ di problemi, con interruzioni settimanali dell’impianto”, dice Jonas Fjellner, section head del Crushing & Conveying department di Boliden Aitik. “Sapevamo che il problema erano i cuscinetti di pulegge motrici e tamburi”. Il sistema di monitoraggio delle vibrazioni esistente aveva alcuni limiti e mancava il know-how per analizzare i valori misurati.
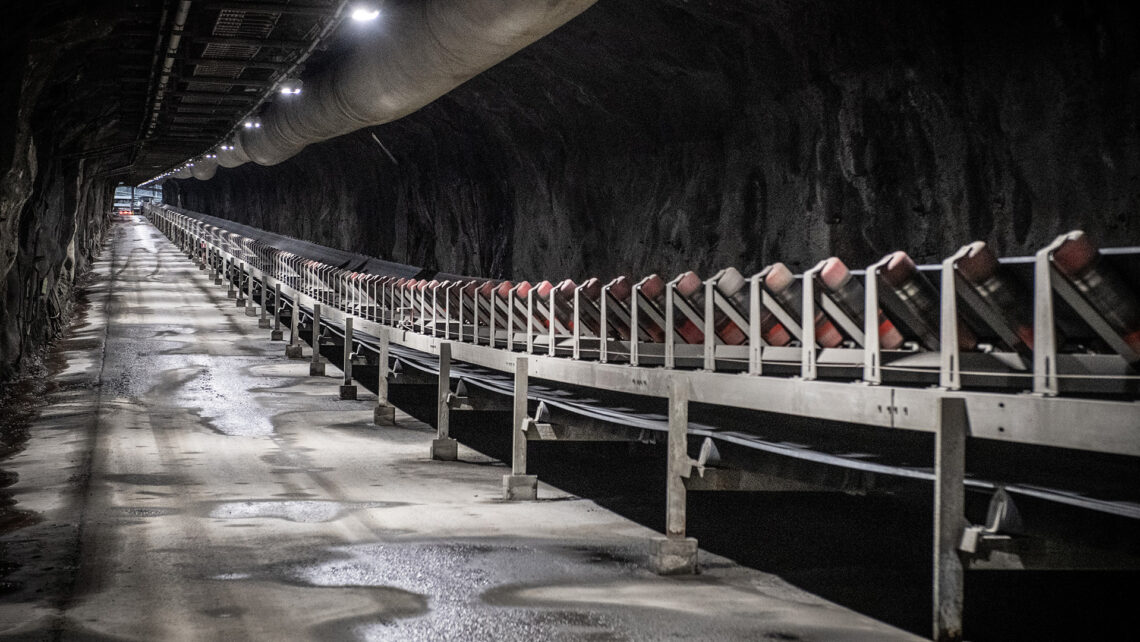
Soluzione “end to end”
Si è cominciato a pensare a un sistema totalmente nuovo. Ci voleva una soluzione end to end e un partner locale, con il quale Boliden potesse collaborare per l’intero processo, dall’installazione alle misurazioni e analisi fino alla risoluzione dei problemi e al miglioramento continuo.
Di qui la decisione, nel 2018, di cambiare sia il sistema di monitoraggio sia il metodo di lavoro, che ha portato alla firma di un contratto di partnership con SKF nel 2019. Come prima cosa, l’hardware è stato interamente sostituito con il sistema di monitoraggio delle vibrazioni SKF. In più si è scelto di installare esclusivamente cuscinetti e supporti SKF. A metà del 2020, quando l’installazione del nuovo sistema era stata estesa a tutto l’impianto, i risultati erano già evidenti. “La disponibilità è decisamente aumentata”, osserva Stefan Johansson. “Dal 2019 non si sono più verificati fermi imprevisti imputabili al cedimento dei cuscinetti e la manutenzione è oggi tutta programmata”.
Riunioni congiunte
Uno dei fattori che più ha contribuito al successo dell’iniziativa è, secondo Johansson, la nuova organizzazione in stretta collaborazione con SKF: “Quando dobbiamo sostituire un cuscinetto, per esempio, SKF ci aiuta a capire cosa è successo mediante l’analisi delle cause originarie; poi, durante le riunioni del gruppo di progetto, valutiamo se sostituire i cuscinetti, le tenute o provare una soluzione diversa”.
SKF ha anche organizzato alcune sessioni di formazione per il personale di Boliden, e ne ha già programmate delle altre.
Al momento SKF gestisce l’analisi dei dati di vibrazione rilevati dal sistema di monitoraggio, spesso in contatto diretto con il personale del settore Crushing & Conveying. “Se durante le misurazioni si attiva un allarme, telefoniamo a SKF per controllare le rilevazioni, anche se è venerdì notte o sabato”, fa notare Johansson.
Emissioni ridotte con il ricondizionamento
La nuova metodologia ha prodotto molti importanti cambiamenti, che sono sfociati sia in una maggiore disponibilità delle macchine sia in un maggior riciclo di materiali grazie al ricondizionamento di cuscinetti e supporti.
“Le misurazioni ci forniscono molte informazioni, e quando capiamo che un cuscinetto deve essere sostituito, coinvolgiamo SKF”, commenta Johansson. SKF effettua una prima valutazione in loco del cuscinetto da sostituire per capire se lo stesso può essere ricondizionato”.
Nel corso del 2022 sono stati ricondizionati 22 tra cuscinetti e supporti e, alla fine di marzo 2023, ne sono stati inviati altri 10 per essere sottoposti al medesimo processo. Oltre a far risparmiare l’equivalente di circa 6 milioni di corone svedesi, il ricondizionamento ha drasticamente ridotto le emissioni di carbonio rispetto alla produzione di cuscinetti nuovi.
Nel 2022 Boliden e SKF hanno firmato un nuovo contratto triennale di partnership. “Questo consolida la nostra collaborazione e conferma la direzione intrapresa”, afferma Johansson.
“Vorrei proprio che adottassimo lo stesso approccio anche in altri siti di Boliden: è davvero eccezionale. Lavoriamo come una squadra, con un grande senso di unità, e puntiamo a obiettivi comuni”.