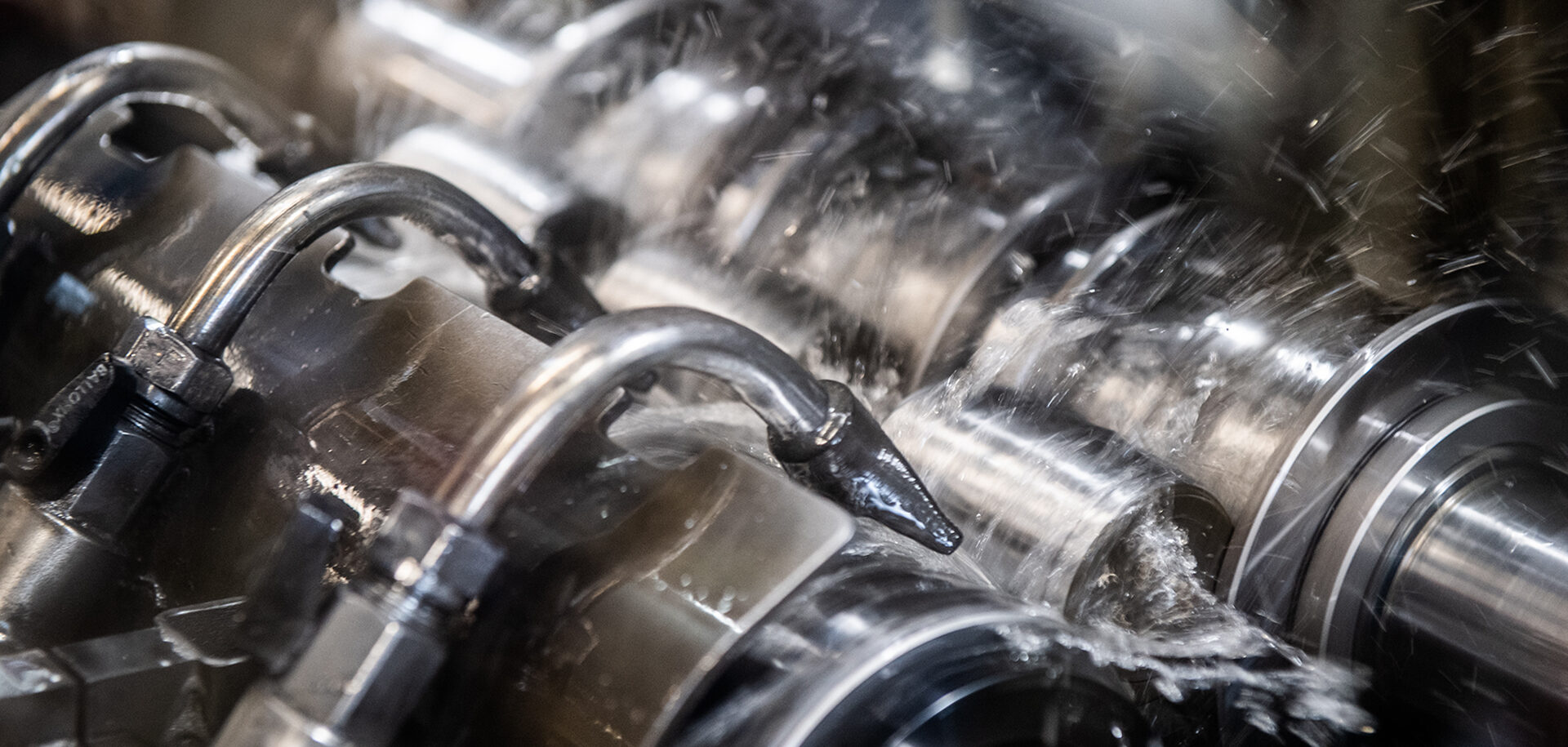
A clean start for bearing performance
Cleanliness is a critical factor for bearing performance and reliability. In the battle against contamination, prevention is always better than cure. SKF has developed clean manufacturing processes for decades. And the innovation continues. With SKF RecondOil, we can eliminate contamination down to nano-size and dramatically extend the life of process oils.
Dirt is the enemy of high-precision components
Over time, particles of dust and debris trapped in a bearing can lead to surface damage, fatigue and premature failure. Worse, contamination can cause problems long before a bearing is shipped to its end user.
If components are not scrupulously clean during manufacture, the critical grinding and honing processes used in production can be compromised, leading to microscopic surface imperfections. When we conducted an extensive study on the manufacturing issues that impact reliability and bearing performance, we found that cleanliness was the single most significant factor.
Clean processes help us produce bearings that have a demonstrably longer and more predictable lifespan along with lower noise and vibration levels. With clean manufacturing we achieve a higher, more stable quality level, reduce waste and eliminate unnecessary production costs. In a clean environment, production tools and process fluids last longer too.
That’s why monitoring, maintaining and improving cleanliness is a central element of the SKF production system, alongside lean productivity improvement methodologies and rigorous process control.
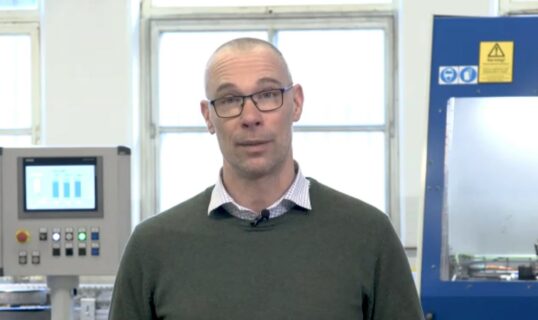
With clean manufacturing we achieve a higher, more stable quality level, reduce waste and eliminate unnecessary production costs.
Petter Hägg
Knowledge Area Manager for Clean Manufacturing at SKF.
A cleaner mindset
To ensure a part meets those targets, we need to pay attention to every aspect of the production environment. A part sitting on a bench waiting for the next process will gradually accumulate dust and contamination from the surrounding environment, for example. To keep that under control we need to think about the conditions inside the building, the performance of the ventilation system and even the quality of the paintwork on the ceiling. We need to understand how long parts are left sitting between process steps, and how they stored and handled on the way.
Building a clean manufacturing system is as much about mindset as anything else. SKF manufacturing specialists spend a lot of time looking at the smallest details of our production processes, identifying potential sources of contamination and finding ways to mitigate them. It is an effort that has a lot of parallels with the incremental continues improvement techniques that have made lean manufacturing so effective.
The solutions we find are often very simple. In one production plant, for example, components were ejected from a machine tool onto a steel slide. Studying the parts, we found that upon impact, microscopic fragments of the slide could break off, which contaminated the parts. The investigating team installed a low friction plastic cover over the steel, eliminating the problem.
In another case, we found that the ‘FlexLink’ conveyor systems used to move parts between workstations were picking up high levels of contamination. We installed a simple cleaning station on each conveyor to continually rinse off those particles. Elsewhere, we found that parts leaving a grinding process often had high levels of contamination on their surface. We developed a flushing station using multiple jets to wash the parts as they exited the machine. This simple modification reduced particle contamination by 80 percent. And because flushing was done using existing process fluids, it involved virtually no additional costs or resources.
A system-wide approach
Perhaps the most common misconception we hear when we talk about clean manufacturing is “it’s all about the washing”. Every component we produce is washed multiple times as it flows through production: between critical product steps, and again before final assembly.
Yet washing is just one part of a much wider and more systematic approach to clean manufacturing. To understand why that is so critical, you need to understand how cleanliness is measured and managed in the production environment.
The International Organization for Standardization has developed a code system for describing the level of particulate contamination found in fluids or on the surface of components. Cleanliness codes start at 0, for extremely clean components and rise up to 24 or above for heavily contaminated parts. Each code is associated with a minimum and maximum number of particles, measured per unit volume for fluids or per unit of surface area for parts. An additional letter code defines upper and lower size limits for the particle counts. Broadly, each step up or down the ISO scale is associated with a doubling or halving of the number of particles found.
An industrial component cleaning process is not designed to achieve a fixed ISO cleanliness grade. Instead, process performance is determined as the difference between the cleanliness of incoming and outgoing parts. For the washing systems most commonly used by SKF, that ‘delta’ is around 75 percent if the process is operating correctly. That means that a part will come out of the machine two ISO grades cleaner than when it went in. It also means that to achieve a certain cleanliness grade after cleaning, you need to precisely control the cleanliness of the ingoing part.
In a bearing production line, we will determine target cleanliness codes for parts and process fluids at each production step. Broadly, materials entering the upstream production process have higher codes (more contamination is acceptable) and the process becomes gradually cleaner as the part progresses through it.
A nanoscale future
The refinement of clean manufacturing at SKF has been a multi-year journey. Like other forms of continuous improvement, we believe that there are always opportunities to do more. One area where we are particularly active today is in the world of nanoscale cleanliness.
Conventional contamination detection systems are designed to detect particles as small as 5µm, with some specialist equipment able to count 1µm particles. Conventional cleaning and filtration systems are designed to deal with participles of similar sizes.
We know from our analysis of contaminated parts, however, that there is a strong inverse relationship between particle size and frequency. The smaller the particles you look for, the more of them you find. That means that parts may be contaminated with high levels of extremely small participles that are too tiny to detect.
In the past, clean manufacturing specialists ignored this nanoscale contamination, simply because there was very little they could do about it. Today, however, new technologies are becoming available that allow the production of super-clean oils and machining fluids, eliminating even the smallest particulate contamination.
In 2019, SKF acquired RecondOil, a small cleantech company with a patented process for cleaning oil at the nanoscale. The process is called Double Separation Technology (DST). With DST, all contaminant particles can be removed from the oil, regardless of size. It is early days, but in tests using fluids treated with SKF RecondOil’s DST system on our manufacturing lines, we have seen significant improvements in component surface parameters and in the noise and vibration performance of complete bearings.
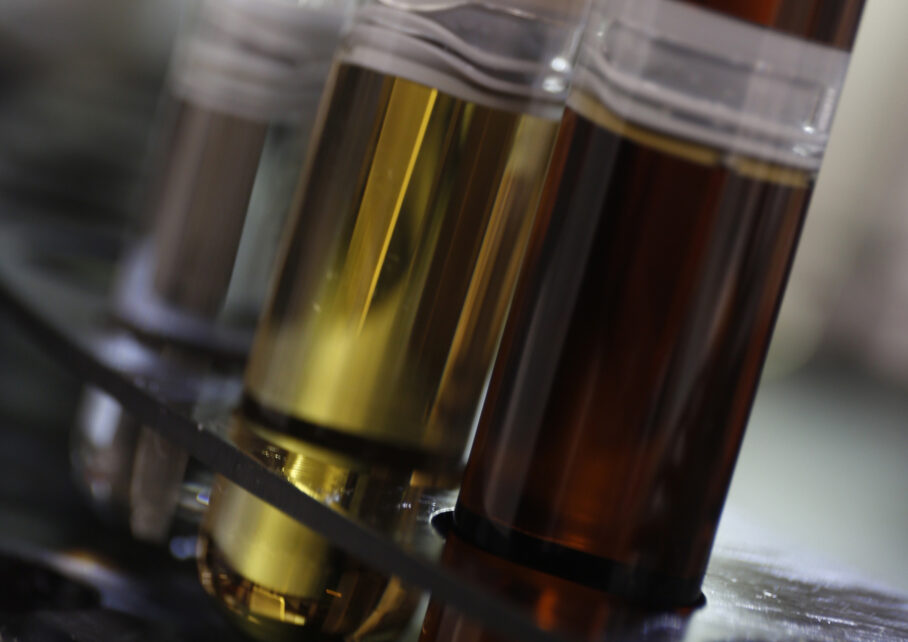