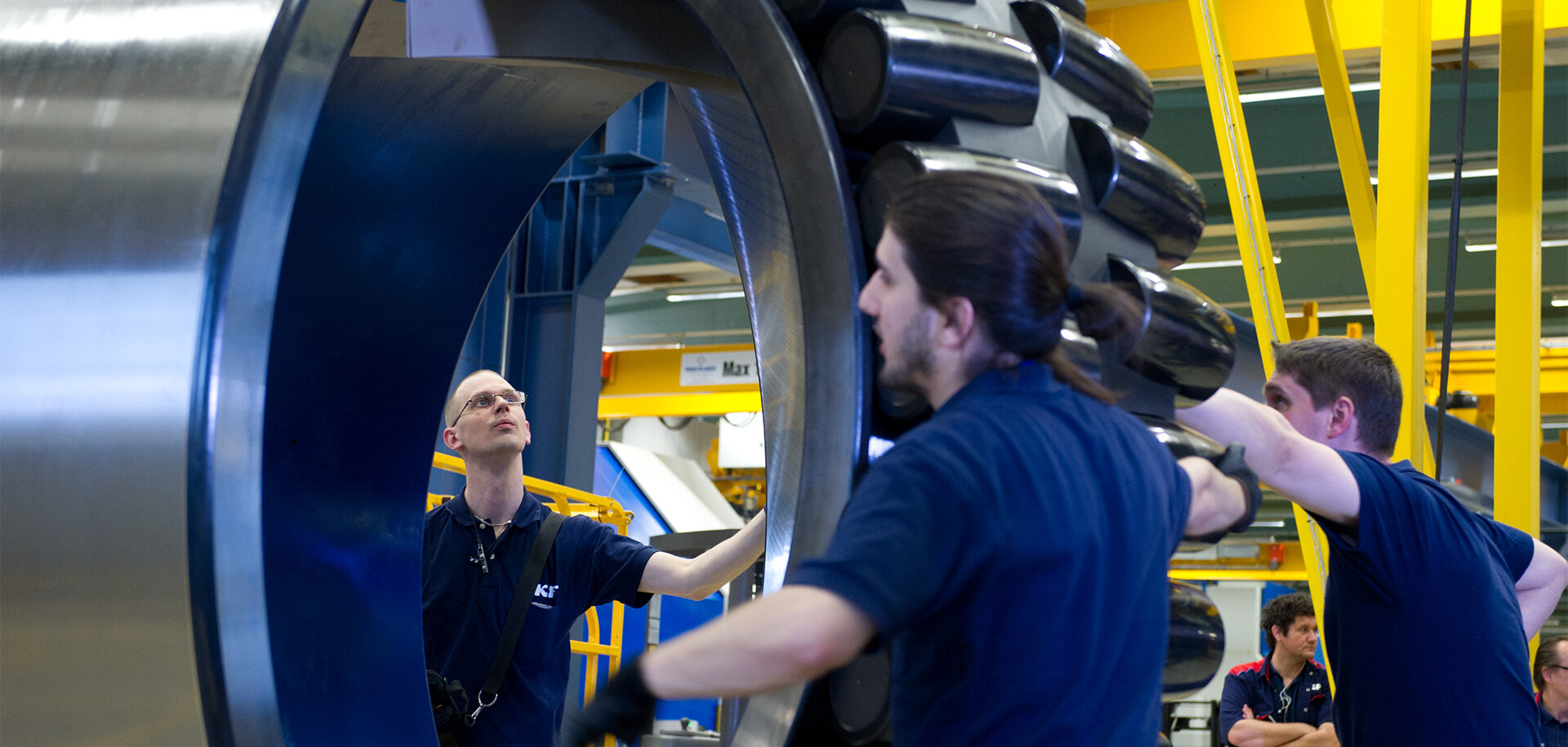
Coatings to improve bearing performance
Coatings maximize the service life and performance of rolling and plain bearings. They can satisfy a variety of operating conditions and application performance requirements. Currently SKF offers more than 35 different speciality coatings.
Nowadays there is an expectation that a rolling bearing can be used and can rotate almost indefinitely if three operating conditions are met: 1) applied stress staying below a certain value; 2) adequate lubrication; and 3) no contamination. Of course, in some cases an application could be far from ideal, and unexpected issues could appear that could increase operation and maintenance costs.
Different strategies have been developed to improve a bearing’s service life and performance when non-ideal conditions are present. One of them is the use of coatings, which can impart a wide variety of features including:
- wear resistance
- increased or reduced friction
- corrosion resistance
- sliding and emergency running properties
- improved lubrication or reduced need for lubrication during periods of operation
- improved lubricant wetting properties
- electrical insulation
- hydrogen barrier
- fretting corrosion prevention
- aesthetic appearance improvement.
Coating a standard bearing steel substrate with materials that have the desired functions can significantly improve the performance of the whole bearing. Coated bearings can also be used to cover the gap between standard bearing steel and ceramic hybrid bearings. For some applications, ceramic rolling elements are a good solution but expensive and, in some cases, not commercially available. In these cases, the operation of standard bearings can be brought to the right level by applying coatings.
Some coatings are deposited in very thin layers, which provides an important advantage. The use of coatings that are just a few microns thick enables the use of standard bearings taken from the production channel without the expense of changing the machining production settings.
Overview of coating technologies
SKF utilizes different coatings technologies as reviewed in fig. 1. They can be divided into three main categories:
- Gaseous state processes, where the coating material passes through a gaseous or vapour phase prior to depositing onto the surface. These include vacuum deposition processes such as physical vapour deposition (PVD) and plasma-assisted chemical vapour deposition (PACVD).
- Solution state processes, where the coating material is present in a liquid phase prior to being deposited as a solid onto the surface. Methods may be divided into the categories of chemical deposition (for example, electroless deposition, chemical conversion, homogeneous chemical reactions and dipping and liquid spraying), and electrochemical depositions, such as the galvanic deposition of a metallic coating on an electrode by a process of electrolysis.
- Molten state processes, where the coating material is melted or semi-melted (softened) prior to being deposited as a solid onto the surface through the use of a source of high energy. Methods are divided into spraying deposition (covering a wide range of techniques in which material is heated rapidly in a hot gaseous medium and simultaneously projected at high velocity onto a surface to produce a coating) and laser cladding technology.
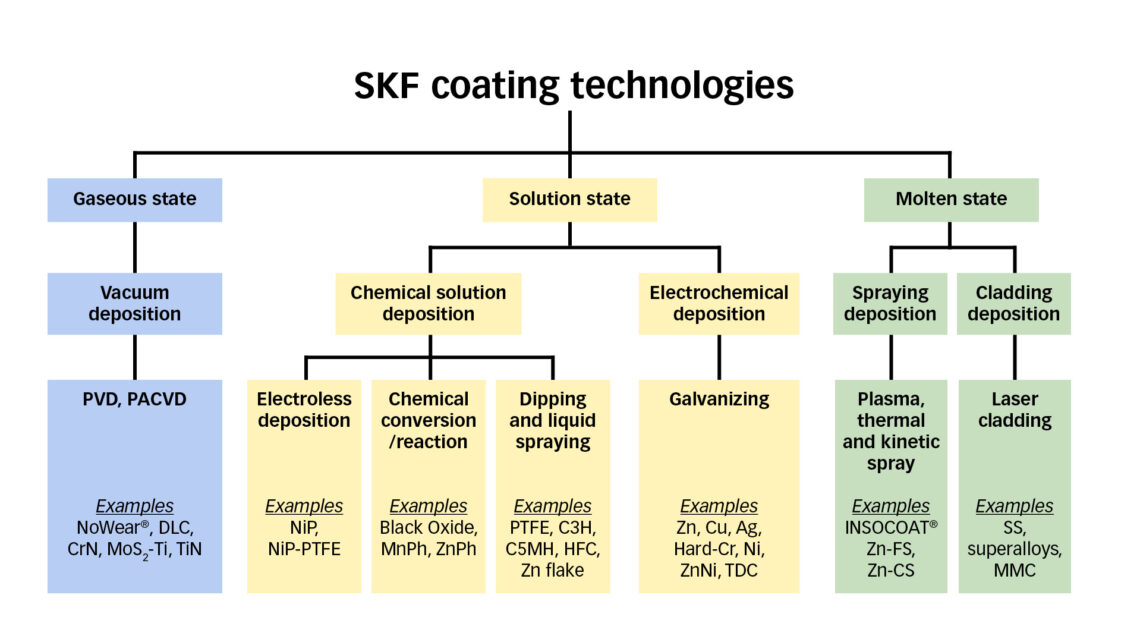
SKF coatings world
SKF has a portfolio with more than 35 different state-of-the-art coatings that can be used in a broad number of applications or different parts of its bearings. All coatings have been optimized to the specific demands of bearings and are based on precise specifications and strict quality control. They are produced in top-level coating facilities that often go far beyond usual coating and equipment standards and provide the maximum in quality, dependability and repeatability.
Some coatings are deposited in very thin layers, which provides an important advantage.
In this article we will discuss some of the most-often-used SKF coatings. The complete list of SKF coatings, together with their physical and tribological properties and all the applications, has recently been published in the online SKF Coatings Catalogue.
Rolling bearings
In the case of rolling bearings, fig. 2 lists 12 main coatings that provide five major functions for rolling element bearing applications, which include anti-sliding wear for cages, electrical insulation, anti-fretting corrosion, anti-corrosion and anti-wear on raceways.
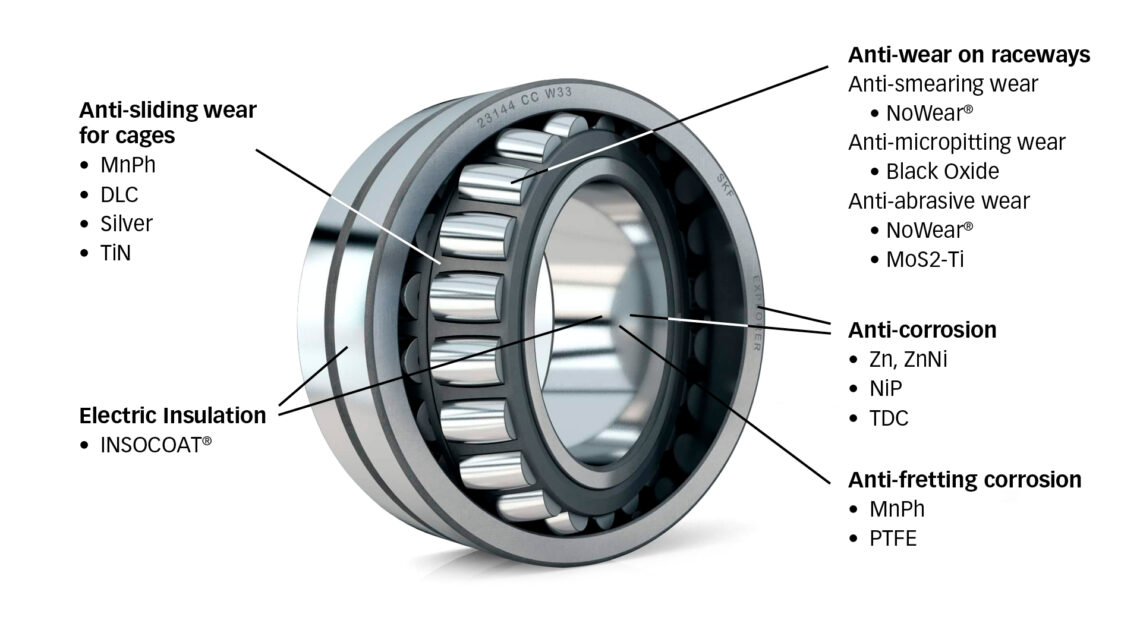
a. Anti-wear on raceways
Black Oxide: This is a surface treatment made by a chemical reaction at the surface of the bearing steel. All bearing surface components are coated. The parts are immersed in different alkaline aqueous salt solutions operating at temperatures in the 140–150 oC range. The reaction between the iron of the steel alloy and the reagents produces a black layer about 1 μm thick consisting of a well-defined blend of FeO, Fe2O3 and Fe3O4. The coating provides many advantages, such as minimizing sliding wear and adhesive wear. It also improves running-in by promoting a very smooth surface, therefore having a lower final steady-state friction than in uncoated bearings. Another advantage is the increase of oil adhesion into the surface, resulting in a light corrosion protection. Black Oxide is also a barrier against hydrogen, protecting the underlying steel. Furthermore, the layer increases the resistance against micro-pitting, smearing, spalling, fretting and the formation of surface cracks and premature fatigue. Finally, the layer protects the surface against detrimental extreme pressure (EP) additives that are frequently used in wind gearbox lubricants.
NoWear®: SKF was the first bearing company in the world to use carbon-based coatings on bearings. All bearing surface components can be coated, but the best results are obtained by coating only the rollers. The parts are introduced into a vacuum chamber where a PACVD method is used, with chemicals and physical reactions in the presence of a plasma producing a mixture of carbon+metal vapour that is condensed onto the workpiece at temperatures below 180 oC. The resulting dark grey amorphous coating, which is about 3 μm thick with moderate hardness and very low friction even in dry state, is optimized for use on bearing raceways under high contact pressures. NoWear®, patented in 1999, reduces adhesion, smearing, surface fatigue and micro-pitting and ensures very low wear in starved lubrication situations. In addition, the engineered multi-layered coating contains a special underlayer for enhancing adhesion and a top graphitic layer for improved running-in.
MoS2+Ti: It is a molybdenum disulphide (MoS2) amorphous layer doped with titanium (Ti) of about 1–3 μm thick, with similar hardness as NoWear® but specially designed to have very low friction and high wear resistance in dry, vacuum and clean room environments. The parts are introduced into a vacuum chamber where a PVD method is used, with physical reactions in the presence of a plasma producing a vapour that is condensed onto the workpiece at temperatures below 180 oC.
b. Anti-corrosion
Zn and ZnNi: Zinc and the zinc-nickel alloy are layers in the range of 1–15 μm thick, deposited by electrolytic methods and later passivated for enhanced protection. They are typically used in non-raceway applications. For anti-corrosion purposes, although zinc has been the traditional approach, alloying with nickel has overcome some of the drawbacks of a pure zinc coating, such as its low hardness. In addition to its anti-corrosion properties, zinc delivers high friction that can be used for an anti-slip or anti-fretting function in outer surfaces for bearing outer diameters, inner diameters or the bores of bearing housings.
NiP: The silver-coloured nickel-phosphorous alloy with thickness in the range of 10–50 μm is deposited by an autocatalytic electroless method. There are three variants, with different amounts of phosphorous concentrations between 6 % and 14 %. The increase of phosphorous improves the anticorrosion property but is detrimental to the hardness and wear resistance. Typically used in non-raceway applications where a combination of anti-corrosion and anti-wear properties is required, this coating could be also used in raceways with thicknesses below 3 μm.
TDC (thin dense chromium): It is a silver-coloured polycrystalline chromium layer in the range of 2–5 μm thick. The coating is made by electrolysis with a chromium acid electrolyte. The process is further catalysed with, e.g., potassium dichromate to form a thin chromium layer with a nodular structure. TDC layers can be applied on bearing raceways and outer surfaces. In addition to good corrosion resistance, the coating has high hardness, low friction and high wear resistance.
c. Anti-fretting corrosion
PTFE: This is a polymer coating 10–20 μm thick. Polytetrafluoroethylene (PTFE) powder is sprayed onto the surface with air-atomized or electrostatic spraying, and the layer is formed through a thermal sintering process. The coating has excellent sliding properties, very low friction and no stick-slip properties. It provides bearings with strong and permanent anti-fretting properties in inner diameters or on outer diameters of bearing rings.
d. Electric insulation
INSOCOAT®: This is an electrical insulating layer of aluminium oxide of about 100–300 μm thick applied by an atmospheric plasma-spray process. Molten Al2O3 particles are sprayed onto the steel substrate, and the porous structure is subsequently sealed. An additional finish grinding step helps to provide correct bearing dimensions. The coating is applied onto either the external surfaces of the bearing outer ring or the inner bore surface of the inner ring. The main advantages of INSOCOAT® are related to electrical insulation preventing the passage of electric current through the bearing that causes erosion of the rolling surfaces.
e. Anti-sliding wear for cages
Ag: Silver (Ag) layers with thicknesses in the range 2–4 μm are deposited by galvanic methods, usually with a copper underlayer to increase its adhesion. It is a soft metal layer with dry lubrication properties used at high temperatures and in vacuum environments. It has excellent electrical conductivity and good corrosion protection against chemicals (moderate alkaline and acidic). It is mainly used for plating of steel cages and, in rare cases, rings and rollers for certain demanding applications, such as dry lubrication in vacuum applications, food and aerospace.
TiN: The titanium nitride (TiN) coatings are golden-coloured layers with thicknesses in the range of 1–5 μm. The parts are introduced into a vacuum chamber where a PVD method is used, with physical reactions in the presence of a nitrogen plasma producing a vapour that is sputtered from a titanium target and condensed onto the workpiece at temperatures below 180 oC. They are used as wear-resistant coatings for cages in the presence of lubricants, and coated sleeves for the food industry.
Plain bearings
In the case of plain bearings, fig. 3 lists eight main coatings that provide three major functions for plain bearing applications: anti-corrosion and anti-wear coatings for bearings with or without grease lubrication.
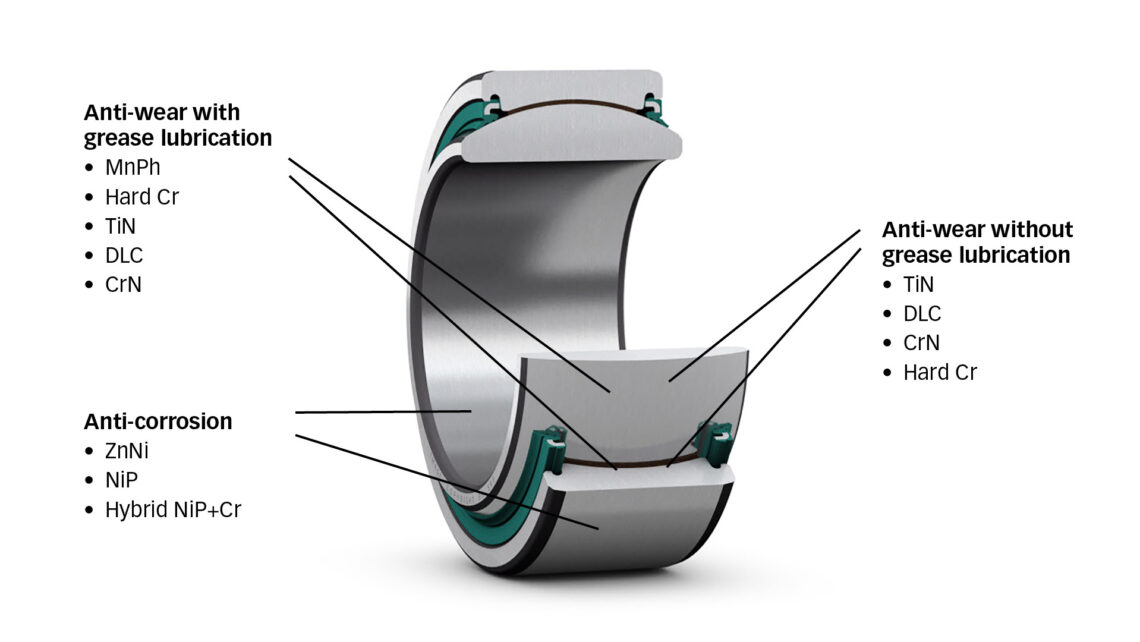
a. Anti-wear without grease lubrication
Hard Cr: This is a silver-coloured hard chromium (Cr) layer in the range of 3–15 μm thick deposited through an electroplating process with chromium acid electrolyte. The process ends with cleaning, removal of hexavalent chromium [Cr(VI)] and oil preservation. The coating gives good sliding contact between plain bearing components, with high hardness and high wear resistance. The resulting chromium layer has microcracks, which means limited anti-corrosion properties at low thickness.
CrN: Chromium nitride (CrN) is a silver-greyish colour layer deposited by PVD with thicknesses in the range of 1–6 μm. The parts are placed in a vacuum chamber, where solid targets of pure chromium are bombarded with a plasma of Ar+N ions that vaporize the Cr material (“sputtering” process). The Cr atoms combine with the N and condensates on the workpieces kept below 180 oC. The result is a hard coating that performs well in sliding wear applications and also in some corrosive environments. The coating can also be used in rolling bearing applications combining CrN coated rings and NoWear® coated rollers. The coating is also used as an underlayer of other coatings to increase the contact pressure support.
DLC (diamond-like carbon): It is the generic name for a group of carbon-based coatings with compositions containing a mixture of graphite and diamond microstructures. They can either include or exclude hydrogen, and the thickness is usually between 2 and 4 μm. The parts to be coated are placed in a vacuum chamber, where several layers are applied on the bearing component surfaces by PVD or PACVD process according to the application. Their composition influences the properties of the coatings. DLC coatings are designed for high wear conditions and poor lubrication situations. They have high sliding and adhesive wear resistance, high load-carrying capacity, excellent abrasion protection and low friction, and they provide surface protection in poor lubrication conditions. DLC coatings are ideal for plain bearings, bearings’ linear drives, bearing shafts, bushings, cam follower pins and sliding parts in rolling bearings (such as cages and seals). The engineered carbon+metal NoWear® coating belongs also to this family of carbon-based coatings; however, there are some differences. Hardness values of DLC coatings for sliding applications are in the range of 18–30 GPa (1800–3000 HV), while NoWear® coatings (used in rolling applications) have hardness values of about 12 GPa (~ 1200 HV).
b. Anti-wear with grease lubrication
MnPh: Manganese phosphate (MnPh) is a grey to black layer with thickness in the range 2–15 μm. The coating is made by a chemical reaction, and all workpiece surfaces are usually coated. The parts are immersed in a manganese phosphating fluid, and the iron in the workpiece reacts with the manganese cations and phosphate anions in the fluid. The coating has anti-wear and anti-fretting properties, improving significantly the smearing and micro-pitting resistance. It also protects under low-kappa and poor lubrication conditions and has an improved oil adhesion. Furthermore, MnPh has good corrosion protection (in oiled condition) and shows electrical insulation properties.
c. Anti-corrosion
Hybrid NiP+Cr: This is a hard silver-coloured bi-layer of nickel-phosphorous and chromium coatings with a thickness in the range of 10–30 μm. The complete coating process consists of two separated parts. The surface is first covered with electroless NiP to improve corrosion protection and give chemical resistance, and then a hard-chromium layer is added by electrolytic deposition that provides mechanical resistance.
Coating the road to sustainability
Sustainability in the area of bearings includes aspects such as energy and resource conservation, waste minimization, process efficiency enhancement and use of renewable materials. As a global technology leader, SKF sees today’s technical transformation as a responsibility and a great opportunity. Reusing industrial materials and components such as oil and bearings is a good start. Offerings – from single seals and bearings to key industrial components and systems – can help, for instance, to develop low-friction, lightweight automotive solutions that can reduce CO2 emissions. Another sustainable approach is to take advantage of the coating technologies, which in some applications reduce friction (and therefore reduce energy consumption) and extend bearing life (hence decreasing the consumption of new raw material).
Final remarks
The use of coatings in bearing applications is gaining interest. By selecting materials and coating architectures, it is possible to tailor unique physical, mechanical and tribological properties to satisfy increasing technological demands. In particular, SKF coatings have been carefully analysed to provide the optimum properties; the processes are in some cases adjusted beyond DIN and ISO standards according to the different applications.
This article has focused on briefly explaining some of the different kinds of SKF coatings to shed some light on terminology, technical aspects and coating design. More information can be found in our SKF Coatings Catalogue.