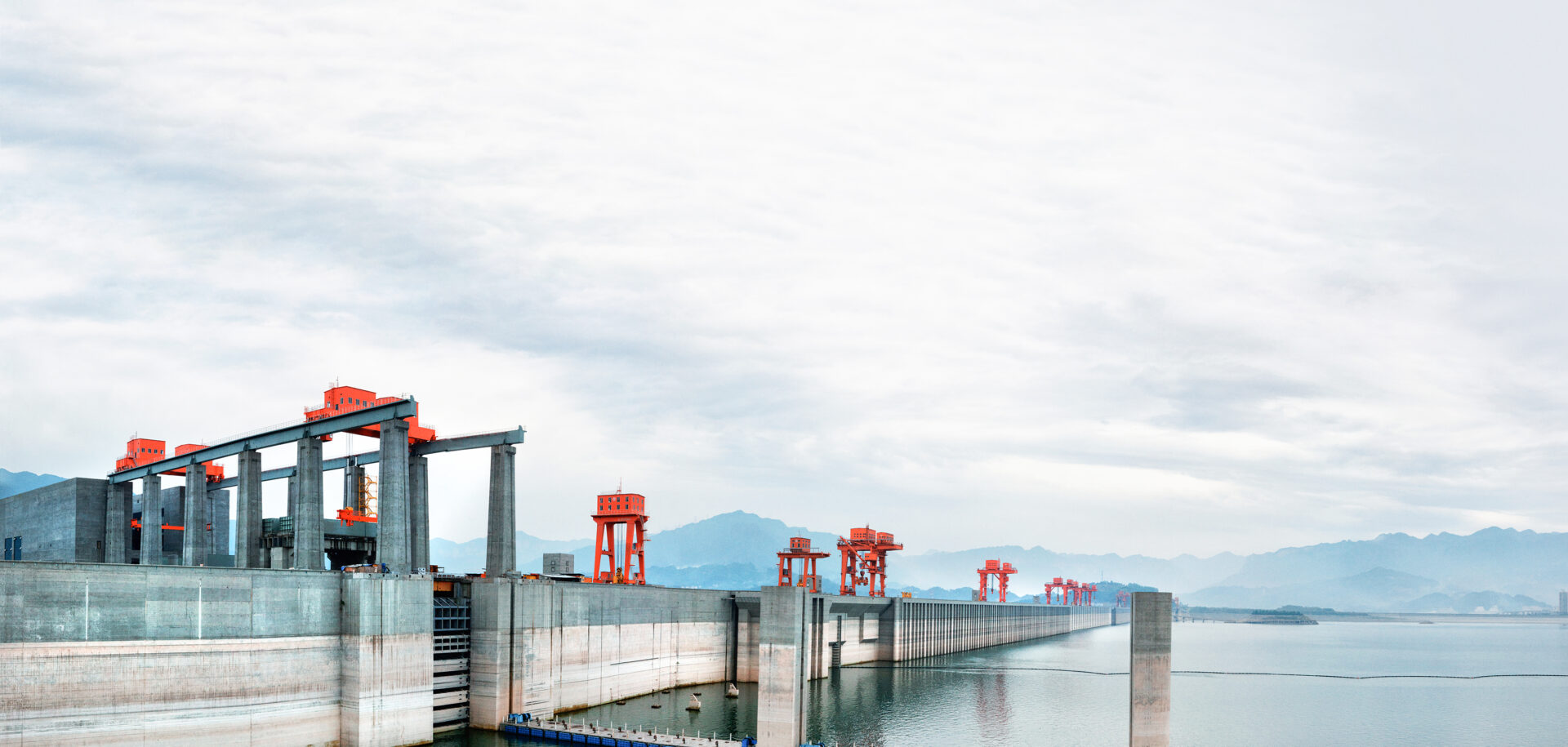
The big lift
The new Three Gorges ship lift is the largest and most complex of its kind in the world. SKF partnered with the Changjiang Institute of Survey, Planning, Design and Research, the Chinese company responsible for its creation, in several important aspects of the project.
To anyone who sees it for the first time, the Three Gorges ship lift is more like a building than a device.
It has a maximum lifting height of 113 metres, enabling 3,000-tonne ships through. Its caisson and related facilities weigh about 15,500 tonnes, making it the largest and most complex ship lift in the world.
Theoretical research on the ship lift, the final part of the Three Gorges Project, began in the 1950s. Its design was completed in 2007 and trial operation began in September 2016.
The ship lift is built to improve the speed of ships’ dam-passing on the Yangtze River, according to Yu Qingkui, project manager of Three Gorges ship lift from the Changjiang Institute of Survey, Planning, Design and Research (CISPDR), affiliated with the Yangtze River Water Resources Commission. He says it now takes about 50 minutes for a ship of max. 3,000-tonnes to go up or down the ship lift, as opposed to the 3.5 hours it would take using a five-level ship lock.
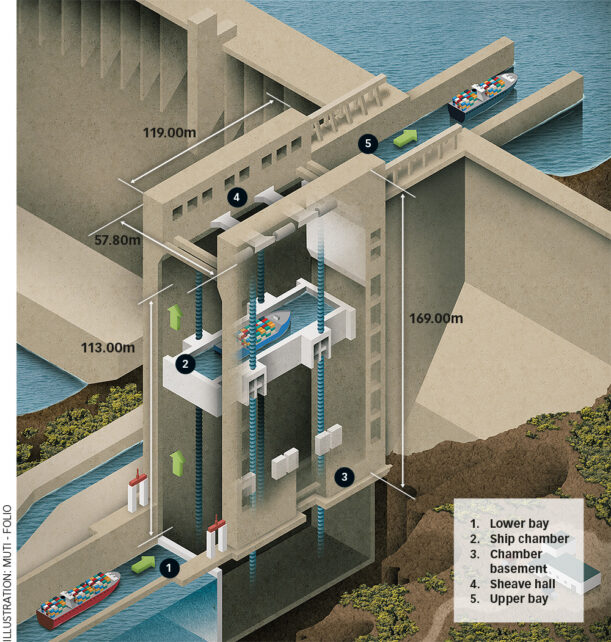
Securing the safety of ships passing through the lift is crucial, Yu explains, and lifting such a heavy caisson to such a height requires precision balance. The Three Gorges ship lift has a counterweight system to balance the weight of the caisson, and a gear-and-rack system to drive the chamber up and down.
The 15,500-tonne counterweight, the equivalent of a fully loaded caisson, is divided into 16 sets, evenly located in the twin towers at the sides of the caisson. The counterweight is connected to the caisson by 256 ropes via 128 double-rope pulleys at the top of the towers. These make sure that the caisson and the counterweight are in balance, no matter the position of the caisson. Four toothed racks are installed in the towers at each of the two sides of the caisson, from the bottom to the top. The caisson is driven up and down by four pinions that engage with these toothed racks.
Each pinion is driven by two electric motors. All drives are interconnected via synchronizing shafts under the caisson.
Thanks to the counterweight system, the pinions and toothed racks only carry about 400 tonnes of total weight instead of 15,500 tonnes, greatly improving efficiency and reducing energy costs.
Although the caisson is balanced by the counterweight system, an appropriate safety device is still needed because even a small accident could be catastrophic. On the advice of experts, CISPDR adopted a safety mechanism consisting of nut post and short screw section (rotary locking rod). When the caisson experiences an unbalanced force, the driving units stop and the caisson is locked vertically by the safety mechanism, thus avoiding possible catastrophe in the event of an accident.
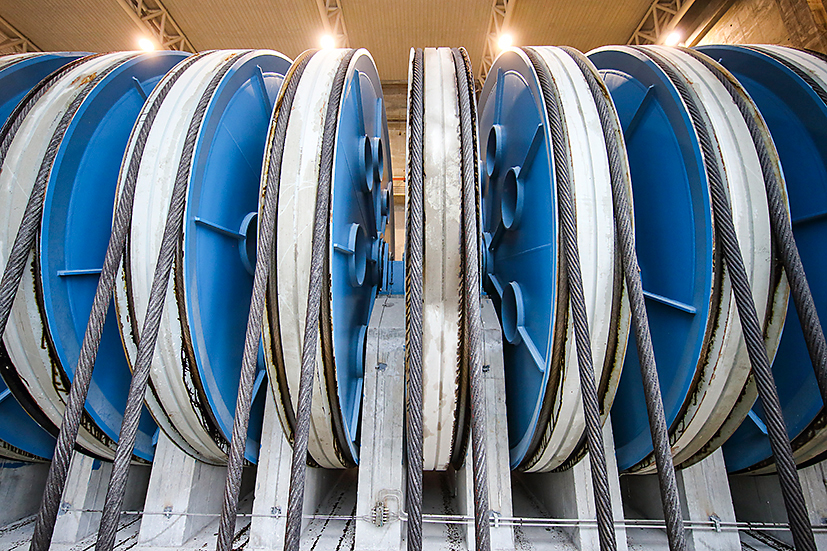
SKF Explorer
SKF has supplied SKF Explorer spherical roller bearings for the climbing mechanism of the ship lift in the Three Gorges Project. The optimized internal design and superficial texture improvement effectively reduce bearing friction, heat generation, wear and noise level, and meet the equipment’s requirements for precision.
At the same time, SKF provides heavy-load grease with excellent water resistance, a property that matches the SKF Explorer bearings, to extend the mainten-ance interval significantly.
SKF also provides sealing solutions for the bearing housings and other critical components of the Three Gorges ship lift.
SKF Explorer is a registered trade mark of the SKF Group.
SKF also supplied hydraulic nuts and hydraulic pumps, as well as other mounting and dismounting tools, to increase the maintenance efficiency.
CISPDR has had considerable technical cooperation and exchanges with SKF since the early stages of the Three Gorges ship lift project, and the company recognizes the high quality of SKF products and service.
Freddy Pan, SKF hydropower segment manager, explains that China Three Gorges Corp. is a key customer and that SKF has been providing technical consultation and on-site services for the operations and maintenance of the Three Gorges ship locks since 2012.
SKF is very trustworthy and they can deliver the products in time.
Yu Qingkui
Project manager
A formal business cooperation between the two companies started in 2014, a result, Yu says, of excellent product performance. “We are satisfied with SKF’s products,” he says. “SKF is very trustworthy and they can deliver the products in time.”
The companies’ cooperation is deepening. SKF is now not only a bearing supplier for the Three Gorges ship lift, but also a sealing solution provider for the bearing housings and other critical components of the ship lift. Three Gorges will continue the cooperation with SKF in the purchase of spare parts after the ship lift starts formal operation.
“We are proud to work with the world-famous Three Gorges Project,” says SKF’s Pan. “We have helped to solve many problems for the ship lift, making the impossible possible. The cooperation has set an industrial benchmark and is win-win for both the Three Gorges Project and SKF.”