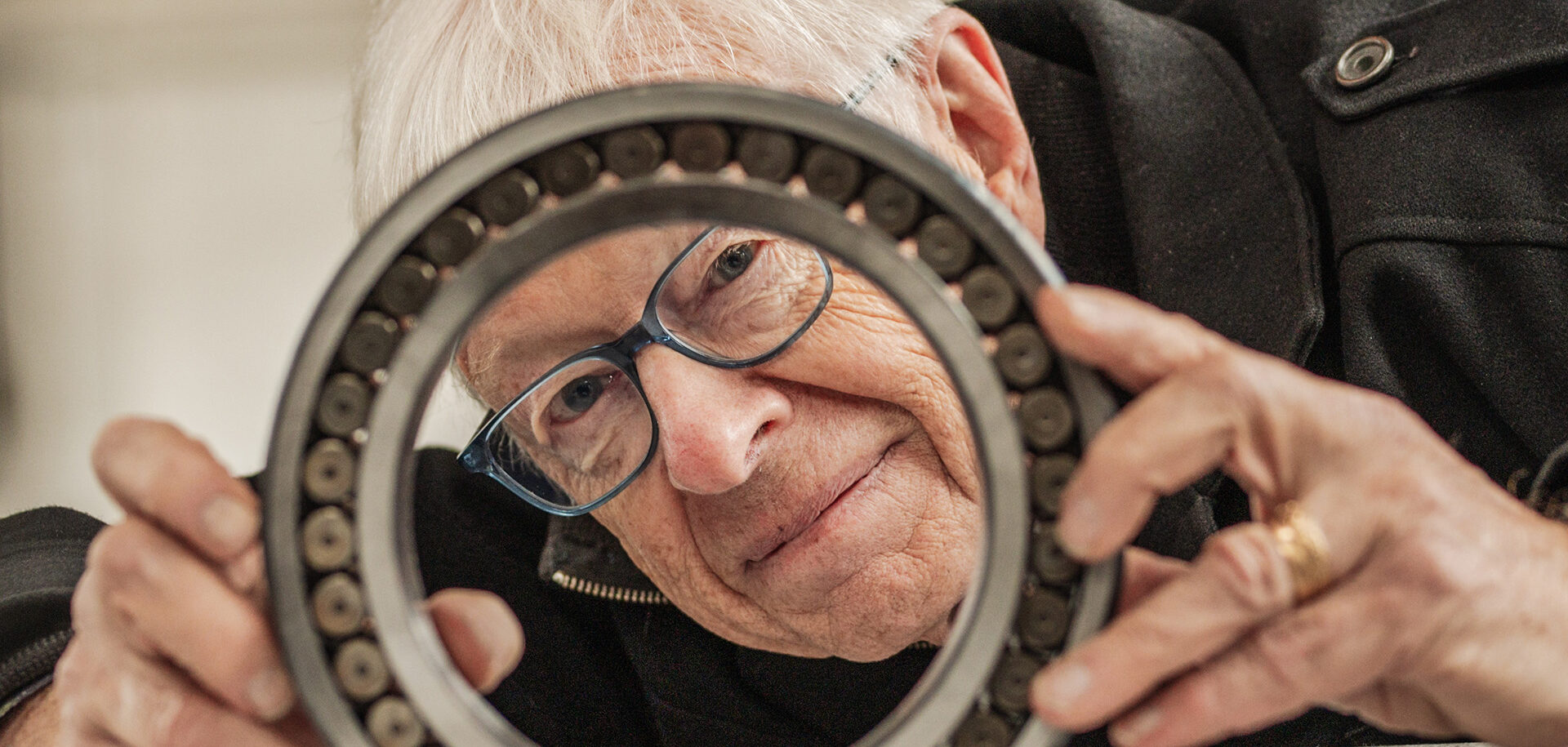
A magic potion for machines
In the 1990s, SKF development engineer Magnus Kellström invented a completely new kind of bearing. His ideas are still changing the world, one revolution at a time.
Magnus Kellström doesn’t let convention stand in the way of a good idea. You can tell that from his bicycle. Retired since 2005, he gets around his hometown on a recumbent two-wheeler, sitting back in a reclining seat with the pedals positioned far forward over the front wheel. It’s a design that enthusiasts say is more comfortable and more aerodynamic than what’s found on standard bicycles.
The same willingness to challenge status quo characterized Kellström’s 39-year career at SKF, where he worked in a wide range of product development roles. During this time, Kellström helped to push forward the art and science of bearing design, bringing new tools and innovative ideas to a class of products that quite literally help the world go round.
In the late 1960s, Kellström worked on the introduction of computers to the engineering process. “All industrial companies were getting computers at the time,” he recalls. “They were as big as a room, but far less powerful than today’s mobile phones. Yet they could still make calculations much faster than any human.”
Those early machines were far from user-friendly, however. Kellström and his colleagues would create programs on paper punch cards, which they then submitted to the data centre for processing. The engineers wouldn’t know if the program had worked until the results came back a day or so later. “Of course, we made mistakes,” he says. “But we only made a mistake once, then we never made it again.”
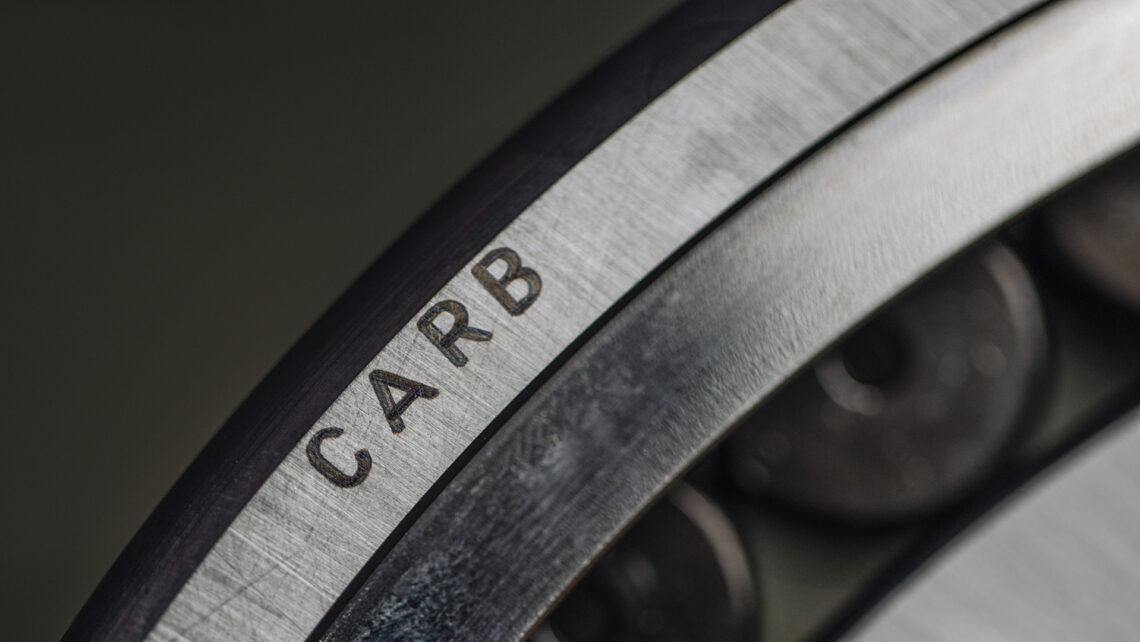
Going global
Kellström’s expertise in computer-aided bearing design took him across the world during the 1970s, with a year-long stint in the US developing a computer program that automated thermal calculations for bearing design. Globalization was in full swing at the time, and like many other industrial companies, SKF was adapting its footprint, creating centres of excellence in different product groups that could serve global markets.
By the early 1980s, he was back in his native Sweden, working at SKF’s main centre for the development and production of spherical roller bearings (SRBs) in Gothenburg. The product, then a mainstay of the bearing industry, can trace its history back to the innovative ideas of Sven Wingquist, SKF’s founder.
“Sven Wingquist invented the self-aligning ball bearing to solve a problem in the factory,” explains Kellström. “Ball bearings offer very low friction, but they cannot tolerate high loads. SKF developed the spherical roller bearing designed to address that limitation.”
Like Wingquist’s original innovation, SRBs are designed to cope with the challenges machines face in the real world. They can support both radial and axial loads, and they can tolerate angular misalignment without significantly increased friction or risk of jamming. That matters because machines must tolerate manufacturing imperfections or distortions due to heavy loads.
At the Gothenburg centre, Kellström and his team refined SKF’s SRB range, creating designs that offered lower friction, higher load capacity and a longer working life. The products were good, but they had their limitations.
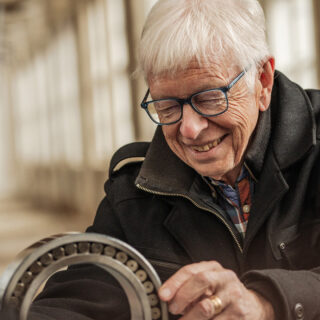
Inventing, for me, is about solving puzzles that most people don’t even realize are puzzles.
Magnus Kellström, SKF development engineer
Making improvements
One problem was heat. When machines change temperature in use, components can expand or contract. Standard SRBs don’t cope well with axial movement that can occur on long shafts. It can lead to higher friction and there is a risk of premature wear. Machine makers explored solutions, but none were ideal; cylindrical roller bearings struggle with misalignment, and mounting SRBs to special sliding housings adds bulk, cost and complexity.
While trying to address premature bearing failures in industrial planetary gearboxes, Kellström realized that there was room for a radically different approach. He sketched an idea for a totally new type of roller bearing, which would cope with axial movement while retaining the SRB’s tolerance of angular misalignment.
It took a few years for Kellström to convince his colleagues that his invention was worth the significant effort needed to turn it into a commercial product, but he eventually secured some R&D funding for a small-scale project. “Our job was making better SRBs, not inventing new bearings, so at the beginning, it was a bit of a ‘skunk works’,” he recalls. “It is true that my name is on the main patent, but there is more to it than that. It takes much more than an idea. I have been surrounded by some real champions, and without them CARB would never have succeeded.” Kellström and his colleagues pressed on with their development efforts during the early 1990s, eventually coming up with a design they called the “compact aligning roller bearing”, or CARB for short.
The CARB’s secret was its shape, which combined features from three existing bearing types: the SRB, the cylindrical roller bearing and the needle roller bearing.
It took several years of analysis, testing and refinement before the team had a design that fulfilled their ambitions. Like many development projects, completion came with little fanfare. “I remember standing with a group of engineers in my carpentry workshop and we just felt ‘now it’s done’,” he recalls.
Hot off the press
It wasn’t done. Invention is only part of innovation. Kellström still had to persuade SKF to make the necessary investments to put CARB into production, and there was no proof that the market was ready for a new bearing concept. “Back then product development was different from today,” he says. “We would come up with ideas and our sales and application engineering colleagues would then see if there was a market for them.”
CARB’s first big breakthrough came in the paper industry. In the early 1990s manufacturers were developing new ranges of extremely high-speed paper production machines. They were looking for a bearing solution for the rollers in those machines, and Kellström’s new design was a perfect fit. “CARB bearings were used on a machine that broke the world record for production of newsprint,” says Kellström. “I think that’s when I knew that our idea was going to have a significant impact.”
SKF launched the CARB commercially in 1995. Its innovative design was soon attracting customers in a wide range of industries, from metals production to renewable energy. “When a German wind turbine company replaced a conventional bearing arrangement with a CARB solution, the weight of the bearings in the turbine was reduced by 2,600 kilograms, and the smaller bearing allowed a lighter, more compact housing, saving another three tonnes.” says Kellström. “That saving allowed reduction of the weight of the tower by several more tonnes.”
Stronger together
The unique shape of the CARB gave it its special characteristics. The rollers inside the CARB were long relative to their diameter, like a needle roller bearing. Like a spherical roller bearing, those rollers had a convex shape, although they were considerably flatter than a conventional SRB. The inner and outer races had a concave profile that closely matched the profile of rollers. The rollers were free to move within the races, accommodating both angular misalignment, like an SRB, and axial movement, like a cylindrical roller bearing.
The CARB bearing was always designed as a partner to the SRB, not as a replacement for it. In typical applications, a shaft is supported at one end by a conventional SRB, which takes the axial loads and keeps the shaft in the correct position. At the other end, a CARB accommodates any axial movement caused by thermal expansion.
Axial movement wasn’t the CARB’s only trick. The new bearing also offered other favourable characteristics. The long rollers could support high loads, for example, while their relatively small diameter made the whole bearing assembly extremely compact. Together that resulted in a bearing that weighed less and took up less room than conventional designs.
The power to save
CARB has been on a roll ever since. SKF’s innovative bearing is now used in many of the world’s most demanding applications, including the electric propulsion systems that power today’s most advanced cruise ships.
“Cutting friction is like giving your machine a magical potion, making it smoother, quieter and longer lasting while saving energy,” says Kellström. “Heat, vibration and extra loads can wear out bearings. Every hour of downtime is an hour of lost production income and profit. It may also trigger maintenance costs and safety risks. When failure like that isn’t an option, reliability is everything.”
The original work of the CARB development team has stood the test of time. Today’s CARB bearings benefit from many incremental SKF innovations, such as advanced new steels, sophisticated seals and clever cage designs. Their basic geometry has changed very little, however.
Kellström moved on to other projects within SKF, but CARB has remained an important part of his life. Following his retirement, he has worked part time as a specialist consultant, advising machine makers on bearing design and selection.
“Now I find enjoyment in resolving bearing problems that would not exist if CARB had been used,” he says.
And when he’s not riding his recumbent bicycle, or advising the world’s top machine makers, Magnus Kellström is still quietly innovating, working on inventions in his garage. “Inventing, for me, is about solving puzzles that most people don’t even realize are puzzles,” he says. “My drive comes from solving problems and making a difference for so many businesses and for society as a whole. Doing something good for SKF is the same as doing something good for the world.”