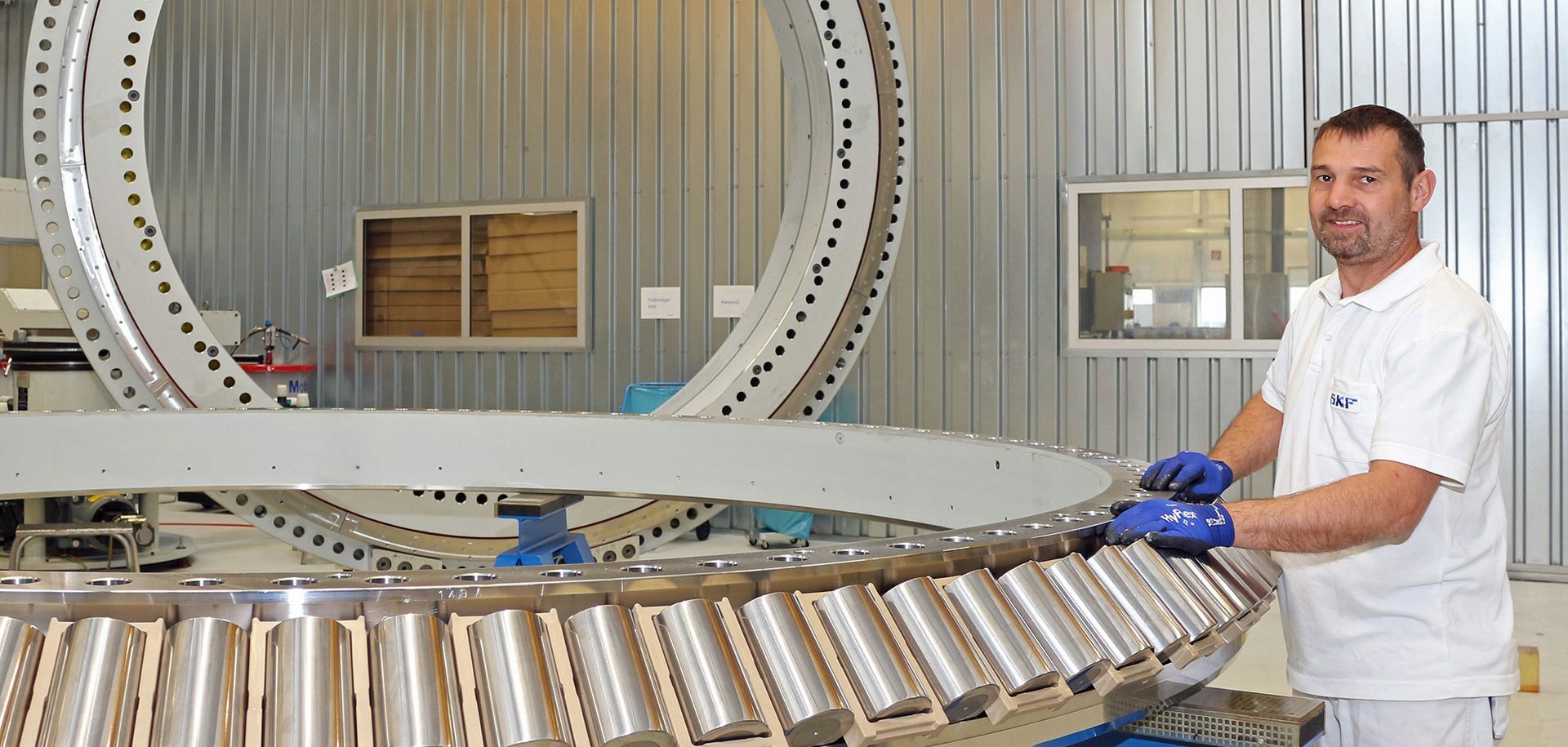
Advanced testing accelerates development of offshore bearings
As offshore wind turbines increase in generating power, main shaft bearings need to meet the ever-higher demands placed on the power generating equipment. Consequently, it is vital that these bearings be tested extensively before they are installed offshore so that they achieve the required operational life.
The testing was carried out at the industry-leading Sven Wingquist Test Centre (SWTC) in Schweinfurt, Germany. This award-winning facility has been specifically designed to test large-size bearings and make sure they meet industry requirements.
Powerful test rig
The SWTC facility is designed to reproduce all the conceivable loads that a bearing may experience in the field over its lifetime, condensed into a matter of weeks. This accelerated programme of testing saves time, money and energy.
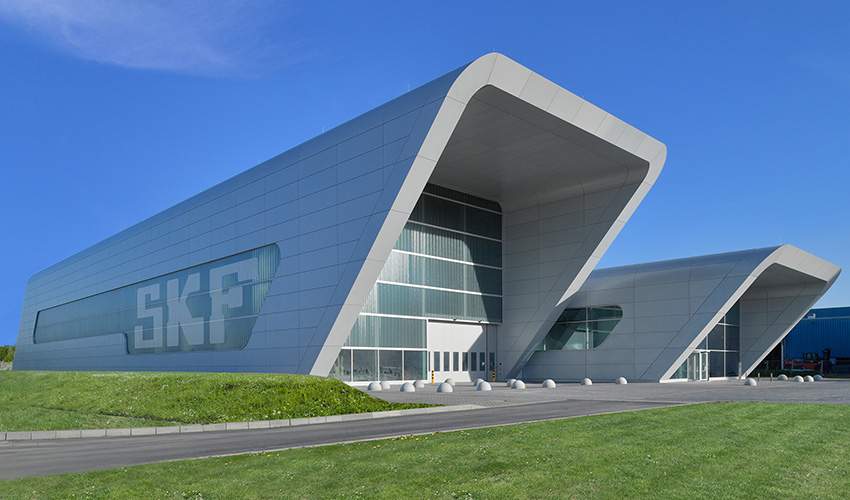
Varied testing regime
Before the MSTR there were limitations on testing because of the lack of suitable test rigs for large-size bearings as well as the challenge of testing such huge components. The MSTR can run a variety of tests, which may run for minutes, weeks or months. The rig can measure temperature at multiple positions, input load, speed and moment of the test rig, friction torque of the bearing, vibrations of bearing and test set-up, roller kinematics and deformations of the test rig structure and the components.
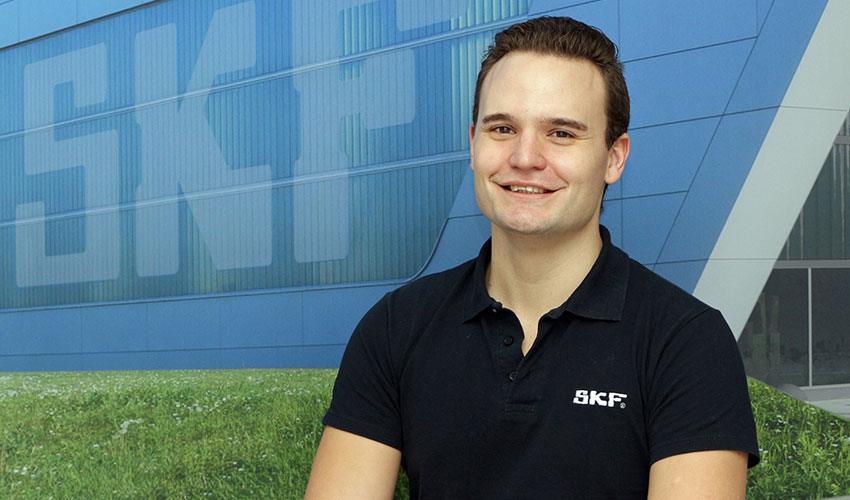
“These measurements can be compared with SKF simulation tools,” he continues, “and the measurements show a very good correlation with one another, which allows for further development of SKF’s testing and simulation competences.”
On the MSTR, the test bearing was accelerated up to 30 revolutions per minute – a milestone and currently the limit of the test rig. Faster rotational speeds directly raise the number of overrollings in the bearing, which helps to fulfil the requirements of an endurance test in a much shorter time and in turn influences cost and duration of the test regime. The ability to produce extreme speed is critical for the bearing components (e.g., cage segments). Due to the faster rotational speed, the component forces based on inertia and roller impacts to flanges and cages are increased significantly. The roller set, which is rotating at about half of the bearing speed, has a mass of 1.6 tonnes – the mass of a mid-size car. For the acceleration from 0 to 30 r/min, the MSTR is capable of applying 880 kW. As a guide, typical rotors for large wind turbines rotate at about 5 to 20 r/min; reaching the higher rotational speeds makes it possible to reduce testing times and test for extreme conditions.
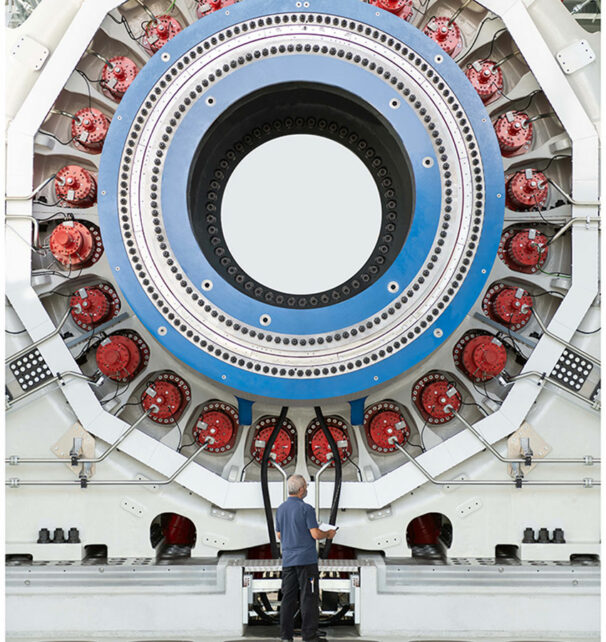
The current test campaign will be completed by the end of 2020, and plans are to include an exchange of the test bearing to another one with a different internal geometry. Test campaigns for 2021 and beyond are in preparation to utilize the MSTR in the most optimal way.
Pathway to the future
So far, the testing has made it possible to compare collected test data under several simulated operating conditions.
“For now, we are very happy with the data that we have collected,” says Engbers. “We still have high expectations for the upcoming test campaigns. Testing to these limits is vital for robust turbine developments, particularly as wind turbines move to the 15 MW power class and beyond for the future.”
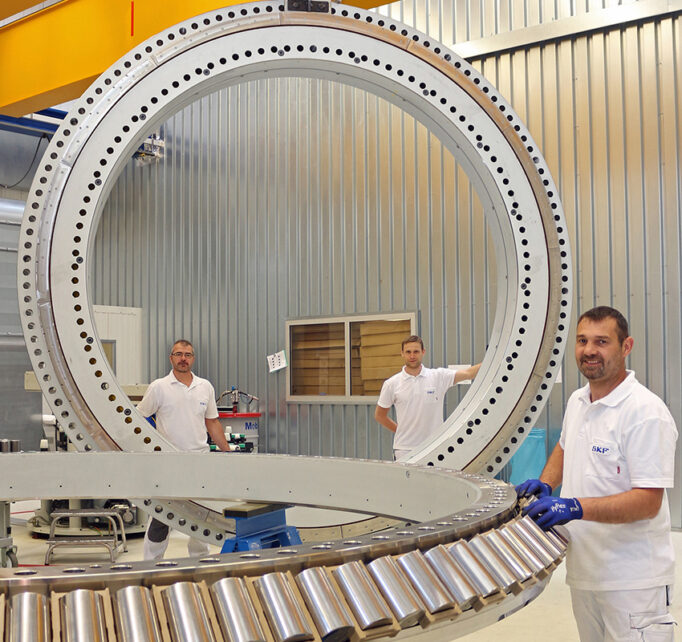
In addition to testing the Nautilus bearing, other bearing types will be tested on the rigs in the SWTC, which comprises four test rigs. This will include testing of large-size, multi-row cylindrical roller bearings, single-row tapered roller bearings, spherical roller bearings, CARB bearings and other bearing types.
SKF Nautilus bearings
The SKF Nautilus is a giant in the bearing world, with an outside diameter of up to four metres, and a weight of up to 14 tonnes. It is used as a main shaft bearing for offshore wind turbines with power ratings of 8 MW. As a main shaft bearing it carries the weight of the rotor and blades as well as accommodating the wind forces acting on the rotor.
The SKF Nautilus is a double-row tapered roller bearing in a back-to-back arrangement (also called an O arrangement). It does the job of two single bearings so that the complete drivetrain can be designed to be more compact. In addition, for special bearing arrangements, the SKF Nautilus bearing can be integrated into the gearbox, though it is still the bearing for the main shaft.
SKF Nautilus bearings in wind applications are expected to attain a bearing life of more than 20 years, so the ability to test them thoroughly is crucial.