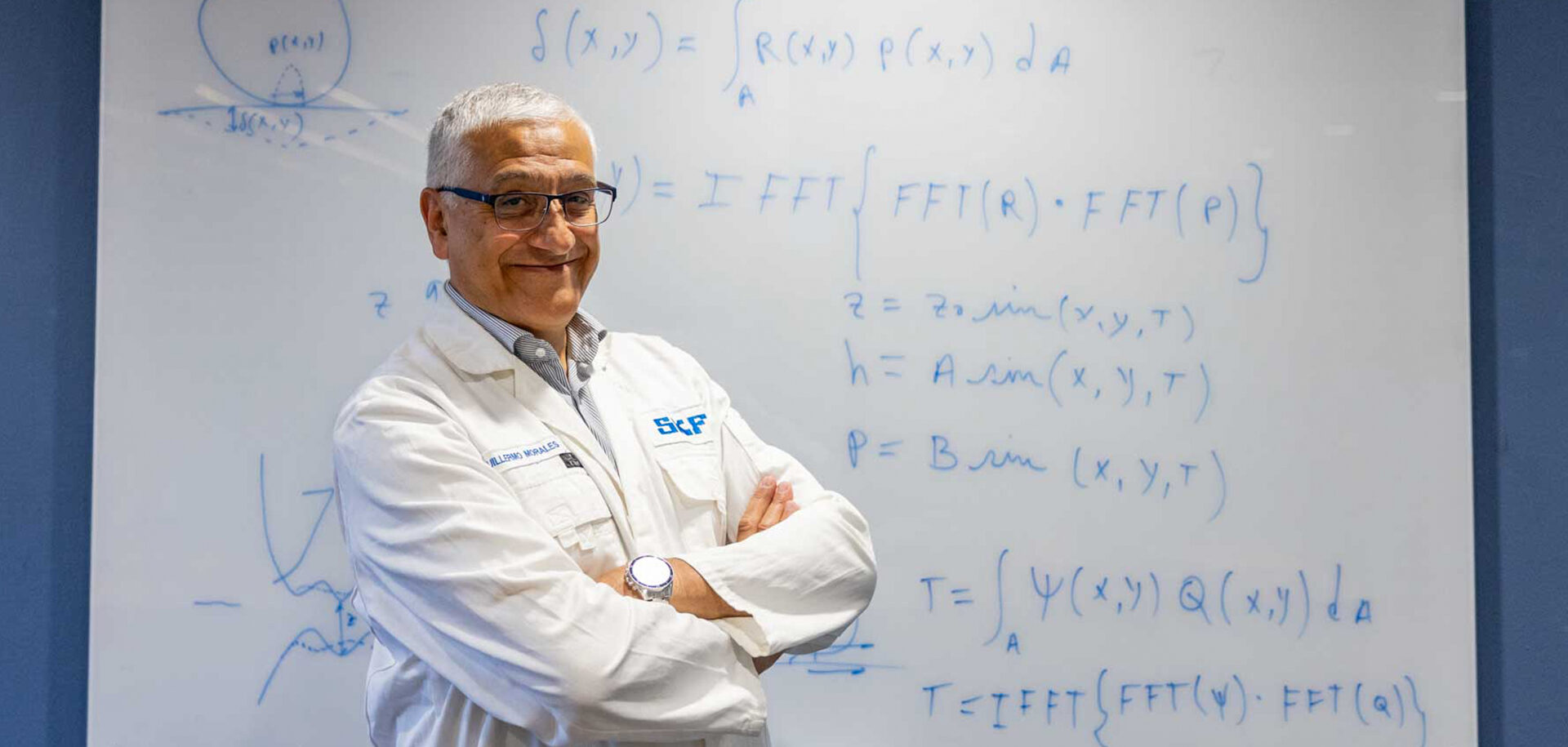
从理论到实践——通用轴承寿命模型的发明者
SKF首席科学家吉列尔莫·莫拉莱斯-埃斯佩杰是轴承寿命预测这一革命性新方法的倡导者。他向《演进》杂志介绍了他的工作,阐述了这项工作对设计工程师、设备制造商和最终用户的积极影响。
机器为什么会出故障?在吉列尔莫·莫拉莱斯的整个职业生涯中,这个根本性问题一直困扰着他。他的足迹曾遍布大半个地球,始终致力于研究顶尖技术以及探索微观缺陷的细微之处。
莫拉莱斯拥有墨西哥和法国双重国籍,目前就职于SKF荷兰研究与技术开发中心,主要负责监管工业研发项目,并在法国里昂大学和英国帝国理工学院担任高级教授职务。他对旋转机械学科做出了诸多贡献,其中最重要的一项是他研究出了在真实工作条件下预测滚动轴承使用寿命的新方法。
莫拉莱斯表示:“只需通过计算应力并确保不超过疲劳极限,就能设计出许多机械部件。用这种方式,你就不必担心疲劳问题,因为这个问题似乎不会出现。但是,轴承的运行周期太长了,需承受的应力也太大了,结果总会出现疲劳。你需要通过数学公式来推算出这些应力及其对部件寿命的影响。”
疲劳对轴承寿命的影响工程师们早已有所认识,但要开发出能够解释这种疲劳现象的模型却历经了几代人的努力。莫拉莱斯说:“你无法以确定的方式来预测轴承寿命。运行条件、材料或几何形状的微小变化都可能会对轴承寿命产生重大影响。因此,必须将统计学与物理学相结合,才能做出有效的预测。”
最早采用这种组合方法来预测轴承寿命的模型问世于20世纪中期,而SKF的科学家们一直走在了这些模型开发的最前沿。莫拉莱斯说:“早期的那些论文介绍了我们至今仍在使用的基本概念,比如轴承的静态和动态承载能力之间的区别。”
在随后的几十年里,随着理论理解的深入和实践经验的积累为研发出更复杂的模型铺平了道路。例如,在20世纪 80年代,工程师们发现了如何在预测轴承寿命时考虑到疲劳极限的问题,即低于这一应力水平时,材料几乎不会产生疲劳。
结缘摩擦学
随着建模技术的进步,轴承寿命模型也得到发展。 莫拉莱斯解释说:“这些20世纪的模型主要基于次表面疲劳。然而,得益于制造技术的进步,例如超洁净钢材的使用,次表面疲劳的难题已基本解决。”
尽管这些现代轴承仍可能会出现疲劳,但其失效更可能是由于一系列不同的原因而引发,包括润滑不良、污染、摩擦发热或电气损坏等。莫拉莱斯指出:“在大多数情况下,问题不是出在轴承本体内部。而是源自其表面。”
而对表面特征的研究正是吉列尔莫·莫拉莱斯非常了解的领域。在墨西哥获得机械工程学士和硕士学位后,他前往英国剑桥大学,继续攻读摩擦学博士学位。
他说:“读博期间,我一直致力于为润滑接触中粗糙度的特性及其影响建模。在摩擦学中,‘粗糙度’是描述任何微几何特征的通用术语。它可能表现为划痕、压痕或表面纹理。这些表面特征让摩擦学专家头疼不已,因为它们会破坏润滑油膜,而这层油膜正是机械部件能够长时间顺畅运动的关键。”
然而,为粗糙度建模并非易事。莫拉莱斯进一步解释道:“过去,人们采用数值方法来模拟粗糙度,但对计算机来说,这是一个非常困难且耗时的挑战。你需要构建一个包括五个方程式组成的系统,其中的五个未知数在时间和空间上均有分布。”
莫拉莱斯的博士论文的研究重点是要找到一种更简便、更快速的方法来解决复杂的粗糙度数学问题。他将粗糙度分解为正弦波,极大简化了所需的计算,同时仍可将任何类型的表面缺陷建模为不同波的集合。
与旧方法相比,这种新方法在分析复杂表面时所需的计算能力降低了几个数量级。在剑桥大学的学习经历不仅让莫拉莱斯对摩擦学产生了终生的兴趣,而这种兴趣也最终引领他加入了SKF。
2000年1月,莫拉莱斯加入了SKF的研究实验室,并迅速为他的建模方法找到了新的应用。其中之一是模拟轴承在混合润滑环境下的性能。在这种环境下,污染或润滑剂不足会导致轴承内部出现金属与金属直接接触的区域。此外,他采用新的建模方法来评估轴承在制造、运输或安装过程中因处理不当而可能产生的小压痕对其寿命的影响。
通用寿命模型
几年后, 莫拉莱斯和他的同事们成功地将混合润滑和表面损伤模型用于解决SKF内部及其客户的各种问题。2012年,一位新任技术总监向莫拉莱斯提出了一个更大的挑战。莫拉莱斯回忆说:“他指出,我们的轴承寿命模型虽然实用,但不够灵活。想要将模型适用于不同的问题或整合新知识,需要付出很多努力。”
技术总监的要求虽看似简单,实则挑战性极大。莫拉莱斯和他的团队能否凭借对表面条件如何影响轴承寿命的了解,构建一个能够更准确地预测真实工况中轴承寿命的通用模型呢?
莫拉莱斯和他的团队花了两年时间应对这一挑战。他表示:“我们已经掌握了一些关键要素。但要构建一个通用的轴承寿命预测模型,必须模拟不同轴承在不同工况下数百万次循环的运行情况。如果没有高效的求解程序,这是无法实现的。”
此外,该模型的构建还要求团队在某些新领域实现突破。莫拉莱斯特别指出,他们必须开发出一种方法,这种方法能够将新的表面损伤模型与评估次表面疲劳的传统方法相结合。
一种模型,解决万千难题
在2015年汉诺威工业博览会上,SKF首次面向客户推出了针对传统钢制轴承的通用轴承寿命模型的最初版本,这一概念为设计工程师日常面临的诸多挑战提供了即时解决方案。莫拉莱斯说:“借助更精准的寿命预测模型,我们就能设计出性能更佳的机器。我们的模型不仅可以帮助设计师为其应用设备选择最佳的轴承尺寸和类型,还能够为终端客户提供更加可靠的维护与更换间隔时间的建议。”该模型提升了资源利用率,减少了设备故障和过早更换仍处于使用寿命期限内的轴承。
在过去十年中, 莫拉莱斯和他的同事们不断深耕,将通用轴承寿命模型的应用范围扩展至新型轴承,特别是针对适用于透平机械、电动汽车变速器等苛刻应用场合的混合陶瓷轴承,成功构建了相应的模型。同时,他们还紧跟传统轴承技术的革新步伐,将新型钢材与更先进的热处理技术等最新成果融入模型当中。
通用轴承寿命模型还帮助SKF顺应行业内的其他重大趋势。例如,在努力寻找进一步降低资源消耗方法的大环境下,客户也希望通过越来越多地转向再制造来延长大型轴承的使用寿命。通用轴承寿命模型能够预测表面损伤累积的速率,为客户提供再制造间隔时间的依据,从而做出明智决策。
展望未来,作为首席科学家,吉列尔莫·莫拉莱斯所作的工作远不止与轴承寿命模型相关,但他对通用轴承寿命模型的发展仍然保持着浓厚的兴趣。他介绍说:“我们已经开发出了一种灵活且可扩展的方法,可以为不同的轴承、运行条件和失效模式建模。但所有这些模型都需要通过实验和测试数据来验证。如今,先进的传感器技术能让我们更好地了解轴承内部的状态,这些数据将帮助我们拓展和改进建模方法。”
你能解决这个数学问题吗?
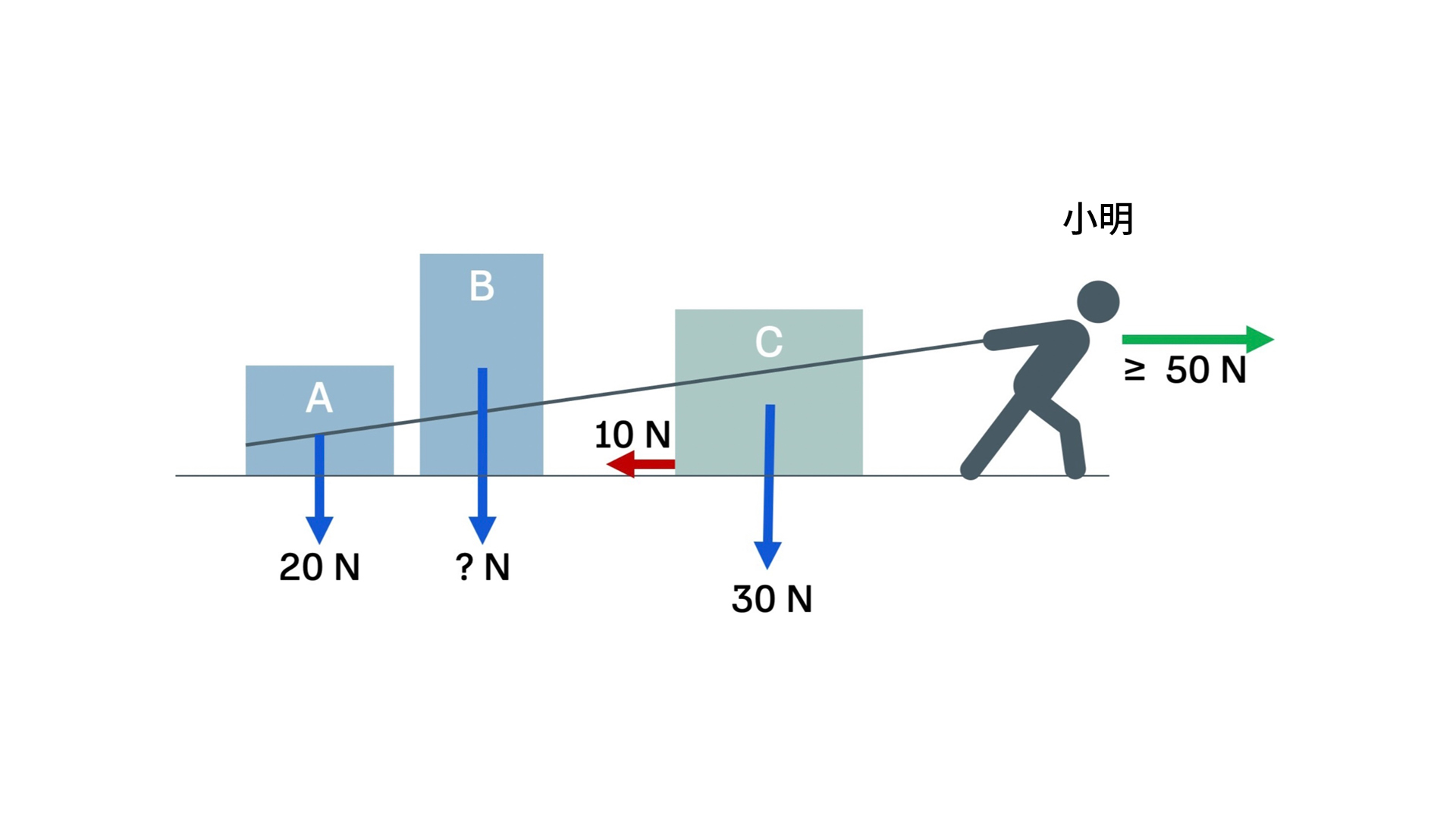
木块B的重量是多少?
背景知识:
阿蒙顿第一定律:摩擦力与作用在物体上的法向力成正比。
阿蒙顿第二定律:摩擦力与接触面的面积大小无关。
摩擦第三定律:摩擦力还取决于接触面的性质。