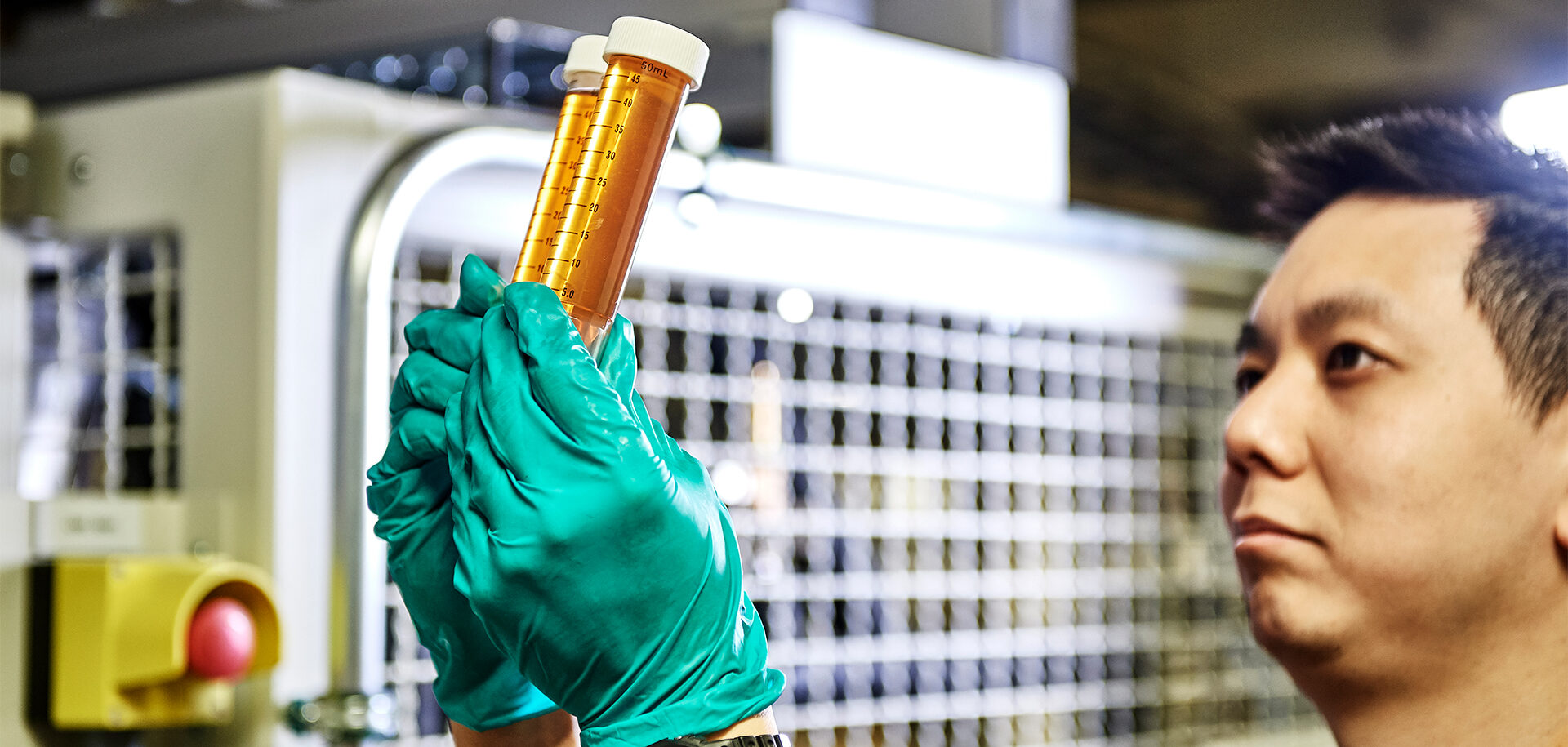
Successful fight against nanoparticles
A well-maintained hydraulic system needs to keep the oil in good condition. An advanced filtration system can remove tiny contaminants that elude conventional filtration systems, leading to reduced costs, lower environmental impact and longer service life.
Hydraulic oil primarily transmits power, but it is also critical for maintaining the smooth operation of the wider system – lubricating moving parts, cooling the system by taking heat away from areas of high load, preventing corrosion of components and removing contamination from critical surfaces. A maintenance strategy for a hydraulic system therefore needs to start with maintaining the oil in good condition.
Abrasive wear is typically found in mechanical systems with relative motion between two surfaces, as hard particles graze the surfaces while in motion. Particulate contamination such as dust, metal particles, rubber and fibres can act as abrasives in the system, accelerating the wear of mechanical components such as pumps, bearings, rods, pistons and seals. Removing these particles from the oil results in a reduced wear rate and longer service life of the system.
Smaller particles and oxidation
Conventional filtration systems excel at removing larger particles, from 5 microns down to 1 micron. But emerging evidence suggests that smaller particles also have a significant role to play, directly affecting oil degradation and thus affecting system performance.
A maintenance strategy for a hydraulic system therefore needs to start with maintaining the oil in good condition.
Another factor is oxidation, which is often viewed as a function of the ageing process of an oil. The occurrence of oxidation in an oil requires the presence of oxygen and a high-enough temperature. The lubricant must also have a catalyst present to initiate and propagate the reaction. Particulate contamination acts as a catalyst for the oxidation process. But if the oil is already filtered, then why do oils still oxidize?
The answer lies in a more hidden problem – nanoparticles. These can be one-thousandth the size of the particles removed by conventional filtration systems. Standard lubricant condition monitoring does not monitor for these smaller particles. The industry standard is instead to supply oil with antioxidant additives. But as the process continues, these additives will be depleted, until eventually oxidation will proceed unhindered.
How to prevent oxidation
A more sustainable approach is to prevent the oxidation reaction from occurring to begin with. To address this issue, SKF RecondOil has developed Double Separation Technology or DST. The process removes nanoparticles from industrial oils, halting the oxidation process at the start. This treatment inhibits the ageing process of the oil, extending the service life of the hydraulic oil and reducing the need for regular oil monitoring.
One of the most important components in hydraulic systems is the seal, keeping oil in and contamination out. Without seals, hydraulic systems simply would not be able to operate. Selecting the suitable seal design and material requires consideration of operating conditions involved, such as temperature, pressure and hydraulic fluids.
The chemical composition of hydraulic fluids can impact seal life and performance. If the seal is not compatible with the fluid, the seal might swell, shrink, harden, soften, dissolve or lose resilience.
SKF has a long history and an extensive database of test results concerning compatibility of various seal materials and fluids, as well as unparalleled expertise in developing materials to meet customers’ needs.
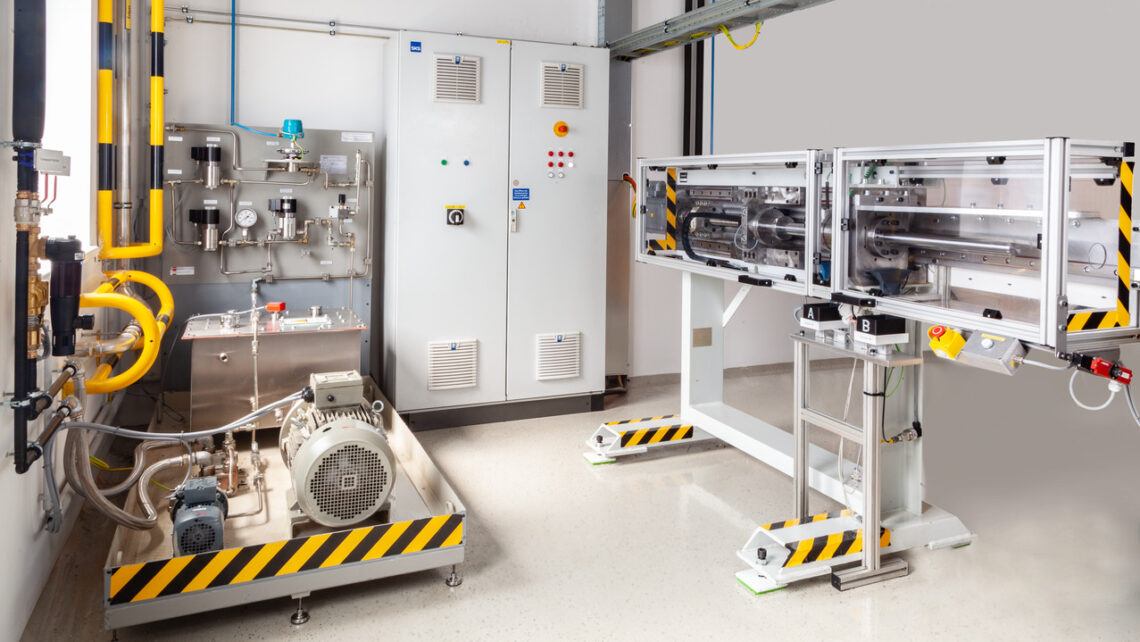
Cleaner hydraulic oil can also decrease labour costs. Because the cleaner oil can remain in service longer, fewer oil drain and fill procedures are needed. The cost of maintenance labour can also be reduced when contamination-related wear and failure decreases.
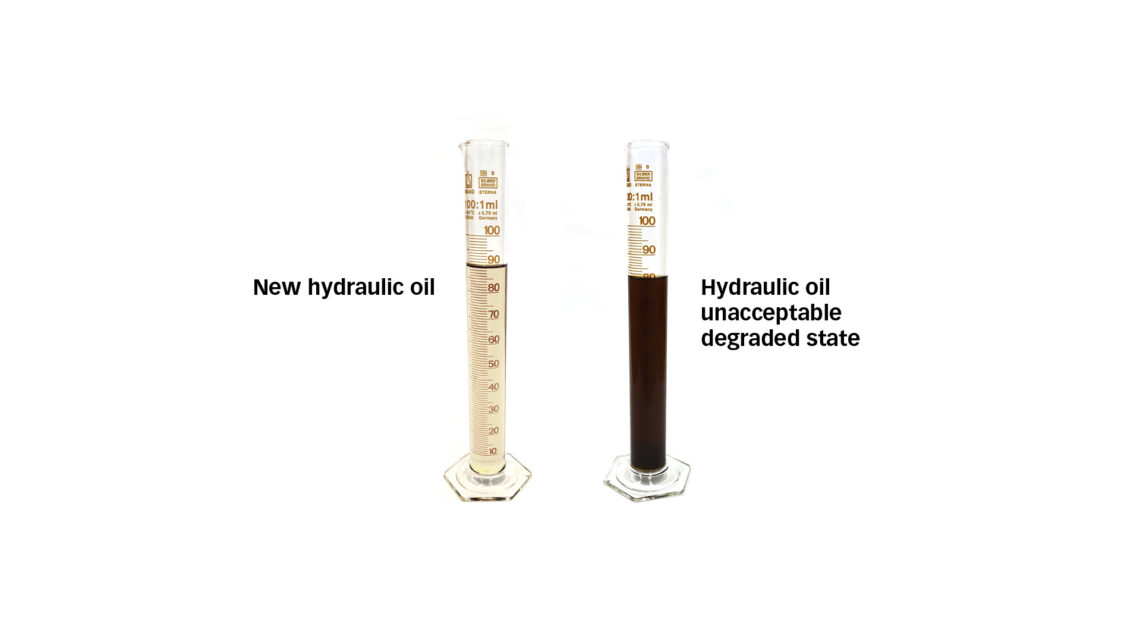
A hydraulic asset is an investment. The service life of hydraulic equipment is a major factor in the success of that investment. Cleaner hydraulic fluid has been shown to extend the service life of hydraulic assets significantly. Greater oil cleanliness levels can multiply the life of a hydraulic machine by as much as 10 times compared with a machine using dirty oil.
Control prevents damage
For all these reasons, it is important to keep hydraulic oil in optimum condition at all operating times. Through careful control of particulate contamination and oxidation catalysts, it is possible to prevent premature wear of hydraulic systems and extend the life of hydraulic oils.
Extensive testing by SKF’s European product-testing team in Judenburg, Austria, found that SKF RecondOil’s Double Separation Technology process could extend the service life of commercially available hydraulic oil. The DST-treated, nano-clean hydraulic oil was not only able to significantly extend the lifetime of the original hydraulic oil but also offered improved lubrication performance.
In-house tests showed the positive effects on the friction performance of seals when hydraulic oil was regenerated with the DST process from SKF RecondOil. These tests highlighted a clear correlation with reduction in friction by using regenerated oil, which in turn will reduce machine wear and the potential for cross-contamination and extend the life of the oil in service.
In this investigation, the lifetime of the hydraulic oil could be at least doubled by the DST treatment’s nano-cleaning process. The lifetime extension of industrial lubricants by removing nanoparticles from oil and preventing oxidation from occurring opens a paradigm shift –treating oil not as a consumable but as an asset. The same oil can be used again and again. A small change in oil can yield significant strategic results.
Would you like to know more about RecondOil? Read our white paper SKF Sealing solutions test results for hydraulic oil.