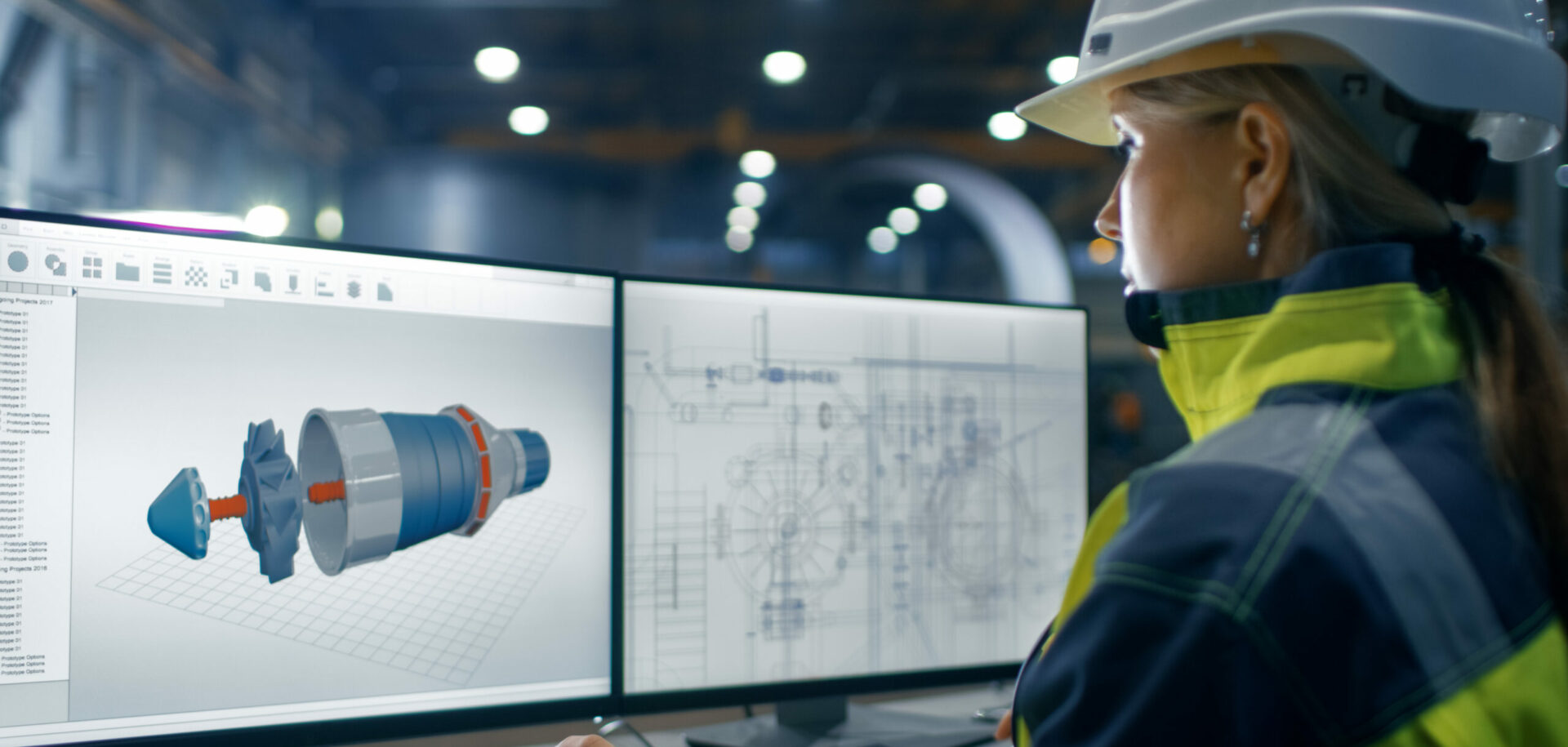
Global warehouse and distribution systems create effective logistics
Managing an efficient global warehouse and distribution system is a key part of SKF’s business activities. Over the past decade, the company has invested in sophisticated logistics systems to enable its products to reach customers worldwide in the most efficient way.
Industry is faced with rapidly changing logistics technology through the development of automated warehouse concepts linked to sophisticated and complex transportation management systems. Meanwhile, customers’ expectations about product delivery times and availability have changed such that they demand fast service – at low cost and with low errors. Manufacturers such as SKF have taken the opportunity to improve the quality of distribution and warehousing and to make savings through improved efficiencies offered by new logistics concepts.
Through a computer system called the Warehouse Administration Service System or WASS, SKF manages all operative tasks in the warehouses of its global distribution network. WASS has resulted in great improvements inproductivity, thanks to more efficient workflows and high accessibility of the system. Since the system’s introduction, productivity has improved more than 50 percent. SKF works with completely paperless processes and work-saving solutions based on sound logistics principles.
In simple terms, WASS is a computer system that supports the six main functions required in warehouse administration:
- Goods inwards;
- Goods replenishment;
- Picking;
- Packing;
- Loading; and
- Inventory control.
The WASS concept was developed by SKF in collaboration with MA Systems, a Swedish company with more than 25 years of experience in warehouse automation systems and installations in more than 20 countries worldwide. In essence, WASS supports all the processes that are used in a modern warehouse operation, working on information in real time. Working as simply and logically as possible, it controls the flow of products in and out of the warehouse. WASS also acts as a link between other administrative systems such as customer order-handling, transportation management and warehouse operations.
Flexibility is important, as WASS needs to be able to work with a range of warehouse technologies, from traditional manual movement of goods using driver-controlled forklift trucks to fully automated storage and retrieval systems (ASRS) under direct computer control. The first WASS installation was made in 1995 at the company’s European Distribution Centre (EDC) at Tongeren in Belgium. This is SKF’s largest product-storage facility, covering an area of 23,500 square metres with a storage capacity exceeding 100,000 locations that have an average of more than 30,000 products in store. Each day the warehouse handles around 14,000 order lines and moves product volumes totalling 160 tonnes.
Despite the differences at individual sites in terms of physical layout, technology and equipment, WASS provides a consistent method of operation based on a series of standard operations that make sure goods coming into the warehouse are registered, validated and stored in determined locations. It also makes sure that products destined to leave are located quickly and retrieved and that the flow of goods is orchestrated efficiently.
Timely information is key to operating an efficient warehouse management system. Key vehicles within a warehouse such as forklift trucks are equipped with on-board computers linked to WASS using wireless communication. WASS receives its orders from SKF’s customer order-handling systems and transmits these orders to the warehouse so that products can be picked from the appropriate pallet locations. In total, WASS handles between 6 and 7 million order lines annually.
WASS has resulted in a number of important benefits. For example, it has enabled SKF to increase throughput without increasing resources. This results in savings in operating costs for warehouse and distribution. As WASS works seamlessly with other computer systems, it means that warehouse and transport control can be integrated, internal transportation can be optimized and greater efficiency in transport volumes can be achieved. The fact that WASS operates in real-time information enables more effective stock control. This means that it is possible to reduce the amount of capital employed in stock or products in transit.
The transportation management system operated by SKF is, in itself, highly complex. It works to a strict timetable and makes sure that local transport systems link into international freight networks, enabling customers to benefit from an integrated system that minimizes, wherever possible, the time for an SKF product to reach a customer’s door. Picking of products within the warehouse, for example, is scheduled according to departure times for the trucks.
The opportunities afforded through computer control to reduce inaccuracies in moving products in and out of the warehouse also offer benefits. Increased quality of service to the customer comes from a reduction in picking errors and correct consignment information. Reduced order lead time and demands for special treatments can be managed and controlled without increasing operational costs.
The growth of e-commerce has significant implications for warehouse and distribution management systems. It puts pressure on companies to respond even faster and to provide a greater amount of information and greater access to that information to the customer than ever before.
One example of the development in logistics to extract greater efficiencies though the use of e-commerce and warehouse management is SKF’s involvement in CoLinx LLC. This is a venture set up in 2001 for the North American market by SKF and other companies to share the costs of running logistics and e-commerce activities and to support growth in that market.
CoLinx operates shared warehouses, a transportation network, freight-bill audit and payment services as well as an information technology group, and it operates in seven locations. Its technology base uses a commercial version of WASS, known as ASTRO, to support all its logistics activities. This system has enabled SKF and its partners to improve their deliveries to customers throughout North America by using a common logistics platform while maintaining control of their own information systems. This reflects the power of a common logistics platform for delivering products to where they are needed.