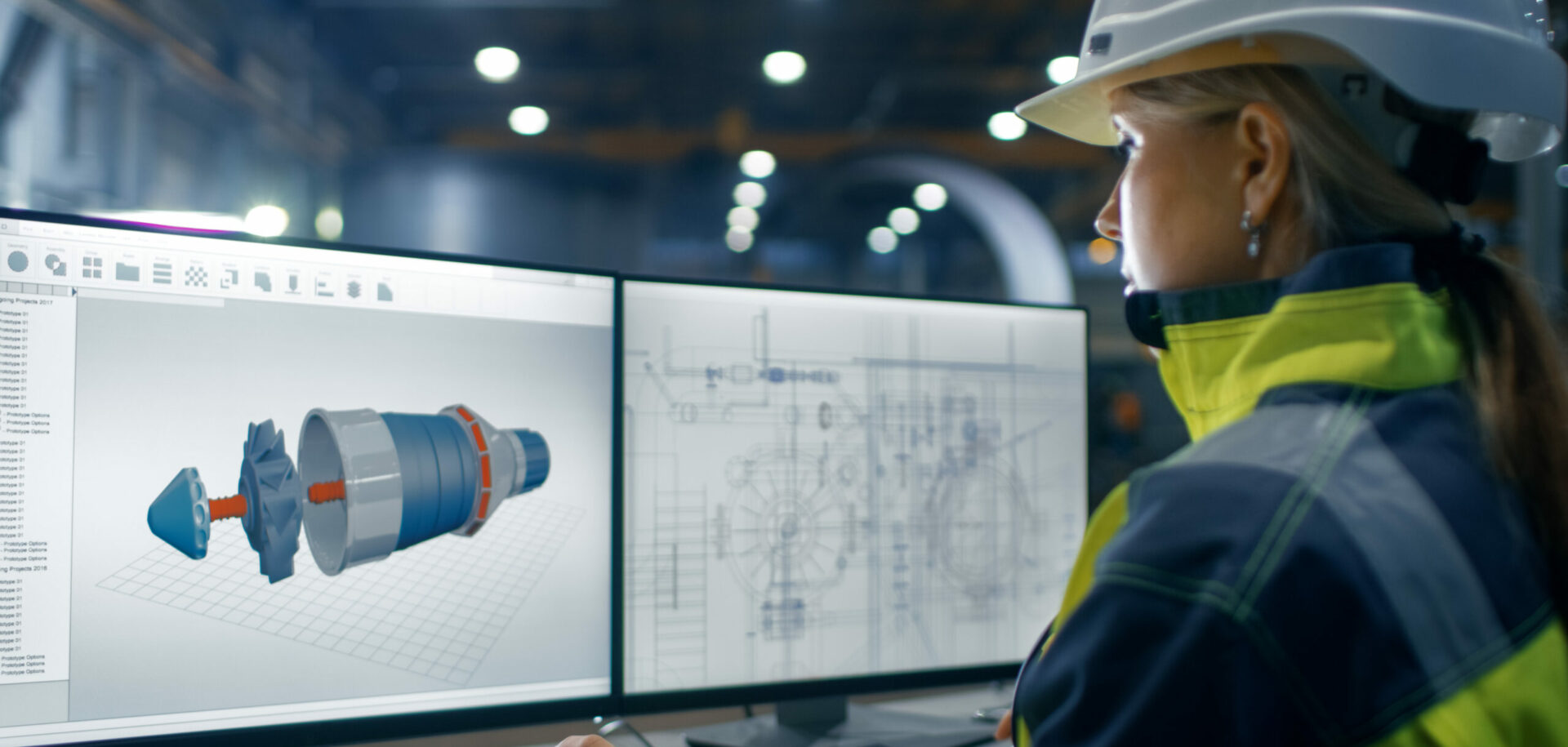
Des systèmes d’étanchéité optimisés grâce à des simulations numériques de pointe
De nos jours, les simulations numériques constituent un outil clé du développement des nouveaux produits et de l’amélioration des produits existants. Afin d’améliorer la conception globale de ses produits et l’assistance offerte aux clients, SKF équipe ses ingénieurs produits d’un outil d’analyse par Eléments Finis développé au sein du Centre d’ingénierie et de recherche SKF basé aux Pays-Bas.
Résumé
Les ingénieurs produits SKF utilisent désormais un puissant outil d’analyse et de calcul pour concevoir et prédire le comportement des nouveaux modèles de joints. Grâce au SKF Seal Designer, les temps de développement des produits sont réduits et les ingénieurs sont mieux à même d’ajuster les performances des joints aux exigences de l’application.
Les simulations numériques jouent un rôle important à différentes étapes du cycle de vie pour un nombre croissant de produits. Des simulations virtuelles basées sur des analyses numériques approfondies réduisent les coûts tout au long des phases de conception et de prototypage en optimisant les prototypes soumis aux tests physiques.
Il existe sur le marché plusieurs outils de calcul qui ont fait leurs preuves en termes de fiabilité et qui offrent une vaste gamme d’applications dans différents domaines. Ces suites logicielles sont conçues pour un usage général et, par conséquent, adaptées pour l’étude de différents types de phénomènes. Toutefois, le maniement de ces outils ainsi que l’interprétation des résultats et leur exploitation pragmatique nécessitent un niveau élevé de compétences.
SKF jouit d’une longue expérience des simulations numériques, non seulement dans l’utilisation de ces solutions de simulations commerciales mais aussi en ce qui concerne le développement en interne d’outils de calcul. Les plateformes Orpheus et BEAST sont utilisées quotidiennement par les ingénieurs SKF pour assister les clients et répondre à leurs questions. Ces outils maison permettent à SKF de simuler des applications de roulements de multiples façons et selon différents niveaux de complexité. Ce type d’expérience et ces outils sont enrichis en continu avec de nouvelles fonctionnalités et plus de puissance pour répondre à la vision SKF de la simulation numérique, qui consiste à simuler tous les composants – roulements, arbres, joints, roues dentées et paliers – au sein d’un système complet (Fig. 1).
Joints et simulations numériques
La première étape de la simulation de systèmes complets consiste à simuler les joints individuellement (Fig. 2). Cette étape initiale qui cible un seul composant de façon détaillée permet à SKF de comprendre de manière encore plus approfondie le fonctionnement du joint une fois installé dans sa position définitive.
Les simulations numériques de joints portent sur plusieurs aspects mécaniques. Ces aspects sont décrits succinctement ci-après pour fournir un aperçu, d’une part de la complexité des simulations de joints et, d’autre part de la technologie développée par SKF pour doter les ingénieurs produits de logiciels puissants et fiables.
Simulations du caoutchouc : un matériau extrêmement non-linéaire
De nombreux calculs techniques effectués aujourd’hui sont basés sur la supposition que le matériau présente un comportement linéaire et élastique, autrement dit que la force et les déplacements dépendent de façon linéaire d’une constante appelée rigidité. Les matériaux caoutchoucs présentent généralement un comportement non linéaire. Il ne suffit pas de définir une constante pour établir le lien entre la force et les déplacements ou la contrainte et la déformation. Au lieu de cela, le caoutchouc requiert des modèles constitutifs plus complexes aptes à traiter la non-linéarité multiaxiale.
Des modèles hyper élastiques notamment sont souvent utilisés pour simuler le comportement des caoutchoucs. Ces modèles de matériaux sont élastiques mais, comme l’illustre la Fig. 3, en dehors d’une certaine plage d’étirement, la relation contrainte-déformation s’écarte nettement d’un comportement linéaire. De plus, la réponse du matériau dépend dans une grande mesure de l’orientation de la déformation.
Le caoutchouc est le matériau le plus communément employé pour les joints, car il leur permet de suivre les mouvements des surfaces d’appui avec lesquelles ils sont en contact, comme les arbres, les bielles ou les roulements. Dans le cadre de la simulation de joints, il est par conséquent nécessaire de disposer d’un moyen fiable de simuler des modèles de matériaux hyperélastiques pouvant subir des déformations importantes selon des orientations multiples.
Simulations du caoutchouc : un matériau presque incompressible
Le caoutchouc est en outre un matériau pratiquement incompressible, c’est-à-dire que la variation du volume d’un échantillon de caoutchouc comprimé ou étiré avant et après déformation est pratiquement nulle. Il s’agit d’un comportement particulier qui défie les méthodes numériques mises en œuvre au sein des logiciels de simulation traditionnels. L’incompressibilité du caoutchouc génère des instabilités numériques ; on parle généralement de « verrouillage volumétrique ». Pour surmonter cette difficulté, une mise en œuvre spéciale du schéma d’intégration a été élaborée dans le but d’obtenir des résultats corrects et stables [1].
La recherche dans la littérature d’une solution au verrouillage volumétrique a conduit à la méthode F bar [1], qui implique une modification des méthodes d’intégration traditionnelles présentées dans la littérature [2]. À cet égard, la collaboration avec le monde universitaire, en particulier avec l’université de Twente, aux Pays-Bas, a permis de démontrer l’exactitude et la précision des algorithmes mis en œuvre. Il a ainsi été possible d’atteindre une qualité de calcul comparable à celle du calcul de charge effectué par l’une des suites d’analyse par éléments finis disponibles sur le marché, comme ABAQUS, Marc ou ANSYS.
Simulation des joints : la mécanique des contacts
Les éléments d’étanchéité doivent être installés en position de fonctionnement avec un certain ajustement entre l’alésage et l’arbre. Il est par conséquent primordial de pouvoir simuler le contact entre les joints et les surfaces environnantes (comme les paliers, arbres, déflecteurs ou roulements) (Fig. 4 et 5).
Pour une simulation correcte de l’ajustement entre les joints et les pièces adjacentes de l’application, la mécanique des contacts a fait partie des exigences clés prises en compte dans le développement de l’outil logiciel. Le contact peut être traité à travers des codes numériques de différentes manières. Compte tenu de la nature du matériau habituellement utilisé en contact (généralement du caoutchouc en contact avec l’acier), aucune co-pénétration entre les corps en contact n’est prise en compte. Cette hypothèse a conduit à l’adoption de la méthode des multiplicateurs de Lagrange (la déformation des joints est forcée pour être mathématiquement égale aux contraintes exercées par les surfaces d’appui environnantes) au lieu de la méthode des pénalités (la déformation du joint est forcée au moyen de fonctions de pénalités qui sont activées dès qu’une contrainte n’est pas respectée).
Simulations d’un système d’étanchéité : une solution de calcul par éléments finis
La meilleure façon de combiner tous les éléments ci-dessus dans des simulations numériques est de recourir à la puissance de la méthode par éléments finis (FEM). Concrètement, cette méthode permet de gérer facilement la combinaison des différents aspects mentionnés : modèles de matériaux hyperélastiques, déformations importantes, mécanique des contacts à travers la méthode des multiplicateurs de Lagrange et mise en œuvre spéciale visant à éviter le problème de verrouillage numérique dû à l’incompressibilité du matériau.
SKF Seal Designer
Avec l’aide de son Centre d’ingénierie et de recherche, SKF a doté ses ingénieurs produits d’un outil de calcul de pointe basé sur la plateforme Orpheus. L’outil en question a été baptisé SKF Seal Designer.
Les principales fonctionnalités du logiciel englobent les prédictions à la fois de fabrication (des outils de moulage à la géométrie finie) et de performances (installation sur un arbre et/ou dans un logement).
Des fonctionnalités de simulation de fabrication sont à la disposition des ingénieurs produits SKF pour améliorer l’étude de conception concernant la forme finale du joint. L’outil est également utilisé pour améliorer la géométrie des moules qui constitue l’un des aspects les plus importants du processus global de conception en raison de la part des coûts qu’elle représente, mais aussi parce que la géométrie des moules peut être réexploitée pour d’autres conceptions.
Des calculs du joint monté sur un arbre constituent une fonctionnalité supplémentaire. Lorsqu’un joint est installé, il exerce une force sur la surface d’appui appelée précontrainte (Fig. 6). La précontrainte fait partie des paramètres les plus importants d’un joint pour les conditions de fonctionnement statiques comme dynamiques. Cette précontrainte assure l’étanchéité souhaitée et est également responsable du frottement du joint qui s’opère sous la lèvre. Un ressort de retenue peut, en outre, être utilisé pour maintenir une précontrainte suffisante pour garantir l’étanchéité malgré le vieillissement du matériau du joint (Fig. 7). C’est la raison pour laquelle une prédiction exacte de la précontrainte dans différentes conditions de service permise par un outil de simulation est cruciale pour contribuer à réduire le nombre d’itérations de conception et, par conséquent, les délais de mise sur le marché de nouveaux produits (Fig. 8 et 9).
Conclusions
SKF Seal Designer met à la disposition des ingénieurs produits SKF toute la puissance des simulations par EF. Cet outil réduit les délais de mise sur le marché en permettant aux ingénieurs produits d’évaluer de façon virtuelle l’impact des paramètres du joint, du cahier des charges du client et des exigences de l’application sur les performances du joint.
Références
[1] Computational Methods for Plasticity: Theory and Applications de E.A. de Souza Neto, D. Peric et D.R.J. Owen (30 déc. 2008).
[2] The Finite Element Method (sixième édition) de O.C. Zienkiewicz et R.L. Taylor (20 sep. 2005).