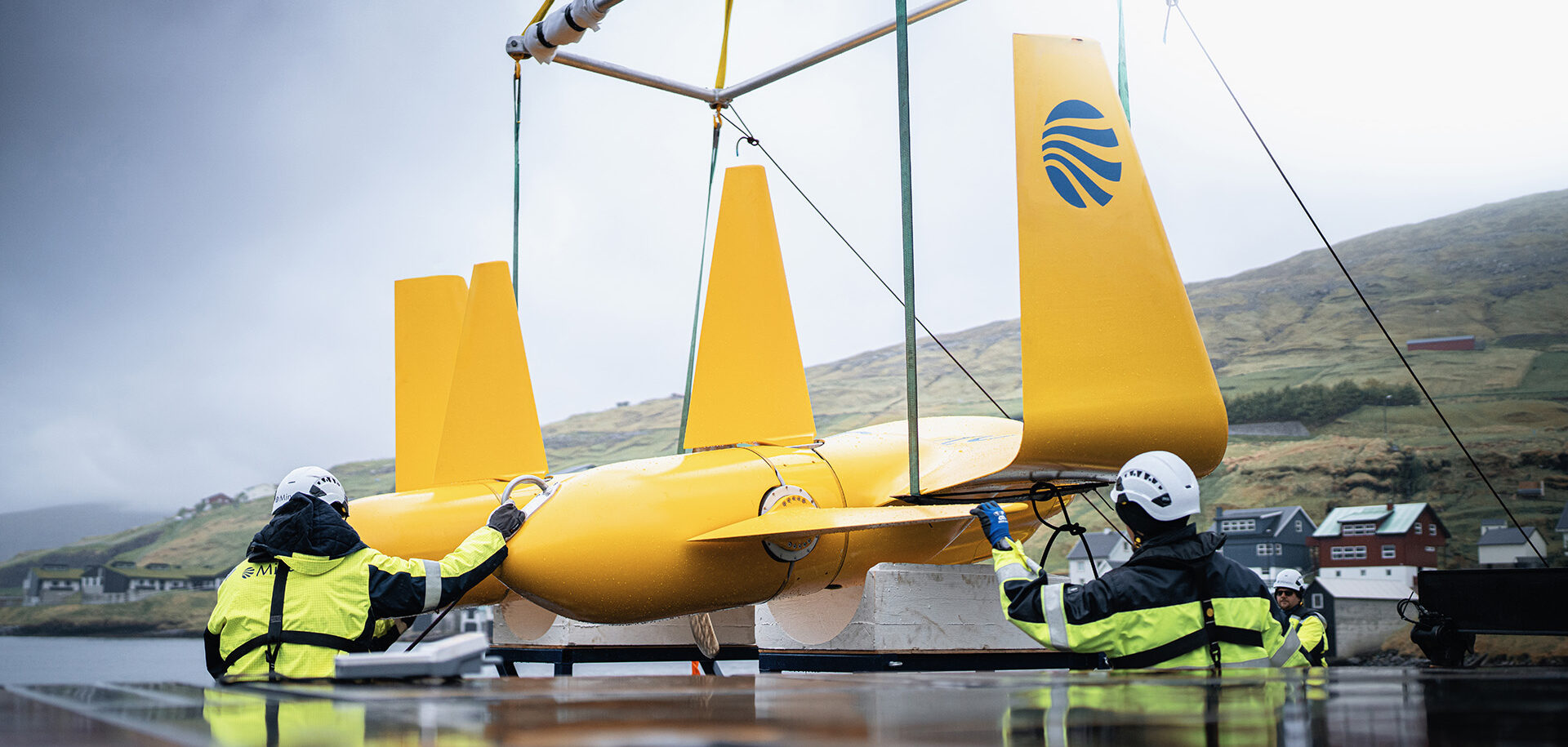
SKF and Minesto collaborate on Faroe Islands
Nordic tidal energy company Minesto has developed a patented technology for underwater kites that makes use of the clean and renewable energy in the ocean’s underwater currents. SKF was brought on board early in the project to develop an efficient bearing and sealing solution.
Imagine flying a kite in the wind. You can feel the force in the string you’re holding. When you steer the kite laterally, it picks up speed and generates additional force. This is the simple principle behind the patented technology developed by Minesto, a marine energy technology developer. But the kite, instead of flying in the wind, flies in the ocean. Water is nearly a thousand times denser than air, so the energy it generates is more concentrated.
The tidal kite, whose design resembles an aeroplane, has been built to cause as little resistance as possible. The wings of the kite use the hydrodynamic lift that is created in underwater currents to push the kite forward. Using a built-in steering system, it follows a predetermined figure-eight pattern, which means that the turbine moves through the water at a speed greater than the actual ocean current. The energy that is generated is then fed via the onboard generator through a fixed cable that connects the kite with the sea floor.
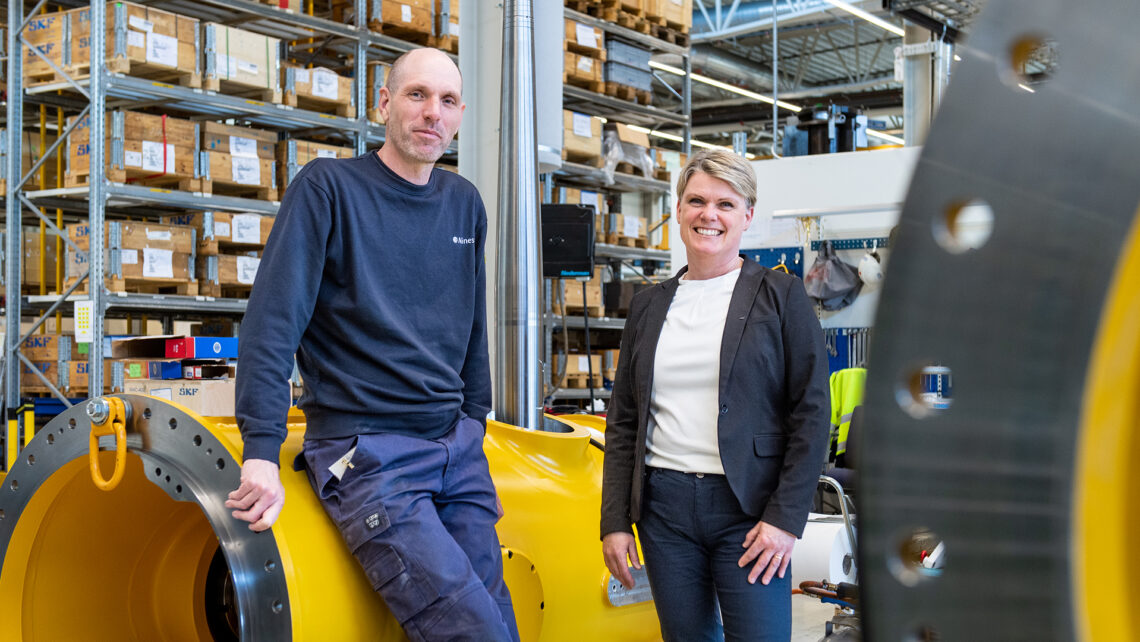
Energy park for tidal kites
The smaller Dragon 4 model of tidal kite has been put into operation off the coast of the town of Vestmanna, in the Faroe Islands. In Hestfjord, a nearby inlet, the world’s first tidal kite energy park is being developed. Once the park is finished, it will have a planned capacity corresponding to 30 MW and annual production of 84 GWh.
I want to be sure that we have the right basic design from the start. That is why it was natural to bring in SKF.
Niklas Lagesson, senior design engineer, Minesto
In parallel, the next generation of kites – Dragon 12, intended for large-scale energy production – is being developed in Gothenburg, Sweden. It has a wingspan of 12 metres, tip to tip, a dry weight of 28 tonnes and a production capacity corresponding to 1.2 MW. Minesto is alone in developing kites that operate in low-velocity tidal and ocean currents, which means the technology will be usable in many ocean areas around the world.
Early in the development phase for Dragon 12, Minesto senior design engineer Niklas Lagesson brought in SKF to help with the design of bearing and sealing systems in the rudders and elevators.
“As a designer, I want to have control over all the parameters and to be sure that we have the right basic design from the start,” Lagesson says. “That is why it was natural to bring in SKF, which has a great deal of experience in bearing and sealing solutions.”
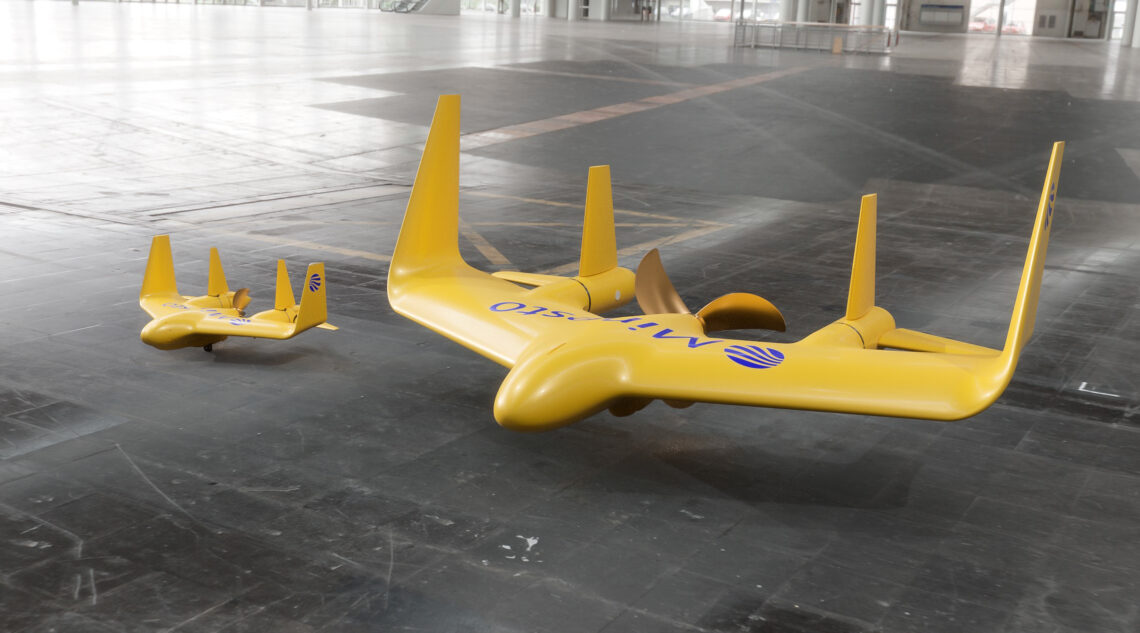
Right idea from the start
For Yvonne Rydberg, the SKF application engineer who supported Niklas Lagesson during the design process, this was a welcome gesture.
“Minesto had the right idea from the start, investing time and resources at an early stage to optimize the bearing solution,” says Rydberg. “This has meant greater freedom in designing a cost-efficient solution with the right performance. This saves both time and money for customers, from design to finished commercial product.”
SKF has also suggested using a special lubricant in the bearings, since the slow back-and-forth movements in the rudder during operation mean it could be difficult to build up a film of lubricant.
“With this solution, we utilized the experiences gained from the wind power industry and the so-called pitch bearing,” Rydberg says. “This is a bearing that connects the rotor hub with the rotor blade, which has a similar movement during operation.”
Another key component of the solution is the seals made of S-Ecopur®, a material that SKF has developed. This unique material is ideal for marine environment applications where the seals are self-lubricating.
“The seals are crucially important in preventing water from entering the machine, and they need to withstand the difficult challenge of following the axle in all positions while rotating with a low degree of friction,” says Anders Jönsson, SKF Sweden’s product line manager for seals.
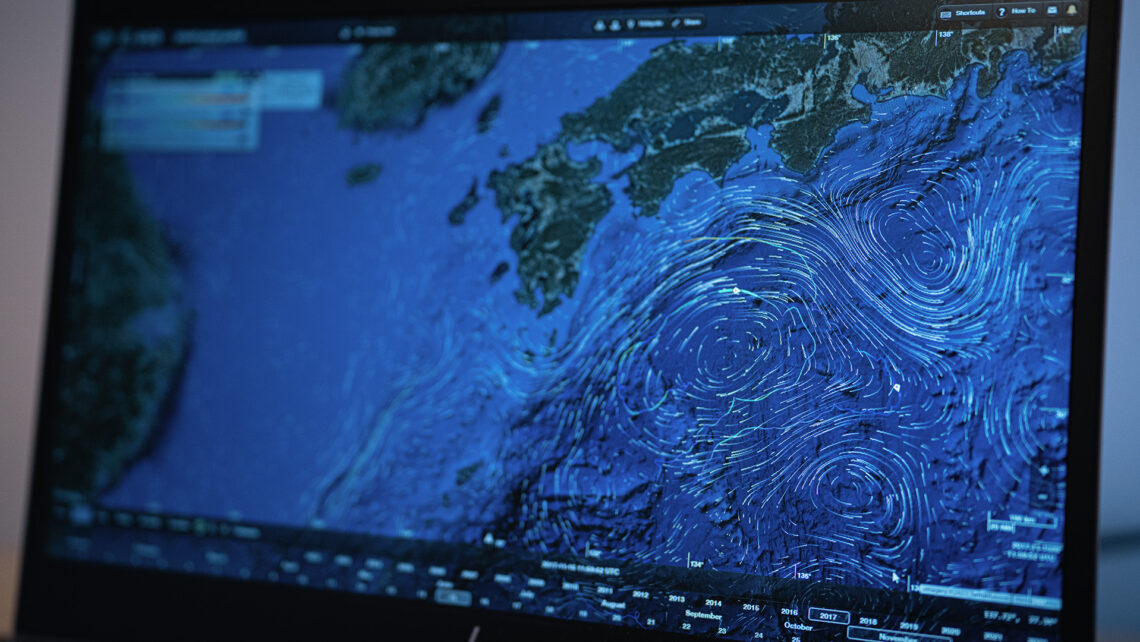
Online tool a great help
During the development of Dragon 12, Niklas Lagesson and his colleagues used SKF’s Simpro Quick, an online tool that was developed to meet designers’ needs to model and evaluate designs and to test the performance of various bearing systems. The tool is intended to facilitate and accelerate the design process and to help the user optimize the choice of bearing in their solution
Through the tool Lagesson gained access to the entire SKF network of engineering expertise.
“Designers are often alone in making decisions, so having access to a larger network of competence is wonderful,” he says. “At the end of the day, it’s the sum total of all the engineers’ contributions that make the best solution.”
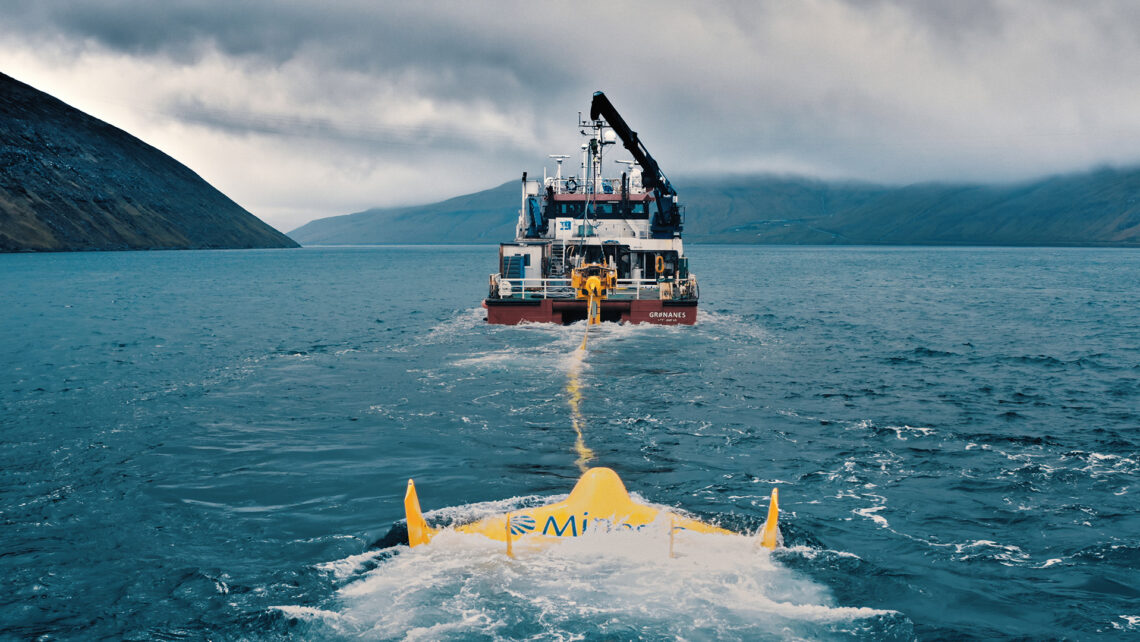
Strong commercial product
Once the kite is in operation the stresses on the materials and components are great. This is due primarily to the predetermined figure-eight pattern, with the kite flying at speeds of up to 20 knots at a depth of 40 metres. The turns are sudden, and the design is dimensioned to handle forces corresponding to 3.5 G in the turns. Critical machine components will be equipped with SKF’s sensors and remote monitoring to analyse and monitor data during operation.
Dragon 12 will also be installed and put into operation in the Faroe Islands, and the components will be monitored and analysed. SKF is conducting a bearing and lubrication analysis in Gothenburg to evaluate whether anything in the solution needs to be adjusted.
“We are creating a great deal of value for each other in our collaboration,” says Yvonne Rydberg. “We are accumulating knowledge and optimizing performance for a strong commercial product.”
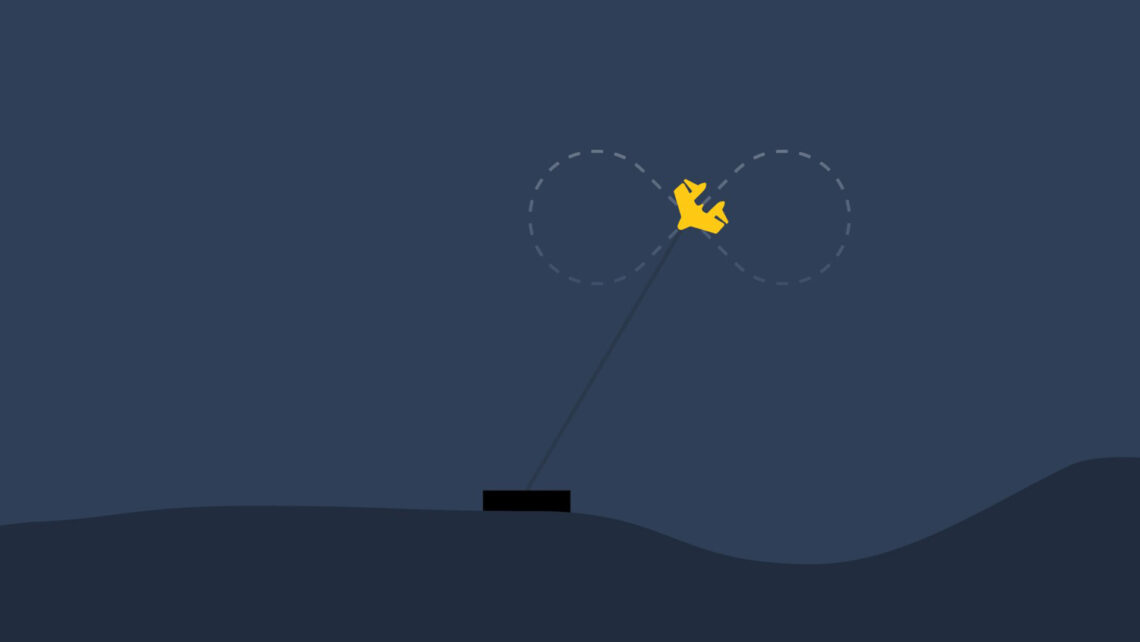