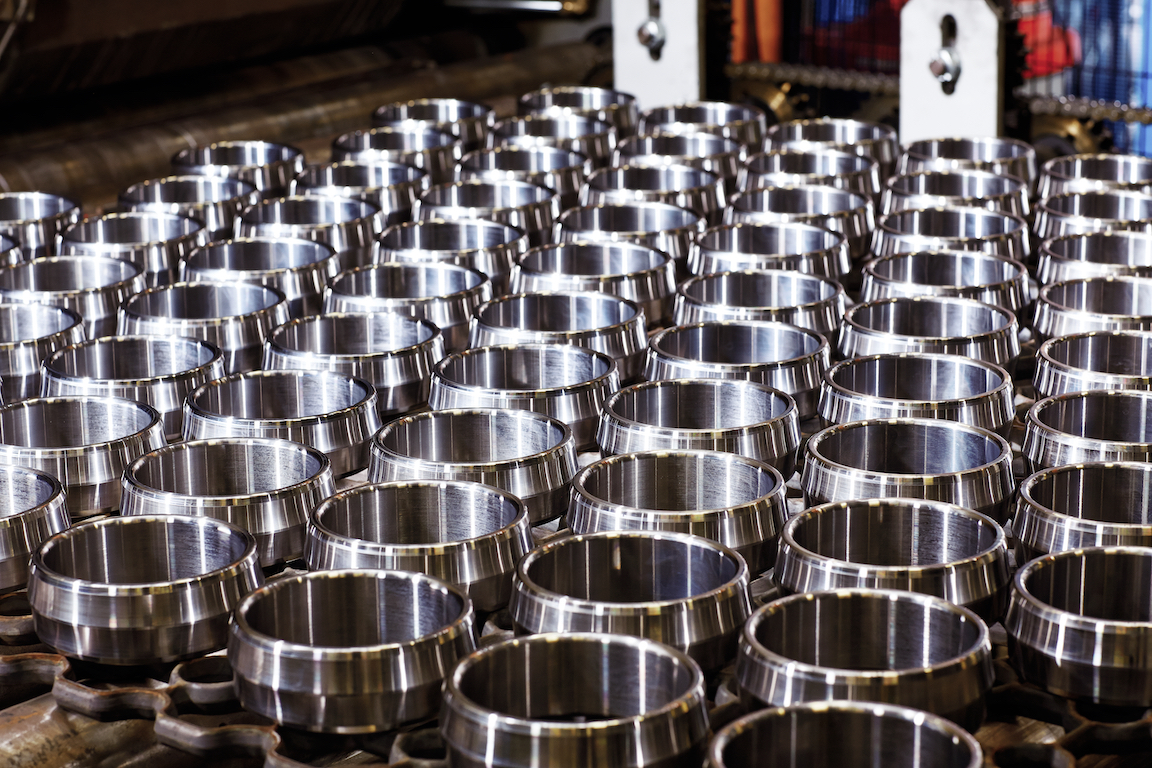
The sweet taste of success
After a devastating financial blow in the 1990s, Philippine sugar-producer Victorias Milling Company is back on top and looking for ways to boost its sustainability and profitability.
The road to Victorias Milling Company (VMC) on the Philippine island of Negros Occidental is busy with large trucks, each groaning under the weight of sugar cane being dropped off for processing. With its lush volcanic soils and tropical climate, the island is well suited to sugar production; 16 of the country’s 32 mills are situated here. At the international airport in the nearby town of Bacolod, a sign proudly welcomes visitors to the “sugar bowl of the Philippines”. VMC, the largest refined-sugar producer in the country, was a pioneer in this area and has been producing the sweet substance since 1919. In 1997, the company fell on hard times and trading of its shares was suspended. It underwent a corporate rehabilitation programme, and a debt restructuring agreement was drafted in 2000. Despite the hardships, the company finished 2012 as the Philippines’ No. 1 refined-sugar producer. Arcadio “Boy” Lozada, vice-president of manufacturing, says the plan is for VMC to be debt-free in 2018. “However, in January 2013, we prepaid 1 billion Philippine pesos (18.6 million euros) and therefore drastically cut our obligations,” he says. “We are quietly optimistic about the future.” In 2012 the island was struck by two typhoons, which thankfully caused only minimal damage. “Sugar milling is an exciting operation; it keeps you on your toes,” Lozada says. Weather, along with the cooperation of the sugar cane farmers and the condition of the operating equipment, acutely influences the mill’s productivity. Although VMC is still recovering from corporate trauma, it has taken some important steps towards increasing its sustainability. For example, bagasse, the fibre that is left behind once sugar cane has been processed, is used in the boiler on the mill. It burns well and is the only fuel required. In addition, VMC recycles its water. Anne Tiongco, corporate communication director at VMC, says sugar mills are traditionally very water-intensive. “Recycling minimizes our dependence on rivers,” she says. “We have also invested in a wastewater treatment plant. The system takes the used water through 15 lagoons for cooling and cleaning before it is let back into the river, so as not to harm the environment. We also have an electrostatic precipitator, which reduces the production of [particulate-heavy] black smoke.” In 2015, the sugar industry in the Philippines will face a severe challenge. The tariff on imported sugar will drop from its current level of 18 percent down to 5 percent, forcing the mills to compete with subsidized foreign sugar. There are several alternative markets for sugar mill products or by-products. Sugar producers are increasingly turning to the production of sugar cane ethanol as well as using molasses for biodegradable plastics. Lozada says he once worked in a sugar mill where the main gearbox bearings were routinely changed every year. “When I asked, ‘How do you know that you have to change that particular bearing?’ they answered that it was standard practice. So we started doing condition monitoring with SKF, and I was surprised at how, in five years, we did not have to change the main gearbox bearings.” Staying No. 1 is tough, and VMC’s 24-hour operation takes its toll on both staff and machinery, Lozada says. Yet VMC boasts higher productivity, a longer milling season and a higher sugar yield than its competitors. “Our higher yield means that even farmers far away will offer their cane to VMC, to get more profit from their crops,” says Tiongco. SKF Microlog is a registered trademark of the SKF Group. Sugar milling is a key business segment for SKF Philippines. SKF has been a partner of Victorias Milling Company (VMC) for 30 years. “If VMC makes a technical improvement, other mills want to follow suit,” says Arnolfo Moncada, head of reliability systems and projects at SKF Philippines. VMC operates some 700 rotating machines, so there is a lot of room for SKF products. Rolling bearings and housings are only the visible part of what SKF offers the company. Training, tools, lubricants and reliable condition monitoring all contribute to VMC’s success. VMC’s Anne Tiongco says there has been a reduction in the machines’ wear and tear thanks to SKF’s maintenance programmes. “It is essential for VMC’s productivity that parts don’t fail and cause downtime,” she says. “SKF’s staff training is important. That is a big part of our partnership.” SKF products and solutions at VMC
SKF and VMC