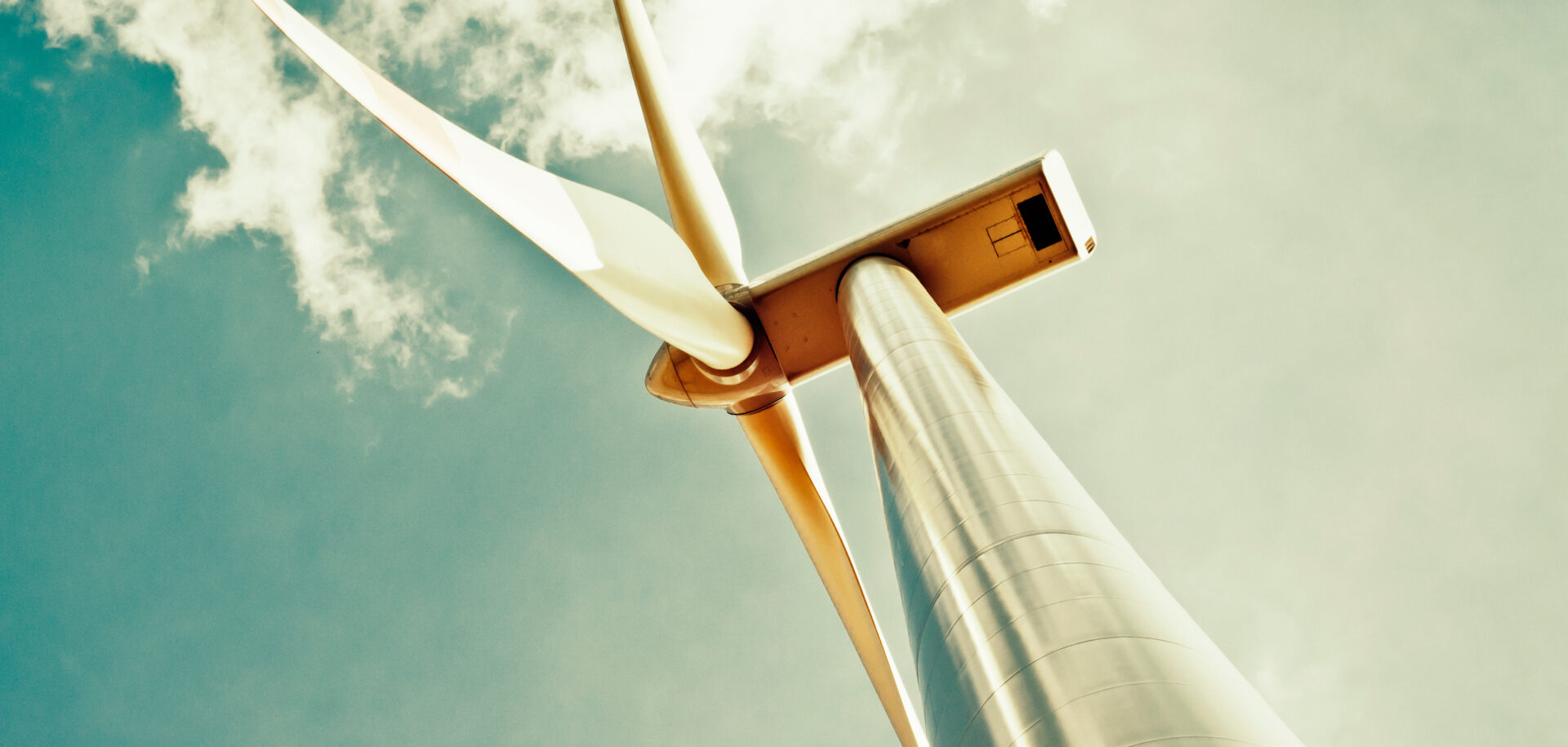
Nel vento o nel mare la lubrificazione è essenziale
Una lubrificazione ottimale è essenziale per l’affidabilità operativa delle turbine che operano in ambienti difficili, come quelle eoliche e quelle delle centrali di sfruttamento delle maree, e deve essere il risultato di soluzioni gestite con intelligenza.
Sintesi
Elevati carichi di tipo meccanico, contaminazione, vibrazioni e umidità condizionano sensibilmente l’affidabilità operativa delle turbine eoliche e a flusso di marea. In particolare, gli organi rotanti, come i cuscinetti e gli ingranaggi, richiedono grande attenzione. I sistemi automatici di lubrificazione forniscono la necessaria quantità di lubrificante alle macchine durante il loro lavoro e contribuiscono a ridurre attrito e contaminazione. In tal modo i cuscinetti possono raggiungere una durata di esercizio ottimale, gli intervalli di manutenzione si possono allungare e si riducono i costi operativi. In queste applicazioni i sistemi automatici di lubrificazione sono di vitale importanza.
Sistemi di lubrificazione per le turbine eoliche
L’energia eolica ha già da lungo tempo perso l’identità di un settore di nicchia, patrimonio di persone visionarie. Oggi essa rappresenta il 14 % del mix energetico europeo [1], ponendosi subito dopo il petrolio, il carbone e l’energia idroelettrica. Il settore eolico dà lavoro a circa 600.000 persone in tutto il mondo [2] ed è caratterizzato da tecnologie molto avanzate e da processi, norme e regolamenti in continua evoluzione. È ormai impossibile immaginare il panorama industriale senza l’energia eolica.
Nel corso degli anni le turbine eoliche hanno subito un costante sviluppo, in particolare per quanto riguarda le dimensioni. Nel 1990, il diametro dei rotori arrivava a soli 23 metri; nel 2014 aveva già raggiunto i 99 metri. Questa tendenza all’incremento di dimensioni, che si sovrappone a tutta una serie di regolamenti e di nuove esigenze, ha imposto nuove sfide ai costruttori di componenti.
I sistemi SKF di lubrificazione automatica hanno accompagnato l’industria eolica sin dagli esordi. Per più di vent’anni i sistemi a linea singola e quelli progressivi sono stati impiegati dalle più note aziende OEM di tutto il mondo (fig. 1).
Con l’aumento delle dimensioni delle turbine e i progressi tecnologici, i sistemi di lubrificazione sono diventati elementi essenziali per i cuscinetti dell’imbardata, delle pale, dell’albero principale e del generatore, e dei relativi ingranaggi.
Con una precisa quantità di lubrificante fatta arrivare al posto giusto e la momento giusto, si ottengono sicuramente vantaggi operativi, ma non è tutto: si possono prolungare gli intervalli di manutenzione e migliorare la disponibilità della turbina. Il rischio di incidenti si riduce al minimo, si evitano eccessi di lubrificazione e si diminuiscono i fermi macchina non programmati. Tutto ciò rende il portafoglio di prodotti SKF Lubrication una tecnologia consolidata e un’interessante opportunità di miglioramento, non solo per il settore OEM, ma anche per l’aftermarket nei progetti di modernizzazione dei vecchi impianti per il quale sono disponibili gli SKF Lubrication Upgrade Kit (fig. 3). Questi possono anche essere impiegati dal settore OEM come dispositivi plug-and-play di facile installazione per realizzare soluzioni personalizzate. Oltre alla pompa i kit comprendono tutti gli elementi di collegamento e gli accessori. Un ampio assortimento di kit conferisce la massima flessibilità alle relative applicazioni e offre la possibilità di servire numerosi punti di lubrificazione.
Grazie alla facilità di impiego, l’aftermarket utilizza principalmente l’SKF ProFlex (fig. 4a), che è un sistema di lubrificazione progressivo e differisce per costruzione e modo di operare da quello SKF MonoFlex (fig. 4b).
In un sistema progressivo il lubrificante viene fornito dalla pompa in modo continuativo al punto da lubrificare lungo la linea primaria e talvolta attraverso una secondaria. Il ciclo dura fino a che tutti i pistoncini del dispositivo di dosaggio hanno provveduto a inviare il lubrificante.
Se il grasso è contaminato o riempito in modo non corretto, può non venire erogato o bloccare i pistoncini. In tal caso, con l’impiego di un sistema di monitoraggio, si riceve un avviso di errore.
Nell’odierna industria i segnali di feedback di un sistema monitorato sono estremamente importanti. Il mercato esige che si operi in modo intelligente per ridurre al minimo i costi operativi e aumentare la durata di esercizio delle turbine. La SKF Lubrication punta a sviluppare sistemi indipendenti di monitoraggio e controllo. Con l’SKF Lubrication Remote Monitor (fig. 5) è possibile rilevare l’eventuale scarsità di lubrificante e segnalare i guasti. Se il serbatoio del grasso è vuoto o c’è un inconveniente nel sistema (ad es. un intasamento dei dosatori), viene inviato un segnale via sms a uno o più smartphone. Gli addetti alla manutenzione vengono subito avvertiti e possono intervenire. L’SKF Lubrication Remote Monitor è facile da usare, grazie al software preinstallato e ai componenti preventivamente configurati. Seguendo le istruzioni via sms è possibile aggiungere o togliere numeri di servizio e impostare ulteriori cicli di lubrificazione. Abbinando pompa e dispositivo, SKF Lubrication offre una soluzione economica per monitorare i sistemi di lubrificazione del mercato retrofit onshore.
Con una capacità installata complessiva, che nel 2015 ha raggiunto in Europa gli 11 GW (fig. 6) [3], il settore eolico offshore continua ad avere un enorme potenziale di crescita. Il Regno Unito offre le migliori prospettive, come dimostra la capacità installata totale pari a più di 5 GW [4].
La particolare collocazione delle turbine e le spesso ostili condizioni del mare esigono che i costi dell’energia offshore siano costantemente sotto stretta osservazione. Questo è in parte garantito dalla classe di protezione C5M (o talvolta alla “C5M – high”; ved. ISO 12944), a cui i costruttori di componenti si devono attenere. Nelle zone costiere e offshore esposte a elevati livelli di salinità essa impone una protezione anticorrosione efficiente per un periodo superiore ai 15 anni. SKF Lubrication utilizza un procedimento di nichelatura electroless che rappresenta un’alternativa più economica rispetto all’acciaio inossidabile.
Nel procedimento di nichelatura electroless i componenti vengono immersi in una soluzione speciale che crea uno strato di nichel di spessore uniforme per renderli resistenti ad aria, acqua, acidi e sostanze alcaline. Alla SKF Lubrication, dosatori, connessioni, supporti, elementi di pompaggio e alloggiamenti delle pompe vengono tutti trattati in tale modo. Per accertare e documentare la perfetta conformità alla classe C5M i componenti vengono sottoposti a un test di 1.440 ore in presenza di nebbia salata.
I sistemi di lubrificazione più usati sono a linea singola, SKF MonoFlex, i cui componenti sono indicati in fig. 7.
Quello a linea singola è un sistema che opera ciclicamente (si confrontino le figg. 4a e 4b). Il lubrificante viene fornito dalla pompa agli iniettori utilizzando solo una linea primaria. Ciascun punto lubrificante è munito di un iniettore, il quale, sotto la pressione della pompa, fornisce il grasso al punto da lubrificare. Diversamente da quanto accade nella sequenza di dosaggio dei sistemi progressivi, gli iniettori sono disposti in parallelo, con il vantaggio che, se un punto di lubrificazione si blocca, gli iniettori rimanenti possono continuare a fornire grasso. Nelle turbine offshore questa tecnologia ha consentito di incrementarne la disponibilità. La pompa continua a immettere grasso nella linea primaria fino a che non viene raggiunta la pressione prevista nel pressostato in essa incorporato, il quale quindi si attiva e spegne la pompa stessa. Nei grossi sistemi la pressione può essere monitorata tramite un pressostato aggiuntivo sistemato al termine della linea. Terminato il ciclo di lubrificazione la pompa viene spenta e la linea viene depressurizzata per mezzo di una valvola incorporata nella pompa stessa. Grazie al rilascio della pressione tra i cicli di lubrificazione, il sistema a linea singola può essere anche usato per fornire rapidamente lubrificanti di tipo diverso.
Sistemi di lubrificazione per turbine a flusso di marea
Con i suoi molti anni di esperienza nell’industria navale ed eolica offshore, SKF Lubrication non poteva non rappresentare un importante punto di riferimento per la nuova industria per lo sfruttamento delle maree (fig. 8).
Gli elementi di una turbina a flusso di marea hanno una tipologia di funzionamento analoga a quella degli elementi di una turbina eolica. Le esigenze di lubrificazione sono tuttavia molto più severe e devono adattarsi al particolare ambiente:
- lunghi intervalli di manutenzione dell’ordine anche di sei anni richiedono grossi serbatoi; non è raro incontrarne con capacità di più di 20 kg di grasso, in quanto l’accesso alle turbine è quanto mai difficoltoso, mentre il lavoro di manutenzione è assai costoso.
- nelle procedure di rabbocco automatico occorre essere certi che le pompe non girino a vuoto e sono quindi previste pompe supplementari.
- l’adozione di sistemi ridondanti raddoppia l’affidabilità della fornitura di grasso; se il dispositivo centrale si guasta, interviene la pompa supplementare.
- il grasso usato che esce attraverso i fori di scarico deve essere raccolto in qualche modo. SKF Lubrication prevede elementi che, disposti davanti alle uscite, aspirano il grasso; questo viene quindi indirizzato verso un apposito serbatoio centrale di raccolta. In tal modo si semplifica il lavoro di manutenzione in quanto si evita di installare contenitori in corrispondenza di tutte le uscite.
- tutti i componenti devono essere conformi alla classe di protezione C5M (ved. sopra).
Molti dispositivi che sfruttano le onde e le maree sono ancora allo stadio di test o di prototipi. Le coste del Regno Unito offrono condizioni ottimali per l’esecuzione dei test in condizioni reali; attualmente vi sono installate turbine sperimentali per un totale di più di 10 MW, valore superiore a quello relativo a tutto il resto del mondo [5].
SKF Lubrication ha già equipaggiato le prime turbine a flusso di marea installate nel Regno Unito. Per un loro effettivo contributo al mix energetico è solo questione di tempo.
Bibliografia:
[1] http://www.ewea.org/publications/reports/aiming-high/
[2] http://www.gwec.net/global-figures/wind-in-numbers/
[3] https://windeurope.org/fileadmin/files/library/publications/
reports/EWEA-Aiming-High.pdf
[4] https://windeurope.org/wp-content/uploads/files/about-wind/statistics/EWEA-Annual-Statistics-2015.pdf
[5] http://www.renewableuk.com/en/renewable-energy/wave-and-tidal/