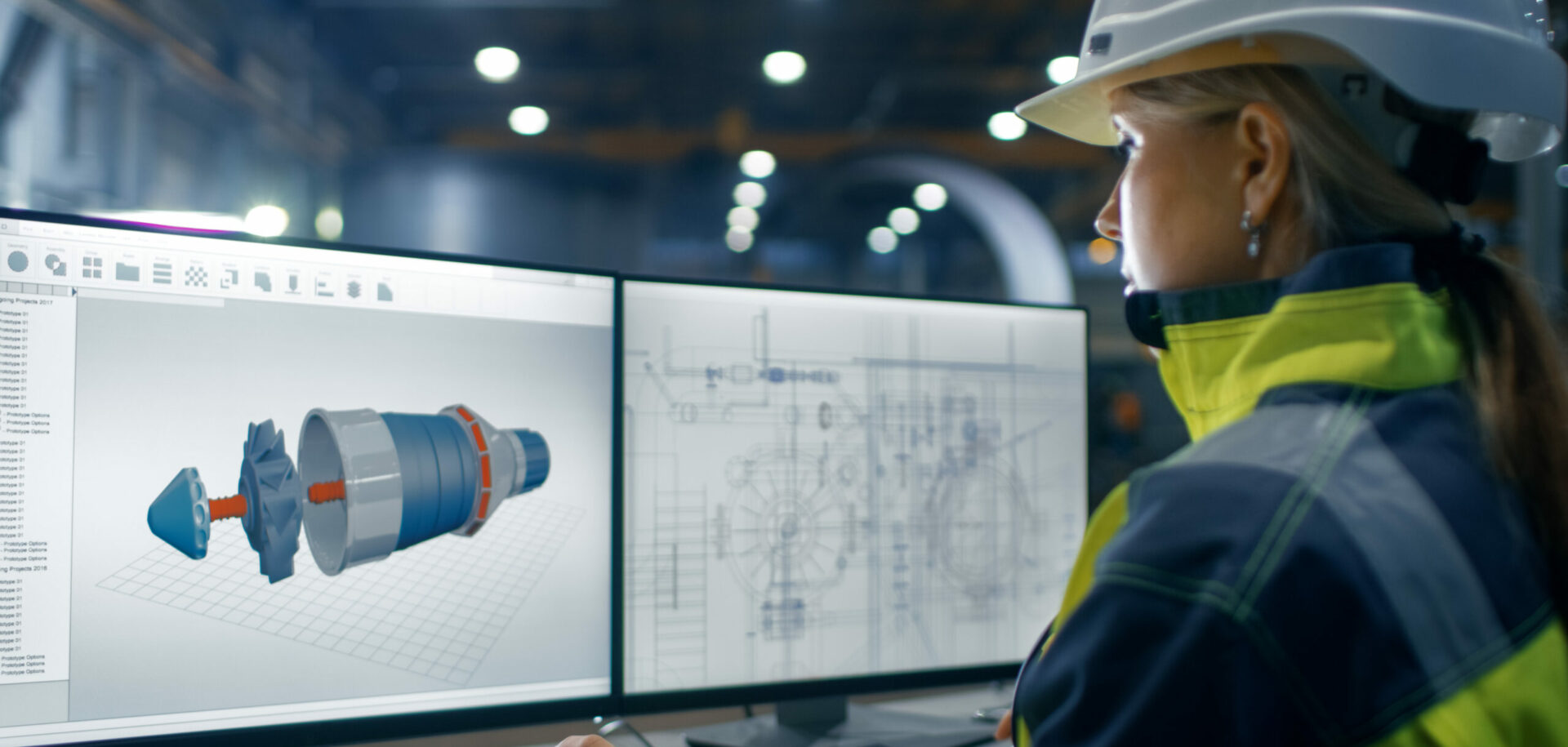
Maintenance works itself out of a job
Summary
Checklist makes you more reliable
Reliability-Centred Maintenance is a process for developing the best policies for managing physical assets.
It ensures that the following seven questions are answered satisfactorily:
- What are the functions and associated desired standards of performance of the asset in its present operating context?
- In what ways can it fail to fulfil its functions?
- What causes each functional failure?
- What happens when each failure occurs?
- In what way does each failure matter?
- What should be done to predict or prevent each failure?
- What should be done if a suitable proactive task cannot be found?
The process produces an asset management strategy that covers safety and environmental issues, as well as equipment performance.
Technologies that predict the future
Asset management professionals use a variety of technologies to monitor the condition of equipment and trend data so that maintenance intervention occurs just in time – never too early or too late. These predictive maintenance technologies include the following: Vibration analysis: Sensors placed at key locations on a machine transmit vibration signals to a computer for analysis. Software identifies faults such as imperfections in a rolling element bearing or a damaged gear tooth so they may be changed prior to machine failure. Infrared thermography: Images captured by portable infrared cameras reveal precise temperature variations in equipment. Temperature anomalies identify potential trouble spots. For example, a hot spot in an electrical cabinet could indicate a loose connection that can be tightened before wiring is damaged by the heat.
Oil and wear particle analysis: Laboratory analysis of lubricating oil taken from industrial machinery can reveal whether an oil change is needed. Analysis of wear particles in the sample can provide information on wear patterns within the machine and possibly point to the failing component.
Electric circuit analysis: Multifunction electrical testing equipment can identify slight abnormalities in motor circuits that are early signs of electrical or mechanical conditions leading to failure.
Precision alignment and balancing:
Relatively small amounts of shaft misalignment – less than half the maximum recommended by the coupling manufacturer – can cut bearing life by 50 percent in some cases. Laser measuring devices speed the alignment of a motor shaft with the shaft of driven equipment.
Information systems: Robust computerised maintenance management systems and enterprise asset management systems provide information to support work planning and scheduling and other asset management decisions. These database applications often integrate with enterprise resource planning systems, manufacturing management systems, and equipment condition monitoring systems.
Scheduled machinery overhauls and quick responses to breakdowns are no longer enough. Now service organisations must attack the root of the problem.Equipment maintenance organisations were once judged for their ability to react quickly to breakdowns and how long it took to get equipment working again. Rigorous adherence to scheduled maintenance tasks prescribed by equipment manufacturers represented top value in maintenance. Troubleshooting and work management skills were important.
Today, though, smart equipment maintenance managers are busy replacing these old values with higher-level paradigms of excellence. These managers are essentially working themselves out of their old jobs and inventing new ones with titles that include terms such as reliability engineering, asset management, asset utilisation, availability management and risk management.
This new breed of manager uses modern technology and analysis techniques to attack the root cause of equipment failures and to eliminate the need for maintenance intervention whenever possible.
Standard maintenance is being put out of business in much the same way that a number of traditional industries are being displaced by the networked global economy. The free flow of information over the Internet has transformed many goods and services into commodities and depressed profit margins. Traditional companies are being forced to reinvent their business model and manufacturing processes.
One of these new business models is the bundling of products and high-technology services into a single offering. Sensors and software in a variety of products, from automobiles to lifts, can now report equipment health to service centres over the Internet using wireless technology.
Physical asset management
Maintenance leaders have re-examined traditional maintenance activities and found that they are really in the physical asset management practice rather than the equipment maintenance practice. Their true mission is to economically manage equipment assets. This new business model adds to profits by reducing costs and increasing return on assets. The asset management approach is of much greater value to the enterprise than simply repairing equipment.
Recent studies have shown that companies can benefit from transforming their maintenance work into effective asset management processes. An Australian study of small and medium-sized manufacturers showed that 58 percent of maintenance work was necessitated by a breakdown and could therefore be classified in the expensive reactive mode; 27 percent was in a preventive or time-based mode; and 15 percent was in a predictive/proactive mode based on results of equipment condition monitoring or root cause analysis.
Several North American studies reflect a similar maintenance work distribution – roughly one-half reactive, one-third preventive and one-sixth predictive/proactive.
According to the Australian study, companies that adopted a strategic asset management policy increased profits by 25 to 60 percent and lowered maintenance costs by 30 percent. There also was a significant increase in productivity and less equipment downtime at these companies.
Although profit-centred asset management produces significant savings over traditional cost-centred maintenance, the real return is from increased plant capacity. A maintenance leader at a chemical company with plants around the world estimated that the productivity increase from its focus on equipment reliability was worth 10 times the potential for cost reduction. The company believes its drive to increase productivity by 10 percent will produce improvements equivalent to US$3.5 billion in capital projects for its chemicals and specialities sector based in the United States.
Two of the organisations leading the way towards proactive asset management are the European Federation of National Maintenance Societies and the Society for Maintenance & Reliability Professionals.
EFNMS, which coordinates maintenance improvement efforts in Europe, has developed a certification programme for maintenance professionals. SMRP is leading the drive to maintenance excellence in North America. One of the member benefits is the opportunity to participate in the society’s benchmarking programme.
Asset management tools
Modern tools of asset management include structured investigation and analysis, open information technology and comprehensive condition monitoring technology.
The most thorough analysis process is Reliability-Centred Maintenance. The process inventories equipment or system functions, identifies possible functional failures and modes of failure, considers the effects and consequences of possible failures, and develops a strategy to ensure equipment operates safely. RCM considers all asset management options, including on-condition tasks, scheduled restoration tasks and run to failure.
Condition assessment technologies such as vibration analysis, infrared thermography, electric circuit analysis, and oil and wear particle analysis provide the basis for on-condition tasks. Data on equipment “health” is gathered with portable instruments or by continuous monitoring systems so corrective actions can be scheduled only when needed.
Information from the different technologies is best used in concert, but it has been difficult because data from each technology is typically delivered in incompatible proprietary formats. This barrier is beginning to crumble under pressure from advocates of open systems. Universal open industry standards for the exchange of equipment information throughout industrial enterprises is under development by the Machinery Information Management Open Systems Alliance (Mimosa).
A Mimosa open system is one in which components are able to communicate and exchange information automatically without any proprietary or supplier-specific interface protocols. More than 200 people representing more than 50 companies around the world have contributed to the Mimosa effort for open information exchange.
The benefits of modern equipment and reliability and asset management initiatives have been documented. Leading companies have made them into a competitive advantage in the new economy. Time may be running out for companies unable to break their old cost-centred maintenance habits and adopt the modern value-adding approach of asset management.
Robert C. Baldwin
editor of Maintenance Technology Magazine