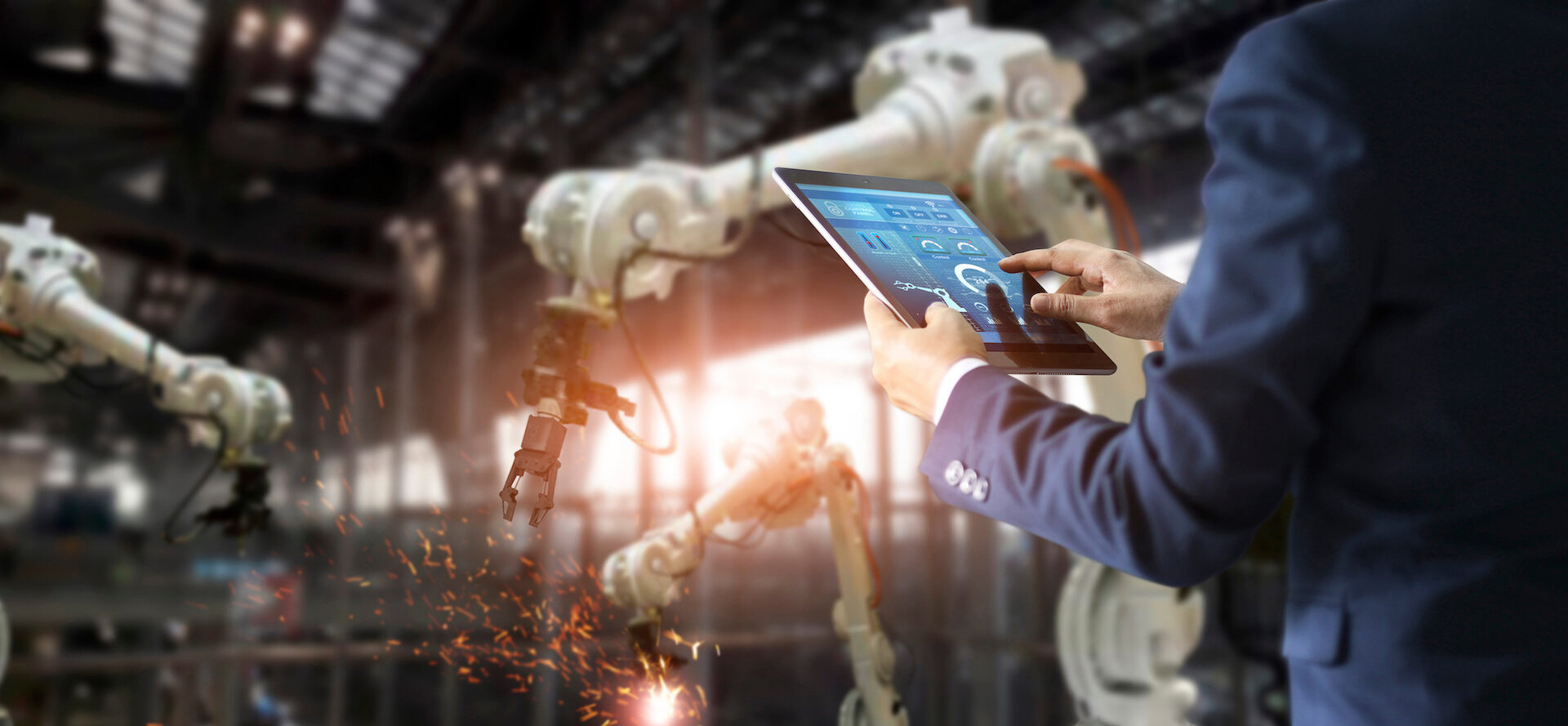
A new wave in industrial communication
The consumer world has embraced wireless communication. In industry, machines still communicate largely by wire. But new developments show promise of making radio waves a reliable option.It started with the wireless radio. Now radio waves envelop us, from the garage door opener to the mobile phone, bringing convenience as well as communication.
Industry has been looking at the potential of wireless communication for some time, but efficiency – not convenience – is the driving force. The prospect of saving money and time has driven the latest developments in industrial radio applications.
But it’s not usually a matter of merely replacing cables with radios. Hugh Burchett, head of the RF Products group at Cambridge Consultants, a major technology and innovation company based in Cambridge in the United Kingdom, says it doesn’t cost much to add a communication cable to an existing power feed, and most machines have a power feed.
“But there are cases where cable installation is expensive or difficult, or where radio can provide additional options,” he says. One example is crane control, where companies offer systems so the operator can stand near the load and operate the crane more safely from there.
Sometimes it’s physical distance that makes wireless communication the best option. In the state of New Mexico, TMC Design Corp is developing a huge radio network that will monitor and control the agricultural irrigation system for the Elephant Butte Irrigation District in the southern part of the state.
Over a total area of more than 600,000 hectares, the state of distribution canals, irrigation channels and boreholes is being monitored and controlled with small, low-cost sensors and transceivers.
The system allows the district to accurately bill farmers for their water use, and helps in planning water needs for 55,000 hectares of irrigated land. The main computers map the entire irrigation system for south-central New Mexico, receiving information from the transceivers about water levels and flows.
“In the end,” says Christopher Ham, TMC’s vice president, “there’ll be 5,000 to 10,000 small solar-powered transceivers, feeding into 500 larger units, which will communicate with the project centre.”
Sometimes the distance is small but hard to bridge. The MoFDI (Mobile Fieldbus Devices in Industry) project, funded by the EU, is developing radio applications for industrial control where the distances involved might be just a few centimetres, even millimetres.
Imagine, for example, a situation in which a control signal needs to cross a moving part, like a bearing. Within the MoFDI project, Kvaser of Kinnahult, Sweden, has developed the WaveCan transceiver, which adapts fieldbus network signals so that they can be carried by radio.
In fieldbus systems, signals are sent between many devices along a single twisted wire circuit. That saves complicated cable runs, and signal coding ensures that only the right devices will respond to a specific signal. Kvaser is a provider and developer of fieldbus systems using CAN (Controller Area Network), one of the main fieldbus protocols.
Even fieldbus systems can confront obstacles. Lars-Berno Fredriksson, president of Kvaser, says that if the system comes up against a moving part, such as a slip ring, that transfers electric current from a stationary to a rotating part, radio might well be the better option.
“The radio signal acts as a bridge between two CAN networks,” says Fredriksson, “but you have to ensure that the CAN error-correction protocols survive across the wireless link, even though the wireless protocols are different.” Kvaser solves the problem by wrapping the CAN signal in a signal using the Bluetooth wireless protocol.
Speed is important
Bluetooth is an exciting tool for industrial control purposes. Although it was developed for consumer use, it provides high-quality, real-time, high throughput rates in the licence-free frequency range of 2.45 gigahertz.
Burchett of Cambridge Consultants says that because of the consumer interest and large potential volumes, major companies are investing heavily in the protocol – investments they might not make if they had to rely on the limited volumes of the industrial market.
But Fredriksson contends that developing the technology for consumer use can be a disadvantage. “Real time for a consumer means ‘pretty fast,’” he says, “whereas in industry we think in milliseconds.” It may not matter much if a Bluetooth signal linking a personal mobile phone to a laptop is a bit late, but the same delay in a machine safety control could be disastrous.
Bluetooth is also being considered as an option for a more adventurous maintenance application. The Arvika project, led by Siemens and supported by the German Ministry of Education, is exploring how to use what is called Augmented Reality for maintenance tasks.
An engineer is equipped with a wearable computer and a virtual reality visor to which a video camera is attached. Video pictures of the machine are compared with a computerised model and the model is superimposed on the real thing in the visor.
The engineer’s instructions come in the form of text “hung” onto the relevant component, although he also has access to advice from a remote expert who will be able to see everything the engineer sees. Wolfgang Friedrich of Siemens, who leads the Arvika Consortium, says, “It would be ergonomically preferable and better for safety to have radio communication between the visor and the computer instead of a cable, but Bluetooth is not yet quick enough to carry the video.” Communication between the wearable computer and the factory’s LAN is already via radio.
Cambridge Consultants’ Burchett says investigations are being conducted into how Bluetooth could be used in the industrial environment, and what level of performance could be expected for time-critical functions. He says work is being done on making the technology cheaper, too. Cambridge Silicon Radio, a spin-off of Cambridge Consultants, is working towards a price of about 5 US dollars for a single CMOS chip.
’Change me’
Even that may be too expensive for some uses. Waldemar Grudzien of the Special Research Project on assembly technology and factory management at the Technical University of Berlin says he wants chips at around 50 US cents.
He is working on incorporating chip-transceivers in consumer products that will record usage and wear, and help with maintenance and disassembly. A chip in a coffee machine has to be cheap if the coffee machine is to find buyers.
So far, his project has been focusing on washing machines. The chip contains information about the machine and records how the various parts are wearing. Before a part wears out, the transceiver signals that the part needs to be replaced. The maintenance technician’s computer then instructs the part to release itself by opening the appropriate side panel and disconnecting the unit.
At the end of the product’s life, the chip can tell the robots at a recycling factory how to take the product apart and which parts are good for recycling. In light of new laws in Europe requiring consumer goods to be recycled, the Life Cycle Unit could be a useful tool. As it is now, every piece of machinery has to be dismantled by hand.
The use of radio frequencies for industrial monitoring and control is still a young technology. The real challenge is to make radio communications resistant to interference and distortion, so that machines can rely on them absolutely.
It may be some time before we can trust our lives to radio as we do to electric wires, but radio’s power over us is increasing all the time.
Michael Lawton
a business journalist based in Köln
illustration Peter Varhelyi