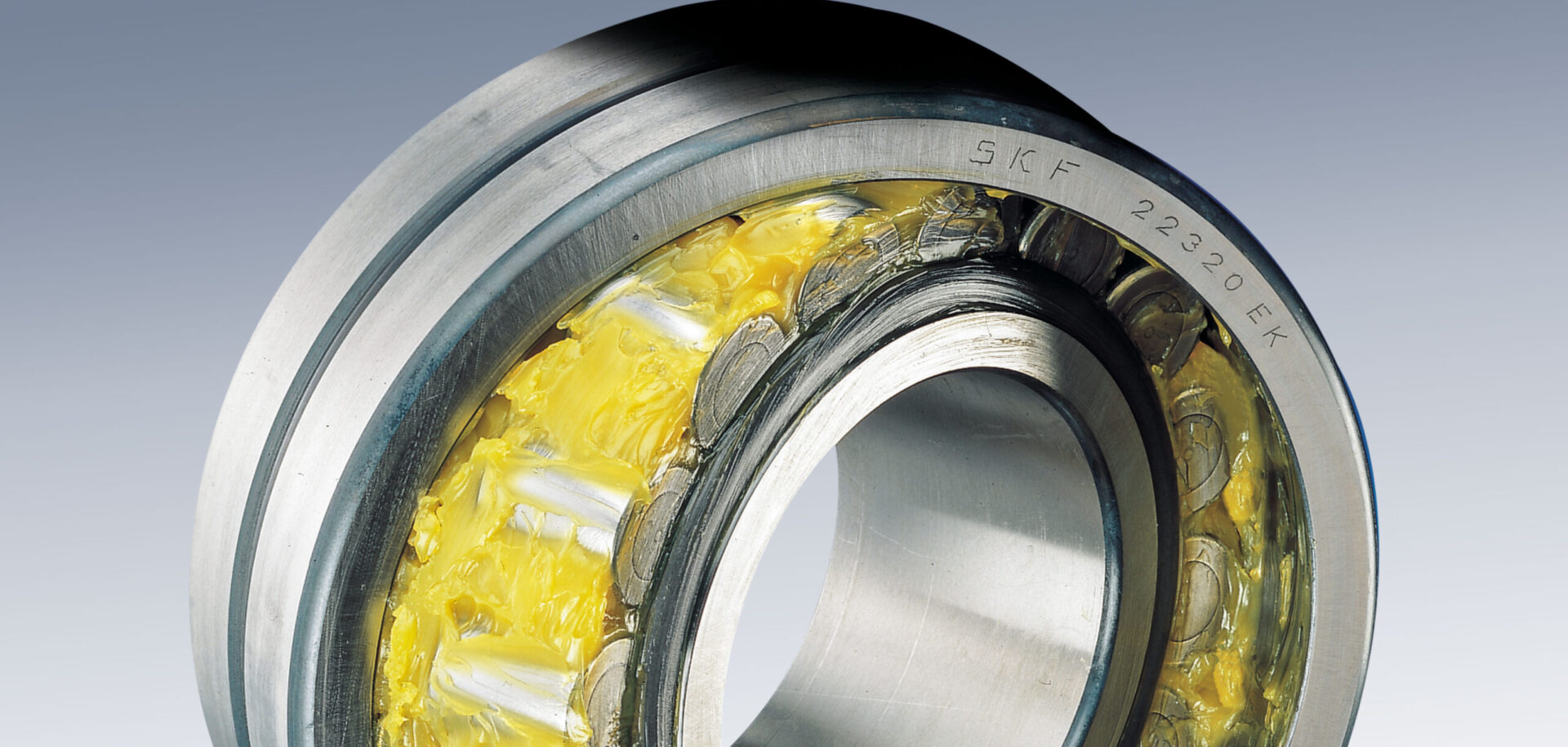
Lubricating Greases: Unravelling the Mysteries of Their Remarkable Behaviour
Lubricating greases have been an integral part of our lives for centuries, playing a crucial role in the smooth operation of machinery and equipment. These semi-solid substances, composed of a base oil and a thickener, possess unique properties that make them indispensable in various applications, from rolling bearings to automotive components.
(Based on the article “A Coarse Grained Molecular Dynamics Model for the Simulation of Lubricating Greases”)
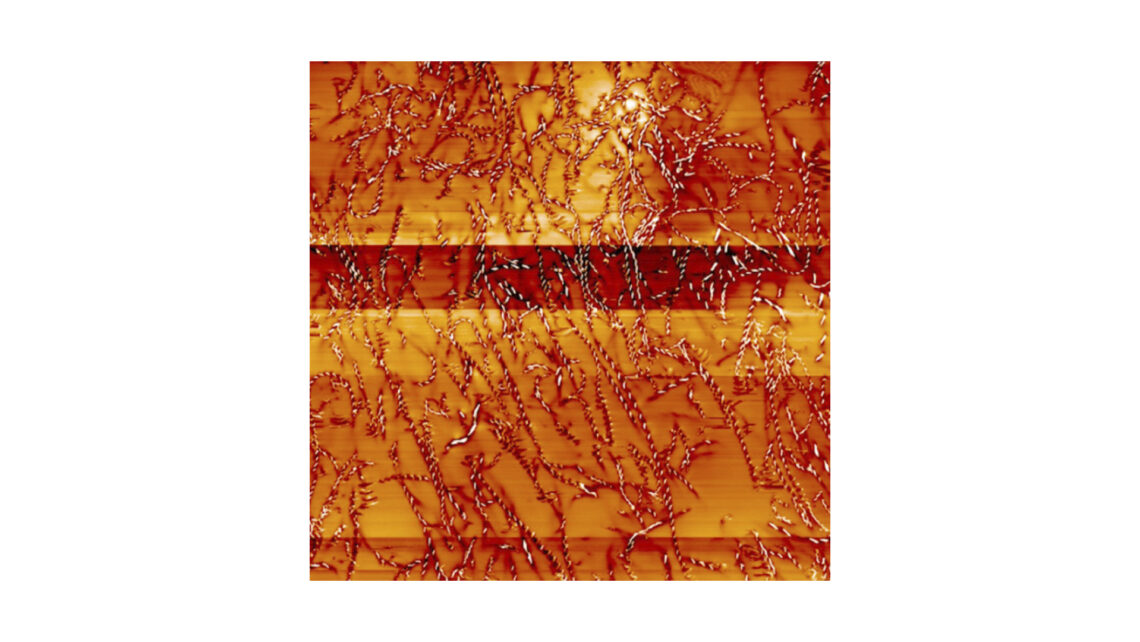
The remarkable performance of lubricating greases is largely attributed to their rheological properties, which determine how they flow and behave under different conditions. Greases exhibit a unique combination of solid-like and liquid-like characteristics, making them both resistant to leakage and highly mobile when subjected to shear forces.
Imagine a grease-filled rolling bearing at rest. In this state, the grease behaves like a solid, preventing it from easily leaking out of the bearing. This is a crucial advantage over using only oil, as it ensures the lubricant remains in place, even in areas where no shear forces are acting, such as on the bearing shoulders, seals and housing.
However, when the bearing starts to rotate, the grease undergoes a remarkable transformation. As it is subjected to shear forces, the grease’s apparent viscosity decreases, allowing it to flow more easily. This shear-thinning behaviour is a result of the grease’s microstructure, which is composed of a network of fibres formed by the thickener molecules.
During the initial “churning” phase of the bearing’s operation, the grease is subjected to substantial shear energy, causing the fibres to align and the network to be temporarily disrupted. This leads to a significant drop in the grease’s viscosity, making it highly mobile and able to flow into the critical areas of the bearing.
As the bearing continues to operate, the grease enters the “bleed” phase, where only a slow, creeping flow takes place. During this phase, the grease’s semi-stationary reservoirs, formed in the unswept areas of the bearing, slowly release the base oil, replenishing the thin lubricating layers in the running tracks. This replenishment is crucial for the bearing’s long life, as it ensures a constant supply of lubricant.
To understand the complex behaviour of lubricating greases, we have developed various models and simulations. One such approach is the use of coarse-grained molecular dynamics, which allows for the study of the interactions between the grease’s components at the mesoscale level. See fig. 2 for an example of the type of systems that we simulate. Note that although only a two-dimensional image is shown, the simulations are three-dimensional.
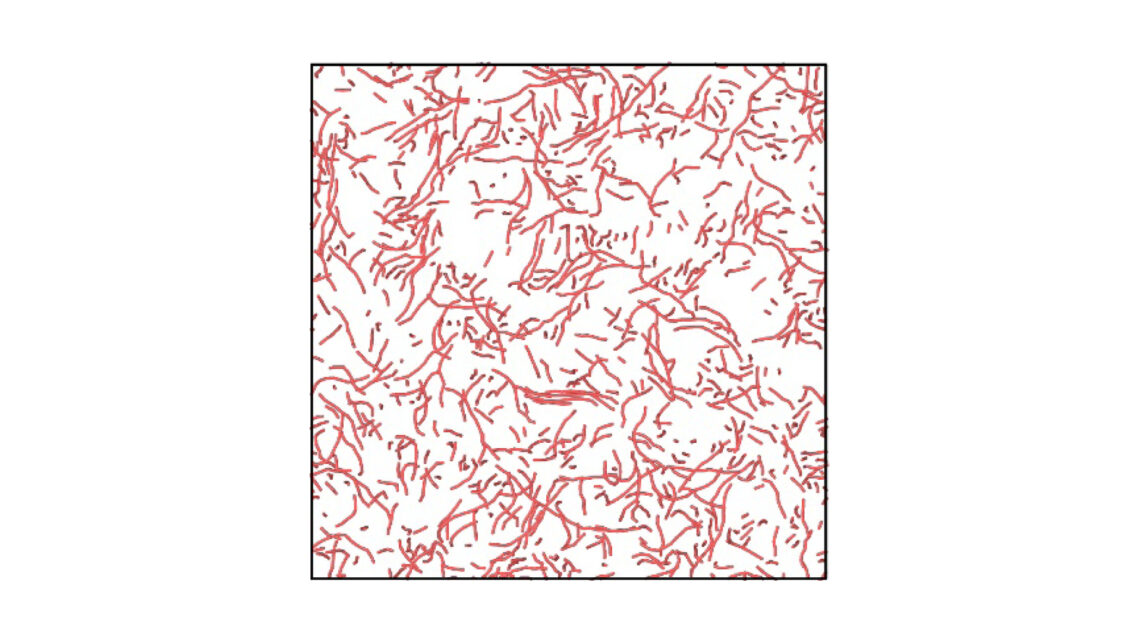
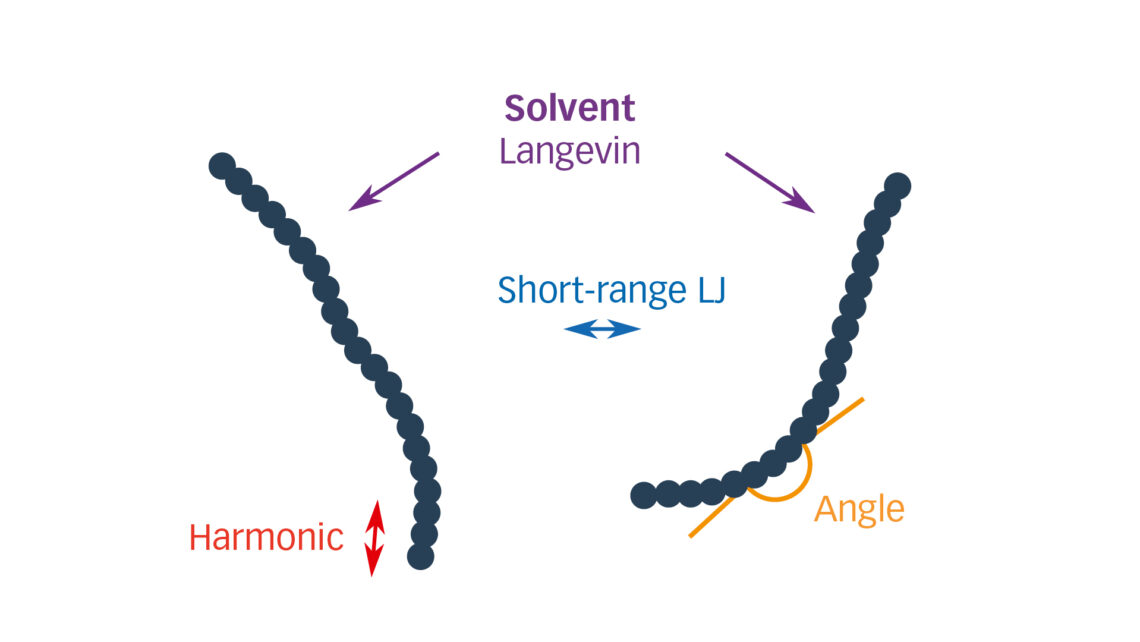
The simulations revealed several fascinating insights. Firstly, we found that longer and stiffer fibres, as well as higher fibre concentrations, tend to align more closely with the direction of the applied shear. This alignment is a result of the fibres’ resistance to deformation, as the stiffer and longer fibres are less likely to collapse or change their orientation under the shear forces.
The simulations also showed that the grease’s viscosity increases with the length, stiffness and concentration of the fibres. This is in line with existing theoretical models, which predict that the presence of non-spherical particles, such as the grease’s fibres, adds resistance to the flow, leading to a higher viscosity (fig. 4).
Interestingly, we were able to delve deeper into the individual behaviour of the fibres. We found that the shear deformation applied to the grease elongates the fibres and increases the tensile stresses within them. While the energy per bond remains constant in the equilibrium state, it rises with the fibre length under shear, making the longer fibres more prone to breaking due to the higher stresses.
We also explored the grease’s behaviour under oscillatory shear, which simulates the dynamic loading conditions experienced in many applications. The simulations showed that both the storage modulus (representing the elastic component) and the loss modulus (representing the viscous component) increase with the length, stiffness and concentration of the fibres, as shown in fig. 5. This is consistent with experimental observations and provides valuable insights into the grease’s viscoelastic properties.
The comprehensive modelling framework developed in this study offers a powerful tool for exploring grease behaviour at time and length scales that are not easily accessible through experiments. While the current findings are primarily qualitative, we anticipate that this approach will serve as a valuable foundation for the development of more advanced grease formulations and the optimization of their performance in various applications.
In conclusion, lubricating greases are remarkable materials that have evolved over centuries, and their complex behaviour continues to fascinate researchers and engineers alike. By unravelling the mysteries of grease rheology through advanced computational modelling, we can gain a deeper understanding of these versatile lubricants and pave the way for the development of even more efficient and reliable solutions for a wide range of industries.