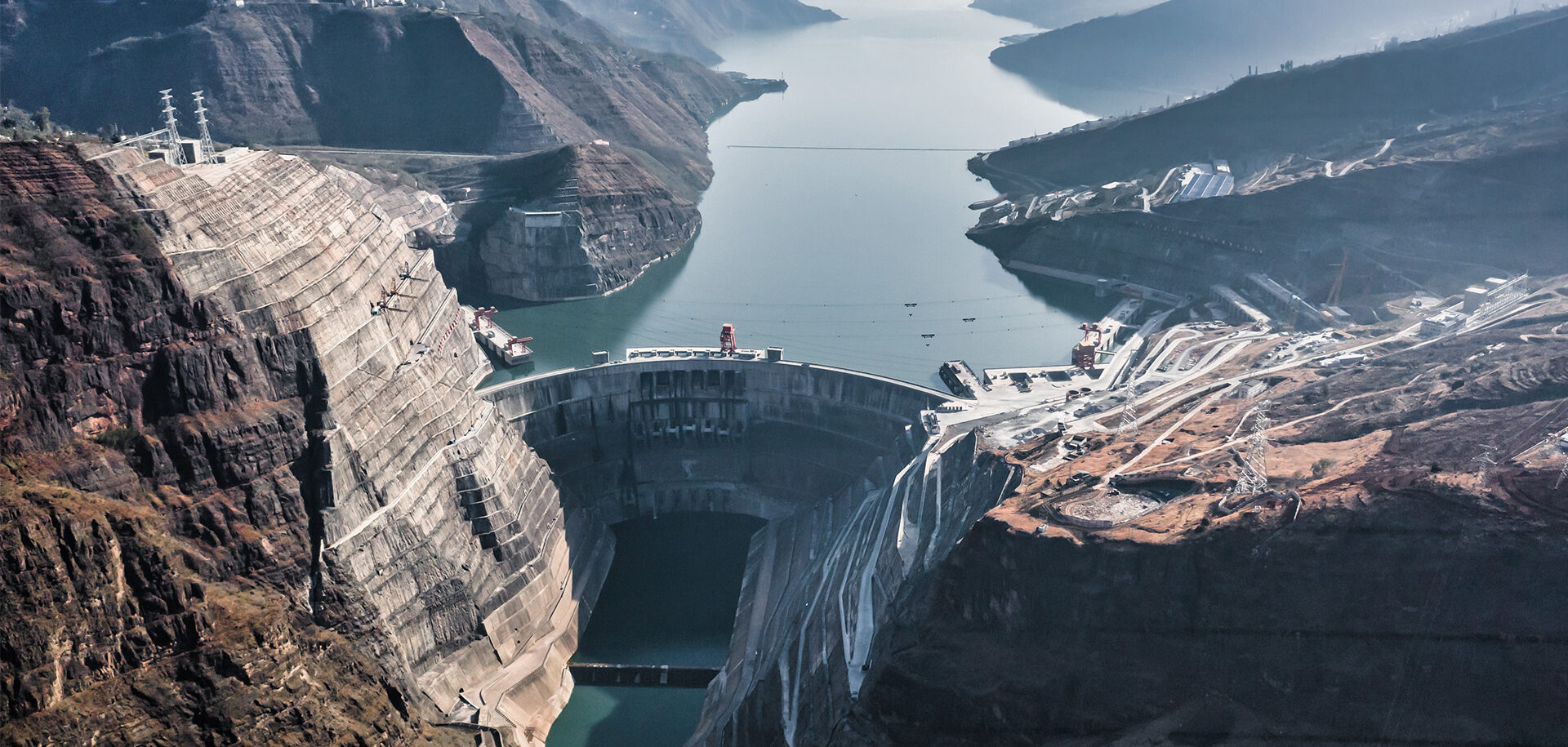
Letting the power flow
China’s latest hydropower mega project is the final piece of the world’s largest renewable energy scheme.
On 20 December 2022, after 13 years in construction, Baihetan Hydropower Station was fully connected to China’s electricity grid. With an installed capacity of 16,000 megawatts, the plant is the last link in China’s “clean energy corridor”, a series of six giant hydroelectric dams built along the Yangtze River and its tributaries that have made significant contributions to the development of clean energy in China. The new station will generate an average of 62.443 billion kilowatt hours of clean electricity every year.
Built on the lower reaches of the Jinsha River, Baihetan Hydropower Station is the second-largest hydropower facility in the world, behind the 22,500 MW Three Gorges Dam, which is 1,300 kilometres downstream along the corridor. The plant is a record-breaker in other ways, however. While Three Gorges Dam produces power using 32 main 700 MW hydroelectric generators, Baihetan is equipped with just 16 giant 1,000 MW units, the largest hydroelectric machines ever built.
Jumbo turbines
In large-scale hydroelectric power production, turbine size matters. Using fewer, bigger turbines reduces installation, maintenance and operating costs and increases the energy conversion efficiency of a plant. And with a peak efficiency of 96.97 percent, Baihetan’s turbines are the most efficient in the world at present, according to the China Three Gorges Corporation, a Chinese power company.
Safety through strength
The water that feeds the Baihetan turbines is held behind a 7-metre-wide, 289-metre-tall double-curved concrete arch dam. This giant structure, the height of a 100-storey building, holds back more than 20 billion cubic metres of water, resisting a hydraulic thrust load of 16.5 million tonnes.
Using fewer, bigger turbines reduces installation, maintenance and operating costs and increases the energy conversion efficiency of a plant
The dam has been designed to work safely in extreme conditions, including a once-in-a-thousand-years catastrophic flood scenario. Its flood discharge facility consists of six overflow outlets and seven bottom outlets on the dam body, together with three spillway tunnels on the left bank. Flow through the hydropower station itself takes place through a bank tower equipped with three separate gates: a stratified inlet gate, a maintenance gate and a quick emergency gate that can drop down to cut off water flow within four minutes under dynamic water conditions.
Inside the cylinder, motion and stability are provided by a new generation of special spherical plain bearings from SKF. The bearings are composed of a copper alloy outer ring inlaid with dry lubricant and a stainless steel inner ring. They are characterized by their high load-carrying capacity, low friction, corrosion resistance, extremely long service life and compact design.