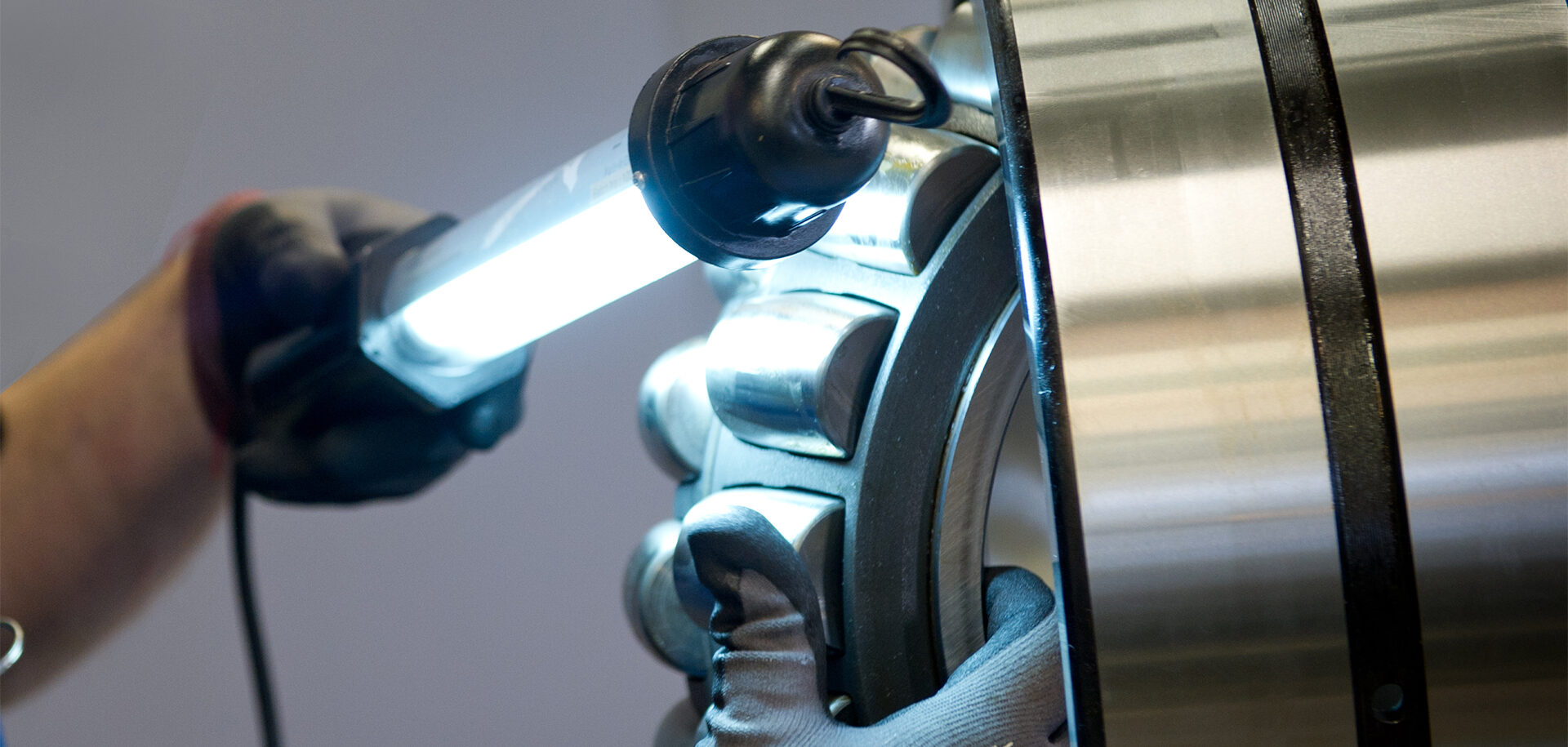
Анализ повреждений подшипников См. стандарт ISO 15243
Возможность выявлять виды отказов и причины повреждения подшипников качения — первый шаг на пути к предотвращению повторных повреждений и повышению надежности оборудования.
Подшипники — один из наиболее распространенных компонентов современного промышленного оборудования. Они соединяют вращающиеся детали (валы) с неподвижными компонентами (корпуса) с минимальным трением. Подшипники обеспечивают плавную работу оборудования, от автомобилей и воздушных судов до генераторов, конвейеров, печатных машин и любого оборудования или техники с вращающимися компонентами.
Специалисты, работающие с промышленной техникой, должны хорошо понимать принципы функционирования подшипников, а также причины их преждевременного выхода из строя.
Учитывая это, Международная организация по стандартизации (ISO) опубликовала стандарт ISO 15243, предоставляющий классификацию различных типов неисправностей подшипников качения. Для каждого типа неисправности в стандарте описаны характеристики, внешние проявления и возможные причины. Последняя редакция стандарта опубликована в 2017 г.
Важно не только знать характеристики и внешние проявления типа неисправности, но также понимать причины ее возникновения. Это позволяет использовать рекомендации по корректирующим мероприятиям, которые помогают избежать неисправностей в будущем. Разумеется, если подшипник эксплуатируется до отказа и происходит его заклинивание, выяснить тип и причины неисправности невозможно.
В данной статье представлен отчет по типам неисправностей ISO для подшипников качения с указанием их причин. Но сначала немного основных сведений.
Основные сведения о подшипниках
Подшипники качения — это детали машин высокой точности, выполненные из легированной подшипниковой стали и, в большинстве случаев в настоящее время, с керамическими элементами качения. Подшипник состоит из внутреннего и наружного колец, шариков или роликов и дополнительно закрыт уплотнениями или защитной шайбой. На рисунке 1 показаны общие компоненты подшипника качения. Герметичные подшипники заполняют смазкой производители. Смазочные материалы (консистентная смазка, масло) играют важнейшую роль при создании пленки необходимой толщины для отделения вращающихся компонентов от дорожек качения. Необходимо выбирать подшипники специально под оборудование, размещать и устанавливать их должным образом. Подшипники должны быть хорошо смазаны и не подвержены загрязнению. При обнаружении признаков повреждений важную роль играет правильное представление о внутренней геометрии подшипников и принципах их работы.
Причины неисправности
Что препятствует правильной работе подшипника и ведет к его поломке?
Также важно (вероятно, даже более важно) понимать причины неисправности, а не просто определять ее тип.
На этот вопрос возможны различные ответы в зависимости от того, кому задается вопрос. Компания SKF часто проводит проверки подшипников и анализ их повреждений как для клиентов, так и в собственных целях. Результаты анализа SKF добавляются в облачное ПО — инструмент отчетности по результатам анализа подшипников Bearing Analysis Reporting Tool (BART). Вместе с оценкой других данных отслеживаются причины вывода подшипников из эксплуатации. Эти данные позволяют компании SKF получить некоторые ответы на следующий вопрос: почему подшипник перестает работать?
Результаты анализа данных показывают, что чаще всего подшипники выходят из строя из-за чрезмерной вибрациий и шума. Подшипники также выводят из эксплуатации для проведения техобслуживания оборудования или при воздействии экстремальных температур (fig. 2).
Классификация типов неисправности по ISO 15243 при эксплуатации подшипников
ISO 15243: 2017 [см. 1 ] классифицирует типы неисправностей, возникающих после установки подшипника в узел/оборудование и во время эксплуатации, за исключением таких дефектов производства, как недостающие детали. Типы неисправностей по ISO разделяются на шесть категорий: контактная усталость, износ, коррозия, электрическая эрозия, пластическая деформация и трещины и сколы (fig. 4). Для более точной классификации типов неисправностей каждая из этих категорий включает несколько подкатегорий.
Нумерация (например 5.1.2) классификации основана на ISO 15243, глава 5.
Справочник «Повреждение подшипника и анализ неисправностей»[ссылка 2] можно использовать для определения типа и причины поломки подшипников.
Далее подробно описаны шесть классификаций:
Контактная усталость (ISO 5.1)
Контактная усталость включает две подкатегории: подповерхностная и поверхностная усталость. Подповерхностная усталость (ISO 5.1.2) (рис. 5). Причины — циклическая нагрузка контактных поверхностей, которая со временем вызывает изменение структуры материала, что ведет к образованию микротрещин. Микротрещины образуются под поверхностью, часто в посторонних включениях в материале, и распространяются на поверхность в виде сколов. На усталость влияет качество подшипников, прилагаемые нагрузки, смазка и чистота. То же самое относится к расчетному сроку службы подшипника, L10mh. Подповерхностная усталость усиливается, если подшипник подвергается высоким нагрузкам, например, при временной перегрузке или в результате других явлений, которые вызывают ослабление материала. В таких случаях срок службы сокращается (на 5–10 % от L10mh). Поверхностная усталость (ISO 5.1.3) (рис. 6) — усталость поверхности качения. Обычно возникает из-за дефектов поверхности в результате плохой смазки или недостаточной чистоты. Недостаточный слой смазки и чрезмерное загрязнение твердыми частицами может привести к контакту металлических поверхностей, что ведет к появлению неровностей, которые смещают друг друга. В дальнейшем возможно появление микротрещин, затем микросколов и, наконец, поверхностной усталости.
Износ (ISO 5.2)
Следующая категория — износ. В ISO износ разделяется на две подкатегории: абразивный и адгезионный износ. Абразивный износ (ISO 5.2.2) (рис. 7) представляет собой постепенный съем материала, обычно при наличии абразивного материала, например загрязняющего вещества, содержащего твердые частицы. Абразивный износ также может возникнуть при недостатке смазки. Как правило, абразивный износ характеризуется тусклым внешним видом поверхности. Абразивный износ — процесс деградации, который обычно разрушает микрогеометрию поверхностей качения подшипников. Абразивные частицы могут быстро изнашивать дорожки качения колец и тела качения, а также выемки в сепараторах. Причиной абразивного износа может быть проникновение загрязненного материала в смазку и подшипник и недостаток смазки в контакте качения.
Коррозия (ISO 5.3)
Следующая категория, коррозия, включает три категории: коррозия в результате воздействия влаги, фрикционная коррозия и ложное бриннелирование. Коррозия в результате воздействия влаги (5.3.2) (рис. 9) — это классическая проблема проникновения влаги внутрь подшипника. Легированный материал подшипников отличается низкой коррозионной стойкостью. Влага может стать причиной повреждения поверхности между телами качения, когда подшипник находится в неподвижном состоянии. Повреждение поверхности может вызывать поверхностную усталость при последующей работе. Влага в основном препятствует образованию пленки смазочного материала в работающем подшипнике. Фреттинг-коррозия (ISO 5.3.3.2) (рис. 10) происходит в ходе микроперемещений на месте сопряжения между контактирующими поверхностями, например между внутренним кольцом подшипника и валом и между наружным кольцом подшипника и корпусом. Причиной может быть неправильная установка подшипника на вал или в корпус в зависимости от прилагаемой нагрузки. Так, подшипник с вращающимся внутренним кольцом при равномерно прилагаемой нагрузке во избежание фреттинг-коррозии требует некоторой минимальной фрикционной посадки внутреннего кольца на вал. Аналогично подшипник с вращающимся внутренним кольцом и прилагаемой к этому кольцу нагрузкой во избежание фреттинг-коррозии требует некоторой минимальной фрикционной посадки наружного кольца подшипника в корпусе. Фреттинг-коррозия проявляется в виде красно-коричневатого окисления в месте сопряжения. Ложное бриннелирование (ISO 5.3.3.3) (fig. 11) происходит в контактной области между телами и дорожкой качения при воздействии мелких колебательных движений или вибрации. Изнашивается поверхность между телами качения. При износе нарушается исходная производственная обработка поверхностей; на поверхности возможно образование красно-коричневых следов окисления, аналогичных окислению при фреттинг-коррозии. Объем износа зависит от интенсивности прилагаемой нагрузки, интенсивности колебаний и вибрации и состояния смазки.
Электрическая эрозия (ISO 5.4)
Электрическая эрозия бывает двух типов: эрозия из-за высокого тока и эрозия из-за утечек тока. Эрозия из-за высокого тока (ISO 5.4.2) (рис. 12) происходит, когда ток проходит через одно кольцо подшипника, тела качения и другое кольцо подшипника. На поверхностях контакта процесс подобен электродуговой сварке (высокая плотность тока на малой контактной поверхности). Материал нагревается до температуры отпуска и далее до уровня плавления. Это ведет к появлению обесцвеченных областей различного размера, в которых произошел отпуск, повторная закалка или расплавление материала. В местах плавления материала и образуются кратеры с последующими сколами из-за вращения подшипника. Избыток материала истирается. Причиной эрозии из-за высокого тока могут быть удары молнии по оборудованию, ремонт сварных швов с неправильным заземлением сварочного оборудования и др. Эрозия из-за утечек тока (ISO 5.4.3) (рис. 13) происходит, когда через подшипник проходит ток малой интенсивности. Повреждения обычно представляют собой маленькие, расположенные рядом друг с другом кратеры. С течением времени появляются серые участки изношенного материала. Тела качения становятся серыми и тусклыми, а смазка может обесцвечиваться. Степень повреждения зависит от интенсивности тока, продолжительности, нагрузки на подшипник, частоты его вращения и смазки. Эрозия из-за утечек тока — обычное явление в электродвигателях с паразитными токами в случае, если вал неправильно заземлен и двигатель управляется с помощью частотно-регулируемого привода.
Пластическая деформация (5.5)
ISO подразделяет пластическую деформацию на две категории: деформация в результате перегрузки и вмятины от воздействия частиц. Деформация в результате перегрузки (ISO 5.5.2) (рис. 14) — механическая неисправность в результате статической перегрузки, например, при неправильном проведении погрузочно-разгрузочных работ (падение подшипников с высоты), неправильного монтажа (удары молотком по подшипнику), пиковые нагрузки при работе оборудования и др. Деформация может проявляться в виде вмятин на дорожках качения или бороздок на поверхности между телами качения, повреждений сепараторов, уплотнений и экранов и пр. Вмятины от воздействия частиц (ISO 5.5.3) (рис. 15) возникают, когда твердые частицы (в загрязнениях или в результате износа) перекатываются в контактной области качения подшипника, создавая тем самым вмятины (деформации) в дорожках и телах качения. На объем повреждений влияют размер, тип и твердость частиц. Дальнейшее перекатывание частицы по вмятинам может привести к поверхностной усталости (ISO 5.1.3).
Трещины и сколы (ISO 5.6)
Последняя категория по ISO — трещины и сколы. Эта категория включает три подкатегории: деформация в результате перегрузки, усталостное растрескивание и термическое растрескивание. Деформация в результате перегрузки (ISO 5.6.2) (рис. 16) возникает в случаях, когда нагрузки превышают предел прочности материала на разрыв. Общими причинами деформации считаются слишком высокое центробежное растягивающее усилие, связанное с установкой подшипника на валу с избыточной фрикционной посадкой, или привод подшипника с коническим отверстием, смещенным относительно конического уплотнения вала или монтажной втулки. Усталостное растрескивание (ISO 5.6.3) (рис. 17) происходит при превышении предела усталости под воздействием циклического изгиба. Многократный изгиб приводит к образованию трещины в кольце или сепараторе. Такая ситуация возможна в подшипнике, если к нему прилагаются большие усилия, а корпус не обеспечивает равномерного распределения жесткости, при этом наружное кольцо подвергается воздействию высоких циклических нагрузок. Термическое растрескивание (ISO 5.6.4) (рис. 18) происходит, когда две поверхности скользят относительно друг друга и в результате трения выделяется тепло. В случае значительного скольжения локальная повторная закалка поверхностей в сочетании с созданием высоких остаточных растягивающих усилий вызывает образование трещин, которые обычно располагаются перпендикулярно направлению скольжения. Термическое растрескивание возможно, если, например, неподвижный корпус контактирует с вращающимся кольцом подшипника.
Подробное описание типов и причин неисправностей подшипников см. в разделе «Литература» (2).
Учтите, что пробы смазочного материала (масло или смазка) из подшипников также помогают тщательно анализировать результаты исследования. Образцы смазки отбираются для сравнения с образцом новой смазки. Можно провести анализ смазочного материала, чтобы учесть содержание твердых частиц и влаги, изменение вязкости, изменение консистенции и т. д.
Также полезную информацию можно получить по результатам проверки уплотнений или экрана подшипника и других компонентов, например втулки.
Такие методы профилактического обслуживания или обслуживания на основе контроля состояния, как анализ вибраций, термический анализ, анализ масла и др., можно использовать для выявления неисправностей до возникновения серьезных повреждений подшипников, а также возможных неисправностей оборудования при работающем подшипнике. Это помогает эффективнее выявлять неисправности. Вывод из эксплуатации крупногабаритных подшипников (диаметр отверстия > 200 мм) до возникновения серьезных неисправностей позволяет восстанавливать такие подшипники. Подшипник можно восстановить до состояния «как новый», снизив расходы на обслуживание и воздействие на окружающую среду (fig. 19).
Наиболее распространенные типы неисправностей
Компания SKF определила1 пять наиболее распространенных типов неисправностей по ISO: абразивный износ (26 %), поверхностная усталость (16 %), коррозия в результате воздействия влаги (14 %), адгезионный износ (7 %) и эрозия из-за утечек тока (7 %) (fig. 20). На эти типы неисправностей приходится около 70 % всех неисправностей, выявленных при анализе подшипников, но у большинства подшипников отмечается фреттинг-коррозия, хотя и незначительная. Другие типы неисправностей по ISO отмечаются в меньшей степени.
Инструмент SKF Bearing Analysis Reporting Tool (BART)
Программное обеспечение SKF BART разработано инженерами SKF и теперь доступно для клиентов SKF. Клиентам предоставляется базовый учебный курс по подшипникам, методам осмотра подшипников и использованию ПО SKF BART. В тесном сотрудничестве с инженерами по применению или специалистами компании SKF клиенты готовят отчеты о результатах осмотра. Отчет по результатам осмотра BART утверждается экспертом SKF. В ходе осмотра можно определить, требуется ли замена подшипника, можно ли его повторно использовать, подлежит ли подшипник восстановлению или утилизации. Отчет также можно использовать для документирования проверки новых подшипников перед тем ,как ввести их в эксплуатацию. Отчет полезен в случае долговременного хранения подшипников на складе.
При необходимости инженеры по применению компании SKF могут провести полный анализ повреждений подшипников и предоставить рекомендации для повышения надежности. Инженеры SKF могут дополнительно использовать искусственный интеллект (AI) [ссылка 3] при проведении анализа повреждений подшипников. Искусственный интеллект использует систему компьютерного зрения, которая способна оценивать повреждение подшипников с помощью цифровой фотографии. Система применяет искусственный интеллект в виде нейтронной сети с алгоритмом распознавания изображений, обученную на основе тысяч изображений поврежденных подшипников из архивов компании SKF.
Заключение
В заключение можно отметить, что для классификации типов неисправностей работающих в оборудовании подшипников качения используется стандарт ISO 15243, который также помогает выявлять причины неисправностей. Знание типовых неисправностей подшипников и причин их возникновения позволяет предпринять корректирующие действия для избежания повторения отказов. Такой подход помогает значительно уменьшить риск возникновения катастрофических поломок и потенциально повысить надежность и доступность оборудования. Во время проведения обслуживания подшипники можно оценить на предмет их повторного использования или возможности восстановления.
Чтобы изучить и получить лучшее представление о работе подшипников, выполняется сбор данных о типах и причинах неисправностей подшипников и других связанных с этим сведений. Компания SKF применяет ПО SKF BART, которое позволяет клиентам проводить инспекцию подшипников и составлять отчеты о причинах неисправностей.
1 Инструмент SKF Bearing Analysis Reporting Tool
Литература
[1.] Международный стандарт ISO 15243:2017, «Подшипники качения. Повреждения и отказы. Термины, характеристики и причины»
[2.] Брошюра SKF 14219, «Повреждение подшипника и анализ неисправностей»
[3.] Статья SKF Evolution, The future of bearing failure analysis is here («Будущее анализа неисправностей подшипников уже здесь»), 2022 г.