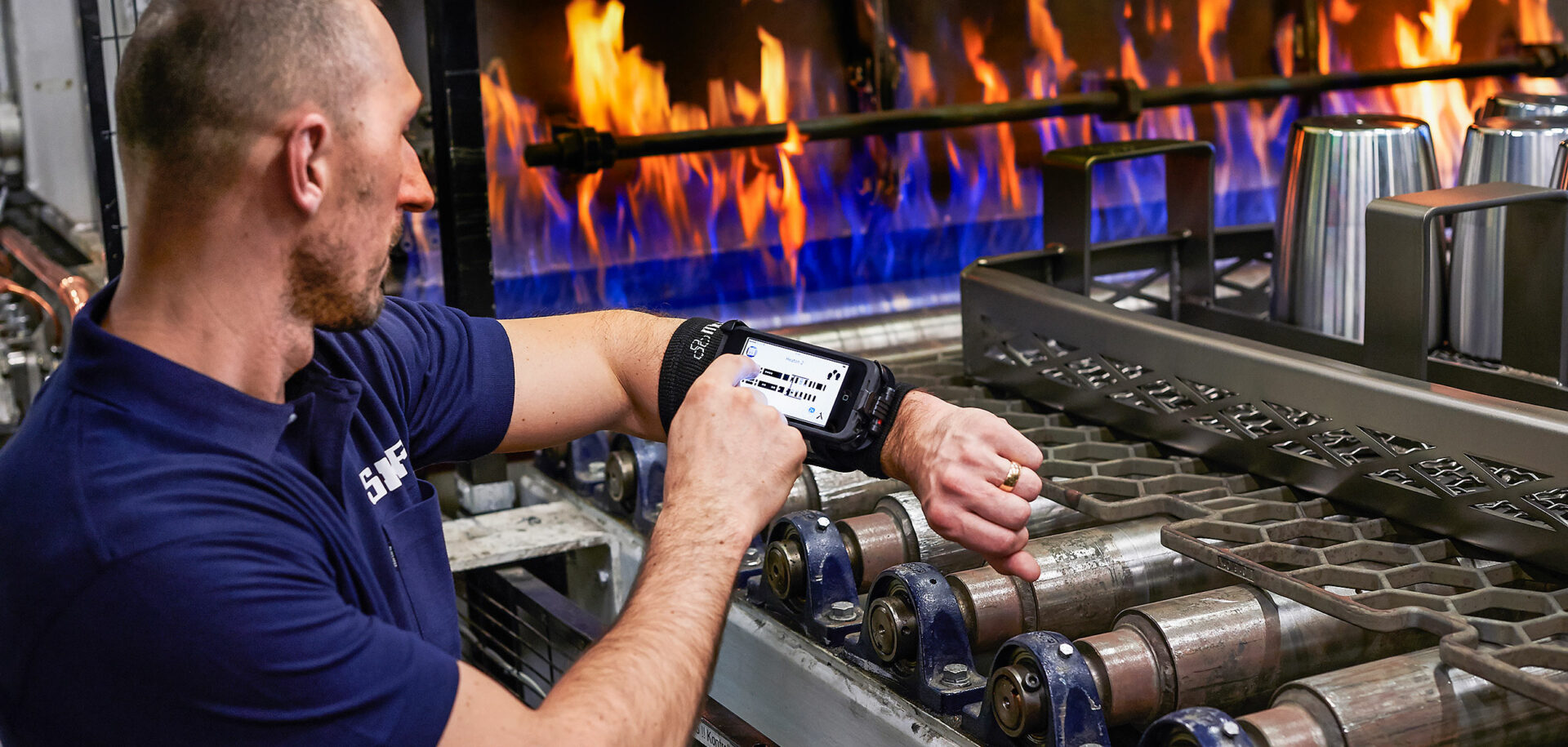
The making of a smart industry
In addition to mobility, digitalization is becoming increasingly important in industry, and the number of devices connected to the Internet keeps growing. In the past couple of years, SKF has taken a lead in digital development, driving the Industry 4.0 topic under the term “smartifying industry”. The fastest-growing connectivity will be in manufacturing, which is expected to represent almost one-third of the total value of Industry 4.0. SKF is smartifying industry in order to utilize these opportunities.
SKF’s smartifying industry delivers added value, which customers can experience as better performance of operations and services. “With smartifying industry, SKF is taking advantage of the opportunity that digitalization and mobility are creating for industry,” explains Christian Gill, SKF’s director of Digital Business Technology. “It is about digital development, which is the connection of assets to the Internet combined with cloud computing and powerful analytics, which leads to insights. This will help SKF to build a strong technical backbone to create new business but also to realize cost-effectiveness in manufacturing, application engineering, product development and cross-functional operations closely connected to those.
“Introduction of a smartifying industry strategy, including the use of smart devices, and establishing dedicated teams for smartified industry,” he says, “will, step by step, bring an entirely new business concept to SKF – a new way of working that will also have a big effect on customer relations.”
SKF aims at consolidating all digitalized applications under one umbrella in such a way that they function together, enabling opportunities to increase asset efficiency. The smartifying concept is tested every day in SKF’s own operations. Experience from in-house utilization provides insight for further development and innovations for customers afterwards.
Smartified industry is creating interesting opportunities for SKF and its customers, whether in SKF’s traditional business, in new business or in improved efficiency in utilizing assets, says Gill.
Applying new ways of doing business through digitalization
SKF intends to be a forerunner in the domain of smartifying its industry. This starts by applying the new ways of doing business to SKF’s own operations. Smart devices are being used group-wide, ensuring that SKF employees can benefit from mobility from sales to the factory floor. For example, production line operators control parameters such as line speed and can instantly see and react to alarms from mobile devices strapped to their forearms.
Smartifying industry by SKF
So, as stated, SKF is smartifying industry to take advantage of the opportunities that digitalization and mobility are creating for traditional industries. Here’s how:
Connect
Data needs to be gathered to understand machinery or assets. For that, sensors, devices, machines and other equipment need to be connected to a central collection point – SKF’s One Global Cloud Collect.
Collect
SKF’s One Global Cloud is a repository for continuous streams of data from interconnected assets. The higher power and lower costs of data storage and processing make it possible to create an infrastructure for easy and secure accessibility and intelligent data transfer.
Correlate
By looking into correlations in the given data and performing advanced analytics, SKF can provide deeper insight into the components, machine or system condition and behaviour. The analytics combined with SKF expertise deliver actionable information for easy and quick decision-making.
Collaborate
Connecting, collecting and correlating enable a new way of collaborating between people and between people and machines as well as between machines that can self-monitor, self-analyse and self-optimize running conditions and production and lead to increased efficiency and productivity.
MOST supports machine operators by connecting machines and people
MOST is a support tool developed by SKF for machine operators. In MOST, the principles of mobility, digitalization and advanced analytics have been applied on SKF’s factory floors. In some operations, employees can manage a partially virtual production flow from a smart device strapped to their forearms.
At the start of each shift, factory employees log in with secure authentication to the MOST app and are presented with a simple user interface depicting the factory floor. A series of shapes represent each machine, and operators can track every bearing product making its way through the production line. The status of machines is identified with colours. Sound alerts inform about problems. Factory employees can also share information and respond to issues instantly, regardless of location, through secure chat.
Complex machine and systems data are shown in a simplified form on an easy-to-use user interface. Employees save time by no longer having to crisscross the factory to collect data from various machines and desktop workstations. Weekly maintenance on factory machinery is also accomplished with the MOST app.
Enlight combines industrial apps for maintenance and reliability
This mobility- and cloud-based solution combines industrial apps developed by SKF with a range of mobile platforms and sensor technologies, providing user-friendly and flexible solutions for mainten-ance and reliability applications. SKF Enlight enables users in the field to collect and measure equipment status data and to connect instantly to subscription-based SKF knowledge services for diagnostic help and recommendations, whenever needed.
SKF Enlight is easy to use, like using a typical app on a smartphone. It gives customers direct access to pay-as-you-go speciality services from SKF knowledge engineers at the touch of a button. The only thing a customer has to do is sign up in order to have everything that is needed to get started; no capital investment is required. For small to medium-size production lines, this kind of smartifying solution can make enough of a cost difference for customers to stay competitive without having to relocate when looking for ways to cut operation costs.
The service includes industry-optimized smartphones and tablets, sensors and cloud storage for the data. Information from sensors is interpreted and displayed as easy-to-understand on-screen graphics that provide an instant status of machine parameters. Functionality can be expanded via application-specific forms.
24/7 access to operational maintenance information
Cloud technology connects and unites SKF Remote Diagnostic Services, providing customers with 24/7 access to operational maintenance information. This cost-effective service already covers half a million machines worldwide.
Any participating company with an Internet connection can access and analyse its machine condition and operating data. Plant or enterprise-wide data can be shared anywhere. The SKF One Global Cloud also means that customers can access condition-monitoring software quickly and without disruption to existing IT systems. The SKF One Global Cloud protects data integrity in key areas of concern, such as data security, data access, data transmission, data storage and data backup.
A great potential involved
Based on cloud computing and big data management, advanced analytics give industry great potential to make factories smarter, which means better productivity, efficiency and competitiveness. Industry is being smartified by means of intelligent solutions that process data into smart information through connectivity, data collecting, deeper insight and collaboration. With the growing interconnectivity of parts and systems, large amounts of data are being generated. This calls for a plan for making best use of it. Real-time analytics gives customers the power to make decisions while they can still make a difference, saving resources and minimizing unnecessary downtime.
The next revolution in industry
- Smartifying industry is about connectivity of people and things. It includes measures to digitalize this connection and to capture opportunities that boost efficiency and in the long term transform our very way of life.
- The boost in efficiency and business is expected to lead to some 110 billion euros in additional revenue from new digital products and solutions and an 18 % efficiency gain within five years in European industry.
- The number of new things connected to the Internet at the present rate amounts to 160 – per second.
- It is about how to transform industry through data connection, collection, correlation and collaboration.
- The gains from these measures include improved control, transparency, speed, productivity, modularity, availability, safety and sustainability.
SKF MOST
- This is an app that connects factory employees to live data from factory equipment, enabling them to collaborate, solve problems and improve factory output.
- The app has an easy-to-use interface.
- The app connects, collects, correlates and collaborates data.
- For example, by using SKF MOST, a new operator can reset a grinding machine in less than two hours, while the average time for an experienced operator is more than three hours. This results in substantial savings.
- Gains from using the app include knowledge sharing, up-to-date information, quick information and problem solving, improved safety and traceability, reduced waste and getting the right information to the right person at the right time.
SKF Enlight
- SKF Enlight is a data collection app with connectivity to multiple critical sensors.
- The sensors send operational data to a smartphone or a tablet via Bluetooth. The app calculates bearing condition and necessary actions through connection to the cloud.
- The app has an easy-to-use interface – no additional training or special experts are required .
- If a warning or alert is triggered, the user has only to push a button to get expert analysis from the SKF Remote Diagnostic Centre.
- The app saves work, as the client using it does not have to take equipment apart and document components manually.
- Smartphones and tablets can be developed for use in environments with an explosive atmosphere.
- The app connects, collects, correlates and collaborates data.
- Gains from using the app include lower costs, fast and easy handling, and instant connection to SKF expertise.