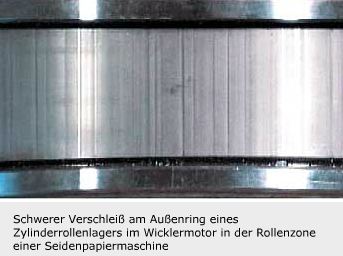
Entscheidungshilfe-system zur Untersuchung von Lagerausfällen
Untersuchung und Auswertung von Wälzlagerschäden und -ausfällen sind für SKF und die Kunden von strategischer Bedeutung. Umfangreiche Erkenntnisse
zu Lagerschäden sind für SKF Ingenieure in einem Webb-gestütztem Entscheidungshilfesystem namens BearingDetective zusammengefasst
Das Programm BearingDetective bietet beim Entscheidungsprozeß rund um Wälzlager schnell und reproduzierbar vernünftige Informationen und Antworten. Es soll verhindern, dass ein Lagerschaden oderausfall mehr als einmal auftritt. Wie jede wissensbasierte Softwarelösung sammelt BearingDetective alle verfügbaren Informationen und Erfahrungswerte zu Lagerschäden, von grundlegenden Angaben bis zu Ergebnissen der technischen Praxis.
Aktuelle wissensbasierte Systeme nutzen die Erfahrung der Expertensysteme aus den 80er Jahren, auch wenn diese in bezug auf “Denkvermögen” und Rechenleistung längst nicht optimal waren. Sie waren oft als Entscheidungsbäume strukturiert, die von Symptomen zu den möglichen Ursachen führten.
Eine solche eindeutige Kausalbeziehung besteht jedoch in der Wirklichkeit nicht. Das liegt daran, dass die Ursachen (etwa unsachgemäßer Einbau der Lager) die Symptome (etwa Anzeichen von Rost) hervorbringen und nicht umgekehrt.
Ein Modell, das eine Beziehung von den Ursachen zu den Symptomen herstellt und bei dem die “möglichen Ausfallzustände” mit einer gewissen Unsicherheit behaftet sind, ist für die physikalischen Erscheinungen in Lagern im Gebrauch wesentlich besser geeignet. Für Entwicklung des BearingDetective wurde dieser Ansatz weiterverfolgt.
Wissensbasiertes System
In einem wissensbasierten System wird zwischen dem Wissensmodell mit seiner Darstellungsform des Wissens und dem Denkprinzip zur Entwicklung der Problemlösungsfähigkeit unterschieden. Wissen lässt sich unterschiedlich darstellen:
- Fälle: Umfangreiches Wissen zu Lagerausfällen findet sich in Fallbeispielen. Leider sind viele Fälle aus der Praxis nicht gut dokumentiert, und auch die dokumentierten Parameter oder Schlussfolgerungen aus dem Ausfallablauf sind uneinheitlich. Sie können jedoch dazu dienen, andere Wissensdarstellungen in ein Modell zu fassen oder zu verifizieren.
- Regeln: Die Wenn-Dann-Regeln zwischen beobachteten Symptomen und möglichen Ursachen können verallgemeinert werden. Das ist jedoch nicht anzuraten, weil verschiedene Ursachen ähnliche Wirkungen hervorrufen können, die als ähnliche Symptome sichtbar werden.
- Künstliche neuronale Netze: Mathematische Beziehungen zwischen Symptomen und Ursachen lassen sich anhand von exemplarischen Lagerausfällen ableiten. Leider liegt keine ausreichend große Zahl solcher eindeutigen Fälle vor.
- Probabilistische Netzwerke: Man kann visuelle Netze ableiten, in denen Zusammenhänge durch Kausalverbindungen hergestellt werden. Daneben werden Wahrscheinlichkeiten zugewiesen, die die Ausprägung dieser Beziehungen angeben. Dieses System löst das Problem der Analyse von Lagerausfällen am besten, weil es die richtige Kausalität von Bedingungen zu Beobachtungen herstellt.
Die Analyse von Lagerschäden und -ausfällen ist grundsätzlich ein Diagnoseproblem. Wenn ein Kranker mit Beschwerden zum Arzt kommt, befragt dieser ihn zunächst zu Kennwerten zu seinem Körper und Leben wie Gewicht, Zigarettenkonsum usw. (Bedingungen).
Anhand dieser Angaben entwickelt der Arzt dann Hypothesen über die vermutliche Krankheit (Ausfallarten). Er verifiziert oder verwirft diese Hypothesen durch weiteres Befragen und Untersuchung des Patienten (Symptome).
Der Prozess der Schadens- oder Ausfallanalyse entspricht der Arbeitsweise eines Arztes. Eine korrekte Diagnose besteht aus zwei wohldurchdachten Schritten:
1. Aufstellen der Hypothese: Mögliche Hypothesen zum Ausfall werden anhand von Daten aufgestellt. Der Arzt stellt dem Patienten beispielsweise Fragen, um eine Vorstellung davon zu bekommen (Hypothese), was nicht stimmt.
2. Bestätigen oder Widerlegen der Hypothesen: Die Hypothesen werden nacheinander untersucht und bestätigt oder widerlegt. Der Arzt untersucht den Patienten mit speziellen Testverfahren (Blutdruck, Puls usw.) auf die wahrscheinlichsten Krankheiten.
Mit einem probabilistischen Netzwerk wird über Vorwärts- und Rückwärts-Wahrscheinlichkeitsberechnungen die Beweisführung in zwei Stufen durchgeführt.
Probabilistisches Netzwerk
Ein probabilistisches Netzwerk ist ein visuelles Netz, in dem Knoten über Kausalbeziehungen miteinander verbunden sind und in dem Wahrscheinlichkeitsrechnungen gelten. Das Netz für die Analyse von Wälzlagerausfällen verfügt über vier Kategorien von Knoten: Bedingungen, interne Mechanismen, Ausfallarten und beobachtete Symptome.
Die Bedingungen stehen für die Betriebsbedingungen des Lagers, zum Beispiel Drehzahl, Bauart, Belastung, Temperatur, Einbau, Umgebung. Die internen Mechanismen bezeichnen die physikalischen Erscheinungen, die im Betrieb auftreten, zum Beispiel Schmierung, Unterbrechung des Schmierfilms, Gleitkontakt.
Ausfallarten sind unterschiedliche Ausfallursachen und -verläufe wie Ermüdung unterhalb der Oberfläche und Reibkorrosion (siehe Tabelle 1). Die beobachteten Symptome sind die erkennbaren Phänomene im Lager und außerhalb, zum Beispiel Verfärbung, Ausbröckelungen, Rost.
Rund 150 Knoten sind über Kausalbeziehungen zwischen den Bedingungen der Lageranwendung, den verdeckten Mechanismen, den Ausfallarten und den beobachteten Symptomen miteinander verbunden. Die Knoten wurden festgelegt, und die Kausalbeziehungen und Wahrscheinlichkeiten sowie die erläuternden Texte (für jeden Knoten) mit Beispielen und Abbildungen ausgearbeitet. Insgesamt sind etwa 250 Abbildungen in das System integriert.
1. Schritt der Berechnung
Aufstellen der Hypothese: Sobald das Modell des Netzes erstellt ist, beginnt die Beweisführung. Die Ausgangsknoten (ohne Input) haben zwei oder mehrere Zustände. Jedem Zustand wird eine höhere Wahrscheinlichkeit zwischen 0 und 1 zugewiesen, wobei die Summe der Zustände größer als 1 ist. Beispiel:
- P (Beschleunigungen = ZUTREFFEND) = 0,05
- P (Beschleunigungen = NICHT ZUTREFFEND) = 0,95
Auf der Bedieneroberfläche kann der Nutzer festlegen, ob für die Beschleunigung das Attribut “zutreffend” gilt. Dadurch werden die obigen Wahrscheinlichkeiten in 1,0 bzw. 0,0 abgeändert. Im Netz sind Tabellen der bedingten Wahrscheinlichkeiten definiert (Tabelle 2).
Wenn Knoten mehr als zwei Zustände haben (mehr als „zutreffend” und „nicht zutreffend”) oder wenn mehr Eingabe-Beziehungen bestehen, werden die Tabellen umfangreicher. In den Tabellen der bedingten Wahrscheinlichkeit berechnen sich die Wahrscheinlichkeiten der anderen Knoten wie folgt:
- P(B) =
P(B|Ai) · P(Ai), für alle i wobei P(B|Ai) bedingte Wahrscheinlichkeit bei Bedingung Ai ist. Beispiel:
- P (Gleitkontakt = ZUTREFFEND ) = 0,6 x 0,05 + 0,2 x 0,95 = 0,22
- P (Gleitkontakt = NICHT ZUTREFFEND ) = 0,4 x 0,05 + 0,8 x 0,95 = 0,78
So werden alle möglichen Wahrscheinlichkeiten der Knoten errechnet, wobei den Ausgangsknoten die höhere Wahrscheinlichkeit zugeordnet wird. Mit Annahme der Betriebsbedingungen als Ausgangsknoten können die Wahrscheinlichkeiten der Ausfallmodi bestimmt und eingeordnet werden (Erstellung der Ausfall-Modus-Analyse).
2. Schritt der Berechnung
Verifizieren oder Verwerfen durch Umkehren: Jede aufgestellte Hypothese muss bestätigt oder verworfen werden. Dies geschieht durch eine Untersuchung des Lagers – von der Sichtprüfung hin zu einfachen oder hochkomplexen Laboruntersuchungen.
Dazu ist zunächst zu klären, wie die Wahrscheinlichkeiten von Beobachtungen die Wahrscheinlichkeiten der Ausfallhypothesen beeinflussen. Da hier unterschiedliche kausale Zusammenhänge vorliegen, ist Rückwärts-Beweisführung angebracht. Grundsätzlich sieht sie wie folgt aus:
- P(B|C) = P (C|B) x P (B) / P(C)
Das bedeutet, dass sich der Glaube an Hypothese B, die Nachweis C erbringt, durch Multiplikation unseres früheren Glaubens P(B) mit der Bedingungswahrscheinlichkeit P(C|B) errechnet, und dass C zutreffend ist, wenn B zutreffend ist.
Die Bedingungswahrscheinlichkeiten P(C|B) sind im Netz als Kausalbeziehung modelliert, wobei P(B) aus der Vorwärts-Beweisführung (Schritt 1) kommt und P(C) bei der Lageruntersuchung bestimmt wird. Diese Beobachtungen dienen als Nachweis für die Ausfallhypothese. P(B|C) wird als spätere Wahrscheinlichkeit bezeichnet, da P(B) die frühere Wahrscheinlichkeit ist.
Statt alle möglichen Beobachtungen und nicht bestimmten Bedingungen zu untersuchen, werden – in Abhängigkeit von der Ausfallhypothese (oder internen Mechanismen) nur die wesentlichen vorgeschlagen, die zu untersuchen sind. Mit anderen Worten, die Bedingungen der Anwendung bzw. Beobachtungen haben den größten Einfluss auf die Ausfallhypothese.
Dieser Einfluss wird mit einer mathematischen Größe bestimmt. Für alle nicht bestimmten Bedingungen bzw. Beobachtungen liegt diese Größe zwischen 0 und 100.
Ein Beispiel finden Sie in den Abbildungen. Schließlich wird durch Untersuchung der Betriebsbedingungen und der Beobachtungen die Wahrscheinlichkeit der einzelnen Ausfallhypothesen festgestellt und in eine Rangordnung gebracht. Dies ist dann die Schlussfolgerung der Lagerschadensanalyse.
BearingDetective verfügt über verschiedene bedienerfreundliche Funktionen. Eine einfache Anleitungsdatei erleichtert den Einstieg. Das System bietet eine Übersetzung der wichtigsten Begriffe in Englisch, Deutsch, Französisch und Schwedisch.
Über eine Datensteuerung können die Daten einer bestimmten Arbeitssitzung gespeichert und gesucht werden. Die Datei „Typische Fälle” führt den Nutzer durch das Programm und seine Funktionen. In Word oder HTML lässt sich bequem ein umfangreicher Bericht mit allen relevanten Bedingungen, Beobachtungen und Wahrscheinlichkeiten des Ausfallmodus erstellen.
Praxisbeispiel
Als „Typische Fälle” werden häufige Ausfallursachen vorgestellt. Sie zeigen, wie der BearingDetective bei der Suche nach der Ausfallursache eines Lagers zum Einsatz kommt, etwa beim Elektromotor in einer Papiermaschine. Ein stromisoliertes Zylinderrollenlager NU 322 ECM/C3VL024 sitzt im Wicklermotor in der Rollenzone einer Seidenpapiermaschine. Die Drehzahl des Motors ist variabel (400 VAC mit Frequenzwandler) von 1000 bis 1500 min-1. Nach nur einem Monat Betriebsdauer trat erheblicher Verschleiß an Innen- und Außenring auf.
Beim Laden des Beispielfalls im BearingDetective werden alle bekannten Betriebsbedingungen der Anwendung eingesetzt (1. Schritt). Die erste Hypothese möglicher Ausfallmodi wird anhand dieser Bedingungen durchgerechnet.
An diesem Punkt der Analyse zeigt der BearingDetective einen hohen Wahrscheinlichkeitswert für Riffelbildung, Haftverschleiß und Stromdurchtritt an. Auf den ersten Blick erscheinen Stromdurchtritt und Riffelbildung unwahrscheinlich, weil doch stromisolierte Lager eingesetzt werden und alle Maschinen zur Dämpfung auf Gummi gelagert sind.
In einem zweiten Analyseschritt untersucht der Nutzer dann das Lager auf Symptome des Ausfalls. Klicken auf “Untersuchen” zeigt die für den ausgewählten Ausfallmodus wichtigsten Schadenssymptome an. Das Lager wird zuerst auf Riffelbildung hin untersucht.
Weil keine flachen Eindrückungen vorliegen, die die Riffelbildung bestätigen würden, wird diese Hypothese verworfen. Die Analyse wird mit der Untersuchung auf die Symptome von Haftverschleiß fortgesetzt. Auch hier sind keine Symptome sichtbar.
Bei der Untersuchung auf die Symptome von Stromdurchgang werden bei Vergrößerung der Laufbahnoberfläche kleine Krater gefunden, die den Stromdurchgang bestätigen. Der Kunde fand daraufhin tatsächlich ein Erdungsproblem in der Rollenzone, die den Stromdurchtritt durch das Lager verursacht hatte.
Schlussfolgerungen
BearingDetective bietet schnelle und zuverlässige Unterstützung bei der Untersuchung von Lagerschäden und -ausfällen. Das System im Internet hilft den SKF Ingenieuren bei der Fehleranalyse und bei der Unterstützung von Kunden zur Behebung von Lagerschäden.