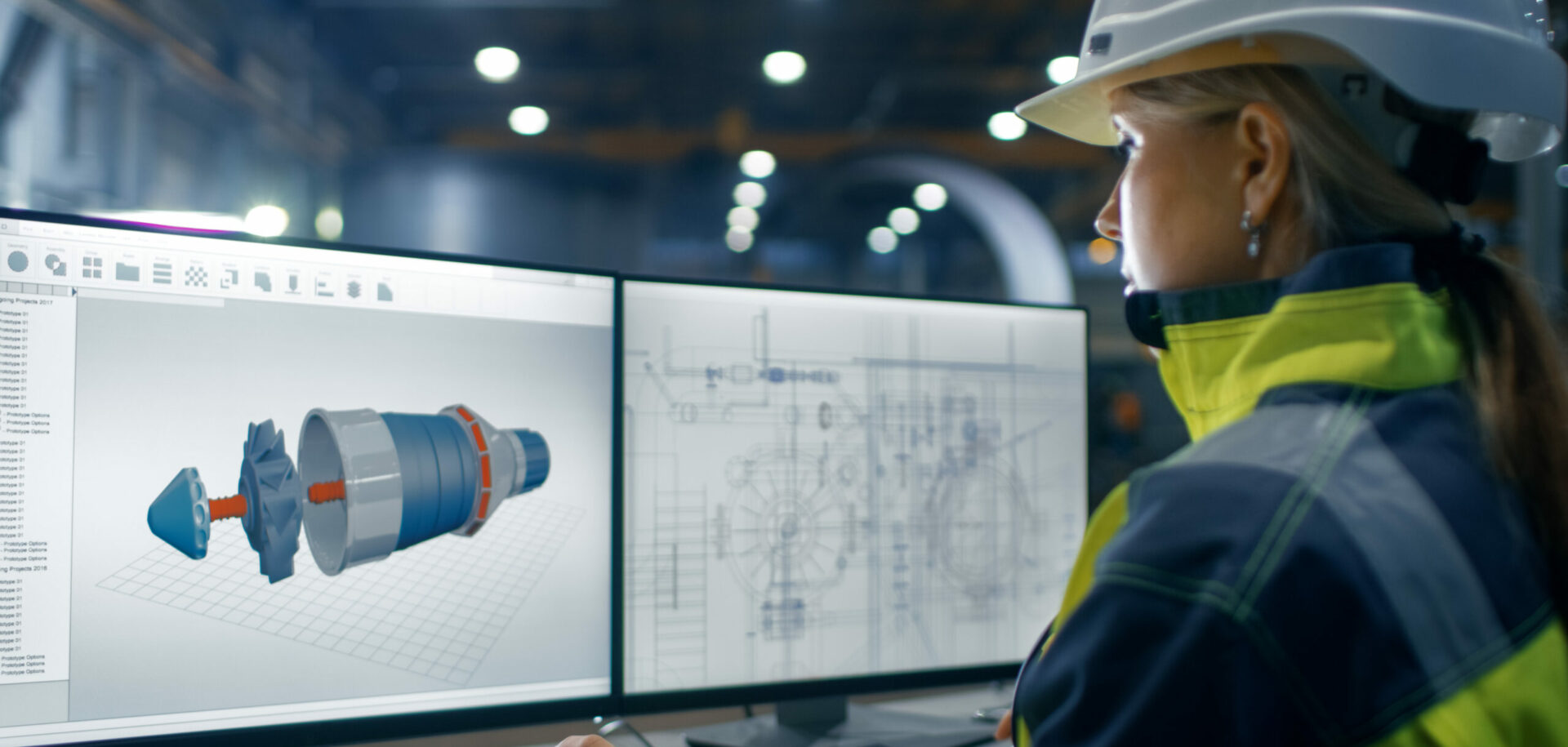
The future of condition monitoring
SKF Insight technology is a new paradigm in condition monitoring focused on measuring parameters that detect damaging operating conditions rather than incipient failure. A key development enabling this approach is the use of a wireless sensor package, integrated into the bearing to record critical parameters that enable a customer to plan intervention to prevent rather than predict bearing failure.
Fact
Condition monitoring has moved into a new era with the development of SKF Insight technology. With the possibility of combining sensors, power, and diagnostics and communications within the bearing, it can make condition monitoring more widely available in applications that were once impossible. Total cost of ownership of a bearing can be radically reduced through highlighting operating conditions that may lead to bearing failures, enabling intervention before damage occurs. SKF Insight is the result of taking a total life-cycle approach to bearing design.
This technology innovation is the culmination of more than 100 years of bearing applications and 30 years of experience in condition monitoring. SKF has a Life Cycle Management approach to its technology platforms and industry knowledge and combines them to work with customers, understanding their needs and demands.
It was out of this approach that SKF became interested in developing an integrated, self-powered sensor package that could communicate the operating environment to which a bearing is subjected. Following extensive R&D work, including miniaturization, solving power generation challenges and developing unique packaging of sensors and electronics, SKF Insight made its official debut during Hannover Messe, Germany, in 2013. With this technology condition monitoring becomes autonomous: It powers itself, and it talks to the Internet. That enables it to be deployed in applications that were never before possible.
The project was born out of the fact that very few bearings fail in service as a result of normal operating conditions. Indeed, most in-service failures result from misuse, neglect, lubrication problems or operating conditions that were not foreseen when the machine was designed or the bearing specified. SKF engineers wondered what would be the outcome if a bearing could detect its operating environment – such as the actual loads it is being asked to carry, the quality of the lubrication, the temperature and so on – and make that information available through the Internet to the plant operator and/or the machine manufacturer. If operating conditions can be monitored, damaging operating conditions can be identified and corrected to make sure that expensive and disruptive failures are avoided, reducing the total cost of ownership and extending the life of the asset.
Traditional condition monitoring looks for early signs of failure by measuring vibration levels. A bearing starts to produce vibration signals when the first small fragments of steel spall off the raceway surface of the rings or the rolling elements. By the time such damage is detectable, it is likely that the end of life of the bearing is getting close – it is already damaged, and it is too late.
By contrast, SKF Insight uses bearing-embedded sensors to monitor the critical parameters that are likely to lead to an early failure, for example lubricant contamination or excessive loads or temperatures (figs. 1 and 2). By proactively eliminating such anomalies, the failure can be avoided. The same technology can be used in a more positive way: By verifying the integrity of an installation and giving a better understanding of the operating environment, a machine may be uprated to extend its life or power rating beyond the initial design.
Combining technology
Bearings have long been considered the heart of rotating machinery. Now, SKF makes them the brain as well. In essence, SKF Insight puts together the technology that can monitor the actual conditions experienced by bearings in a particular application. Embedded sensors measure loads, lubrication conditions, speed, vibration and temperature using power harvested from the application environment (fig. 3).
SKF algorithms and diagnostics interpret this data in terms of the severity of the conditions, or how far the operating conditions are departing from their original design condition. It can also identify excessive loads, duty excursions, lubricant contamination and lubrication problems so that modifications can be made to the operating conditions to avoid damage before it occurs. This package of sensors and algorithms has been named SKF Insight because that is what it provides – an insight into the operating conditions and how those are likely to affect the reliability of the installation.
Intelligent wireless communication technology packaged inside the bearing enables it to communicate within environments where traditional Wi-fi cannot operate. Bearings enabled with SKF Insight create smart networks, communicating through one another and via a wireless gateway to send information relevant to their condition for analysis. The gateway can be local to the machine or local to the plant. System information is either made available to the customer for analysis using SKF @ptitude or sent via the SKF cloud to SKF Remote Diagnostic Centres (fig. 4). From here, dashboards and reports can be made available to the plant operator, the machine manufacturer, SKF or any other authorized person with Internet access. Real-time condition monitoring data is accessible to everyone involved. SKF Insight gives customers more control over planning their machinery maintenance and optimizing their machinery operations than ever before.
By combining integrated SKF Insight technologies with associated asset diagnostic and bearing health services, information relating to actual operating conditions is sent to cloud servers for remote diagnostics, enabling an understanding of the risk of future damage and failure.
Prior to SKF Insight, condition monitoring techniques could only monitor damage after it had occurred. Now, by sensing directly on the bearing, SKF can identify the risk of failure before the first microscopic damage has occurred, and with this information customers can take remedial action to avoid the cause of possible damage to the bearing – adding lubricant, mitigating transient overloads, etc. SKF Insight makes it possible to measure the loads the bearing actually experiences rather than what it was designed for. This valuable information can be routed back into the design phase to improve both the system and bearing design.
Improving accessibility
One of the purposes of SKF Insight technology is to make condition monitoring more widely applicable and accessible, particularly in applications where it has been considered impossible or impractical. This is one reason why the technology has been tested in challenging industries such as wind power (fig. 5), railways (fig. 6) and steel manufacturing.
Wind farms can be remote and difficult to access. SKF is working with customers to integrate SKF Insight technology and develop a smart bearing for wind turbine monitoring. This technology can wirelessly communicate dynamic bearing information to provide loads and lubrication operating conditions within its true operating environment. The cost of changing a wind turbine main bearing in an offshore application can be sufficient to undermine the business case for building the turbine in the first place. Therefore it makes business sense to record loads and lubrication conditions in service and take action to eliminate damaging conditions. It also may allow the turbine to be operated outside its design envelope when load and lubrication conditions are favourable. It is often the case that the most life-consuming operations will be conditions not included in the original design brief.
Within the railway industry SKF is integrating smart components and providing wheel end bearing monitoring solutions. Powered by the rotation of the bearing, these solutions can wirelessly communicate the bearing condition. In this application SKF Insight provides a highly cost-effective means of collecting condition monitoring data, where the risk of failure for each bearing can be determined throughout its service life, allowing optimized maintenance planning and scheduling.
Similarly in the demanding and hostile environment found in the steel industry, SKF has developed a smart bearing solution that can monitor and communicate wirelessly the key parameters used to control and optimize the steel manufacturing process. It has successfully monitored the condition and operating environment of bearings in a continuous caster using embedded self-powered wireless sensors – an environment where cables and external sensors simply do not survive.
Conclusion
The focus of SKF’s technology development today is to reduce the environmental impact of an asset during its life cycle, both in its own and its customers’ operations. SKF Insight technology will make condition monitoring more widely applicable, especially in applications where it was previously impossible or impractical. Maintenance can be scheduled before conventional condition monitoring picks up the early signs of a developing failure. Above all, by acting proactively to eliminate damaging conditions, failures can be eliminated rather than detected. By selecting an SKF bearing with integrated SKF Insight technology, the total cost of ownership can be radically reduced. This is especially true in applications where a large number of points need to be monitored over a large area. A bearing with SKF Insight also offers the typical benefits associated with similar non-integrated condition monitoring solutions, such as better maintenance planning, reduced maintenance costs, optimized manpower resources, improved operational efficiency and virtual elimination of unplanned downtime and disruptive failures.
SKF Insight is a trademark of the SKF Group
SKF @ptitude is a registered trademark of the SKF Group