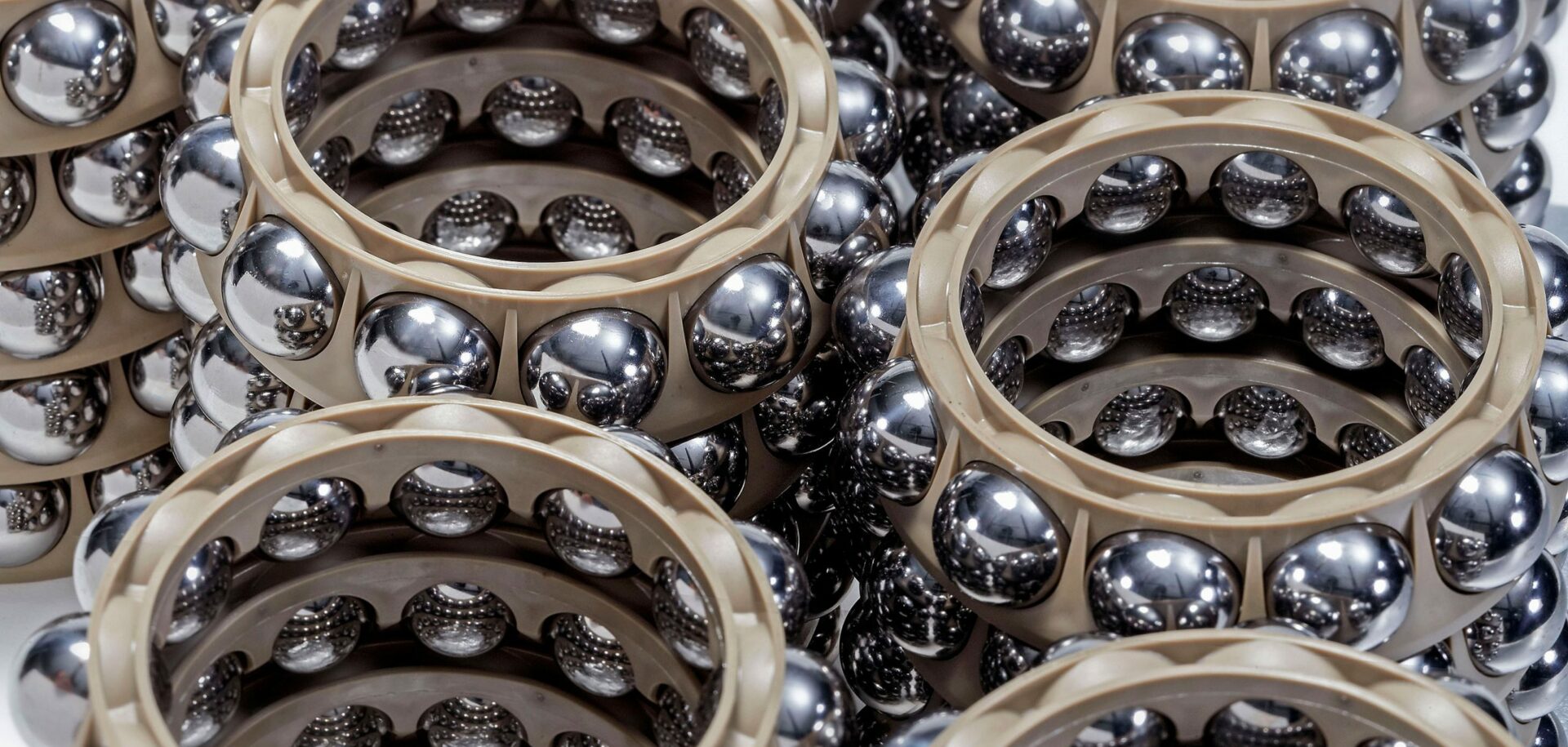
SKF polymer products and components
SKF is very well known as a leading bearing manufacturer worldwide, with high competence in steel-based bearing products and polymer sealing devices. However, and in parallel, many different polymer products and components have been developed by SKF over the years. This article gives a first overview of SKF’s competences in that field.
Summary
For decades and with great experience, SKF has used a large portfolio of different polymers and composites to design and manufacture cost-effective solutions for many different products, such as rolling bearings, plain bearings, overmoulded bearing units and housings for many different applications in the industrial, automotive and aerospace markets.
Polymer components for rolling bearings
SKF polymer cages excel in a number of characteristics, such as low weight, low noise level and good sliding properties coupled with low friction and minimal wear, high corrosion resistance and excellent emergency running properties, resulting in long service life. The possibility of designing complex cage geometries in combination with fast and high-volume one-step injection moulding manufacturing processes is an additional benefit for using polymer grades for rolling bearing cages.
For high-temperature applications and/or aggressive media requirements, SKF mainly selects the chemical-resistant fibre-reinforced polyetheretherketone (PEEK) polymer for cage production (fig. 1). PEEK cages are often used in applications such as screw compressors with ammonia as refrigerant or in sour gas applications, high-speed machine spindles, concrete vibrators, process pumps lubricated with hydrocarbons or liquefied gases or fire-safe hydraulic fluids, liquid-cooled car alternators, silent-running elevator gearboxes and many Formula 1 car-racing applications, including engine, gearbox, drivetrain and suspension linkages. Due to their strong performance in harsh environments, PEEK cage segments are also used for large SKF Nautilus bearings in wind energy applications (fig. 2).
SKF polymer cages for standard applications are mainly made from semi-crystalline polyamide (PA) material, reinforced with glass fibres to increase the mechanical strength and stiffness of the polymer matrix. These polyamide cages are used for standard applications in many different bearing types such as deep groove and angular contact ball bearings, cylindrical roller, needle roller and tapered roller bearings and also CARB toroidal roller bearings.
In railway applications, cages for SKF tapered roller bearing units (TBU) are made from super-tough polyamide to improve their shock-load resistance. In addition, to avoid fretting corrosion from separation of the TBU inner ring side face and axle backing ring due to axle bending, a polymer spacer with a special stiff and high creeping- and compression-resistant fibre-reinforced polyamide is used (fig. 3).
Full complement cylindrical roller bearings by definition have no cage. They have very high load-carrying capacity, but roller-to-roller contact can lead to slip, smearing and wear. A cost-effective solution to avoid this is to insert special SKF polymer spacers between the rollers (fig. 4). The results are reduced slip, higher speed limits and longer service life.
New SKF LBC D-series linear ball bearings have been developed to facilitate mounting and to obtain higher load ratings and extended life. The optimized polymer cage design contains a reduced number of components and has larger raceway slides, an optimized ball transmission zone and a larger grease reservoir (fig. 5). In combination, these properties lead to exceptionally high running smoothness with low friction and reduced noise levels. The new LBC D-series are particularly suitable for sensitive applications, e.g., medical engineering.
SKF polymer ball bearings are corrosion- and chemical-resistant, lightweight and quiet-running solutions with good damping properties (figs. 6a and 6b). Polypropylene (PP) or polyoxy-methylene (POM) are the standard materials used for the bearing rings, but other polymers are also possible on request. Balls can be made from polymer, stainless steel, glass or other materials. Cages are made from polyamide or polypropylene. Polymer ball bearings are self-lubricating with a low coefficient of friction and can run dry without additional lubricant, preferential in applications where lubricants cannot be used, e.g., for hygienic reasons. The high specific strength (strength-to-weight ratio) is also a valuable property of polymer bearings, especially in applications where weight is an important design consideration. Polymer ball bearings are typically used in applications where resistance to moisture or chemicals is essential and steel cannot be used or can be used only with certain restrictions.
Special SKF bearing units are used in a number of specific applications. SKF bearings can be overmoulded with polymers and combined with high-density and wear-resistant SKF metal powder gears in a one-step injection moulding process to create gear units, e.g., for twine tensioner units in hay press machines (fig. 7). Other SKF bearings are overmoulded with glass fibre-reinforced polypropylene (PP-GF) to create support hubs for top-loading washing machines (fig. 8). Cast polyamide is used to produce corrosion-resistant bearing housings (fig. 9).
Plain bearing polymer parts
Polymer compounds and composite materials play a key role in many SKF plain bearings. They contain polytetrafluoroethylene (PTFE) as a self-lubricating additive in a well-defined concentration and distribution, which results in low friction and wear behaviour of the composite sliding material.
SKF spherical plain bearings containing fibre-reinforced polymer material consisting of polyamide/PTFE/fibre sliding panels are either directly injection moulded or glued onto the inner surface of the steel bearing outer ring and slide against the steel inner ring (fig. 10). Especially when it comes to vibrations or medium shock loads, the excellent damping behaviour of these relatively thick compound panels pays off. In applications where dirt or moisture cannot be avoided, a certain embedding capability for small particles into the polymer matrix provides additional arguments for the use of the SKF fibre-reinforced polymer material.
SKF TX spherical plain bearings are fitted with a fabric liner sliding material that uses woven fabric of PTFE and reinforcement fibres embedded in a thermosetting three-dimensional chemical linked matrix resin (fig. 11). The TX fabric liner has a high stiffness and offers the lowest steady friction level throughout the entire service life. Furthermore, it offers excellent wear resistance and the highest load-carrying capability. SKF TX spherical plain bearings must not be lubricated and are maintenance-free.
SKF filament wound bushings contain PTFE and reinforcement fibres as sliding layer with glass-fibre backing embedded in a cured thermosetting resin matrix (fig. 12). These bushings have an excellent tribology behaviour even under harsh operating conditions. They are insensitive to edge pressure and misalignment, have a good ability to accommodate shock loads and have very good frictional properties, which opens up a wide field of possible maintenance-free applications.
SKF PTFE polyamide bushings (fig. 13) provide good heat-conducting characteristics due to the small wall thickness, enabling high sliding velocities at medium pressures. They have an adequate load-carrying capacity and a good wear performance and are very cost-effective.
Composite bushings, washers and strips are made from a steel backing with a porous bronze interlayer and a polyoxymethylene (POM) or PTFE+MoS2 compound top layer (fig. 14).
Polymer parts for the automotive market
SKF automotive polymer parts often combine some outstanding polymer properties such as low weight, good damping and corrosion resistance, together with the high strength and stiffness of steel.
A typical example are bearings that are mounted and overmoulded with high-temperature-resistant polymers. This is done in a one-step process by injection moulding into sheet metal housings to produce lightweight and stiff bearing units, e.g., for centrifuges to clean hot and oily blow-by gases blown from crank housings (fig. 15).
SKF power transmission polymer products such as high-performance fibre-reinforced polyurethane belts can be installed in many different applications; SKF bearings are overmoulded with polymers to produce lightweight and wear-resistant pulleys, e.g., for engine drive applications (fig. 16).
Thrust washers made from polyamide that incorporate small grease pockets to reduce friction and wear are used for universal joint bearings in truck drive shafts (fig. 17).
SKF also offers robust MacPherson Suspension Bearing Units (MSBU) with a polymer housing, integrated metallic spring seat for low deformation and optimized high sealing performance. SKF MSBU can withstand severe operating conditions and contribute to extending the operating life of the suspension (fig. 18).
Steering applications such as vibration absorber rings made from soft thermoplastic elastomers mounted onto bearing outer rings (fig. 19) or housings for steering units made from polyamide (fig. 20) are further examples of useful polymer parts in the field of SKF automotive applications.
Aerospace polymer parts
At SKF Aerospace, special polymeric composite materials based on fibre-reinforced thermosetting resins are used to produce low-weight and high-strength composite rods for wing boxes, floor beam struts and flight control rods (fig. 21).
Aerospace spherical plain bearings, including maintenance-free and self-lubricating polymer composite liners, are used for helicopter rotor systems, landing gear, pylon-to-wing attachments, engine-to-pylon attachments, flight control actuation and engine accessories attachments (fig. 22).
Precision elastomeric devices (PED) such as elastomeric bearings, isolators/mounts, diaphragm seals and boots as well as dampers (fig. 23) are further examples in the field of SKF polymer parts.