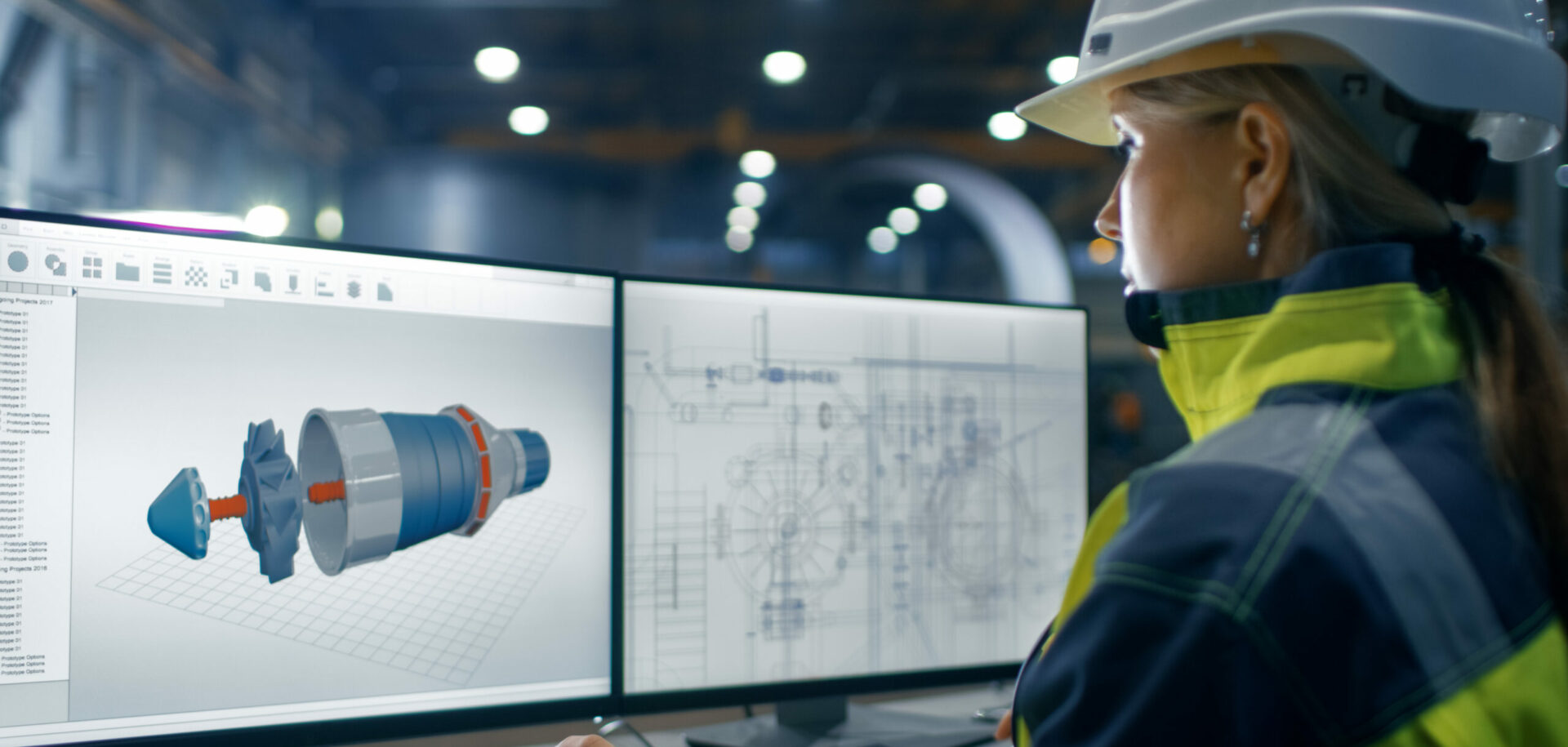
Metodi SKF di test non distruttivi
Per mantenere un livello uniforme di qualità, in linea con le specifiche aziendali, SKF impiega vari metodi di test non distruttivi.
Sintesi
SKF è impegnata nell’assicurare un’elevata qualità nella fabbricazione e nella ricostruzione dei prodotti attraverso tecniche di ispezione altamente affidabili, adottate lungo tutto il processo produttivo. I test non distruttivi sono mezzi di grande importanza ai quali SKF impone continui miglioramenti, standardizzazione e progressi tecnologici. L’elevata affidabilità degli NDT in SKF è supportata dall’impiego di apparecchiature idonee ed efficienti, procedure ben definite, operatori ben addestrati ed esperti e un elevato grado di automazione. SKF è anche preparata a cogliere le nuove opportunità offerte dalla digitalizzazione delle misurazioni NDT lungo tutto il processo di fabbricazione.
Negli stabilimenti di produzione, SKF impiega moderni metodi di test non distruttivi, con l’obiettivo di accertare che i prodotti siano integri e affidabili, controllare i processi di fabbricazione, abbassare i costi di produzione e mantenere un livello uniforme di qualità, in linea con le specifiche aziendali.
Il Quality Technology (QT) è un gruppo centralizzato dell’SKF Group Technology Development (GTD), che si occupa della standardizzazione e dello sviluppo di tutti i controlli di qualità degli stabilimenti SKF. Una delle attività più importanti portate avanti da tale gruppo è nel settore dei test non distruttivi (NDT, Non-Destructive Testing).
Tecnologie NDT
Un test non distruttivo è per definizione un processo di ispezione, collaudo o valutazione di componenti o unità, ad esempio per verificare la presenza di disomogeneità o differenze nelle caratteristiche dei materiali, che non influisce sulla funzionalità degli elementi esaminati. In altre parole al termine del test componenti e unità possono continuare ad essere utilizzati.
Le tecnologie NDT sfruttano fenomeni fisici come la radiazione elettromagnetica, la propagazione dei suoni e le proprietà intrinseche dei materiali per esaminare campioni solidi, come ad esempio i componenti dei cuscinetti. Esistono molti metodi di test, i più comuni sono i seguenti:
- con ultrasuoni
- elettromagnetici
- con particelle magnetiche (con correnti parassite)
- radiografici
- con liquidi penetranti
- visivi
- con emissioni acustiche
- termici/con infrarossi.
Dei metodi citati quelli con ultrasuoni e con correnti parassite sono i più usati nella fabbricazione dei cuscinetti. Li descriviamo nel dettaglio qui di seguito.
Test con ultrasuoni
I test con ultrasuoni (UT, Ultrasonic Testing) vengono realizzati con una serie di tecniche non distruttive che si basano sulla propagazione di onde ultrasoniche nel materiale o nell’oggetto da ispezionare. Nei casi più comuni, vengono fatti passare attraverso i materiali impulsi ultrasonici molto brevi di onde con frequenze da 0,1 a 20 MHz, per rilevare imperfezioni interne o per caratterizzare i materiali stessi.
In pratica, l’energia sonora viene introdotta nel componente da verificare portandolo in contatto con un trasduttore collegato a uno strumento di diagnosi. L’elemento centrale del trasduttore è un cristallo piezoelettrico che trasforma l’energia elettrica in energia meccanica sotto forma di impulsi sonori che passano attraverso il materiale [1].
Gli impulsi vengono riflessi dalle discontinuità del materiale, come le inclusioni e le porosità che si possono formare durante la produzione dell’acciaio (fig. 1).
La fig. 2 illustra le parti principali del trasduttore e il campo sonoro risultante, qui rappresentato dalla distribuzione delle pressioni sonore delle onde che si propagano nell’acqua.
Test con correnti parassite
Quello con correnti parassite (ET, Eddy Current Testing) è uno dei molti metodi di tipo elettromagnetico usati negli NDT, che utilizza l’induzione elettromagnetica per rilevare e caratterizzare imperfezioni superficiali e sotto-superficiali dei materiali conduttori, come acciaio e alluminio.
Il principio di funzionamento degli ET [2] è illustrato in fig. 3. Le correnti parassite vengono create sfruttando il fenomeno dell’induzione elettromagnetica. Quando si applica una corrente alternata a un conduttore – ad es. un filo di rame – intorno a questo e al suo interno si crea un campo magnetico (a), che si espande allorché la corrente alternata raggiunge il suo massimo e diminuisce quando la corrente va a zero. Se a questo campo magnetico variabile si avvicina un altro conduttore elettrico in quest’ultimo si forma per induzione una corrente elettrica. Le correnti parassite sono correnti elettriche indotte che compiono un percorso circolare (b).
Variazioni di conduttività elettrica e permeabilità magnetica nell’oggetto in prova e la presenza di difetti provocano una variazione della corrente parassita e un corrispondente cambiamento di fase e ampiezza che può essere rilevato con uno strumento collegato alla sonda (c).
In vari stadi dei processi di fabbricazione SKF, si applicano le tecniche ET su componenti finiti o semi-finiti dei cuscinetti per caratterizzarne le proprietà dei materiali e per rilevare difetti prossimi alla superficie, quali cricche e danni da surriscaldamento che si possono originare durante le operazioni di taglio.
NDT negli stabilimenti SKF
L’impegno SKF nell’assicurare la qualità inizia già dalla materia prima. L’azienda collabora con i fornitori per fare in modo che tutta la materia prima acquistata soddisfi i requisiti SKF. Particolare importanza assumono i controlli automatici in linea al 100 % eseguiti con i metodi NDT.
La maggior parte delle ispezioni NDT in SKF sono eseguite durante il processo di fabbricazione. L’azienda segue tutte le norme prescritte dalle industrie dove si impiegano cuscinetti SKF, in particolare da quelle ferroviaria e aerospaziale. La fig. 4 illustra una macchina per i test in linea al 100 % di cuscinetti per ruote e boccole ferroviarie.
Sulla spinta della necessità di avere una sempre maggiore affidabilità, altre industrie, come quella automobilistica e quella delle energie rinnovabili, richiedono il ricorso a tecnologie NDT. Per i cuscinetti impiegati nelle turbine eoliche, SKF adotta particolari procedure.
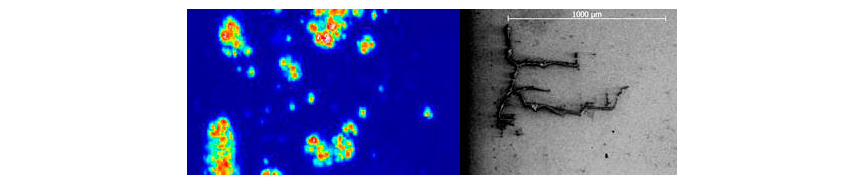
Ricostruzioni e ispezioni avanzate su cuscinetti resi
I cuscinetti che hanno funzionato o che sono stati sottoposti a prove di durata possono essere esaminati con vari metodi NDT, nell’intento di conoscerne più a fondo le cause dei guasti e i meccanismi di degradazione oppure, nel caso delle ispezioni fatte per stabilire le possibilità di ricostruzione di un cuscinetto, per verificare i danneggiamenti sotto-superficiali e vedere se un componente è adatto per continuare a lavorare.
In SKF, i test con gli ultrasuoni si usano per scoprire le eventuali cricche da fatica sotto-superficiali come parte del processo investigativo. La fig 5 (a sin.) mostra un’immagine ultrasonica C-scan che rappresenta l’energia riflessa da cricche esistenti sotto la superficie lungo la circonferenza della pista di un cuscinetto. Dopo il sezionamento e un esame al microscopio, i segnali ultrasonici possono essere correlati con l’effettivo danneggiamento sotto la superficie, fig. 5 (a destra).
NDT automatici e manuali
SKF cerca di automatizzare al massimo i metodi NDT nei processi di fabbricazione, in quanto l’automazione è in grado di aumentare l’affidabilità delle procedure di ispezione. La cosa è stata dimostrata in vari studi, secondo i quali, anche seguendo procedimenti molto dettagliati e affidandosi a operatori esperti, tutte le ispezioni manuali presentano deficienze dovute al fattore umano [3,4,5].
Tutti i metodi NDT sono per natura di tipo statistico e la loro capacità di scoprire difetti deve essere considerata in termini probabilistici. Di conseguenza negli NDT non ci sono certezze, solo probabilità. Oltre alla probabilità di scoprire un difetto veramente esistente, occorre considerare la probabilità di ricevere indicazioni circa la presenza di difetti che in realtà non ci sono (falso scarto) o quella di non rilevare difetti esistenti (falsa accettazione) [6].
L’affidabilità di un metodo NDT si può esprimere come una misura statistica quantitativa della capacità, in certe circostanze, di rilevare difetti di una certa entità in un dato punto. L’affidabilità del metodo NDT dipende da vari fattori: dalla scelta tra il metodo manuale e quello automatico, dalle potenzialità delle apparecchiature e dall’abilità degli operatori. In produzione l’affidabilità del metodo si può esprimere utilizzando la cosiddetta curva della Probability of Detection (POD). La fig. 6 ne mostra i principi, mentre la fig 7 illustra gli obiettivi SKF di miglioramento della POD e dell’affidabilità delle tecniche NDT ottenibili con ispezioni automatiche, operatori addestrati ed esperti, procedimenti dettagliati e apparecchiature efficienti.
Digitalizzazione
La digitalizzazione è il procedimento adottato per convertire le informazioni in formato digitale. Nei processi produttivi SKF, essa fa parte della trasformazione industriale, la cosiddetta Industry 4.0. Questa trasformazione è anche supportata dalla digitalizzazione dei dati delle ispezioni ottenuti dai test non distruttivi eseguiti in tutti i processi di fabbricazione.
Per tradizione, i dati della valutazione non distruttiva (NDE, Non-Destructive Evaluation) vengono spesso trascurati una volta terminato un test, perdendo la possibilità di sapere come un componente progredisce nel tempo. Anche quando i dati vengono conservati, spesso manca ogni correlazione tra di loro, e non si ha la possibilità né di integrarli in un’olistica rappresentazione del componente [7] né di intraprendere azioni nel processo produttivo che sfruttino le conoscenze originate dai dati stessi. Dati di ispezioni digitalizzati e correlati possono offrire nuove opportunità nella produzione dei cuscinetti, ad es. consentendo rapidi controlli e feedback dei processi di fabbricazione.
Modellazione
Per accelerare gli sviluppi e ridurre i test eseguiti su apparecchiature, che richiedono tempo e risorse, SKF si sta concentrando sull’impiego nell’ambito NDT di strumenti analitici e simulazioni. La fig. 8 mostra un esempio dei risultati ottenuti dalla modellazione della pressione di un campo sonoro sull’anello di un cuscinetto.
Collaborazione SKF con importanti partner esterni
Per garantirsi l’accesso agli ultimi sviluppi nel settore degli NDT, SKF valuta continuamente le opportunità di collaborazione con i migliori istituti, università e fornitori.
Una delle iniziative sponsorizzate da SKF è il Research Consortium in Non-Destructive Evaluation (RCNDE) [8]. Si tratta di una positiva collaborazione tra l’industria e l’accademia, co-fondata dal britannico Engineering and Physical Sciences Research Council (EPSRC). Membri del consorzio sono imprese internazionali dei settori manifatturiero, petrolio e gas, aerospaziale e nucleare, assieme a università britanniche, quali quella di Manchester, l’Imperial College di Londra, l’Università di Nottingham e quelle di Warwick, Strathclyde e Bristol. Queste università eseguono ricerche su progetti industriali di carattere generale, nonché su progetti che interessano in modo specifico SKF.
Recentemente SKF ha anche firmato un accordo di membership con l’Advanced Remanufacturing and Technology Centre (ARTC) di Singapore [9]. Il centro assiste SKF nello sviluppo delle tecnologie di fabbricazione e ricostruzione su livelli di maturità tecnologica (Technology Readiness Level, TRL) tra il 4 e il 6, dimostrando quindi nuove tecnologie in un ambiente rilevante. Lo sviluppo delle tecnologie non distruttive nelle verifiche dei componenti ricostruiti e le ispezioni sulla produzione sono i punti forti del centro.
SKF è anche membro del Jernkontoret, una branca dell’industria svedese nel settore dell’acciaio[10]. Uno dei suoi comitati di ricerca è interessato proprio agli NDT. Il suo ruolo è quello di avviare e gestire progetti di ricerca sui test non distruttivi finanziati dal governo svedese e portati avanti presso le università e gli istituti svedesi.
Bibliografia
[1] ASNT Handbook Non-destructive testing Volume 7 – Ultrasonic testing, 2007
[2] ASNT Non-destructive testing Handbook Volume 5 – Electromagnetic testing, 2004
[3] Marija Bertovic Human Factors Approach to the Acquisition and Evaluation of NDT Data, 18th World Conference on Non-destructive Testing, 16-20 April 2012, Durban, South Africa.
[4] Harris, D. H. and Chaney, F. B. Human Factors in Quality Assurance. (1969). New York, John Wiley and Sons.
[5] Drury, C. G. and Fox, J. G. Human Reliability in Quality Control. (1975). London, Taylor & Francis, Ltd.
[6] Guidelines to Minimize Manufacturing Induced Anomalies in Critical Rotating Parts, DOT/FAA/AR-06/3 – AIA Rotor Manufacturing Project (RoMan) Report October 24th, 2006.
[7] S. Holland, E. Gregory, T. Lesthaeghe Toward Automated Interpretation of Integrated Information: Managing “Big Data” for NDE, ASNT Research Symposium 24 March 2014.
[8] Research Centre in Non-Destructive Evaluation. https://www.rcnde.ac.uk/
[9] Advanced Remanufacturing & Technology Centre, Singapore. https://www.a-star.edu.sg/artc.
[10] Jernkontoret http://www.jernkontoret.se/en/research–education/.