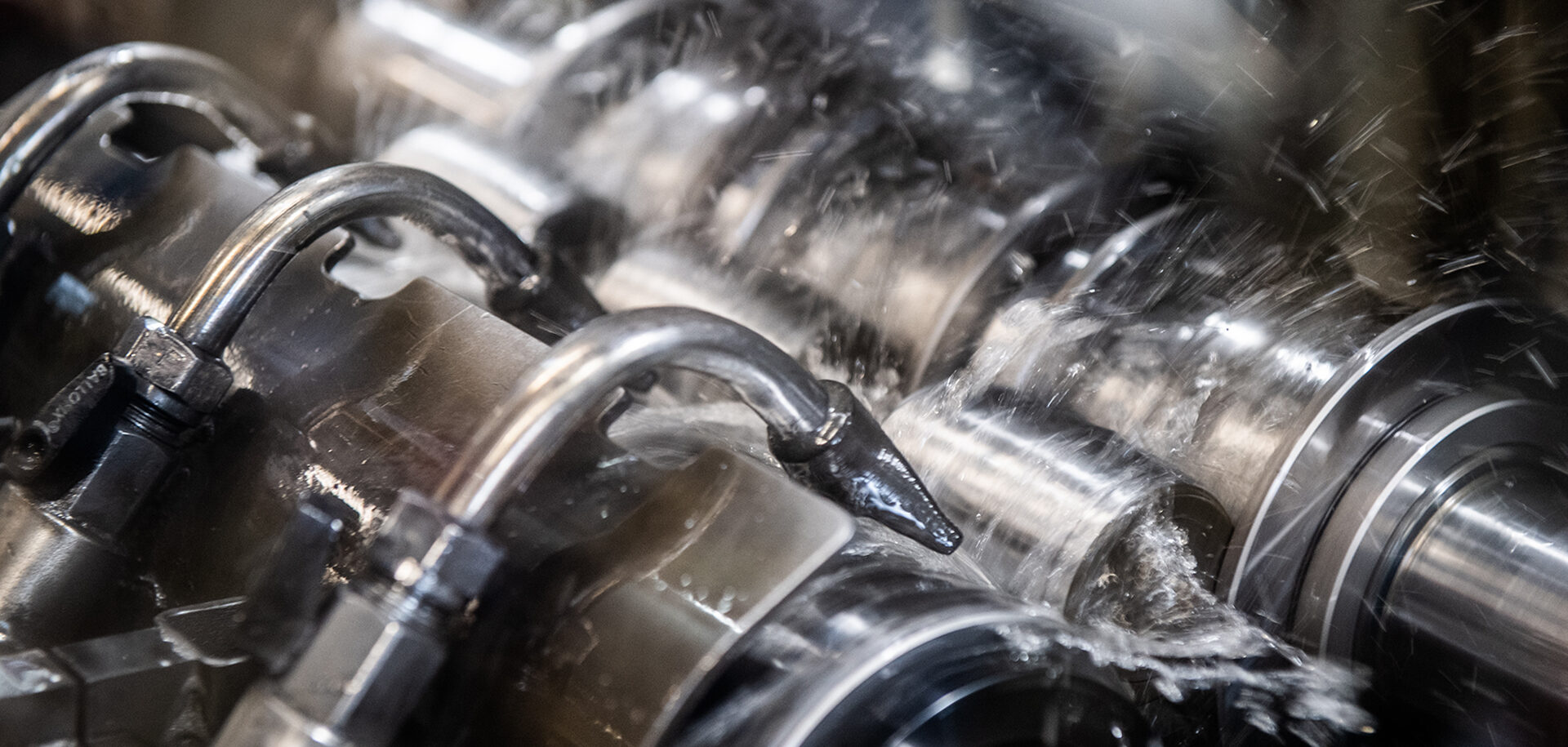
Un démarrage propre pour des roulements haute performance
La propreté est un facteur essentiel de la performance et de la fiabilité des roulements. Dans la lutte contre la contamination, mieux vaut prévenir que guérir. SKF met au point ses systèmes de fabrication propres depuis des décennies. L'innovation se poursuit aujourd'hui avec l'adoption d'une nouvelle technologie qui élimine la contamination nanométrique et augmente considérablement la durée des huiles de fonctionnement.
La saleté est l’ennemie des composants de haute précision
Au fil du temps, les particules de saleté et les débris piégés dans un roulement peuvent entraîner une avarie superficielle, de la fatigue et une défaillance prématurée. Pire, la contamination peut engendrer des problèmes bien avant l’expédition d’un roulement à son utilisateur final.
Si les composants ne sont pas parfaitement propres pendant leur fabrication, les processus de rectification et rodage critiques exécutés lors de la production peuvent être compromis, conduisant à de microscopiques imperfections à la surface. Lors de l’étude que nous avons menée sur les problèmes de fabrication affectant la fiabilité et les performances des roulements, nous avons constaté que la propreté était LE facteur le plus important.
Des processus propres nous permettent de produire des roulements avec une durée de vie plus longue et plus prévisible avérée, présentant des niveaux sonores et de vibrations réduits. Avec une fabrication propre, nous obtenons un niveau de qualité plus élevé et plus stable, réduisons les déchets et éliminons les coûts de production inutiles. Dans un environnement propre, les outils de production et les fluides de traitement durent aussi plus longtemps.
C’est pourquoi la surveillance, le maintien et l’amélioration de la propreté sont au cœur du système de production SKF, parallèlement à des méthodologies d’amélioration de la productivité optimisées et à un contrôle rigoureux des processus.
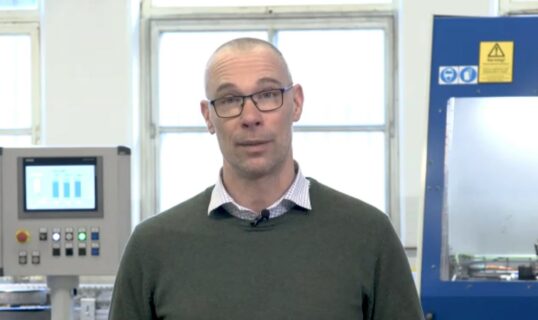
Avec une fabrication propre, nous obtenons un niveau de qualité plus élevé et plus stable, réduisons les déchets et éliminons les coûts de production inutiles.
Petter Hägg
responsable Knowledge Area pour une fabrication propre chez SKF
Une approche plus axée sur la propreté
Pour être sûrs d’atteindre ces objectifs, nous devons prêter attention à chaque aspect de l’environnement de production. Une pièce placée sur un banc dans l’attente du processus suivant accumule progressivement de la poussière et des impuretés environnantes, par exemple. Pour garder la contamination sous contrôle, nous devons réfléchir aux conditions à l’intérieur du bâtiment, aux performances du système de ventilation, voire à la qualité de la peinture au plafond. Nous devons connaître la durée d’immobilisation des pièces entre deux étapes de processus et leur mode de stockage et de manutention tout du long.
Créer un système de fabrication propre est surtout un état d’esprit. Les spécialistes de la fabrication SKF consacrent beaucoup de temps à observer le moindre détail de nos processus de production, à identifier les sources potentielles de contamination et à trouver des moyens de les limiter. C’est un effort qui présente beaucoup de similitudes avec les techniques d’amélioration continue incrémentielles qui contribuent à l’efficacité d’une fabrication optimisée.
Les solutions que nous trouvons sont souvent très simples. Dans une usine de production, par exemple, les composants étaient éjectés d’une machine-outil vers une glissière en acier. En étudiant les pièces, nous avons constaté qu’en cas d’impact, des fragments microscopiques de la glissière pouvaient se détacher et les contaminer. L’équipe de recherche a recouvert l’acier avec un plastique à faible frottement, éliminant ainsi le problème.
Dans un autre cas, nous avons découvert que les systèmes de convoyeurs « FlexLink » servant à déplacer des pièces entre les postes de travail accumulaient des niveaux élevés de contamination. Nous avons installé une station de nettoyage simple sur chaque convoyeur pour éliminer en continu ces particules. Ailleurs, nous avons remarqué que les pièces quittant un processus de rectification présentaient souvent des niveaux élevés de contamination superficielle. Nous avons mis au point une station de rinçage à plusieurs jets pour laver les pièces à mesure qu’elles quittent la machine. Cette simple modification a réduit de 80 % la contamination par particules. Et comme le rinçage était effectué avec des fluides de traitement existantes, quasiment aucun coût ou ressource supplémentaire n’a été nécessaire.
Une approche systémique
L’idée reçue la plus courante que l’on entend lorsque l’on parle de fabrication propre est peut-être que « tout est une question de lavage ». Chaque composant que nous produisons subit plusieurs lavages tout au long de la production : entre les phases de production critiques et à nouveau avant l’assemblage final.
Pourtant, le lavage ne représente qu’une infime partie d’une approche plus large et plus systématique de la fabrication propre. Pour comprendre son importance, vous devez comprendre comment la propreté est mesurée et assurée dans l’environnement de production.
L’organisation internationale de normalisation (ISO) a élaboré un système de codes pour décrire le niveau de contamination par particules décelé dans les fluides ou à la surface des composants. Les codes de propreté commencent à 0 pour des composants extrêmement propres et vont jusqu’à 24 ou plus pour les pièces très contaminées. Chaque code est associé à un nombre minimum et maximum de particules, mesuré par volume unitaire pour les fluides et par unité de superficie pour les pièces. Un code alphabétique supplémentaire définit les limites de taille supérieure et inférieure des comptages de particules. En gros, chaque échelon supérieur ou inférieur dans l’échelle ISO est associé à la multiplication ou à la division par deux du nombre de particules détecté.
Un processus de nettoyage de composants industriels n’est pas conçu pour atteindre un degré de propreté ISO fixe. En revanche, les performances du processus sont déterminées comme la différence entre la propreté des pièces entrantes et sortantes. Pour les systèmes de lavage les plus couramment utilisés par SKF, ce « delta » avoisine les 75 % si le processus fonctionne correctement. Cela signifie qu’une pièce sortira de la machine plus propre de deux degrés ISO que lorsqu’elle y est entrée. Cela signifie aussi que pour atteindre un certain degré de propreté après le nettoyage, vous devez contrôler avec précision la propreté de la pièce entrante.
Dans une ligne de production de roulements, nous déterminerons les codes de propreté cibles des pièces et des fluides de traitement à chaque étape de la production. Dans l’ensemble, les matériaux entrant dans le processus de production en amont comportent des codes plus élevés (une contamination plus importante est acceptable) et le processus devient progressivement plus propre à mesure que la pièce avance.
Un futur nanométrique
Le perfectionnement de la fabrication propre chez SKF a pris plusieurs années. Comme d’autres formes d’amélioration continue, nous pensons qu’il est toujours possible de faire mieux. Un point sur lequel nous sommes particulièrement concentrés aujourd’hui est la propreté nanométrique.
Les systèmes de détection de la contamination classiques sont conçus pour détecter des particules de 5 µm, et certains équipements spécialisés sont capables de comptabiliser des particules de 1 µm. Les systèmes de nettoyage et de filtration classiques sont conçus pour traiter les particules de même taille.
Grâce à notre analyse des pièces contaminées, nous savons toutefois qu’il existe une forte relation inverse entre la taille de particule et la fréquence. Plus vous recherchez de petites pièces, plus vous en trouverez. Cela signifie que les pièces peuvent être contaminées par des niveaux élevés de particules extrêmement petites qui sont trop minuscules pour pouvoir être détectées.
Par le passé, les spécialistes de la fabrication propre ont ignoré cette contamination nanométrique, simplement parce qu’ils ne pouvaient pas y faire grand-chose. Aujourd’hui, cependant, de nouvelles technologies permettent la production d’huiles et de fluides d’usinage super-propres, éliminant même la contamination par les plus petites particules.
En 2019, SKF a acquis RecondOil, une petite entreprise de technologies propres possédant un processus breveté de nettoyage de l’huile à l’échelle nanométrique. Ce processus est appelé Technologie à double séparation (DST). Avec la DST, il est possible d’éliminer toutes les particules polluantes de l’huile, quelle que soit leur taille. Nous n’en sommes qu’au début, mais les tests réalisés avec des fluides traités avec le système DST de SKF RecondOil dans notre ligne de fabrication ont révélé d’importantes améliorations dans les paramètres de surface des composants et dans les performances sonores et vibratoires des roulements complets.
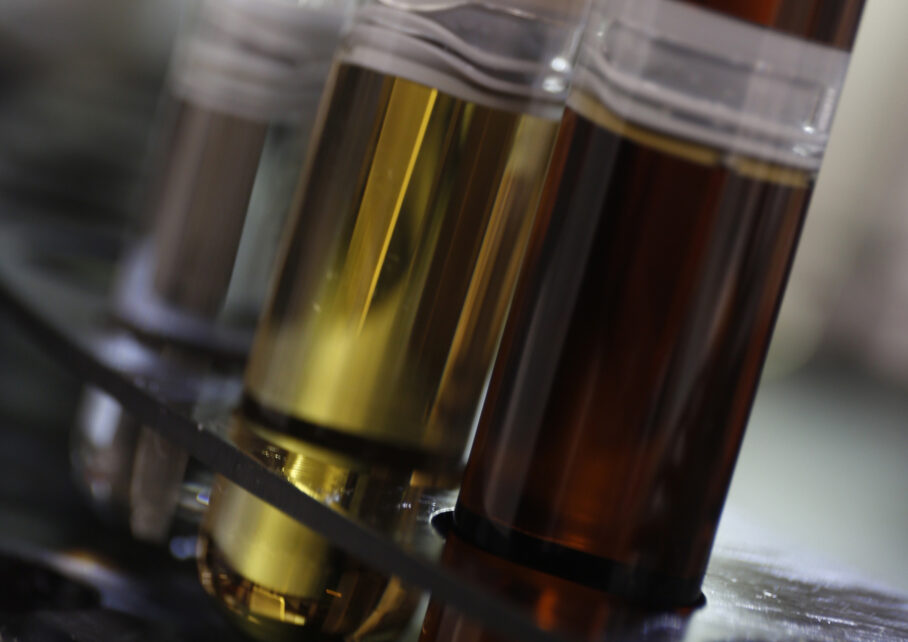