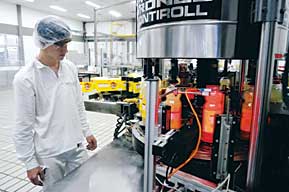
Una soluzione per la soia
Il forte sviluppo del settore agro-alimentare brasiliano e la concorrenza impongono alle società di contenere i costi. Per raggiungere questo obiettivo, la Bunge Alimentos ha adottato un sistema completo di manutenzione, controllo e formazione, che pone l’accento sulla prevenzione.
Sintesi
L’accordo commerciale tra il concessionario SKF Trevotek e la Bunge Alimentos risale al dicembre 2001, quando la Trevotek presenta la tecnologia relativa a cuscinetti, strumenti e attrezzature durante il meeting annuale dei manager industriali della Bunge, presso la sede centrale brasiliana. Nel gennaio 2002, Rúbio Muller, responsabile degli impianti di frantumazione, interpella la Trevotek per richiedere una proposta di soluzione integrata. Nei sei mesi che seguono, tecnici Trevotek visitano tutti gli impianti di frantumazione della soia della Bunge situati in Brasile. Compongono quindi un kit di base composto da 14 strumenti e parti, personalizzabile per ogni sito. Il contratto, siglato nell’agosto 2002, è il più importante di questo tipo per la SKF: 170.000 dollari iniziali per i primi nove impianti, da estendere successivamente ad altri due. Il miglioramento dell’efficienza e la riduzione dei fermi macchina hanno reso gli stabilimenti brasiliani della Bunge tra i più produttivi al mondo; l’impianto per la frantumazione a Ponta Grossa, nello stato meridionale di Paraná, è diventato un punto di riferimento a livello internazionale.
L’agricoltura brasiliana vive oggi un momento di grande espansione. Alle tradizionali coltivazioni di canna da zucchero e caffè sono state affiancate nuove colture, con una rapidità pari solo alla crescita della superficie dei terreni coltivabili. La soia è la protagonista assoluta di questa evoluzione: nuove tecnologie, semi potenti, la maggior parte dei quali non geneticamente modificati, e un terreno fertile hanno permesso di uguagliare la produttività degli Stati Uniti.
La Bunge Alimentos è la consociata della Bunge Ltd per il settore alimentare, con sede negli Stati Uniti, a White Plains, New York. Lo stabilimento brasiliano, che comprende una divisione fertilizzanti, nei primi nove mesi del 2003 ha realizzato un fatturato pari a circa 4,9 miliardi di dollari, con un incremento del 59% rispetto allo stesso periodo del 2002. Sebbene le fluttuazioni valutarie e i prezzi delle materie prime abbiano svolto un ruolo determinante, le cifre riflettono l’enorme espansione dell’agricoltura brasiliana attualmente in corso.
Impianti sotto pressione
Rúbio Muller, responsabile degli stabilimenti per la frantumazione della soia della Bunge in Brasile, dice che il raccolto brasiliano della soia cresce con un tasso annuo del 10-15%, e nel 2004 sono previste 60 milioni di tonnellate.
Per far fronte alla crescente quantità di prodotto da lavorare bisogna controllare i costi. «Questo è il punto di partenza – afferma Muller – Il nostro business sono le materie prime. Produciamo olio e farina di soia e i margini sono molto stretti. Il mercato agro-alimentare è sempre più competitivo e le società che non riducono i costi sono semplicemente destinate a scomparire».
Muller sostiene che gli impianti devono funzionare 24 su 24, per sette giorni alla settimana, quasi per tutto l’anno. E’ un cambiamento rispetto al passato: quando tra un raccolto e l’altro passavano parecchi mesi, una volta all’anno i macchinari per la frantumazione della soia venivano completamente smontati e rimontati, cosa che avviene ancora solo per la canna da zucchero e il succo d’arancia. «E’ un metodo molto costoso oltre che rischioso di gestire la manutenzione – afferma Muller – Il fatto di dover ricorrere a fornitori esterni comporta un rischio elevato che il lavoro non sia fatto bene».
E’ un rischio che la Bunge non intende più correre. Negli ultimi anni si sono resi disponibili notevoli quantitativi di materie prime, al punto che gli impianti funzionano in modo quasi continuo. Obiettivo di Muller è limitare i tempi di fermo macchina a 15 giorni senza compromettere l’intero impianto.
Tutto questo ha comportato un vero e proprio cambiamento culturale. Nel passato, infatti, le macchine venivano fatte funzionare con scarsi controlli. «Abbiamo iniziato a concentrare l’attenzione sulla prevenzione piuttosto che sulla correzione» – afferma Muller. Inizialmente si è trattato di introdurre concetti basilari quali il controllo di vibrazione e temperatura. «Convincere le persone dell’importanza di queste azioni ha richiesto molto impegno – ricorda Muller – Sostituire una macchina è facile, difficile è far cambiare alla gente il modo di pensare».
Soluzione integrata
Nel gennaio 2002, Muller decide di rivolgersi a Eduardo De Peder della Trevotek, concessionario SKF a San Paolo, che aveva già effettuato un servizio di monitoraggio degli impianti presso la Bunge, per richiedere una soluzione integrata della SKF. Trevotek propone un complesso di strumenti per il monitoraggio e la manutenzione e un programma di formazione per il personale. La Trevotek assiste la Bunge anche nel controllo e nella riduzione delle scorte di cuscinetti e altri componenti di ricambio, pur garantendone la disponibilità quando necessari.
L’entità di questa partnership, sostiene Muller, è ben visibile presso il nuovo stabilimento brasiliano della Bunge a Uruçuí, nello stato nordorientale di Piauí, la cui attività è iniziata nel luglio 2003. Lo stabilimento sorge completamente isolato, lungo il nuovo confine agricolo.
Proprio per la sua posizione, Uruçuí deve poter essere completamente auto-sufficiente. Grazie all’addestramento del suo personale interno ad opera della Trevotek, la Bunge ha potuto evitare di rivolgersi ad un fornitore esterno per effettuare l’allineamento laser dei macchinari, prima dell’inizio dell’attività.
«Tutto ciò è stato fatto con il chiaro obiettivo di ridurre i costi» afferma Muller.
Per rendere l’idea dei risparmi resi possibili dalla collaborazione con Trevotek, Muller dice che nel passato le perdite di produzione causate da fermi macchina per guasti, manutenzione e altri motivi, in alcuni stabilimenti ammontavano a circa il 10%. Attualmente, gli impianti della Bunge in Brasile con le migliori prestazioni hanno perdite di produzione dello 0,5 %.