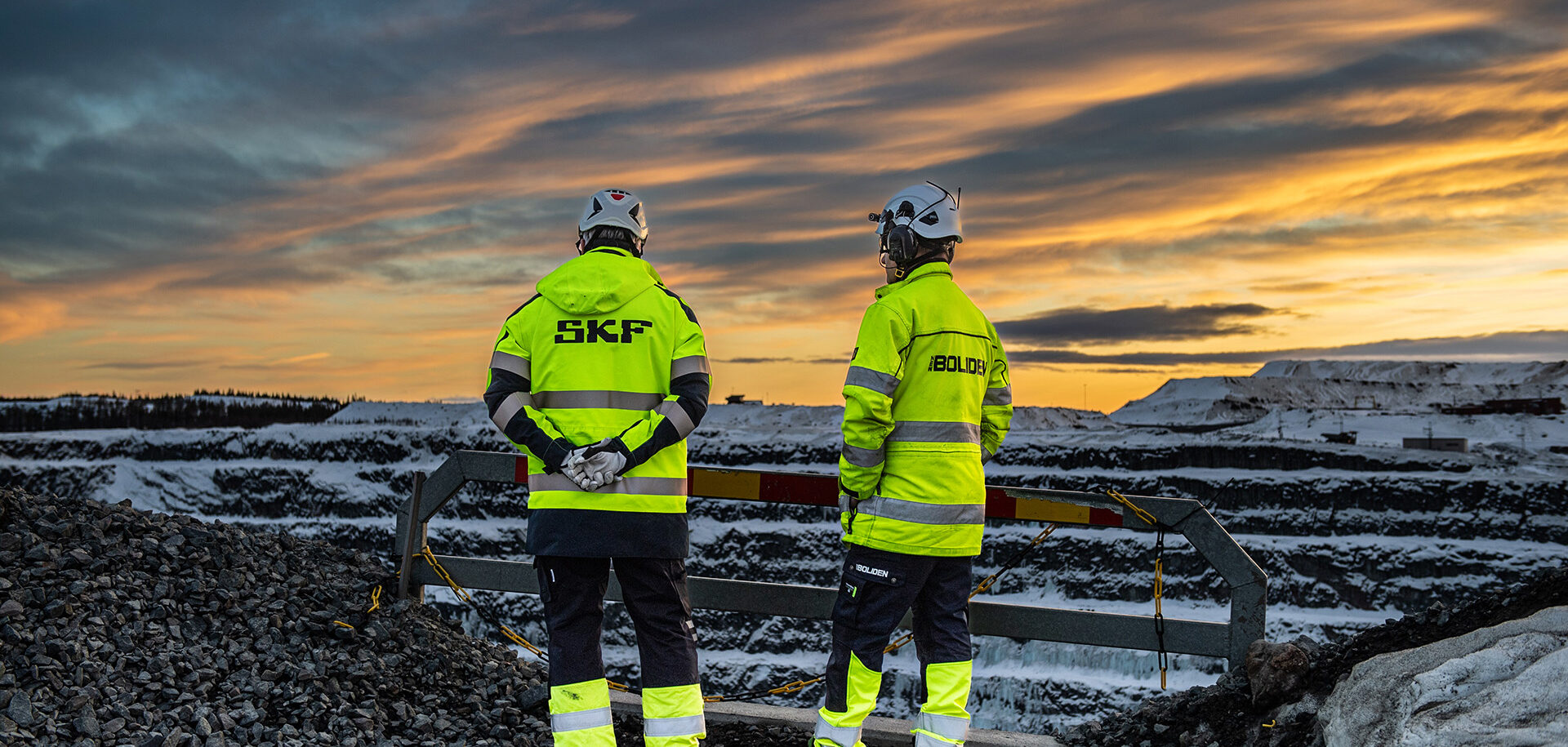
New cooperation increased the reliability of conveyors
Problems and disruptions plagued the lengthy conveyor belt at the Boliden Aitik copper mine. The solution was a new vibration monitoring system and a partnership with SKF.
Boliden’s Aitik copper mine in northern Sweden now has its preventive maintenance under control, thanks to new vibration monitoring and a partnership with SKF.
“Previously, we had unplanned disruptions to operations every week, but today we have largely only planned stoppages,” says Stefan Johansson, supervisor for preventive maintenance at the Crushing & Conveying department at Boliden Aitik, situated outside the city of Gällivare.
Today we have largely only planned stoppages.
Stefan Johansson, supervisor for preventive maintenance at the Crushing & Conveying department at Boliden Aitik
Transport is a critical function in the Aitik copper mine. To extract an ore content of approximately 0.2 percent, enormous volumes of rock have to be quarried and transported, first by trucks to the crushers in the open-pit mine and then further on via conveyor belts up to the concentrator. Since the start of operations in 2010, the seven-kilometre-long conveyor belt line has been a weak link in the chain.
“We had an incredible amount of trouble with disruptions to operations every week,” says Jonas Fjellner, former section head of the Crushing & Conveying department at Boliden Aitik. “We knew that the bearings in the drive pulleys and drums were the problem.” The vibration monitoring system that was installed had certain shortcomings, and the know-how to analyse the measurement values in the organization was lacking.
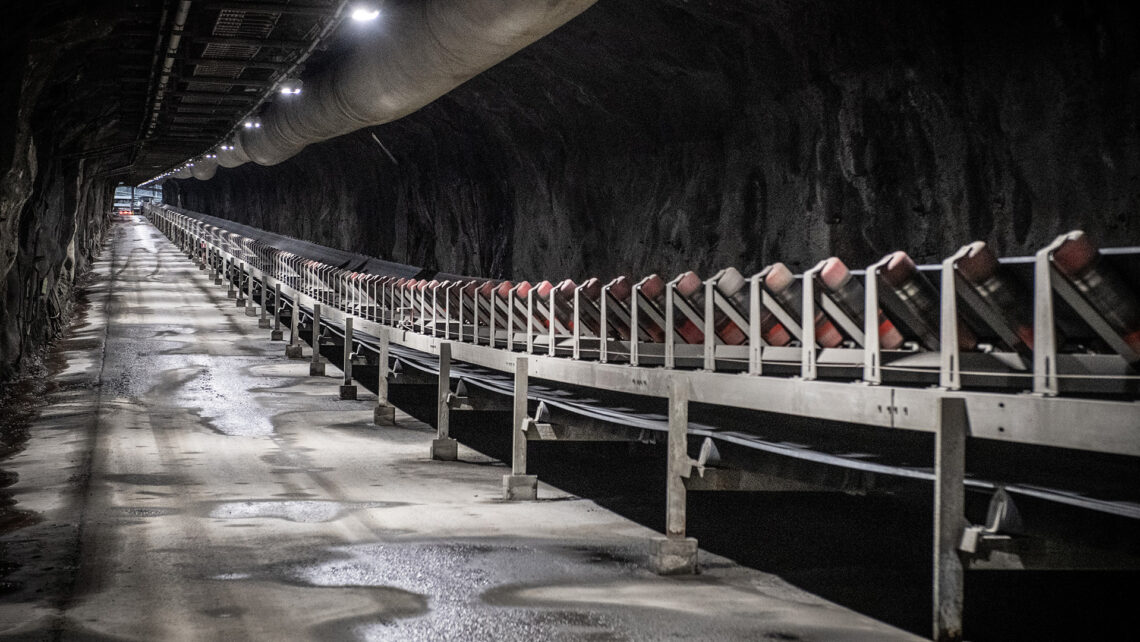
End-to-end solution
There was talk of starting fresh with an entirely new system. What was wanted was an end-to-end solution and a local partner that Boliden could work with for the entire process – from installation, measurement and analysis to problem-solving and continual improvements.
In 2018 it was decided that both the vibration monitoring system and the working method needed to be changed, and in 2019 a partnership agreement was signed with SKF. The first step was replacing all the hardware with SKF’s system for monitoring vibrations. The decision was also made to switch entirely to SKF bearings and bearing housings. By mid-2020, when the new system had been installed throughout the facility, results were already noticeable. “Availability has definitely increased,” says Stefan Johansson. “Since 2019 we haven’t had any unplanned stoppages due to bearings failures, and today all our maintenance is planned.”
Joint meetings
Johansson says that one major contributing success factor is a new organization with close collaboration with SKF. He explains: “If, for example, we replace a bearing, SKF helps us with a root-cause analysis to identify what happened, and at our project group meetings we discuss whether we need to replace bearings, change seals or test a different solution.”
SKF has also conducted a few training sessions with staff from Boliden, and more are in the pipeline.
At present, SKF manages the analysis of measurement data from the vibration monitoring, often in direct contact with staff from the Crushing & Conveying department. “If an alarm sounds during the measurements, we could get a call from SKF to check something that’s been detected, even on a Friday night or a Saturday,” Johansson says.
Fewer emissions with remanufacturing
The new working method has resulted in many important changes that have led to both increased availability and recycling of materials through reconditioning bearings and bearing housings.
“We get a lot of information from the measurements, and if we see that it’s time to replace a bearing we bring SKF in,” Johansson says. In conjunction with the replacement SKF checks the bearing on site and makes an initial assessment of whether it can be remanufactured.”
In 2022, 22 items, both bearings and bearing housings, were remanufactured, and by the end of March 2023 a further 10 items had been sent for remanufacture. In addition to realizing savings of approximately SEK 6 million, remanufacturing drastically reduced carbon emissions compared with making new products.
In 2022 Boliden and SKF signed a new three-year partnership agreement. “This means we are deepening our cooperation and continuing on the path we have laid down,” Johansson says.
“I’d really like to see us working this way at more of Boliden’s sites,” he says. “It’s a fantastic approach. We wear the same team colours, work towards common goals and gain a great sense of unity in the group.”