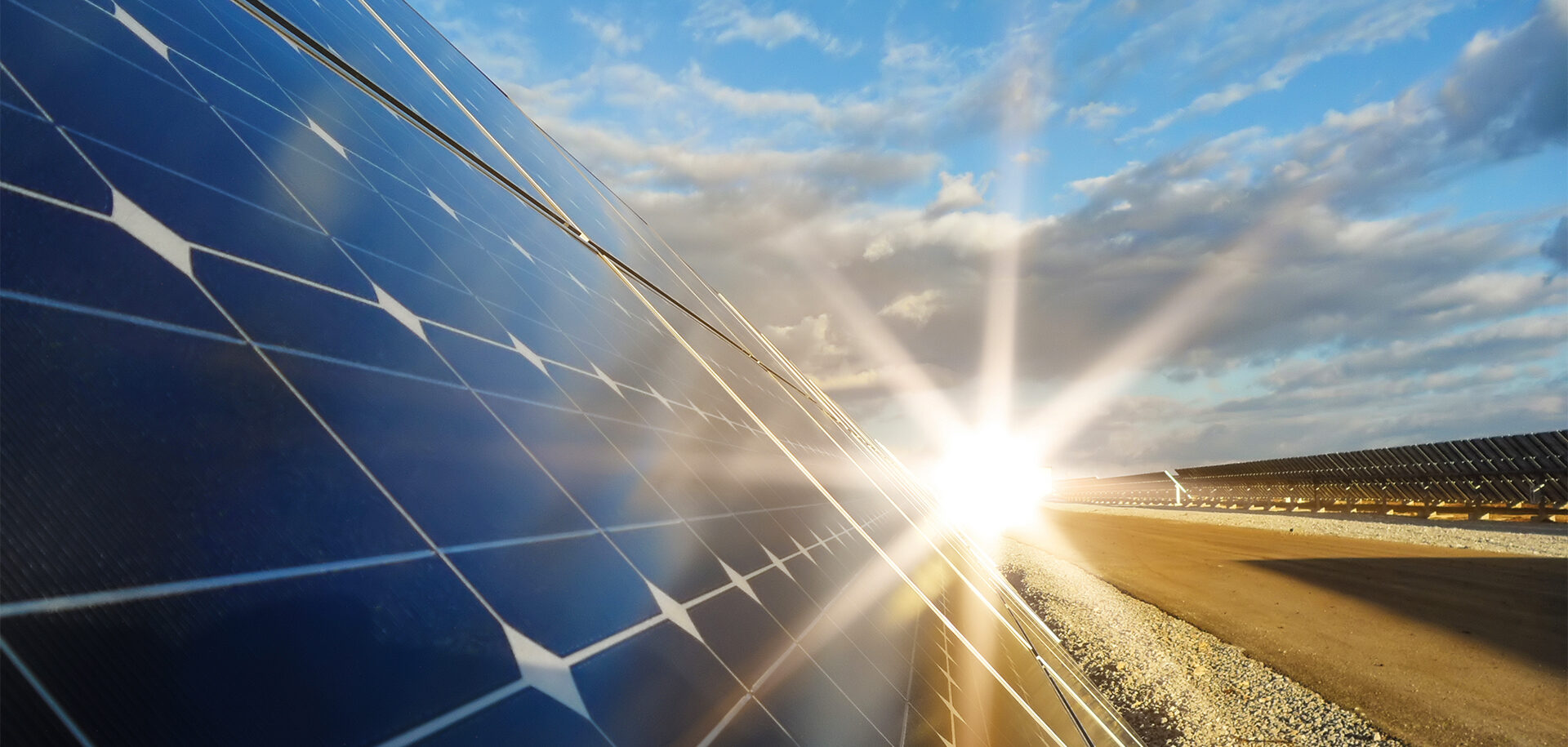
Supporting the energy revolution
Active magnetic bearings from SKF are key components in today’s energy transition and optimization. Now they are finding applications in the technologies that will power a cleaner and more sustainable future.
As the world makes the transition from fossil fuels to zero-carbon alternatives, active magnetic bearings are finding new applications in the emerging technologies of the energy revolution. One important area of future growth is likely to be in hydrogen production and transport.
While most of the hydrogen produced today is created from fossil fuels, the gas can also be produced by the electrolysis of water. If the power for that process comes from renewable sources, the resulting “green” hydrogen is a carbon-free clean energy source. Hydrogen has potential advantages over other energy carriers in many applications. Its relatively high energy density could make it an appropriate fuel for ships, aircraft and heavy trucks.
In addition, the combustion of hydrogen is a clean way to generate the very high temperatures needed for steelmaking and other industrial and chemical processes. Hydrogen is a key ingredient for synthetic liquid fuels that could be a low-carbon drop-in replacement for fossil-fuel-based alternatives.
Although hydrogen gas needs to be liquefied for transport and storage, active magnetic bearings offer all the same advantages here that they do in hydrocarbon applications. Efficient, reliable turbomachines will be a critical element in many of the proposed models for green hydrogen production. They include the use of giant solar farms in desert locations such as in the Middle East and Australia, and production located close to windfarms.
More growth in store
Another area of potential growth for magnetic bearings is carbon capture, utilization and storage (CCUS). This group of technologies is designed to keep greenhouse gas emissions out of the atmosphere by collecting CO2 at the source and containing it at suitable storage locations such as depleted oil and gas wells. As with hydrogen, many CCUS technologies rely on efficient, large-scale compressors.
Active magnetic bearings are constructed a little like an electric motor.
“Blue” hydrogen technology is another area where there is extremely active development underway. This approach combines conventional hydrogen production with CCUS, creating a way to make continuing use of conventional fossil fuel resources while mitigating their climate change impact at the source. The blue hydrogen sector will need plenty of efficient turbomachinery to handle the flows of input gas, output hydrogen and CO2.
The transition from conventional fossil fuels to low- and zero-carbon alternatives is predicted to be the most significant change in the global energy system over the past century. The shift will require fundamental changes by energy producers, energy consumers and society at large. It will also need plenty of clean, efficient rotating machinery. Active magnetic bearings offer equipment makers a proven, reliable and robust solution to some of the key technical challenges they face today.
Subsea gas compressors are a vital but hidden part of today’s global energy system, allowing for increased gas production from existing subsea wells. Installed on the seabed under hundreds of metres of water, these powerful machines push natural gas from offshore wells through pipelines that deliver it to onshore receiving facilities. They operate 24 hours a day, 365 days a year, with little opportunity for inspection, maintenance or repair.
Many subsea wells are becoming depleted because they are losing pressure. With the use of active magnetic bearings on platforms and in subsea applications, we diminish the environmental impact from both the construction and the operational points of view. This additional gas will allow a smoother transition to a greener energy.
Equipment that operates in such extreme conditions requires highly specialized engineering. And the bearings are among the most critical parts of subsea compressor design. Manufacturers need a bearing that can operate at high loads and speeds, can offer a decades-long operating life and can run without the need of adjustment or lubrication after installation.
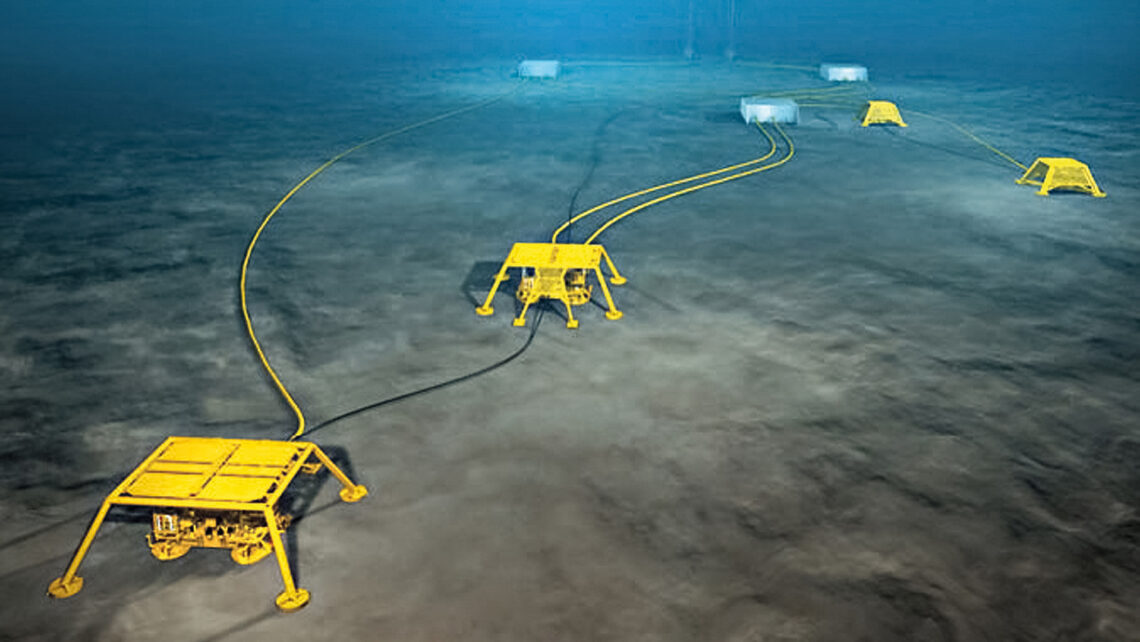
An attractive option
For many of the world’s major producers of offshore equipment, the preferred solution for such applications is SKF’s active magnetic bearing technology. Active magnetic bearings are constructed a little like an electric motor. The bearing housing incorporates a stator, containing multiple copper coils. In use, an electric current runs through each of these coils, creating a magnetic field. This field attracts rotor components fixed to the shaft of the machine, lifting it away from contact with the housing.
As the shaft rotates, proprietary position-sensing technology tracks its precise location and a high-speed signal processing system continually adjusts the current flowing to the stator coils. That keeps the shaft floating within the bearing, with a clearance of 0.15 to 0.5 millimetres, depending on the application.
Because there is no contact between the rotating and stationary parts of the bearing, magnetic bearings are not subject to mechanical wear, and there is no need for a lubricating oil system. Those are the right ingredients for a long, maintenance-free operating life. SKF active magnetic bearings have been in continuous operation in subsea applications since 2015, and their typical design life is more than 30 years. Some turbomachines built in the 1980s have magnetic bearings that are still in use today.
Cool, clean and robust
Active magnetic bearings offer plenty of other advantages besides their long life. Because they do not require lubrication, there is no risk of lubricant leaks that could contaminate process fluids or pollute the environment. And active magnetic bearings can operate at very low or high temperatures, without the need for elaborate heating or cooling systems to protect the lubricant.
That can lead to significant energy savings. In the case of a 6 MW turboexpander used in a petrochemical process, conventional bearings consume 50 to 100 kW of power to run heaters, cooling systems and lubricant pumps. When the manufacturer switched to SKF active magnetic bearings turboexpanders, the active magnetic bearing solution has a power loss that is at least one factor of 10 lower than the oil-film bearing solution.
The active control system in a magnetic bearing can also compensate automatically for process loads or imbalance in the machine. And the data collected by the bearing controller acts as a built-in condition-monitoring system, providing operators with valuable information on vibrations, which can be used to diagnose problems or predict potential faults.
Active magnetic bearings are used in many different industries today. They have found a perfect fit wherever clean, quiet operation and long-term reliability are high priorities. Common applications for smaller bearings include high-performance micro-molecule vacuum pumps for semiconductor manufacturing, chiller applications and neutron choppers.
Big in energy
For larger active magnetic bearings, the energy sector has become the most important market over the past 10 years. Much of the growth in demand has been driven by the evolution of the oil and gas market, especially with the exploitation of offshore gas reserves in deeper waters and increasingly remote locations.
Magnetic bearing technology is also being used in a range of onshore energy applications. Liquefied natural gas (LNG) has transformed energy markets in recent years, as vessels carrying LNG create a vital link between producers and customers in markets too distant to serve via pipeline. Active magnetic bearings are now widely used in eliminating gas flaring and optimizing LNG transport with advanced boil-off systems equipped with high-speed electric motors on magnetic bearings. These SKF motors can spin at up to 60,000 r/min and have powers up to 1 MW. Magnetic bearings are also found in the turbo expanders used to increase energy efficiency, as well as to maximize productivity in hydrocarbon applications and other gas processing, such as hydrogen, air separators and petrochemical applications.