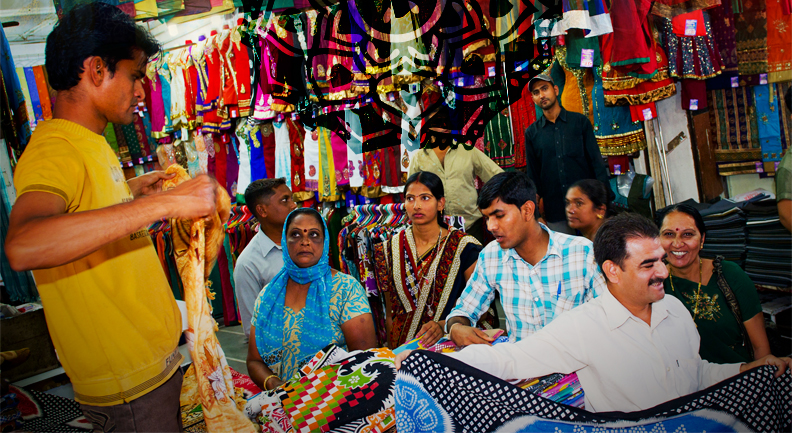
Tissu industriel
Dans l’État du Gujarat, en Inde, les producteurs de textiles cherchent à réduire les coûts et l’impact sur l’environnement en faisant appel aux technologies économes en énergie.
En bref
L’histoire du sari
Il y a plus de 80 façons de porter un sari. La polyvalence et la commodité du vêtement sud-asiatique explique facilement pourquoi il a survécu à la civilisation de la vallée de l’Indus (2800-1800 avant notre ère) jusqu’au 21e siècle. Son drapé très ample est parfaitement approprié pour le climat chaud et humide de nombreuses régions d’Inde. Et bien sûr, les saris sont magnifiques. Bien que les Indiennes, en particulier en ville, s’habillent souvent à l’occidentale, le sari est toujours le vêtement privilégié pour bon nombre. Bollywood a largement contribué à le faire connaître dans le monde entier, grâce aux actrices telles que Aishwarya Rai.
Liens apparentés
Contact commercial
Marcel Soltermann, Marcel.Soltermann@skf.com
Au marché de Badra à Ahmedabad, les rues étroites et tortueuses sont bordées de petites échoppes et d’étalages proposant toutes les étoffes possibles et imaginables. Les vendeurs rivalisent pour attirer l’attention des femmes et des jeunes filles vêtues de saris colorés aux motifs magnifiques. Les acheteuses montrent du doigt, choisissent et marchandent leurs futurs atours. Il n’y a pas de meilleur endroit pour faire l’expérience, tous sens confondus, du centre de l’industrie textile indienne.
Le Gujarat produit plus de coton que n’importe quel autre État indien et fabrique 30 % des tissus du pays. Avec ses six millions d’habitants, Ahmedabad est sa plus grande ville et, étant le centre de l’industrie textile industrielle de l’Inde depuis les années 1800, on la surnomme le « Manchester de l’Orient ».
Face à l’inquiétude grandissante relative au réchauffement climatique et aux coûts élevés de l’énergie en Inde, économiser l’énergie est une priorité pour les filatures. L’un des pionniers du développement de technologies économes en énergie est Indian Textile Engineers d’Ahmedabad, une entreprise qui fabrique les machines imprimant les motifs sur les étoffes pour saris et draps, par exemple. « Nos utilisateurs finaux nous demandent constamment de réduire la consommation d’énergie, car celle-ci renchérit leurs coûts », explique son directeur général Niki Thakore.
Dans les machines classiques d’impression sur textile, des vérins hydrauliques soulèvent et abaissent les écrans qui transfèrent le motif. La consommation élevée d’énergie n’est pas le seul inconvénient écologique de ces systèmes : 400 litres d’huile hydraulique sont nécessaires chaque année et par machine pour actionner les deux vérins installés sur chaque machine d’Indian Textile Engineers.
Il y a quelques années, la société a commencé à s’enquérir d’une solution de rechange. « J’ai eu l’idée de remplacer le système hydraulique par des vérins électromécaniques, fait valoir Niki Thakore. Et le premier fournisseur qui m’est venu à l’esprit est SKF. »
Les systèmes hydrauliques ont besoin d’une alimentation électrique constante, même lorsque les vérins sont à l’arrêt, tandis que les solutions électromécaniques ne consomment de l’énergie qu’en mouvement. La transmission de la puissance électromécanique ne nécessite pas d’huile, ce qui élimine sa consommation et les fuites dans les machines et sur le sol des filatures. Elle améliore également les conditions de travail des opérateurs grâce à la réduction du niveau sonore et des vibrations.
Ensemble, SKF et Indian Textile Engineers ont étudié plusieurs modèles de vérins. Après de nombreux essais, leur choix s’est porté sur le vérin électromécanique SKF CASM, qui peut supporter les lourdes charges et les vitesses élevées d’une machine d’impression sur textile tout en augmentant la productivité. Deux vérins électromécaniques ont été montés à l’essai sur une machine : la réduction de la consommation d’énergie estimée à 7 MWh par an (l’équivalent de 5,3 tonnes de CO2 par an sur la base d’un facteur d’émission du réseau électrique mondial de 0,749 kg CO2/kWh) est révélatrice.
L’étape suivante a consisté à tester la solution auprès de certains clients. Les économies d’énergie se sont élevées à environ 120 euros par mois et par machine. Avec environ 5 000 machines d’impression opérant dans le pays, Indian Textile Engineers entrevoit un énorme potentiel d’économies d’énergie et d’argent. En outre, une filature d’Ahmedabad a fait passer sa productivité de 600 à 850 m/h en adoptant les vérins électromécaniques SKF CASM.
L’installation réussie de 17 vérins dans les machines d’Indian Textile Engineers a suscité la commande de 300 autres vérins électromécaniques CASM SKF en 2012, lesquels seront installés dans les machines d’impression flambants neuves ainsi que dans les machines déjà en service dans diverses filatures.
Un produit SKF BeyondZero
Le vérin électromécanique SKF CASM est l’un des premiers produits validés pour le portefeuille SKF BeyondZero. Les solutions SKF BeyondZero se traduisent par d’importants gains sur le plan environnemental, lesquels aident les clients à améliorer leur propre performance en matière de protection de l’environnement. Le cahier des charges est extrêmement sévère, l’admission du produit passant par des audits sur mesure et la validation par un comité.
« Tout d’abord, il doit avoir une action tangible en faveur de l’environnement, explique Mats Berglund, chef de projet chez SKF Group Manufacturing Development. Et pas de compromis possible : si on améliore un aspect, entre la conception et le recyclage, du cycle de vie d’un produit, ce ne doit pas être au détriment d’un autre ; par exemple, il ne peut pas avoir un plus fort impact sur le plan de la fabrication. »