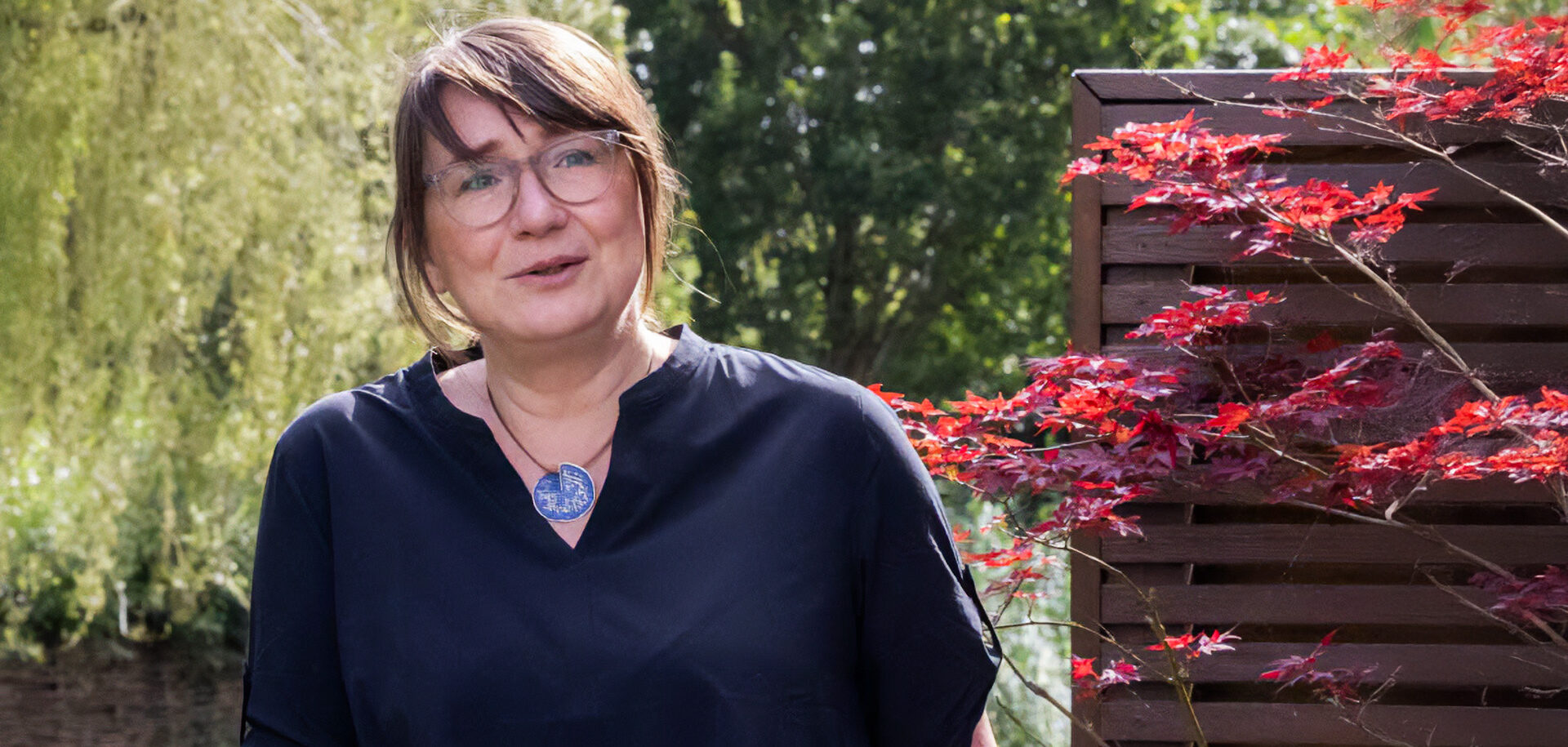
The Ceramic Revolution
For more than two decades, SKF has been unlocking the secrets of hybrid bearing technology and now the company is bringing this advanced solution to the mainstream.
At the heart of this journey are hybrid bearings, which combine advanced ceramic materials with traditional steel components to deliver unmatched performance for high demand applications. Charlotte Vieillard, a materials scientist, has been instrumental in this journey. Joining SKF’s R&D facility in the Netherlands as a graduate researcher, bringing her expertise in non-metallic materials to the development of hybrid bearings. While the company’s reputation is built on the strength of high-quality steel, Vieillard and her colleagues have focussed on harnessing the potential of ceramics.
Hybrid bearings offer many advantages over conventional steel designs, especially in high-performance applications (see fact box). Early adopters of the technology were using hybrids to the extreme. Typical examples included spindles for machine lathes or machining centres with very high speeds and F1 racing cars wheels and gearboxes.
Over the years, says Vieillard, hybrid bearings have found their way into many more products, from the Thrust SSC (supersonic car) and NASA’s Space Shuttle to hospital air fans, building air-conditioning units, windmill generators and many industrial pumps and compressors. Currently, she says, the biggest growth area is in electric motors, which are replacing internal combustion engines in cars, motorcycles and other mobility applications.
These applications benefit from another key advantage of ceramic materials, Vieillard explains. They are excellent electrical insulators, so the bearings are not susceptible to damage from the stray currents that can go through them in high-frequency electrical machines.
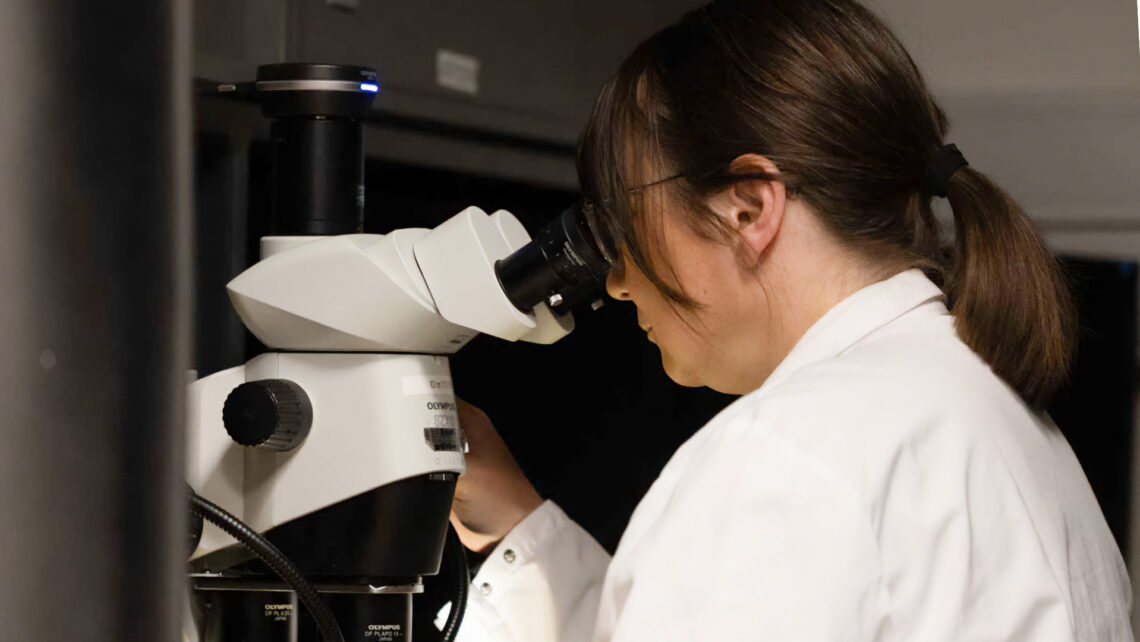
Hard materials, harder to make
But, Vieillard says, there’s one thing standing in the way of wider adoption of hybrid bearings: ceramic rolling elements are difficult and costly to make. “It’s a challenge to make routinely and systematically high-quality silicon nitride rolling elements that can withstand the highly loaded point contacts of a bearing,” she explains. “You need a really good material, and because ceramics are more brittle than steel, you have to secure a high toughness and strength by developing a specific microstructure.”
Ceramic components are made by a sintering process and similar processes to those in powder metallurgy. Fine powders of silicon nitride and other additives are milled together and compacted into a shape, then heated under high pressure until the material “fuses” or sinters into a solid, dense “blank”. The blanks are then ground and superfinished into precision balls and rollers. Production requires tight control over multiple parameters at each manufacturing step to achieve the desired final structure and quality.
“Many companies produce silicon nitride parts,” says Vieillard, “but few achieve today the quality level and consistency we need for bearing components production.”
Costly processes were more acceptable for early hybrid bearing implementation. Customers in the aerospace industry, for example, needed relatively small volumes of product, and they could absorb the higher cost of hybrids in exchange for the performance benefits they offered.
For Vieillard, a key focus throughout her years of working with hybrids has been to ensure that customers received the benefits of hybrids in every bearing SKF delivered. To do this has required understanding the performance of the materials and the finished components as well as the entire hybrid bearing behaviour, the associated detailed components specifications and the inspection or characterization processes as well as paying relentless attention to quality control and inspection processes to ensure that each batch of bearings met all the specifications.
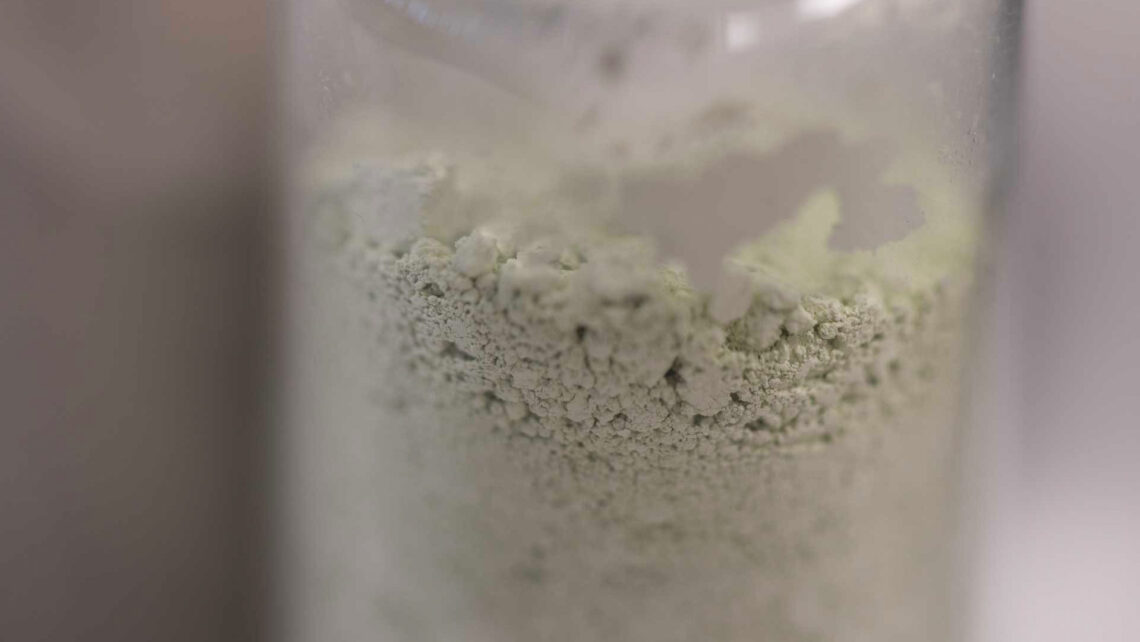
From niche to mainstream
As hybrid bearings move into mainstream applications such as automotive powertrains, Vieillard and her team face a greater challenge. SKF has invested in a full in-house powder-to-finished-product value chain in parallel with strategic suppliers and has developed larger production systems for this new bearing generation.
Not only will the work continue to unveil new performance understanding and life-prediction capabilities of such product performance, striving for fit-for-purpose specifications at best cost, but now more detailed work on manufacturing-step optimization and impact on final product quality is crucial.
SKF’s ceramic community, comprising researchers, designers, developers and production staff, is now tasked with reducing cost by exploring all process improvements and innovations across the entire value chain. This extends from raw-powder selection to finished-product inspection techniques, including automation and improved near-net-shape compaction or sintering methods.
Further research is needed to uncover and understand many of these opportunities, Vieillard says.
Two materials, multiple benefits
Hybrid bearings combine steel raceways with rolling elements made of ceramic material, called silicon nitride. This combination gives hybrid bearings some unique and compelling properties. “Ceramic is 60 percent lighter than steel,” says SKF materials scientist Charlotte Vieillard. “That gives you a weight saving, especially in larger bearings. But the low-weight rolling elements reduce significantly the extra centrifugal forces you normally have on the whole bearing at very high speeds, so a hybrid bearing can now operate successfully at a much higher speed.
“Ceramic also provides a very hard and smooth surface that does not stick to steel easily,” she continues. “That helps reduce friction and surface damage, especially in difficult operating conditions where you don’t have a complete film of lubricant separating the rolling elements from the raceways.”
These mechanisms keep the health of bearing thermals and surfaces under check, which helps the grease and the bearing last longer. Even more magic happens at the interface between ceramic and steel, she says. “With the silicon nitride ceramic being much harder and stiffer than the steel, this bearing contact has another power – the power to better cope with contamination or imperfections in the raceway surface.”
In some cases, Vieillard notes, ceramic rolling elements can flatten out the raised parts of dents and imperfections of the counter steel race, relieving the damage that could come out of it before it can threaten the integrity of the bearing. Add to that the fact that steel and ceramic do not seize together easily and you have a recipe for an extremely durable, long-lasting bearing.
Meanwhile, the use of steel rings makes hybrid bearings a user-friendly option for both bearing manufacturers and end users, as they can be assembled and installed in a manner similar to conventional steel bearings, simplifying manufacturing and making hybrids a plug-in solution for many applications.
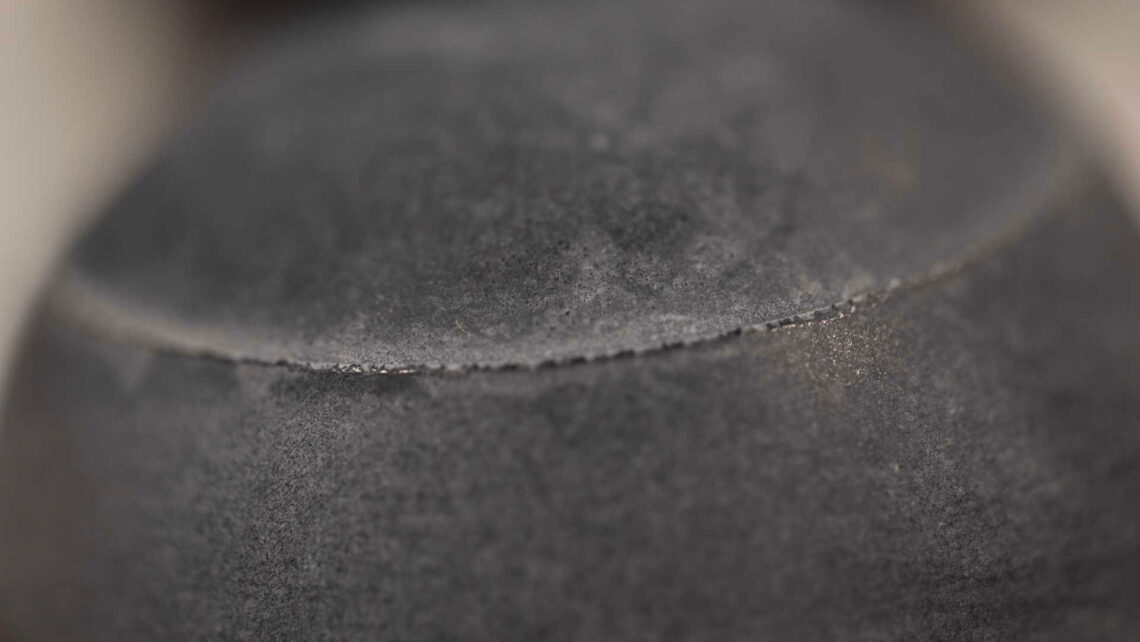