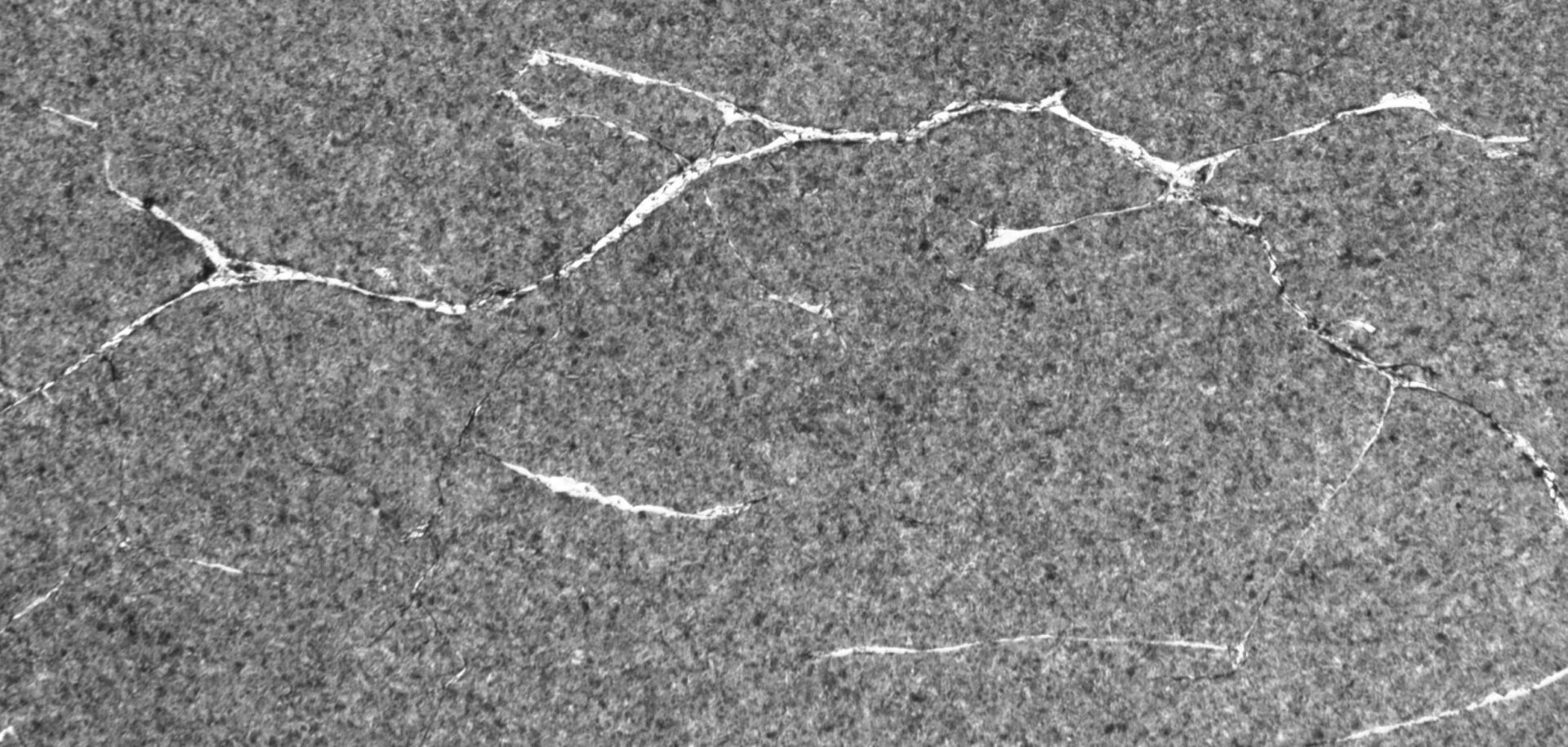
„White Etching Cracks“
Lager sind betriebswichtige Maschinenkomponenten für die Lastaufnahme und Bewegungsübertragung. Die Herausforderung der immer größer werdenden Leistungsdichte im modernen Anlagenbau stellt immer höhere Anforderungen an die Tragfähigkeit und Zuverlässigkeit der Lager.
Lagerausfälle aufgrund von Wälzkontaktermüdung sind heute eher selten, und die effektive Gebrauchsdauer von Wälzlagern liegt normalerweise weit über der berechneten Lebensdauer. Es gibt jedoch Fälle, in denen Lager in speziellen Anwendungen bei 5 bis 10 Prozent der berechneten Lebensdauer vorzeitig ausfallen.
Vorzeitige Lagerausfälle treten typischerweise in sehr kurzen Abständen hintereinander auf, d. h. die Weibull-Verteilung weist im Vergleich zur klassischen Wälzlagerermüdung eine hohe Steigung auf (Bild 2).
Ein charakteristisches Merkmal vieler frühzeitiger Lagerausfälle ist das ausgedehnte, unter der Oberfläche liegende Rissnetzwerk mit einem weiß anätzenden Erscheinungsbild, das allgemein auch unter der Bezeichnung „White Etching Cracks“ (WEC) bekannt ist (Bild 1). Solche Risse breiten sich typischerweise bis an die Oberfläche aus und verursachen Ausbrüche auf der Lagerlaufbahn, die üblicherweise bei Feldretouren aus Anwendungen wie Windgetrieben [1], Kfz-Antriebssträngen, Generatoren und peripheren Zusatzeinrichtungen [2][3], Papiermaschinen und Schiffsantrieben [4] festgestellt werden. Einige typische Beispiele sind in Bild 3 dargestellt. Die Hauptursache dieser Ausfälle wird seit rund 15 Jahren intensiv diskutiert, und es wurden verschiedene Hypothesen aufgestellt, die auf Untersuchungen aus unterschiedlichen Perspektiven basieren. Eine umfassende Überprüfung und Analyse der verschiedenen Hypothesen findet sich in den Referenzen [5][6]. Die Tatsache, dass vorzeitige Lagerausfälle in den letzten Jahrzehnten aus unterschiedlichen Perspektiven betrachtet wurden, hat zu einem besseren Verständnis der spezifischen Aspekte des Problems geführt. Allerdings besteht bei den Hauptbeteiligten auf dem Gebiet der Lagerausfallanalyse noch immer kein Konsens über die Hauptursache und die Ausfallmechanismen.
In den vergangenen vier Jahren hat SKF Studien, Untersuchungen und Forschung zum Phänomen der WEC intensiviert, um zu klären, welche Rolle WEC bei der Wälzlagerermüdung und der beschleunigten Wälzlagerermüdung (vorzeitige Ausbrüche) spielen. Während das Thema in der materialwissenschaftlichen Fachwelt noch immer diskutiert wird, weisen die Ergebnisse von SKF vor allem darauf hin, dass WEC am Ende der Versagenskette auftreten und eine natürliche Folge von Rissnetzwerken in vorzeitig ausgefallenen Lagern sind. WEC werden eher als Symptom denn als Hauptursache für Ermüdungsversagen angesehen. In diesem Beitrag wird eine mehrheitlich konsensfähige Sichtweise der SKF Experten auf vorzeitige Ausfälle und WEC dargelegt. Außerdem wird eine Definition von WEC vorgeschlagen, deren Ursachen werden diskutiert, und es wird ein System für alle Ausfallursachen vorgestellt, die zur Entstehung von WEC führen.
„White Etching Cracks“
„White Etching Cracks“ sind Risse im Gefüge von Wälzlagerstahl, die mit weiß anätzenden Bereichen („White Etching Areas“, WEA) „dekoriert“ sind. „White Etching“ bezieht sich auf das weiße Erscheinungsbild des veränderten Gefüges einer polierten und geätzten Stahlprobe. Die betroffenen Bereiche bestehen aus feinstem, nanokristallinem, karbidfreiem Ferrit bzw. Ferrit mit einer sehr feinen Verteilung der Karbide. Die WEA werden durch Amorphisierung aufgrund von Reibung an den Rissoberflächen beim Überrollen gebildet. Diese Bereiche erscheinen unter dem Mikroskop aufgrund ihrer geringen Ätzreaktion auf das Ätzmittel weiß. Die weiß anätzenden Bereiche um die Risse herum sind ca. 10 bis 50 Prozent härter als das sie umgebende, nicht betroffene Gefüge.
Ursachen für die Entstehung von „White Etching Cracks“
WEC bei Wälzlagerermüdung
Bei kleinen, hoch belasteten Lagern mit langer Gebrauchsdauer ist bekannt, dass die Lager mehrere Ermüdungsphasen durchlaufen, bis es zum Ausfall kommt („Ermüdung bei hoher Lastspielzahl“) [7]. Die erste Phase ist dabei der „Shakedown“, der zu mikroplastischen Verformungen, Kaltverfestigung und allmählichem Aufbau von Eigenspannungen führt. Beim „Shakedown“ kann auch die Lageroberfläche mikroplastischen Verformungen ausgesetzt sein, wobei Oberflächenunebenheiten abgeflacht werden. Nach dem „Shakedown“ ist der überwiegende Teil der Lagerlebensdauer geprägt von fortschreitenden Gefügeveränderungen [8]. In dieser Phase verändert sich die Karbidverteilung aufgrund der mikroplastischen Verformungen [9][10]. Die Veränderungen im Gefüge und Rest-Austenit gehen mit einem gleichzeitigen Aufbau von Eigenspannungen einher. Im fortgeschrittenen Stadium der Wälzlagerermüdung treten sowohl dunkel anätzende Zonen („Dark Etching Regions“, DER) als auch „White Etching“, „Low-Angle Bands“ (LAB) und „High-Angle Bands“ (HAB) auf (Bild 4 links). Obwohl HAB und LAB ebenfalls weiß anätzend sind, unterscheiden sie sich optisch von der unregelmäßigen WEC-Beschaffenheit, die bei einigen Lagerfrühausfällen zu beobachten ist. Daraus lässt sich schließen, dass die unregelmäßige WEC-Beschaffenheit nicht Teil der Wälzlagerermüdung ist. Allerdings unterscheidet sich das Gefüge dieser weiß anätzenden Bereiche in seiner kristallinen Struktur nicht wesentlich von den weiß anätzenden Bereichen, die bei vorzeitigem Ausfall zu beobachten sind.
Bei mittelgroßen bis großen Lagern treten die o. g. Effekte nicht unbedingt in derselben Form auf wie bei kleinen, hoch belasteten Lagern. Wie andere mechanische Komponenten können diese Lager typischerweise durch das Versagen ihres schwächsten Glieds ausfallen (z. B. aufgrund bereits vorhandener Gefügefehler wie Einschlüsse und Poren). Wie in ISO/TR 1281-2:2008 erläutert, nimmt die Ermüdungsgrenze ab einem mittleren Lagerdurchmesser von 100 mm ab. Des Weiteren wird – im Vergleich zu kleineren Lagern – bei größeren Lagern bei gleichem Kontaktdruck ein größeres Volumen mit möglichen Schwachstellen belastet. Die in allen Lagerstählen natürlich vorkommenden Einschlüsse sind beispielsweise solche Schwachstellen [11]. Ein weiterer Einflussfaktor ist der Kontaktdruck selbst. Beim Beispiel in Bild 4, wo „Low-Angle Bands“ und „High-Angle Bands“ entstanden sind, ist der Kontaktdruck relativ hoch (> 3,2 GPa). Bei vielen mittelgroßen bis großen Lagern liegen die auftretenden Kontaktdrücke deutlich unter 3 GPa. Dies bedeutet, dass die Ermüdungsbelastung in verschiedenen Bereichen wirkt, wodurch weniger globale Schäden und mehr lokale Schäden rund um nichtmetallische Einschlüsse entstehen.
Bereits in den 1960er-Jahren wurde über WEC und dunkel anätzende Dekorationen im Zusammenhang mit Wälzlagerermüdung berichtet [12] (siehe auch SKF Arbeiten aus den 1980er-Jahren [13]). Nachträgliche Untersuchungen von mittelgroßen bis großen vorzeitig ausgefallenen Lagern (entweder aus hochbeschleunigten Lebensdauertests (HALT) oder aus standardisierten Lagerlebensdauerversuchen) haben das Auftreten ausgedehnter, unregelmäßiger WEC-Netzwerke als natürliches Nebenprodukt von Wälzlagerermüdung bestätigt (Bild 4 rechts).
WEC bei beschleunigter Wälzlagerermüdung (vorzeitige Ausbrüche)
Der Unterschied zwischen vorzeitigen Ausbrüchen (in der Industrie häufig als WEC-Ausfälle interpretiert) und klassischer Wälzlagerermüdung kann u. U. in der Dauer liegen, die für das Auftreten der verschiedenen Symptome bis hin zu Ausbrüchen benötigt wird (Bild 5). Hinzu kommt, dass vorzeitige Ausfälle im Gegensatz zu Lebensdauertests oder zur klassischen Wälzlagerermüdung oft einhergehen mit einer Rissbildung an mehreren Stellen bzw. in mehreren Bereichen, wie aus der Lagerausfallanalyse hervorgeht.
Die Gründe für die Rissbildung bei Wälzlagerstählen können sehr unterschiedlich sein. Bei hohen Belastungen und/oder bei verringerter Festigkeit verursacht durch Umwelteinflüsse beschleunigt sich die Rissentstehung und ausbreitung (Bild 6).
Die auf die Lager einwirkenden Belastungen können unerwartet hoch sein. Hier einige Beispiele für solche Situationen:
- Kurze, hohe Belastungen können durch unvorhergesehene Dynamik oder Temperatureffekte hervorgerufen werden, die zu hohen Vorspannungen, bedingt durch strukturelle Verformungen, Kantenspannungen usw. führen.
- Strukturbelastungen im Material des Lagers, bedingt z. B. durch Formabweichungen, Schiefstellungen oder sonstige Faktoren, erhöhen die Spannung im Material [14].
- Erhöhte Belastungen im Bereich der Laufbahn können auch durch ungünstige tribologische Bedingungen, z. B. schlechte Schmierbedingungen und/oder starken Schlupf, in Kombination mit bestimmten Schmierstoffen verursacht werden [15].
Die Materialfestigkeit eines Lagers kann durch Umweltfaktoren beeinträchtigt werden, die im Verdacht stehen, Wasserstoff zu bilden [16], wie beispielsweise
- Kontaminierung des Schmierstoffs mit Wasser
- Korrosion [17] und
- elektrische Streuströme.
In solchen Fällen können bereits mittlere Belastungen zum vorzeitigen Ausfall führen.
Die festgestellten Schadenstreiber für eine beschleunigte Ermüdung, die sowohl auf höhere Belastungen als auch auf eine geringere Materialfestigkeit zurückzuführen ist, wurden durch spezielle Lagertests bei SKF verifiziert.
Sobald auch nur ansatzweise Risse entstehen (manchmal einhergehend mit dem Auftreten von lokalen dunkel anätzenden Zonen (DER)) führt ein Aneinanderreiben der Rissoberflächen [18]–[22] zum Materialtransfer von einer Seite des Risses zur anderen. Dadurch entsteht eine Rissverzweigung, auf deren Flanken sich weiß anätzende Bereiche anhäufen.
Die Bildung von weiß anätzenden Bereichen (WEA) ist auch vom Rissverlauf unter der Oberfläche abhängig, der sich auf die einwirkenden inneren Kräfte und Verformungen zurückführen lässt. Daher sind WEA häufiger in horizontal (parallel zur Laufbahn) verlaufenden Rissen zu finden. Vertikal verlaufende Teile des Risses weisen dagegen meist weniger WEA auf (Bild 7). Des Weiteren ist die Bildung von WEA abhängig vom Zwischenraum zwischen den Rissflächen, der Anzahl der Belastungszyklen sowie dem inneren Spannungszustand im Werkstoff.
Beispiele für die Bildung von WEC aufgrund höherer Belastung
Die Bilder 8, 9 und 10 zeigen zwei Beispiele für die Bildung spannungsbedingter WEC. Die in den Bildern 8 und 9 dargestellten Ergebnisse beziehen sich auf einen Lagerprüfstand, der so konzipiert wurde, dass durch Welligkeiten strukturelle Spannungen oder strukturelle Verformungen künstlich in den Lagersitz eingebracht werden. Dadurch entstehen lokale Zugspannungen im Lagerinnenring. Bei der Prüfung wird ein Zylinderrollenlager mit seinem Innenring (Bohrungsdurchmesser 220 mm) mit normaler Passung auf einer Hülse mit fünf Wellen montiert, die wiederum auf der Prüfstandswelle mit Übermaß befestigt ist. Eine solche wellenförmige Hülse, die durch Hartdrehen hergestellt wird, wird in der Nähe der Laufbahnoberfläche des Innenrings fünf Zonen mit einer Zugspannung von etwa 205 MPa induzieren. Beim Prüflager handelt es sich um ein modifiziertes zweireihiges Zylinderrollenlager, das im mittleren Teil des Innenrings mit einer Reihe von acht (statt zwei Reihen mit 24) Rollen bestückt ist, damit der Prüfstand die erforderliche Kontaktspannung aufbauen kann (Bild 8). Der Lagerwerkstoff ist Wälzlagerstahl 100Cr6 (SAE 52100). Das Lagergefüge besteht aus angelassenem Martensit mit Rest-Austenit bis zu 7 Prozent (Volumen) und einer Härte von 62 HRC.
Die Lager wurden bei einem maximalen Hertz‘schen Kontaktdruck von 1,8 GPa und einem Kappa-Wert von etwa 2 bis zum Ausfall getestet.
Nach 1.150 Stunden (dies entspricht 6,35×108 Belastungszyklen) ist ein Lager, welches auf der Hülse mit fünf Wellen montiert war, mit einem sichtbaren Axialriss auf dem Innenring ausgefallen. Das zweite Lager ist nach 1.570 Stunden (dies entspricht 8,67×108 Belastungszyklen) mit zwei sichtbaren Axialrissen ausgefallen. Die Lage der Axialrisse im Innenring korreliert mit den Welligkeitsmaxima der Hülse. Das heißt, die Risse entstanden aufgrund lokaler Zugspannungen verursacht durch die welligkeitsbedingte strukturelle Verformung des Innenrings.
Dabei ist anzumerken, dass vier der gleichen Lager zuvor unter den gleichen Bedingungen mit einer Standard-Wellenpassung (ohne künstlich eingeführte Welligkeit) geprüft wurden. Keines dieser Lager versagte bis zur Einstellung der Prüfung nach etwa 2.200 Stunden (dies entspricht 1,21×109 Belastungszyklen), und bei der Nachanalyse wurden weder Oberflächenrisse noch weiß anätzende Risse unter der Oberfläche festgestellt.
Die Nachanalyse umfasst zerstörungsfreie Prüfungen (NDT) mittels Ultraschall (UST) und Farbeindringmittel, die Messung der Ringrundheit, die fraktographische Analyse und die metallographische Untersuchung unter dem Mikroskop.
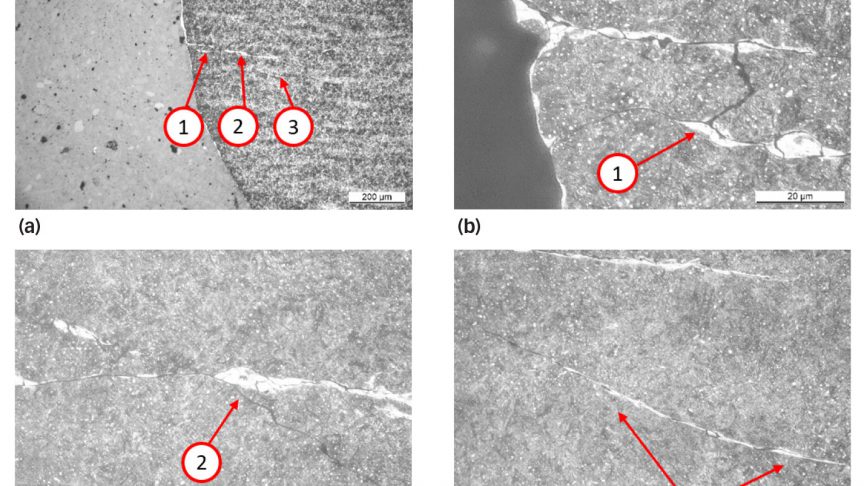
An der Probe wurde ein Parallelschnitt an einem geöffneten Riss, wie in Bild 9 gezeigt, durchgeführt. Es ist zu erkennen, dass nach dem Ätzen ein Teil des Hauptrisses mittels optischer Mikroskopie weiß erscheint, und dass sich der Riss in einer Tiefe von ca. 500 µm unter der Oberfläche verzweigt hat. Bei den verzweigten Rissen handelt es sich ebenfalls um WEC, die sich parallel zur Laufbahn etwa 400 µm vom Hauptriss entfernt ausgebreitet haben. Eine Vergrößerung der verzweigten Risse (Bilder 9 b), c) und d)) unterstützt die These, dass Risse sich miteinander verbinden und vernetzte WEC unter der Oberfläche bilden. An zwei weiteren Umfangspositionen des Innenrings, im Bereich der durch die Welligkeitshülse verursachten maximalen Zugspannungen, wurden Parallelschnitte vorgenommen. Obwohl auf der jeweiligen Innenringlaufbahn keine Oberflächenrisse festgestellt wurden, fanden sich mehrere WEC unterhalb der Oberfläche. Näheres dazu in Referenz [14].
Die in Bild 10 dargestellten Ergebnisse beziehen sich auf einen Test mit Pendelrollenlagern 23024, die kurzzeitig hohen Belastungen ausgesetzt wurden.
Bei kurzzeitig hoher Belastung wird das Lager bei guten Schmierbedingungen (Kappa-Wert von etwa 3,5) ca. 15 Minuten lang einem Kontaktdruck über 3 GPa ausgesetzt.
Das Lager, das zuvor einer kurzzeitig hohen Belastung ausgesetzt war, wird anschließend in einen Radialprüfstand eingebaut. Hier werden ein moderater Kontaktdruck von etwa 1,7 GPa und ein Kappa-Wert von etwa 2 aufgebracht. Unter diesen Bedingungen liefen die Lager entweder ca. 3,3×107 Lastzyklen (am Außenring) oder sind vorher ausgefallen. Bild 10 zeigt einen Umfangsschnitt und die Nitalätzung eines Außenrings. Das betreffende Lager ist nach 1,9×107 Zyklen aufgrund eines Ausbruchs im belasteten Bereich des Außenrings ausgefallen.
Beispiele für die Entstehung von WEC aufgrund geringerer Materialfestigkeit
Ein Beispiel für unter der Oberfläche verlaufende WEC in einem Lager unter Wasserstoffeinfluss wurde bereits in Bild 7 gezeigt. In Referenz [22] ist eine detaillierte Nachanalyse von wasserstoffbelasteten und wasserstofffreien Schräg- und Rillenkugellagern zu finden.
Beispiele für die Entstehung von WEC unter dem Einfluss von Mischreibung und Schmierstoffen
WEC wurden in ausgefallenen Axial-Zylinderrollenlagern 81212 bei Versuchen zur Beurteilung von Schmierölen auf FE8-Prüfständen festgestellt [23]. Die Prüfbedingungen, eine Kombination aus Mischreibung und hohem kinematischen Schlupf (nicht repräsentativ für Radialrollenlager), zeigen bisher keine eindeutigen Ergebnisse. Bisher kann noch keine abschließende Aussage getroffen werden, ob WEC in FE8-Tests eher eine Folge von einer unter der Oberfläche beginnenden Ermüdung (bei der auch der Schmierstoff eine wichtige Rolle spielt) oder das Ergebnis von Wasserstoffeintritt oder einer Kombination aus beidem sind.
Es wurden Lagertests mit Stahl/Stahl-Axial-Zylinderrollenlagern 81212 durchgeführt. Der Lagerwerkstoff ist ein Standardlagerstahl nach SAE 52100, martensitisch gehärtet, mit einem Rest-Austenitgehalt von unter 3 Prozent und einer Härte von rund 60 HRC. Diese Lager wurden bei mittleren Belastungen (max. Kontaktdruck etwa 1,9 GPa) und unter unzureichenden Schmierbedingungen (Kappa-Wert etwa 0,3) geprüft.
Es wurden verschiedene Schmieröle und Schmierölmischungen getestet. Ein typisches Ausfallerscheinungsbild ist in Bild 11 dargestellt.
Auch wenn dies hier nicht im Detail dargestellt ist, sind bei allen durchgeführten Tests meistens die Rollen und selten die Scheiben ausgefallen. Die Tests wurden entweder bis zum Ausfall (Ausbrüche) durchgeführt oder eingestellt. Bei Lagern, die durch Ausbrüche ausfielen und bei denen WEC festgestellt wurden, wird davon ausgegangen, dass sich bereits vor den Ausbrüchen weiß anätzende dekorierte Risse unter der Oberfläche gebildet hatten. Dies ist darauf zurückzuführen, dass manchmal auch bei Bauteilen ohne Ausbrüche Risse unter der Oberfläche festgestellt werden. Weitere Ausführungen dazu in Referenz [15].
Diskussion
Die obigen Erkenntnisse erklären, warum WEC in allen Industriezweigen, allen Lagertypen und bei allen Wärmebehandlungsarten (durchgehärtete sowie einsatzgehärtete Werkstoffe) vorkommen [1], da WEC am Ende der Versagenskette auftreten und eine natürliche Folge von Rissnetzwerken in vorzeitig ausgefallenen Lagern sind.
Der Schlüssel zur Bestimmung der Hauptursachen vorzeitiger Lagerausfälle liegt nicht nur in der Untersuchung von WEC, sondern vielmehr darin, die jeweiligen Schwächungseffekte (im Zusammenhang mit höherer Belastung oder geringerer Materialfestigkeit), die zu einer beschleunigten Ermüdung führen, festzustellen.
Im Allgemeinen ist der Ausfall eines jeden mechanischen Bauteils auf den Bruch des schwächsten Glieds innerhalb einer Kette zurückzuführen. Dies ist dann der Fall, wenn die lokale Belastung die lokale Festigkeit übersteigt. Ein vorzeitiger Ausfall ist die Folge einer deutlichen Schwächung des schwächsten Glieds. Die Zuverlässigkeit von Wälzlagern, die in den verschiedensten Anwendungen eingesetzt werden, folgt dem Prinzip des schwächsten Glieds. Schwachstellen gibt es immer im Werkstoff oder auf der Wälzkontaktfläche. Ein Lager versagt, wenn das schwächste Glied der Kette gebrochen ist. Bei schlechter Schmierung oder rauer Oberfläche (z. B. nach Partikeleindrückungen) könnte das schwächste Glied an der Oberfläche liegen, und das Lager fällt aufgrund von Oberflächenschäden wie Oberflächenzerrüttung oder Verschleiß aus. Bei guten Schmierbedingungen könnte das schwächste Glied unter der Oberfläche liegen, da Materialfehler wie Einschlüsse und hohe Schubspannungen durch Hertz‘sche Pressung vorliegen und der Lagerausfall auf eine Rissbildung und -ausbreitung aufgrund bereits vorhandener Materialfehler zurückzuführen ist. Bei Wälzlagern kann die Festigkeit des schwächsten Glieds auf eine Belastungs- oder Spannungsgrenze bezogen werden, die Ermüdungsgrenze genannt wird. Ein Lager fällt aus, wenn die Ermüdungsgrenze überschritten wird. Ein vorzeitiger Lagerausfall tritt ein, wenn die Ermüdungsgrenze deutlich herabgesetzt ist, d. h. wenn die Festigkeit des schwächsten Glieds erheblich reduziert ist. Es ist die Schwächung, die infolge höherer Belastung oder geringerer Materialfestigkeit zu frühzeitiger Rissbildung und beschleunigter Rissausbreitung und damit zu vorzeitigem Lagerausfall führt, nicht aber die WEC. Wenn keine Schwächung vorliegt, kann ein Lager infolge „normaler“ Wälzlagerermüdung durch einen einzelnen Ausbruch versagen, wobei nur wenige oder gar keine WEC vorhanden sind, da sich die Risse am Ende der Lebensdauer des Werkstoffs schnell ausbreiten [7]. Somit bleibt keine Zeit für die Materialumwandlung innerhalb des Risssystems. Bei zunehmender Schwächung kann das Lager aufgrund ausgedehnter WEC vorzeitig ausfallen, da der Werkstoff in initiierten Risssystemen Zeit hat, sich lokal von DEA in WEA umzuwandeln. Bei zunehmendem Schweregrad können Axialrisse mit reduzierter WEA-Dekoration oder sogar Brüche ohne WEA-Dekoration auftreten, da sich Risse zu schnell ausbreiten [14].
Empfehlungen
Jeder vorzeitige Lagerausfall ist ein Fall für sich. Anhand von Bild 6 lässt sich feststellen, dass die Ursachen für vorzeitige Ausbrüche sehr unterschiedlich sein können. Es gibt keine allgemeingültige Ursache, und jeder Ausfall muss individuell unter den jeweiligen Betriebsbedingungen analysiert werden.
Aufgrund der Einteilung der Schadenstreiber in „Höhere Spannungen/Belastungen“ und „Geringere Materialfestigkeit“ können, wie in Tabelle 1 dargestellt, sehr allgemeine Empfehlungen formuliert werden. Die Tabelle unterscheidet zwischen Empfehlungen für die Anwendung selbst (Lagersystem, Entwurfsprozess) und Maßnahmen zur weiteren Verbesserung der Robustheit der Lager. Welche Möglichkeit am besten geeignet ist, um vorzeitige Ausfälle zu verhindern, hängt von den jeweiligen anwendungsspezifischen Gegebenheiten ab. Wenn weitere Informationen benötigt werden, sind die Experten des technischen SKF Beratungsservice die richtigen Ansprechpartner.
Literatur
[1] K. Stadler, A. Stubenrauch, Vorzeitige Lagerausfälle in Windgetrieben und „White Etching Cracks“ (WEC), SKF Evolution #2, 2013, http://evolution.skf.com/de/vorzeitige-lagerausfalle-in-windgetrieben-und-white-etching-cracks-wec/
[2] K. Tamada, H. Tanaka, Occurrence of brittle flaking on bearings used for auto-motive electrical instruments and auxiliary devices, Wear 199 (1996) 245–252.
[3] N. Kino, K. Otani, The influence of hydrogen on rolling contact fatigue life and its improvement, JSME Rev. 24 (2003) 289–294.
[4] B. Carr, More bearing failures for cruise ship pod drives, The eBearing News, http://www.ebearing.com/news2006/052201.htm, May 2006.
[5] M.H. Evans, An updated review: white etching cracks (WECs) and axial cracks in wind turbine gearbox bearings, Mat. Sci. Tech., DOI: 10.1080 / 02670836.2015.1133022, 2016, 1-37.
[6] K. Stadler, J. Lai, R.H. Vegter, A review: the dilemma with premature white etching crack (WEC) bearing failure, J. ASTM Int. (2015), STP1580.
[7] A. Voskamp, “Microstructural Changes during Rolling Contact Fatigue,” Ph.D. thesis, Delft University of Technology, 1996.
[8] R.H. Vegter and J.T. Slycke, ‘Metal Physics and Rolling Contact Fatigue Testing’, presented at the Ninth International Symposium on Bearing Steel Technol-ogies: Advances in Rolling Contact Fatigue Strength Testing and Related Substitute Technologies, November 17-18, 2011, Tampa, FL, USA, published in ASTM STP 1548 (editor J.M. Beswick), ASTM International 2012.
[9] J.-H. Kang and P.E.J. Rivera-Diaz-del-Castillo, ‘Carbide dissolution in bearing steel’, Computational Materials Science, 67 (2013) 364-372.
[10] J.-H. Kang, B. Hosseinkhani, R.H. Vegter and P.E.J. Rivera-Diaz-del-Castillo, ‘Modelling dislocation assisted tempering during rolling contact fatigue of bearing steels’, International Journal of Fatigue, Volume 75, June 2015, Pages 115–125.
[11] T. Lund, Sub-Surface initiated rolling contact fatigue-influence of non-metallic inclusions, processing history, and operating conditions. J ASTM Int 2010;7(5):81–96.
[12] D. Scott, B. Loy and G.H. Mills, “Metallurgical Aspects of Rolling Contact Fatigue, Proceedings of the Institution of Mechanical Engineers,” IMechE Arch., Vol. 181, No. 15, 1966, pp. 94–103.
[13] P.C. Becker, Microstructural changes around non-metallic inclusions caused by rolling contact fatigue of ball-bearing steels, Metals Technology, Fatigue of ball-bearing steel, 234-243, 1981.
[14] J. Lai, K. Stadler, Investigation on the mechanisms of white etching crack (WEC) formation in rolling contact fatigue and identification of a root cause for bearing premature failure, http://dx.doi.org/ 10.1016/j.wear.2016.08.001, Wear, 2016.
[15] K. Stadler, R.H. Vegter, M. Ersson, D. Vaes, Causes for premature failures and the role of white etching cracks, Proceedings of the “Tribologie-Fachtagung 2016”, Gesellschaft für Tribologie (GfT), 2016.
[16] R.H. Vegter, J.T. Slycke, The role of hydrogen on rolling contact fatigue response of rolling element bearings. J ASTM Int 2009;7(2):1–12.
[17] I. Strandell, C. Faiers, T. Lund, Corrosion – one root cause for premature failure, in: Proceedings of the 37th Leeds-Lyon Symposium on Tribology, Leeds Trinity University, Leeds, UK, 7–10 September, 2010, Elsevier, New York, 2012.
[18] W. Solano-Alvarez, H.K.D.H. Bhadeshia, White-etching matter in bearing steels. Part I: controlled cracking of 52100 steel. Metall Mater Trans A 2014;45A:4906–15.
[19] W. Solano-Alvarez, H.K.D.H. Bhadeshia, White-etching matter in bearing steels. Part II: distinguishing cause and effect in bearing steel failure. Metall Mater Trans A 2014;45A:4916–31.
[20] Y. Kadin, M.Y. Sherif, Energy dissipation at rubbing crack faces in rolling contact fatigue as the mechanism of white etching area formation, International Journal of Fatigue 96, 114-126, 2017, http://dx.doi.org/ 10.1016/j.ijfatigue.2016.11.006.
[21] B. Gould, A. Greco, K. Stadler, X. Xiao, An analysis of premature cracking associated with microstructural alterations in an AISI 52100 failed wind turbine bearing using X-ray tomography, Material and Design 117, 2017, http://dx.doi.org/10.1016/j.matdes.2016.12.089.
[22] S.W. Ooi, A. Gola, R.H. Vegter, P. Yan, K. Stadler, Evolution of white-etching cracks and associated microstructural alterations during bearing tests, Material Science and Technology, http://dx.doi.org/10.1080/02670836.2017.1310431, 2017.
[23] H. Surborg, Einfluss von Grundölen und Additiven auf die Bildung von WEC in Wälz-lagern, Dissertation, Otto-von-Guericke-Universität Magdeburg, 2014.