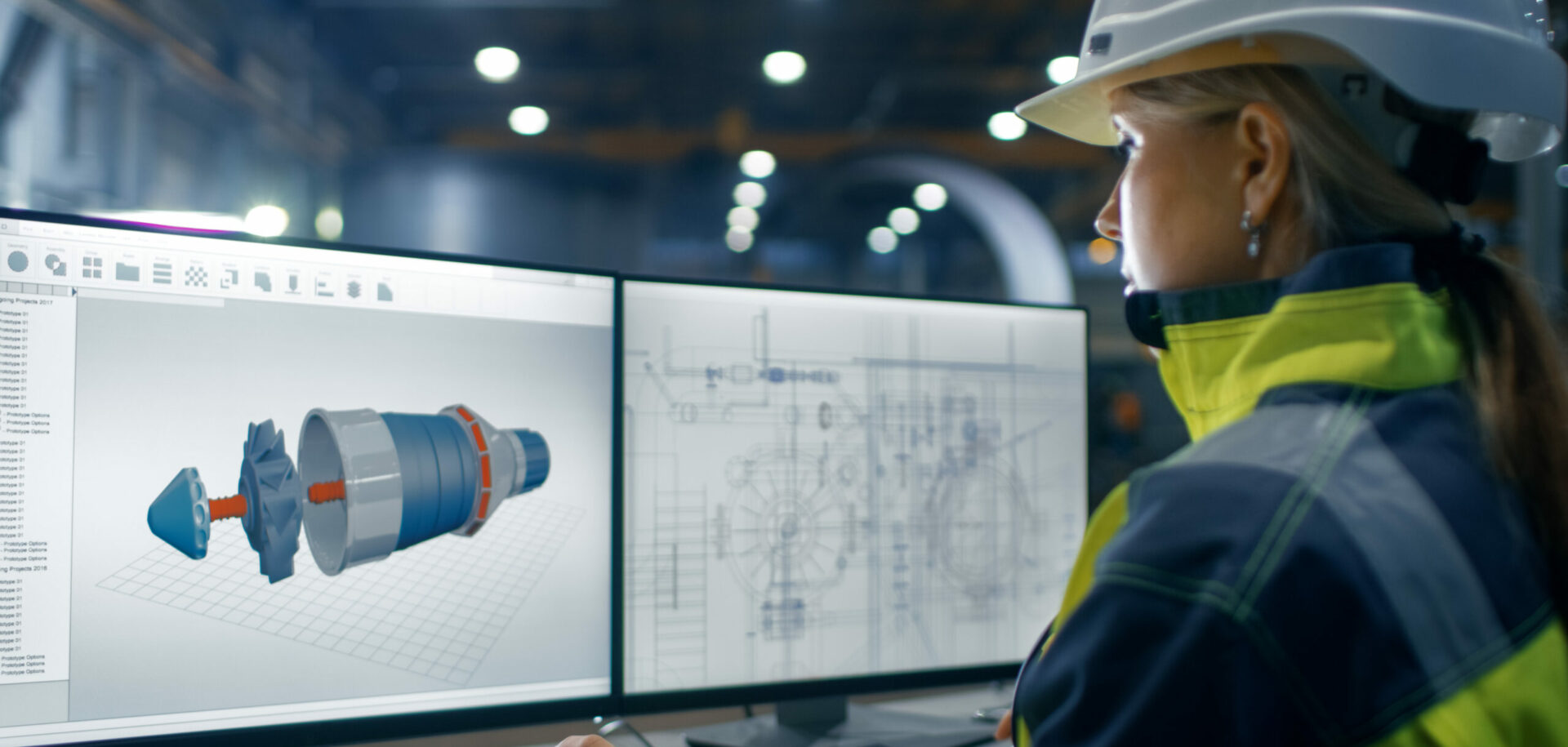
Engineering polymers for designer cages
Steel cages are traditionally made from sheet metal by stamping and forming.
Polymer materials are increasingly replacing metal in bearing cage design. The factors behind this growth
are linked to improvements in engineering polymer’s mechanical performance coupled with the advantages
of flexible production.Injection moulding techniques for cage production provide the opportunity to create innovative designs that offer improvements with respect to roller guidance, damping bearing noise levels and bearing running temperature.
Metal cages still dominate in areas where high temperature and aggressive media make the application of engineering plastics impossible. For metal cage geometry, however, the design always has to take into account the bearing performance and the cage manufacturing process so that compromises may have to be made.
Steel cages are traditionally made from sheet metal by stamping and forming.
The contact geometry between the cage and the rollers is optimised to provide the best support to the rollers, bearing in mind the limitations of the production method. Metal cage pockets appear to have sharp edges facing the rollers. Under dynamic conditions, the cage and the rollers are exposed to high impact forces almost without any damping capabilities in between. Under such conditions, the lubrication distribution cannot be considered optimum for the desired bearing performance. In the worst case, the steel cage bar can act as a scraper for the lubricant on the roller surface.
No restrictions
Opting for a polymer cage fabricated by injection moulding techniques allows the product design engineer to concentrate on the cage design without being faced with restrictions imposed by the manufacturing process. The cage pocket geometry of polymer cages can be optimised for rolling element guidance. It enables a hydrodynamic pressure generation between the cage bars and the rollers. In addition to allowing good polymer material damping and elasticity properties, hydrodynamic lubricant pressure in the cage roller contact also contributes to a reduction in bearing noise.
Improved control of lubricant distribution is directly measurable through lower bearing running temperature, reduced roller and raceway wear and fatigue, thus increasing overall bearing service life.
When compared with metal designs, polymer cages offer the advantage in operation of lower noise, lower friction, longer maintenance intervals and optimised design coupled with improved safety through avoidance of bearing seizure.
Polymer range
There are at least 25 chemical companies worldwide that produce in excess of 50 different base polymers. In addition, there are specialist companies that modify the characteristics of these polymers through a combination of additives.
Polymer structures are normally characterised as either amorphous or semi-crystalline, with further subdivision according to their particular application. Normally polymers are either classed as standard, engineering or high performance.
Standard polymers normally cover the application range for ambient temperatures and low loads. This class of materials, encompassing materials such as polyvinyl chloride, polyethylene and polypropylene, is unsuitable for bearing cage applications and is typically used for packaging, low-temperature domestic applications, medical devices, containers and toys.
For those applications where higher temperatures (up to 100 °C) and higher load-carrying capacities are required, engineering polymers are employed. Here suitable materials include polyamide, polycarbonate and polybutyleneteraphthalate. They are found in structural components, housings, bushings and car components, for example.
High performance grades are special polymers with increased thermal stability above 100 °C and with mechanical properties that can match or exceed those of engineering polymers. Typical uses include electrical connectors, gear wheels, switches, valves, journal bearings and lamp housings.
Cost is also a factor in the use of a particular material. Low-grade plastics sell for around US$1/kg while more sophisticated products cost around US$60/kg.
Material selection
For bearing cage applications, five properties can be used to define the suitability of a particular polymer. These are:
- High temperature limit, THlim
This is measured by material stiffness at maximum continuous operating temperature - Ductility, eB
Maximum deformation of the cage and cage pocket lips during cage mounting - Impact strength, acU
Shock loading during bearing operation - Ductility of aged polymers, eBa
This indicates chemical compatibility with lubricants - Strain amplitude for dynamic bending, ad
A factor that indicates polymer material fatigue
Unlike steel, the properties of polymer materials strongly depend on the actual operating temperature, exposure time, stress level and environment media. For example, when exposed to temperatures above 120 °C, the elasticity modulus of polyamide 6,6 having 25% glass fibre reinforcement decays to less than 50%
of its original value at room temperature.
For this reason, standard polymer materials could not be used in bearing applications, owing to their lack of stiffness at higher temperatures.
Polymer ageing, resulting from chemical interaction with lubricants or other environmental media, is characterised by the change of maximum polymer strain and/or stress. In the worst case, both are reduced.
An additional parameter to consider is environmental stress cracking resistance, or ESCR. Nearly all amorphous polymers are subject to this, thus ruling out their use in bearing cages. Semi-crystalline engineering and higher performance polymers are those targeted for cage applications.
Setting standards
SKF has identified the polymers within these groups that offer the best performance in bearing cage applications. In particular, polyamide, from the engineering class of semi-crystalline polymers, was found to have the best performance with regard to static and dynamic mechanical properties as well as chemical compatibility with SKF lubricants.
The most widely used polymer for bearing cages is PA66-GF25, representing 95% of all polymer cage production. Variants such as PA46 and ST-PA are used for applications where slightly better chemical resistance or impact strength is required, such as in gearboxes and railway bearings. Where ageing resistance at higher temperatures is required, PEEK-GF15 is normally chosen.
Work has been carried out to identify the high temperature limits of the SKF-preferred polymers. Chemical compatibility with different oils and greases was used to identify the maximum continuous operating temperature. These values provide a guide to the selection of polymers of bearing cage applications.
Polymer ageing, however, is always a function of the actual temperature and the time duration of exposure. For example, for the polymer, PA66-GF25, the life expectation using mild lubricants at a temperature of 240 °C is 10 hours maximum. When the actual operating temperature is below 100 °C, the life is more than 1,000 times higher. For aggressive lubricants, such as gearbox oils, the cage life in the worst case is a factor of 10 lower than for mild lubricants.
Challenging future
Current developments in technical applications place heavy demands on bearing cage performance. In many application areas, the continuous operating temperature can be up to
150 °C. At present aggressive lubrication media make the PA66 cages undesirable under these conditions. So for applications such as car and industrial gearboxes, trucks and certain fluid machines, metal bearing cages remain the best option.
There is a polymer, PEEK, that can provide performance levels that match metal cages at high temperatures, though its prohibitive costs currently rule it out for practical applications. Chemical manufacturers are now developing a range of polymer materials that could offer PEEK performance at more competitive prices to match PA66 price levels, thus bridging the gap between performance and cost.
Vedran Tadic,
SKF Engineering & Research Centre B.V. (ERC),
Nieuwegein, the Netherlands