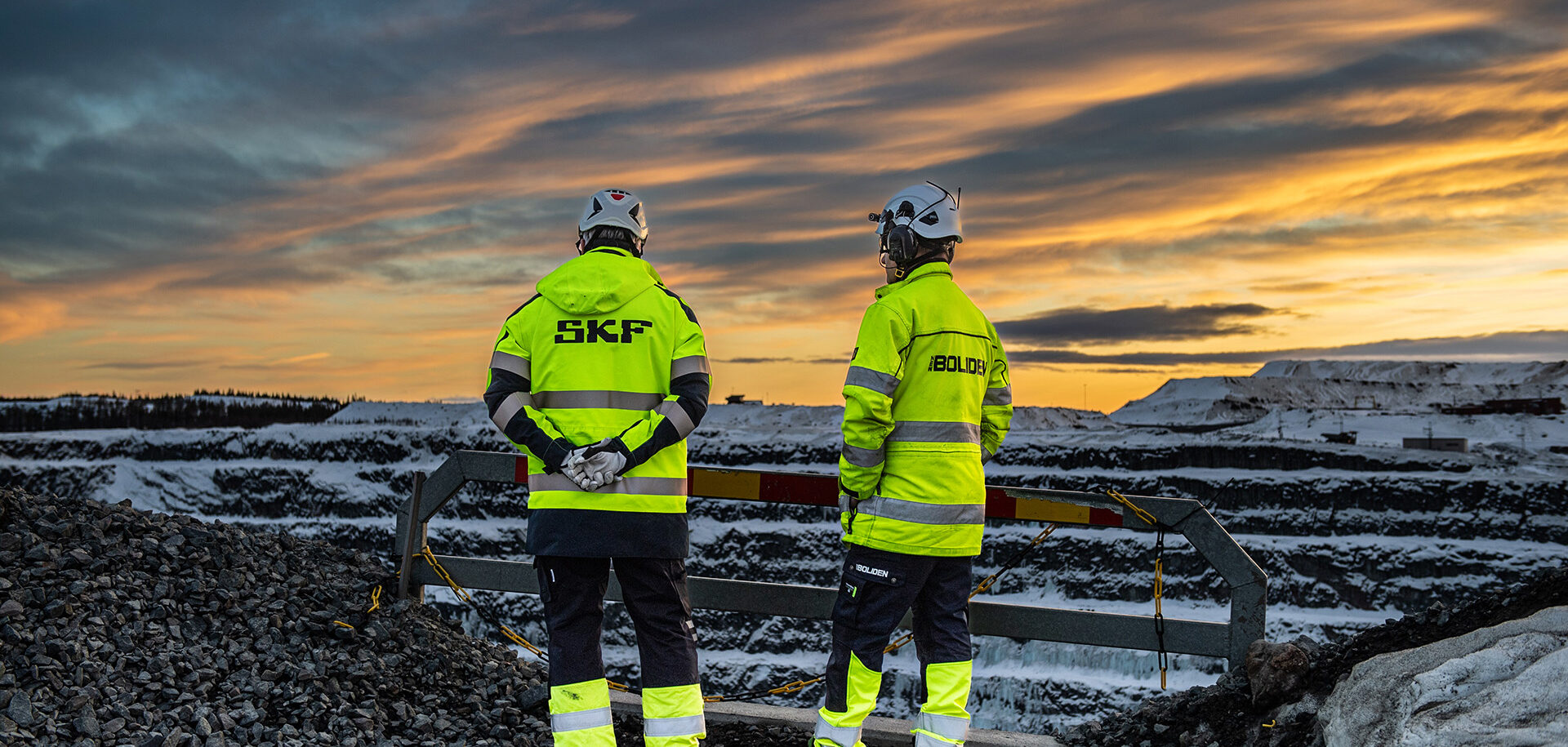
Una nueva colaboración incrementa la confiabilidad de las cintas transportadoras
La larga cinta transportadora de la mina de cobre Aitik de Boliden sufría continuos problemas e interrupciones. La solución fue un nuevo sistema de monitoreo de la vibración y una colaboración con SKF.
La mina de cobre Aitik de Boliden, en el norte de Suecia, por fin tiene controlado su mantenimiento preventivo, gracias a un nuevo sistema de monitoreo de la vibración y una colaboración con SKF.
“Antes, cada semana, teníamos que parar la actividad por incidencias no previstas. Ahora, casi todas las paradas están programadas”, afirma Stefan Johansson, supervisor de mantenimiento preventivo del departamento de Trituración y Transporte de la mina Aitik de Boliden, situada a las afueras de la ciudad de Gällivare.
Ahora, casi todas las paradas están programadas.
Stefan Johansson, supervisor de mantenimiento preventivo del departamento de Trituración y Transporte de Aitik de Boliden
El transporte es una función crítica en la mina de cobre Aitik. Para extraer un contenido de mineral aproximado del 0,2 %, es necesario arrancar y transportar volúmenes enormes de roca, primero en camiones hasta las trituradoras de la mina a cielo abierto y, después, en cintas transportadoras hasta la planta concentradora. Desde la inauguración de la mina en 2010, la cinta transportadora de siete kilómetros de largo siempre ha sido el eslabón débil de la cadena.
“Cada semana, teníamos muchísimos problemas que impactaban en nuestras operaciones”, explica Jonas Fjellner, antiguo jefe de sección del departamento de Trituración y Transporte de Aitik de Boliden. “Ya habíamos identificado los rodamientos de las poleas de transmisión y los tambores como origen del problema”. El sistema de monitoreo de la vibración que se había instalado presentaba ciertas deficiencias, y no había el conocimiento necesario para analizar los valores medidos.
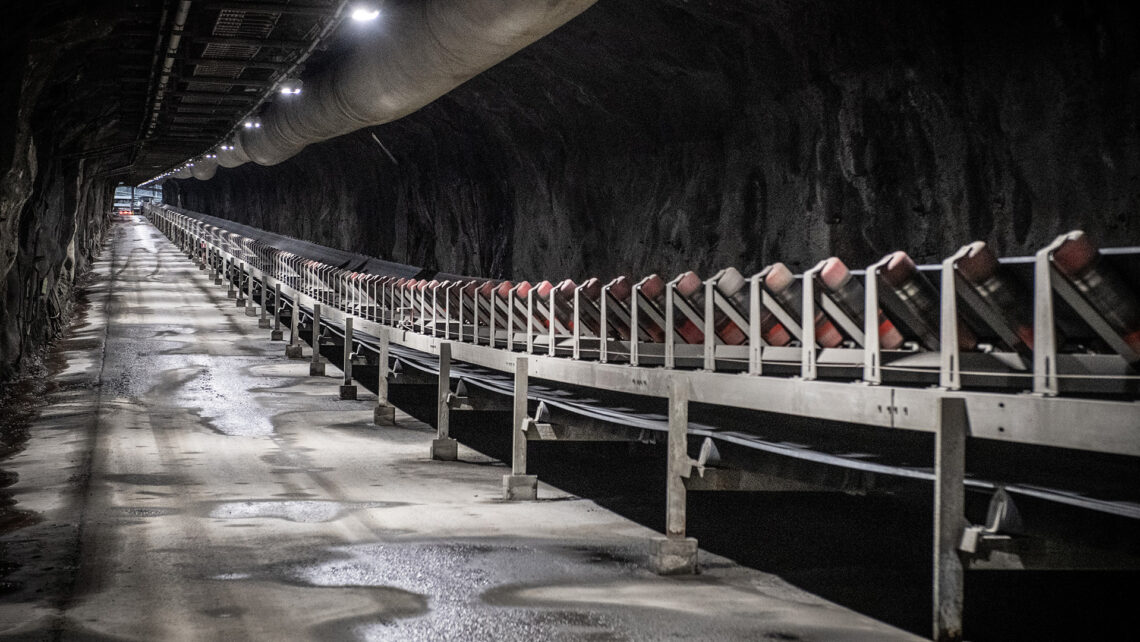
Solución integral
Se hablaba de empezar de cero con un sistema completamente nuevo. Lo que se buscaba era una solución integral y un colaborador local con el que Boliden pudiera trabajar durante todo el proceso: desde la instalación, medición y análisis hasta la resolución de problemas y las mejoras continuas.
En 2018, se decidió que había que cambiar tanto el sistema de monitoreo de la vibración como el método de trabajo, y en 2019 se firmó un contrato de colaboración con SKF. El primer paso fue sustituir todo el hardware con el sistema de SKF para el monitoreo de la vibración. También se decidió pasar íntegramente a los rodamientos y soportes de rodamiento de SKF. Una vez instalado el nuevo sistema, a mediados de 2020, los resultados ya eran apreciables. “La disponibilidad ha aumentado, sin duda”, confirma Stefan Johansson. “Desde 2019, no hemos tenido paradas imprevistas por fallas en los rodamientos, y hoy, todas las operaciones de mantenimiento son planificadas”.
Reuniones conjuntas
Uno de los factores que más han contribuido al éxito, según Johansson, es la implementación de un sistema organizativo nuevo basado en una colaboración estrecha con SKF. Explica: “por ejemplo, si sustituimos un rodamiento, SKF nos ayuda con un análisis de causa raíz para identificar qué ha pasado, y en nuestras reuniones del grupo de proyecto, decidimos si debemos sustituir los rodamientos, cambiar los sellos o probar una solución diferente”.
SKF también ha impartido sesiones de capacitación para el personal de Boliden, y habrá más en el futuro.
De momento, SKF gestiona el análisis de los datos de medición obtenidos del monitoreo de la vibración, generalmente en contacto directo con el personal del departamento de Trituración y Transporte. “Si suena una alarma durante las mediciones, nos puede llegar una llamada desde SKF, incluso los viernes por la noche o los sábados, para que comprobemos algo que han detectado”, continúa Johansson.
Menos emisiones con el reacondicionamiento
El nuevo método de trabajo ha facilitado muchos cambios importantes que han aumentado tanto la disponibilidad como el reciclaje de materiales mediante el reacondicionamiento de rodamientos y soportes.
“Las mediciones nos brindan mucha información, y, si vemos que ha llegado el momento de sustituir un rodamiento, llamamos a SKF”, dice Johansson. Después de sustituirlo, SKF inspecciona el rodamiento in situ y realiza una evaluación inicial para considerar las posibilidades de reacondicionamiento”.
En 2022, se reacondicionaron 22 unidades, tanto rodamientos como soportes de rodamiento, y a finales de marzo de 2023, se habían enviado otras 10 para su reacondicionamiento. Además de ahorrar unos 520 000 euros, el reacondicionamiento supuso una reducción significativa de las emisiones de carbono en comparación con la fabricación de productos nuevos.
En 2022, Boliden y SKF firmaron un nuevo contrato de colaboración de tres años. “Este nuevo contrato nos permitirá profundizar nuestra colaboración y continuar por el camino que nos hemos fijado”, afirma Johansson.
“Me gustaría ver replicada esta iniciativa en otras minas de Boliden”, dice. “Es una forma fantástica de trabajar. Avanzamos todos en la misma dirección, trabajamos hacia objetivos comunes y el grupo está muy cohesionado”.