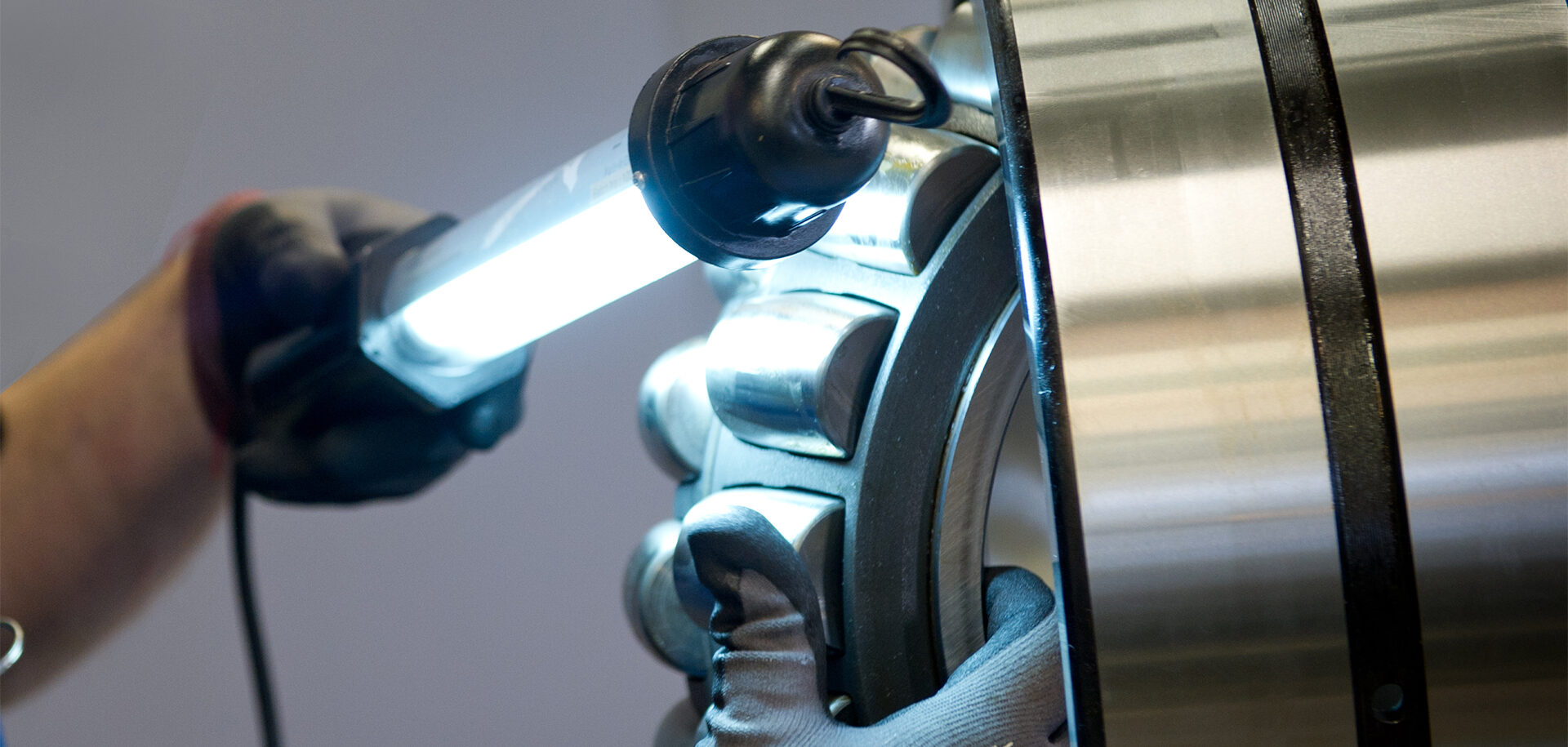
Analyse des détériorations de roulements : laissez-vous guider par la norme ISO 15243
Pour éviter qu'une détérioration de roulement ne se reproduise et améliorer ainsi la fiabilité d'une machine, la première étape consiste à identifier le mode de défaillance et les causes de cette défaillance.
Les roulements font partie des composants les plus courants dans les machines industrielles modernes. Ils assurent la liaison entre la partie tournante (arbre) et la partie fixe (palier) avec un frottement minimal. Ils contribuent au bon fonctionnement de machines diverses, des voitures et avions aux générateurs, convoyeurs, presses à imprimer en passant par tout type de machines ou équipements tournants.
Les personnes qui travaillent avec des machines industrielles ont tout intérêt à mieux comprendre le fonctionnement de celles-ci et les causes des défaillances précoces parfois observées.
C’est ce qui a conduit l’Organisation internationale de normalisation (ISO) à publier la norme ISO 15243, qui fournit une classification des différents modes de défaillance des roulements. Pour chaque mode de défaillance, la norme décrit les caractéristiques, l’aspect et les causes possibles de la défaillance. La version la plus récente de la norme a été publiée en 2017.
En plus de pouvoir identifier les caractéristiques et l’aspect d’un mode de défaillance, il est important de comprendre ce qui a causé cette défaillance. Ces connaissances permettent de recommander des mesures correctives pour éviter de nouvelles détériorations à l’avenir. Bien entendu, si le roulement est utilisé jusqu’à la défaillance (RTF) et qu’un grippage se produit, l’identification du mode et des causes de défaillance peut s’avérer impossible.
Une synthèse des modes de défaillance ISO des roulements et de leurs causes est fournie ci-après. Ces informations restent cependant basiques.
Notions de base sur les roulements
Les roulements sont des pièces mécaniques de haute précision fabriquées en acier pour roulements de dureté élevée avec, de plus en plus souvent aujourd’hui, des éléments roulants en céramique. Un roulement comporte une bague intérieure et une bague extérieure, des billes ou des rouleaux, une cage et, éventuellement, des joints ou un flasque. La Figure 1 illustre les éléments constitutifs courants d’un roulement. Les roulements avec étanchéités intégrées sont garnis de graisse en usine. La lubrification, qu’elle soit à la graisse ou à l’huile, est essentielle pour permettre la formation d’un film lubrifiant suffisamment épais pour séparer les éléments roulants des chemins de roulement. Le roulement doit être spécialement adapté à la machine, correctement monté et ajusté sur celle-ci, lubrifié de manière adéquate et exempt de contamination. La recherche de signes de détérioration nécessite de solides connaissances sur la géométrie interne du roulement et sur le fonctionnement attendu de celui-ci.
Causes de défaillance
Qu’est-ce qui empêche un roulement de fonctionner correctement et entraîne sa défaillance ?
Au-delà de la compréhension du mode de défaillance, il est également important, voire plus important, de comprendre la cause de la défaillance.
La réponse à cette question peut varier en fonction de la personne à qui vous la posez. SKF réalise de nombreuses inspections de roulements et analyses de détériorations pour ses clients et pour son propre compte. Les conclusions de ces recherches sont documentées dans un logiciel basé sur le cloud, le Bearing Analysis Reporting Tool (BART) (outil de rapports d’analyse de roulements). Cet outil permet de consigner les motifs pour lesquels les roulements sont mis hors service et les causes sous-jacentes, parmi d’autres données. Toutes ces informations permettent à SKF d’apporter des réponses à la question : pourquoi un roulement ne fonctionne-t-il plus ?
Les données révèlent que la plupart des roulements sont retirés en raison de vibrations et de bruits excessifs. Les roulements sont également démontés lorsque la machine fait l’objet d’une intervention de maintenance ou lorsqu’une température excessive est relevée (Fig. 2).
Classification des modes de défaillance pendant le fonctionnement du roulement selon ISO 15243
ISO 15243: 2017 [Réf.1 ] classe les modes de défaillance survenant lorsque le roulement est installé sur l’équipement/machine et en cours de fonctionnement, ce qui signifie que les défauts de fabrication, comme des pièces manquantes par exemple, ne sont pas inclus. Les modes de défaillance ISO se répartissent en six catégories : fatigue de contact de roulement, usure, corrosion, électroérosion, déformation plastique, fissuration et rupture (Fig. 4). Chacune est elle-même divisée en sous-catégories pour une classification plus spécifique des modes de défaillance.
La numérotation (par exemple 5.1.2) des classes des modes de défaillance suit celle du chapitre 5 de la norme ISO 15243.
Le guide Analyse des détériorations et défaillances de roulements [Réf.2] peut être utile pour identifier les modes de défaillance des roulements et leurs causes.
Les six classes se définissent comme suit :
Fatigue de contact de roulement (ISO 5.1)
La fatigue de contact de roulement comprend deux sous-catégories : fatigue initiée en sous-couche et fatigue initiée en surface. La fatigue initiée en sous-couche (ISO 5.1.2) (Fig. 5) est causée par la charge cyclique exercée sur les surfaces de contact de roulement qui, au fil du temps, entraîne un changement structurel du matériau conduisant à l’apparition de micro-fissures. Les micro-fissures se forment sous la surface, souvent au niveau d’une inclusion dans le matériau, et se propagent vers la surface où elles provoquent un écaillage. La fatigue dépend de la qualité du roulement, des charges appliquées, de la lubrification et de la propreté. C’est ce que reflète la durée nominale du roulement, L10mh. La fatigue initiée en sous-couche peut s’accélérer en présence de contraintes élevées dues, par exemple, à une surcharge temporaire ou à un autre événement fragilisant le matériau. Dans de tels cas, la durée de vie en fatigue est courte (5 à 10 % de L10mh). La fatigue initiée en surface (ISO 5.1.3) (Fig. 6) est une fatigue provoquée en surface du roulement par une dégradation de celle-ci due à une mauvaise lubrification ou un défaut de propreté. Une épaisseur du film lubrifiant insuffisante et le passage des éléments roulants sur des contaminants solides peuvent conduire à un contact métal sur métal, entraînant un cisaillement des aspérités de surface les unes sur les autres. Des micro-fissures peuvent ensuite apparaître, puis des micro-écaillages, et enfin une fatigue initiée en surface.
Usure (ISO 5.2)
La catégorie suivante est l’usure. L’usure selon la norme ISO comprend deux sous-catégories : usure par abrasion et usure par adhésion. L’usure par abrasion (ISO 5.2.2) (Fig. 7) est l’enlèvement progressif de matière, généralement en présence de matière abrasive comme des particules solides. Une usure par abrasion peut également survenir en raison d’une lubrification inappropriée. L’usure par abrasion se caractérise généralement par un aspect mat des surfaces. L’usure par abrasion est un processus de dégradation qui peut mener à la destruction de la microgéométrie des surfaces de roulement d’un roulement. Des particules abrasives peuvent causer une usure rapide des pistes des bagues, des éléments roulants, ainsi que des alvéoles de la cage. L’usure par abrasion peut être causée par la pénétration de corps étrangers dans le lubrifiant et le roulement, et par l’absence de lubrifiant dans le contact de roulement.
Corrosion (ISO 5.3)
La catégorie suivante, la corrosion, comprend trois sous-catégories : la corrosion due à l’humidité, la corrosion par frottement et le faux effet Brinell. La corrosion due à l’humidité (5.3.2) (Fig. 9) est un problème classique lié à l’infiltration d’humidité dans le roulement. Le matériau du roulement présente une dureté élevée mais une faible résistance à la corrosion. L’humidité causera des détériorations entre les éléments roulants pendant les périodes statiques. Cette détérioration de la surface peut entraîner lors de la période de fonctionnement suivante une fatigue initiée en surface. L’humidité compromet grandement la formation d’un film lubrifiant d’épaisseur suffisante dans un roulement en fonctionnement. La corrosion de contact (ISO 5.3.3.2) (Fig. 10) se produit en cas de micromouvements oscillatoires des surfaces de glissement associées, par exemple entre la bague intérieure du roulement et l’arbre ou entre la bague extérieure du roulement et le logement. Elle peut être due à un montage incorrect du roulement sur l’arbre ou dans le logement, en fonction de la charge appliquée. Par exemple, un roulement avec bague intérieure tournante soumis à une charge appliquée fixe exige un ajustement serré minimum de sa bague intérieure sur l’arbre pour éviter la corrosion de contact. De même, un roulement avec bague intérieure tournante et une charge tournante appliquée sur la bague intérieure exige un ajustement serré minimum de sa bague extérieure sur l’arbre pour éviter la corrosion de contact. La corrosion de contact se présente sous l’aspect d’une oxydation rouge/noirâtre dans l’interface. Le faux effet Brinell (ISO 5.3.3.3) (Fig. 11) se produit dans la zone de contact entre les éléments roulants et le chemin de roulement en raison de micromouvements ou de faibles vibrations. Cette usure apparaît entre les éléments roulants. Elle élimine les finitions de surface d’origine et peut également prendre l’aspect d’une oxydation rouge/noirâtre sur les surfaces, à l’instar de la corrosion de contact. Le degré d’usure dépend de l’intensité de la charge appliquée, des oscillations et des vibrations, ainsi que des conditions de lubrification.
Électroérosion (ISO 5.4)
L’électroérosion comprend deux sous-catégories : l’érosion due à une surtension et l’érosion due à une fuite de courant. L’érosion due à une surtension (ISO 5.4.2) (Fig. 12) se produit lorsqu’un courant électrique passe d’une bague de roulement à une autre à travers les éléments roulants. Au niveau des surfaces de contact, le processus est similaire à celui exploité pour le soudage à l’arc électrique (densité de courant élevée sur une petite surface de contact). La température du matériau s’élève à des niveaux compris entre le niveau de trempe et le niveau de fusion. Apparaissent alors des zones décolorées, de dimensions variables, dans lesquelles le matériau a été trempé, re-durci ou a fondu. Des cratères se forment aux endroits où le métal a fondu, puis se détachent sous l’effet de la rotation du roulement. Une usure du matériau en excès s’opère. Une érosion due à une surtension peut être causée par l’exposition de la machine à la foudre, une mise à la terre incorrecte de l’équipement de soudage lors de réparations de soudure sur la machine, etc. L’érosion due à une fuite de courant (ISO 5.4.3) (Fig. 13) se produit lorsqu’un courant de faible intensité traverse le roulement. La détérioration se présente généralement sous forme de cratères peu profonds, rapprochés et de faibles dimensions, et un motif gris/rainurage apparaît au fil du temps. Les éléments roulants peuvent prendre un aspect gris terne et le lubrifiant peut se décolorer. L’ampleur de la détérioration dépend de l’intensité du courant, la durée, la charge du roulement, la vitesse et le lubrifiant. L’érosion due à une fuite de courant est fréquente dans les moteurs électriques sujets aux courants vagabonds lorsque l’arbre n’est pas correctement mis à la terre et que le moteur est commandé par un variateur de vitesse (EFV).
Déformation plastique (5.5)
La norme ISO classe la déformation plastique en deux catégories : la déformation due à une surcharge et l’indentation par des particules. La déformation due à une surcharge (ISO 5.5.2) (Fig. 14) est une détérioration mécanique causée par une surcharge statique telle qu’une mauvaise manipulation (roulement tombé de hauteur), un montage incorrect (martelage sur roulement), des charges maximales dues au fonctionnement de la machine, etc. Elle peut se manifester par une indentation des chemins de roulements ou des entailles dans les espaces entres les éléments roulants, des détériorations causées aux cages, aux joints et aux flasques, etc. Les indentations par des corps étrangers (ISO 5.5.3) (Fig. 15) se produisent lorsque des contaminants solides ou des débris sont laminés dans la zone de contact de roulement du roulement, provoquant ainsi des indentations (déformations) sur les chemins de roulement et les éléments roulants. La taille, le type et la dureté des particules influent sur l’étendue des détériorations. L’indentation peut conduire à une fatigue initiée en surface (ISO 5.1.3) sous l’effet du roulement.
Fissuration et rupture (ISO 5.6)
La dernière catégorie ISO est la catégorie de fissuration et rupture. Elle comprend trois catégories : rupture forcée, rupture par fatigue et fissuration thermique. Une rupture forcée (ISO 5.6.2) (Fig. 16) se produit lorsque les concentrations de contraintes dépassent la résistance à la traction du matériau. Les causes courantes d’une rupture forcée sont des contraintes circonférentielles trop élevées dues à un ajustement trop serré du roulement sur l’arbre ou à un enfoncement excessif d’un roulement à alésage conique au-delà de sa portée conique sur l’arbre ou du manchon de serrage. La rupture par fatigue (ISO 5.6.2) (Fig. 17) apparaît en cas de flexion cyclique induisant un dépassement de la résistance à la fatigue du matériau. Une flexion répétée conduit à une fissure qui se propage jusqu’à la bague ou la cage. Cela peut se produire dans un roulement soumis à de lourdes charges appliquées si la rigidité du palier n’est pas uniforme, induisant des contraintes cycliques élevées sur la bague extérieure. La fissuration thermique (ISO 5.6.4) (Fig. 18) se produit lorsque deux surfaces glissent l’une contre l’autre, générant un échauffement par frottement. Si le glissement est important, un redurcissement local des surfaces combiné au développement de contraintes de traction résiduelles élevées peut être à l’origine de fissures, généralement perpendiculaires au sens de glissement. Des fissures thermiques peuvent se produire lorsqu’un palier fixe, par exemple, entre en contact avec la bague de roulement tournante.
Une description plus détaillée des causes et des modes de défaillance des roulements est fournie dans la Référence 2.
Gardez à l’esprit que le lubrifiant (huile ou graisse) à l’intérieur du roulement détérioré peut également apporter des informations utiles dans le cadre de l’analyse des causes de défaillance. Il suffit de prélever un échantillon de lubrifiant pour le comparer à un échantillon de lubrifiant frais. Une analyse du lubrifiant peut être réalisée pour permettre la prise en compte de la teneur en particules et en humidité, des variations de viscosité, des changements de consistance de la graisse, etc.
L’examen des joints ou du flasque du roulement et d’autres composants tels que le manchon peut également se révéler instructif.
Des techniques de maintenance prédictive (PdM) ou de maintenance conditionnelle (CBM) telles que l’analyse vibratoire, la thermographie, l’analyse de l’huile, etc., peuvent être utilisées pour détecter des défauts avant que de graves détériorations du roulement ne surviennent et que l’équipement sur lequel le roulement est monté ne subisse également des dommages. Elles facilitent, en outre, l’identification des modes de défaillance. Démonter des roulements de grandes dimensions (alésage > 200 mm) avant qu’une détérioration de grande ampleur ne soit à déplorer permet, en outre, de les réparer. Le roulement peut ainsi retrouver un état « comme neuf », ce qui réduit les coûts de maintenance et l’impact sur l’environnement (Fig. 19).
Les modes de défaillance les plus courants
D’après les données1 de SKF, les cinq modes de défaillance ISO les plus courants sont l’usure par abrasion (26 %), la fatigue initiée en surface (16 %), la corrosion due à l’humidité (14 %), l’usure par adhésion (7 %) et l’érosion due à une fuite de courant (7 %) (Fig. 20). Ces modes de défaillance représentent environ 70 % de tous les modes de défaillance identifiés dans des inspections de roulements. Cependant une corrosion de contact, même mineure, est observée dans la plupart des roulements. Les autres modes de défaillance ISO sont également observés mais dans une moindre mesure.
SKF Bearing Analysis Reporting Tool (BART)
Déployé dans un premier temps auprès des ingénieurs SKF, le logiciel BART de SKF est désormais disponible pour les clients. Ces derniers bénéficient d’une formation de base sur les roulements, les techniques d’inspection des roulements et l’utilisation du logiciel SKF BART. Ils travaillent en collaboration étroite avec un ingénieur d’applications ou expert SKF pour compléter le rapport d’inspection. Le rapport d’inspection BART est approuvé par l’expert SKF. L’inspection révèle si le roulement doit être remplacé ou s’il peut être réutilisé, si une réparation est possible ou s’il doit être mis au rebut. Il peut également être utilisé pour documenter l’inspection d’un roulement neuf avant sa mise en service. Cela peut être utile dans le cas d’un roulement stocké depuis longtemps.
Si nécessaire, un ingénieur d’applications SKF peut réaliser une analyse complète des détériorations en vue d’établir des recommandations pour améliorer la fiabilité des roulements. Les ingénieurs SKF peuvent utiliser l’intelligence artificielle (IA) [Réf. 3] pour aller plus loin dans l’analyse des détériorations de roulements. La solution d’IA employée repose sur un système de computer vision pour évaluer le degré de détérioration des roulements à partir de photographies numériques. Ce système utilise l’intelligence artificielle sous forme d’un algorithme de reconnaissance d’image par réseau de neurones qui a été entraîné avec des milliers d’images de roulements détériorés tirées des archives de SKF.
Résumé
En résumé, la norme ISO 15243 est utile pour classer les modes de défaillance de roulements utilisés sur des équipements et identifier les causes de défaillance. La connaissance des modes et causes de défaillance courants des roulements permet d’adopter de mesures correctives pour éviter que les défaillances ne se reproduisent. Cela peut réduire considérablement les risques de défaillances imprévues et catastrophiques, et potentiellement améliorer la fiabilité et la disponibilité des équipements. Les roulements qui sont démontés pour des raisons de maintenance peuvent faire l’objet d’une inspection permettant de déterminer les possibilités de réutilisation et de réparation.
Les données relatives aux modes et aux causes de défaillance des roulements sont collectées, ainsi que d’autres données associées, pour améliorer la connaissance du fonctionnement des roulements. Le logiciel BART de SKF est utilisé par SKF et disponible auprès des clients pour la réalisation de rapports d’inspection de roulements et d’analyse des détériorations.
1 SKF Bearing Analysis Reporting Tool
References
[1.] Norme internationale ISO 15243:2017 « Roulements — Détérioration et défaillance — Termes, caractéristiques et causes »
[2.] Brochure SKF 1219 : « Analyse des détériorations et défaillances de roulements »
[3.] Article SKF Evolution : « L’avenir de l’analyse des défaillances de roulements s’écrit au présent » (2022)