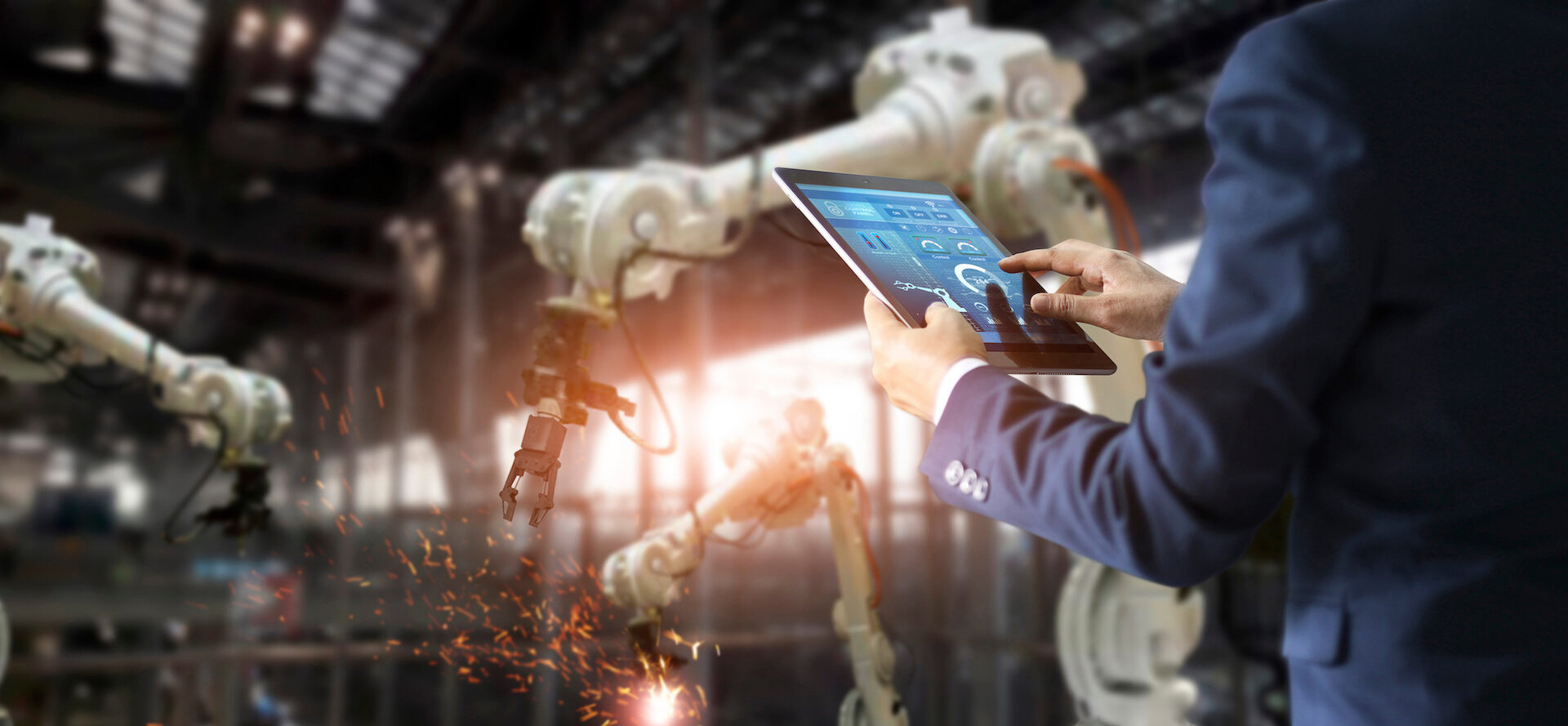
Covering the distance with SKF Axletronic odometers
Harmonization of rail network control systems offers international interoperability as well as major savings on investment and maintenance costs and easier operation. SKF is contributing to this development with its SKF Axletronic odometers.
Summary
The growth in European-wide rail travel is promoting the need for the harmonization of the systems that control the trains as they cross international borders. To meet new technical standards, SKF has developed SKF Axletronic odometers that fulfil the requirements of the European EN standards.
The signals from the odometer’s sensors are compatible with the electronic control units and European Train Control System (ETCS) produced by the main electronic system suppliers. The odometers offer an easy and maintenance-free solution for original equipment manufacturers and aftermarket customers wishing to upgrade trains currently in commercial service.
Today, high-speed trains, cruising at 300 km/h have changed Europe’s geography, and distances between large cities are no longer counted in kilometres but rather in TGV, ICE, Eurostar, Talgo or other train hours. The dark clouds of global warming threatening our planet are seen as rays of sunshine to this most sustainable transport medium, with other continents and countries following the growth path initiated by Europe and Japan. High-speed rail represents the solution to sustainable mobility needs and symbolizes the future of the passenger transport business.
Harmonization in rail control
The need and support for harmonization in rail control systems is highlighted by the fact that there are 20 signalling and speed-control systems installed throughout Europe. These systems were historically developed on a national basis without considering common international technical and operational standards. Typically, these developments were mainly driven by national operators in cooperation with the national rail industry. The European THALYS high-speed train linking Paris and Brussels must be equipped with seven different signalling and speed control systems. This results in enormous costs for equipment investment and maintenance, combined with an increased risk of breakdown and the challenges of complex operation, including driver training and workload. With several different systems on board and the need for tailor-made design for each specific route, it increases the cost for each high-speed train set of the Paris – Brussels – Köln / Amsterdam line by around 60 %. The driver’s cab has to be equipped with the different signalling systems plus a dedicated screen for operation on specific lines. These technical barriers have been a bottleneck for international rail interoperability.
This situation is changing as Europe moves towards greater rail integration. The international rail transport industry is implementing a new common system. Similar efforts have already started in other countries, including China, India, Japan and Korea.
The European Rail Traffic Management System
Traffic management systems make sure that trains run safely and efficiently on the right tracks, observe the appropriate speeds and avoid collisions with other trains. The European Rail Traffic Management System (ERTMS) currently features two basic functions, communications and control:
-
The communications function, GSM-R is based on the GSM standard but uses different frequencies and offers certain advanced functions. It is a radio system used to exchange voice and data information between trackside and on board.
-
The European Train Control System (ETCS) is basically a train-based computer, the Eurocab, which compares the speed of the train as transmitted from the track with the maximum permitted speed and slows down the train automatically if the latter is exceeded.
With ETCS, a track-mounted device called Eurobalise sends information to the train, enabling it to calculate continuously its maximum permitted speed. On lines where there is trackside signalling (lights and traffic signs enabling the driver to know the permitted speed), this information can be forwarded by standard beacons (light signals) located along the track and connected to the Eurobalises. This is ETCS level 1.
For ETCS level 2, information can also be forwarded by radio (GSM-R), and longer trackside signals are no longer required. This enables substantial savings in investment and in maintenance. The position of trains is still detected by trackside systems.
For ETCS level 3, the train itself sends its rear-end location, making it possible to optimize line capacity and further reduce the trackside equipment. For all levels of ETCS, the train-based Eurocab computer compares the speed of the train with the max-imum permitted speed and slows down the train automatically when required.
A Technical Specification for Interoperability (TSI) has been drawn up by the European Association for Railway Interoperability to support the implementation of European harmonization. The TSI has emerged following consultations with operators, system and subsystem manufacturers who are in favour of ERTMS introduction. Now ERTMS will be compulsory in Europe for any new installation or renewal of signalling for a number of rail corridors. The ETCS also meets the requirements of other national automatic train-protection systems such as the Italian SCMT (Sistema controllo movimentazione treno) and Spanish ASFAD (Aviso de Señales y Frenado Automatico).
SKF Axletronic odometers
An increasing number of new railway vehicles use odometers, devices that indicate the distance travelled. Odometers are also useful for the ETCS. New and existing vehicles could be easily upgraded with SKF Axletronic odometers. The SKF odometer solution has already been used successfully for Alstom and Ansaldo trains.
The SKF Axletronic railway sensor solution is a flexible platform for railway axleboxes with options to detect speed, temperature, vibration, sense of rotation and distance travelled. These signals can be used for:
-
odometry systems such as the ETCS
-
rotational speed for the wheel slip/slide protection and traction control unit
-
bearing temperature signal for the on-board monitoring system
-
direction of movement
-
vertical and/or lateral acceleration for monitoring systems.
In principle, there are two SKF Axletronic odometer conse bild urations available to the railway industry, depending on where the sensor is located. These are:
-
sensor installed onto the bearing seal as integral part of the axlebox bearing unit
-
sensor installed onto the axlebox front cover without interfering with the axlebox bearing unit.
SKF Axletronic odometer for bearing units
In this case, the pre-lubricated and sealed bearing units can be based on both tapered and cylindrical roller bearing designs, having integrated sensors. The bearing unit’s seals accommodate the odometer sensors. This is a smart and easy solution that saves space and parts.
SKF Axletronic odometer for axlebox front cover
In some cases, customers require unmodified bearing units. Here, SKF Axletronic odometers are offered for integration with the axlebox front cover. This solution is especially valuable for upgrading existing rolling stock as well as supporting original equipment manufacturers for the addition of the odometer function without needing to implement major design changes. The odometer sensor is placed on the axlebox front cover and can be used with any type axlebox bearing using a sensor mounting plate and a tooth end cup.
SKF Axletronic odometer advantages
With the SKF solution, a redundant and independent system can be achieved through several independent odometer sensor conse bild urations. A further advantage of this integrated odometer is that the original axle design can be used without any redesign.
-
The SKF Axletronic odometer is a flexible, modular solution that can be tailored to individual customer requirements. The installation is a plug-and-play solution, requiring no adjustment or calibration.
-
The SKF Axletronic odometer is a contact-less design without any components that may be subject to wear. A functional signal control can be done without moving the train or the wheel set. No further maintenance is needed.
-
The main advantage is the “free axle end.” This is in contrast to conventional odom-eters that are designed to be installed at the end of the front cover with mechan-ical connection to the rotating wheel set through an additional small shaft that must be supported by bearing and sealing components. These designs need more space and block the interface for earth-return devices that are compulsory for most rolling stock axleboxes to avoid the current flow through the bearing.
SKF Axletronic is a trademark of the SKF Group.