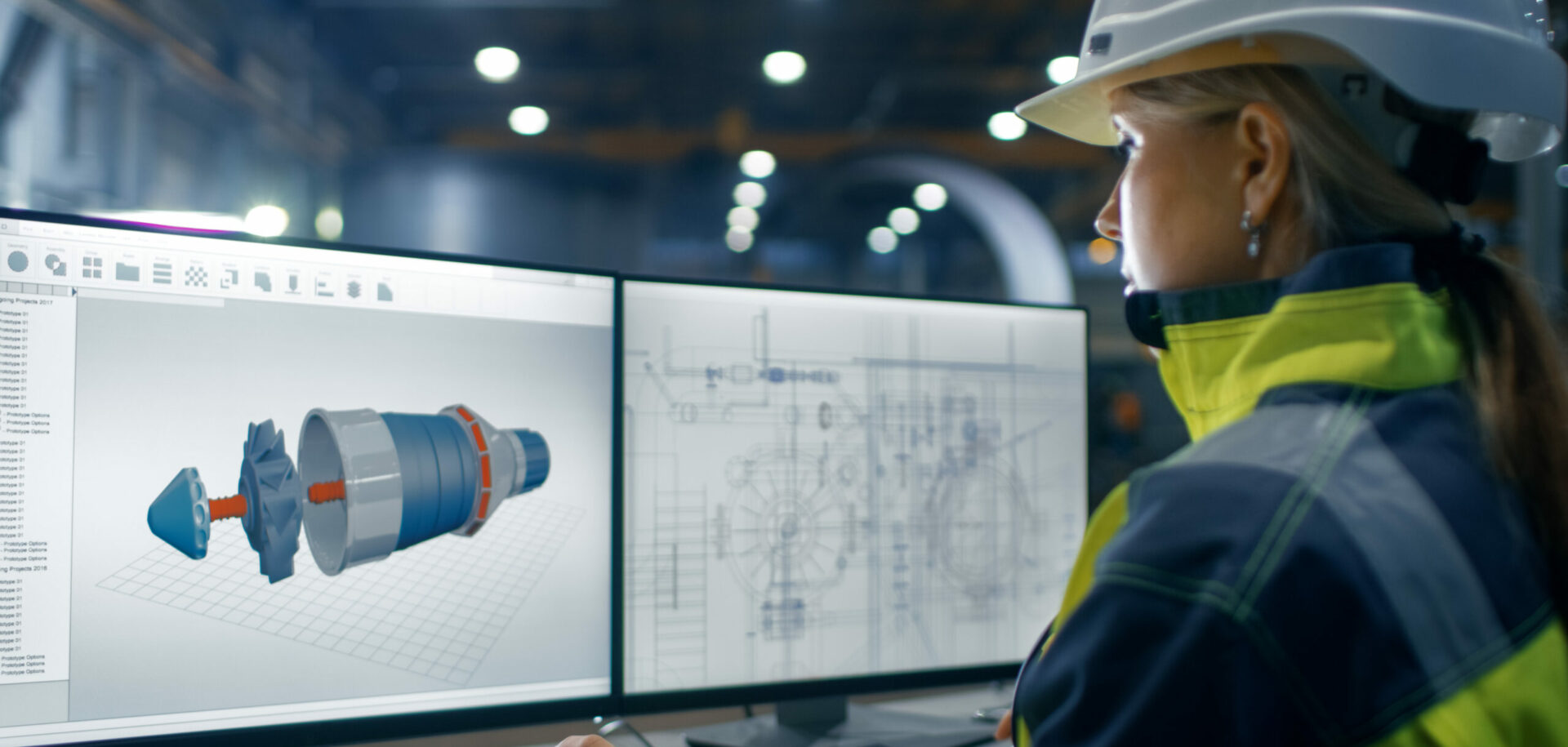
New generation TIH induction heaters
SKF began introducing a new generation of induction heaters with improved features and a more competitive price in November 2004. Developed with the customer’s needs in mind, this new generation of heaters offers features such as a remote control, foldable bearing support arms that combine yoke storage and efficient and reliable power electronics. Induction heaters are best practice when installing a bearing on a cylindrical seating with an interference fit.
The principle of a bearing induction heater can be compared with a transformer using a primary coil with a large number of windings and a secondary coil with a few windings on a mutual iron core.
The input/output voltage ratio is equal to the ratio of the windings, while the
energy remains the same. In the case of induction heaters, the bearing acts as a short circuit (single turn, secondary coil) through which a low AC voltage flows at high amperage, thus generating heat. The heater, the induction coil and the yoke remain at an ambient temperature.
Managing the electric current flow to achieve the most efficient heat-up rate for the bearing is vital, with the application of uniform temperature to the bearing inner ring being very important. SKF induction heaters are programmed to monitor the rate at which the bearing heats up. If the rate is too slow an alarm will activate and stop the heating. This is very useful where the operator may have placed the temperature probe in the wrong location.
Demagnetization at the end of the induction heating cycle is a critical part of the process. The residual magnetic field in the bearing must be decreased to a minimum. Failure to demagnetize completely means a risk of contamination from metal particles attracted to the bearing raceways, which can lead to bearing damage.
Selection of the appropriate heater size is determined through a review of the work piece that would be heated – the shape and dimensions, the mass, the metallurgical characteristics, the required temperature or interference fit to overcome and the frequency of the heating process (number of bearings or work pieces to be heated per day).
The basic elements of an induction heater are the core, the yoke, the induction coil, the control panel, the temperature probe and the body. The performance of the finished product is a function of how well the combination of mechanical and electrical engineering design challenges are met.
Induction heating is recognized as the worldwide best practice for many bearing-mounting operations on cylindrical shafts, as well as for other work pieces such as gears, bushings and bearing housings. The combination of speed, consistency of results, quality and safety has provided an increase in demand for induction heaters worldwide.
The benefits of induction heating are equally valid for the maintenance of
assets within a production operation or for the manufacturing manager who has responsibility for the effective and efficient mounting of bearings or other machine components into new machines or assets (OEM).
Following a review of customer feedback, SKF determined that an upgrade in heater design and performance was required to meet the changing market needs. The decision to develop a new generation of heaters (TIH 030m and TIH 100m) reflected a focus on the customers and their needs as the sole driver for new product innovation. A number of new product features were introduced quickly, without having to compromise on price and functionality.
Within the product development process, a design decision was made to apply a “platform concept” approach. In doing this, SKF could introduce a number of products from the same design and manufacturing base. This speeds up time to market, allowing innovations to be incorporated into more products as well as enabling greater commonality of parts across individual products. In addition, large-size custom heaters (for work pieces up to a few tonnes) are available on request.
The novelty of SKF’s new generation of induction heaters is that a number of important features, such as reliable remote control communication and power electronics, a separate electronics box and the m20 concept (see box), have been combined in one product that is portable, easy-to-use and safe.
Reliable remote control communication
Both the TIH 030m and the TIH 100m are equipped with a remote control panel that provides reliable remote control communication with the main unit, which is not influenced by the electromagnetic field generated by the heater. This means that the heater is not prone to the variability (seen as failure in function) that is often the case, for products with remote control that are required to work within an electromagnetic environment.
Power electronics
The power electronics has been further improved for the highest reliability, which has been achieved through good electronic engineering and component selection. Key features include accurate electric current control, cut-outs to avoid overheating, controls on rate of temperature increase and minimum heating rate.
Separate electronics box
Separating the electronics box from the body of the heater (where the core, induction coil and yoke are situated) was a design decision made to improve long-term heater reliability. The separate electronics unit enables the electronics to operate at low temperatures, thus improving component and system reliability and performance. This means costly design features present on earlier models of heaters, such as a cooling fan, are no longer necessary.
Portability
At a weight of 21 kg the TIH 030m is portable and can be easily moved from the workshop to the mounting job. At 42 kg, the TIH 100m heater cannot be considered as manually portable but for the weight of work piece it can heat, the TIH 100m does represent a very viable option for being transported to the work piece, rather than having to bring the workpiece and all other components to the workshop.
Health and safety
All SKF heaters are compliant to the latest stringent European safety norms. However, SKF has taken a number of additional steps towards offering the safest possible product to the market.
- Remote control panel Exposure to the low electromagnetic field generated by the heater should be limited as much as possible, and not only to the
required level. Similarly, the risk of exposure to the hot work piece should also be minimized. Which is why the new generation TIH heaters incorporate a remote control panel to operate the heater further away from the hot work piece, as well as from the low level electromagnetic field generated by the heater. - Foldable bearing support arms Safety considerations were also a key input in the decision to design a heater with foldable bearing support arms, thus enabling a much more stable work platform. If a 100 kg bearing at 110 °C (230 °F) falls off a heater, it can represent a major problem.
m20 concept
The decision to maintain the m20 designation format for heaters with the new generation TIH induction heater range was easy. The m20 concept is now well accepted and seen as a useful quantitative measure for induction heater performance. Rather than identifying the maximum bearing size that can be heated, SKF prefers to identify the maximum weight that can be heated in 20 minutes, which is seen as efficient use of operator time as well as an indicator of heater power output.
SKF addressed the issue of ease of assembly, to make sure the economic benefits of design would show in the price for the finished product. Ease of maintenance, if at all required, was another criterion taken into account in the design phase for the product. This is supported by the clear instructions for use, covering all elements of health and safety in operating the heater. In total, these combine to make the new generation of induction heaters from SKF state-of-the-art products for the maintenance or manufacturing professional.
Definition of “m20”
The “m20” is defined as the weight (kg) of the heaviest spherical roller bearing in the 231 series that can be heated from 20 to 110 °C in 20 minutes. Selection of the 231 series bearing reflects a commonly fitted type, with an average bore and cross-section configuration. Such an approach provides a quantitative measure for heater performance and also acts as an easy-to-understand descriptor for power output of the heater. The new heater number designation relates to its m20, with the m20 of 97 kg for the TIH 100m and m20 of 28 kg for the earlier TIH 030m seen within their designations.
Key reasons to heat a bearing:
- Hot mounting for expansion of the bearing bore to overcome the interference fit when mounting a bearing directly on a cylindrical shaft.
- Safe mounting, e.g., excluding the use of potentially dangerous cold mounting with a press.
- An alternative to the often inappropriate cold mounting techniques, such as hammering on the outer ring of the bearing.
Safe and efficient
Induction heating is a very efficient and safe manner of heating a bearing. The alternatives are:
-
Heating in an oven. While usually a low-cost option after the initial high investment for an oven is made, it is time- and energy-consuming. Overall, the process is inefficient and causes an increase in operating costs.
-
Heating in an oil bath. This is a time- and energy-consuming option, with the additional problem of making sure all the heating oil is out of the bearing. Furthermore, if the oil is not clean (very often the case), then the bearing will be contaminated prior to mounting. This is unacceptable because it can lead to premature bearing failure. The process is potentionally dangerous, due to the combination of fire and oil and the potential for oil spills that could make the workplace unsafe. These disadvantages are in addition to the more general considerations of the health and fire risks.
- Heating with an open flame. This is unacceptable as heat absorption and dissipation is highly uneven and can result in geometrical deformation of the bearing. Furthermore, local overheating can create metallurgical composition modification of the bearing, and these defects could lead to premature failure.