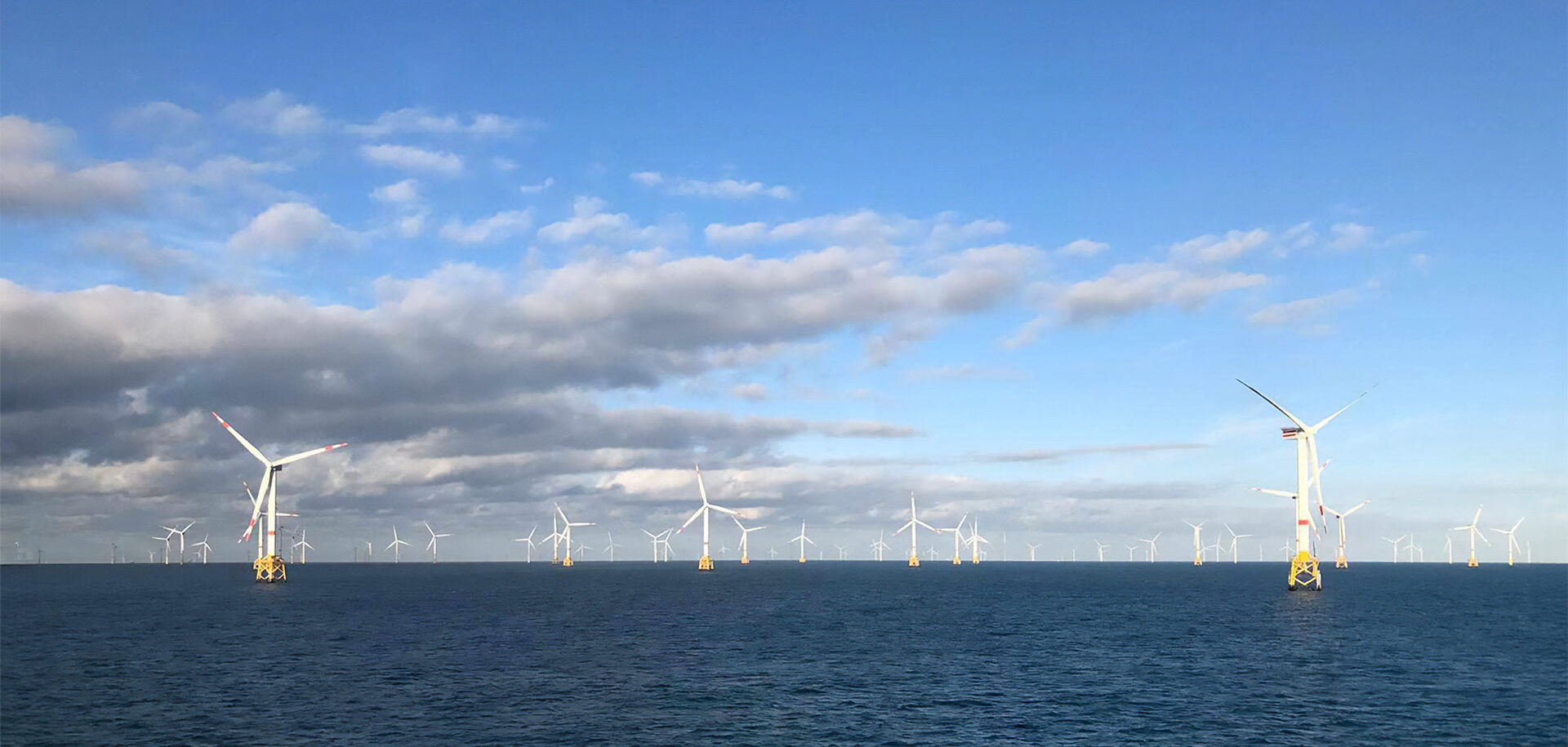
Zusammenarbeit hält alternden Windpark in Topform
Einer der ersten europäischen Offshore-Windparks ist ein wenig in die Jahre gekommen. Aber mit innovativen Service- und Supportlösungen von SKF drehen die Windräder sich weiterhin reibungslos.
Auf der Sandbank Thornton etwa 30 km vor der belgischen Küste drehen sich 54 Windturbinen im Nordseewind. Der 325-MW-Windpark von C-Power ist in dem Gebiet eine von neun Offshore-Anlagen für erneuerbare Energie mit einer Gesamtkapazität von 2,2 GW. Weitere drei Gigawatt befinden sich in Entwicklung.
Die erste Etappe des C-Power-Windparks mit sechs Windturbinen war 2009 Belgiens erstes kommerzielles Offshore-Projekt zur Erzeugung von erneuerbarer Energie. Der Windpark ist in zwei Felder aufgeteilt; zwischen ihnen verlaufen eine Gaspipeline und ein Seekabel. Obgleich die 5- und 6-MW-Turbinen des Windparks nur halb so groß sind wie die größten Modelle von heute, gelten sie immer noch als technische Meisterwerke. Drei Rotorblätter mit einer Länge von 61,5 Metern drehen sich auf einer Nabe in circa 95 Metern Höhe über dem Meeresspiegel. Die Höhe ergibt sich daraus, dass ein 68 Meter hoher Stahlturm auf einem 45 Meter hohen Fundament montiert ist. Während für die ersten Turbinen des Windparks noch massive Betonfundamente mit einem Gewicht von bis zu 3.000 Tonnen verwendet wurden, stehen heute die meisten auf leichteren Stahlgitterkonstruktionen, die auf vier im Meeresboden verankerten Pfählen mit jeweils zwei Metern Durchmesser ruhen.
Auf jedem Turm befindet sich eine 320 Tonnen schwere Gondel, in der Rotorlager, Getriebe, Azimutsystem und Umrichter der Turbine untergebracht sind. C-Power beschreibt seine Turbinen sowie das separate Offshore-Umspannwerk des Windparks als „55 Fabriken, die Wartung und Instandhaltung benötigen“.
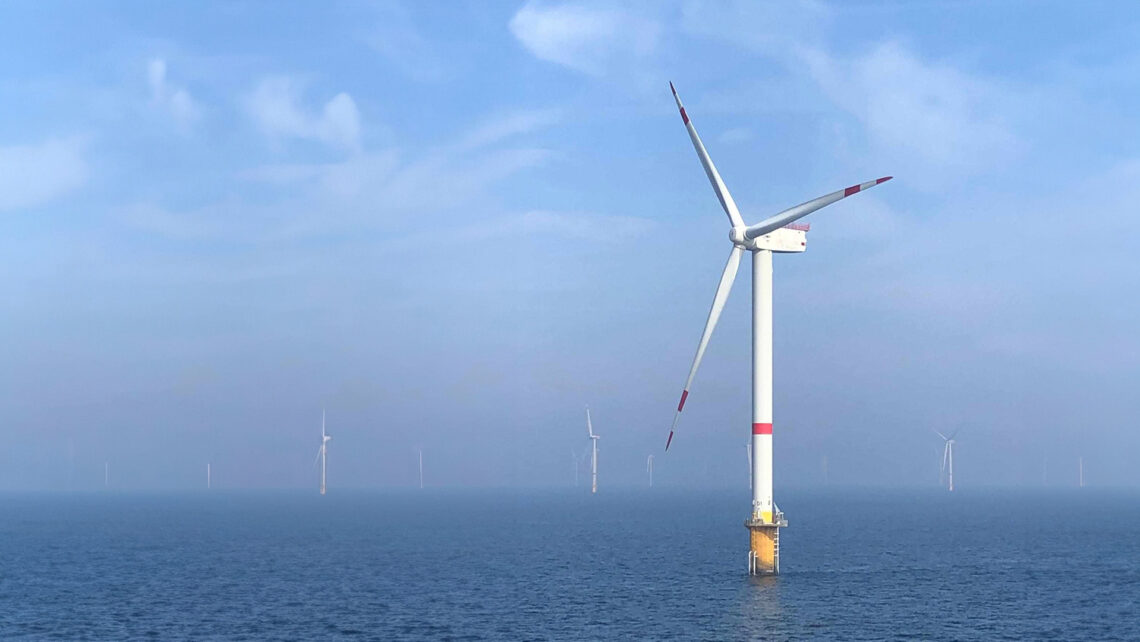
Ein Vollzeit-Job
Die ältesten Turbinen von C-power sind seit 14 Jahren im rauen Nordseeklima in Betrieb. Das ist etwas mehr als die Hälfte ihrer errechneten Lebensdauer von 25 Jahren. Auch die jüngsten Turbinen sind über zehn Jahre alt.
Turbinen mittleren Alters brauchen besondere Pflege und Instandhaltung, damit sie in Topform bleiben. C-Power führt den gesamten Betrieb sowie alle Wartungs- und Instandhaltungsmaßnahmen in eigener Regie durch. Das ist bei Offshore-Windkraftanlagen ungewöhnlich.
Das ganze Jahr über fahren Wartungsteams fast jeden Morgen mit dem Schiff von Ostende zu den Turbinen, um dort Arbeiten auszuführen. Grundlage ihres Instandhaltungsplans ist ein umfassendes Programm von jährlichen und halbjährlichen vorbeugenden Wartungsmaßnahmen. Der zeitliche Aufwand dabei beträgt für jede Turbine durchschnittlich 11 Tage pro Jahr. Darüber hinaus werden Wartungsteams zur Behebung von Störungen sowie zur Durchführung anfallender Reparaturen gerufen.
Die Wartungsschiffe fahren abends wieder zurück, aber C-Power kontrolliert seine Anlagen über eine Fernüberwachungsstation im Hafen von Ostende rund um die Uhr. Falls die Wetterverhältnisse zu schlecht sein sollten, um auf dem Seeweg zu den Turbinen zu gelangen, kann das Wartungsteam jede Turbine zudem über eine Helikopter-Abseilplattform erreichen, um notwendige Reparaturen durchzuführen.
Im Rahmen einer mehrjährigen Partnerschaft erhält C-Power bei der Wartung und Instandhaltung der Turbinen Unterstützung von SKF. Es besteht eine enge Zusammenarbeit bei der Verbesserung der Zuverlässigkeit der Turbinen und der Entwicklung innovativer Lösungen für den Offshore-Energiesektor. Bei wöchentlichen Statusmeetings mit Teams beider Unternehmen wird der Stand laufender Projekte besprochen und eruiert, wo sich neue Zusammenarbeitsmöglichkeiten ergeben könnten.
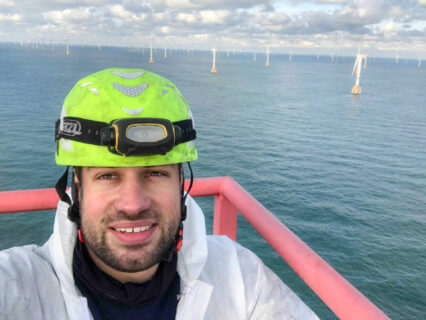
Wir nutzen Zustandsüberwachungstechnologie, um den Status unserer Turbinen zu ermitteln
Bryan Uyttersprot, Wartungs- und Kontrollraumingenieur bei C-Power
Ferngesteuert
Alle fünf Wochen überprüft der Wartungsingenieur Bryan Uyttersprot als zuständiger Techniker den Kontrollraum des C-Power-Windparks. In seiner übrigen Zeit ist er für eine Vielzahl von Reparaturmaßnahmen und Projekten zur Verbesserung der Zuverlässigkeit verantwortlich. „Manchmal fahre ich mit und arbeite zusammen mit unseren Wartungsteams an den Turbinen, vor allem wenn irgendwo eine neue Lösung getestet wird“, sagt er. „Die meiste Zeit verbringe ich jedoch im Büro und arbeite an langfristigen Projekten.“
Solche Kontroll-Intervalle sind ein gutes Beispiel für die enge Beziehung zwischen SKF und C-Power. „Wir nutzen Zustandsüberwachungstechnologie, um den Status unserer Turbinen zu ermitteln“, fährt Uyttersprot fort. „Ihre Generatorlager und Getriebe sind mit 14 Schwingungssensoren ausgestattet, und weitere Sensoren sind in den Hauptlagern der Rotorwelle installiert.“
Die Daten der Sensoren werden mithilfe der Zustandsüberwachungstechnik SKF Multilog IMX erfasst und über eine sichere Datenverbindung an das Remote Diagnostics Service Center (RDC) von SKF in Hamburg übertragen. Dort analysieren SKF Spezialisten für Zustandsüberwachung in der Windenergiebranche das Schwingungsspektrum und suchen nach ersten Anzeichen von Problemen an wesentlichen Bauteilen.
„Ich arbeite mit den Ingenieuren im RDC eng zusammen“, erklärt Uyttersprot. „Ihre Analysen zeigen uns, ob wir es mit einer Schwachstelle wie etwa einem defekten Lagerring oder beschädigten Wälzkörpern zu tun haben.“ Auf der Grundlage der Berichte von SKF entscheidet Uyttersprot dann, welche Maßnahmen zu ergreifen sind, damit die Turbine ihren Betrieb wieder vollumfänglich aufnehmen kann.
„Probleme mit einem Lager im Generator oder im Getriebe sind einfach zu beheben, obwohl der Austausch von einem Spezialistenteam vorgenommen werden muss“, so Uyttersprot. Die Gondeln der Windturbinen sind jeweils mit einem Hydraulikkran ausgestattet, den die Techniker nutzen können, um die schweren Bauteile sicher zu bewegen.
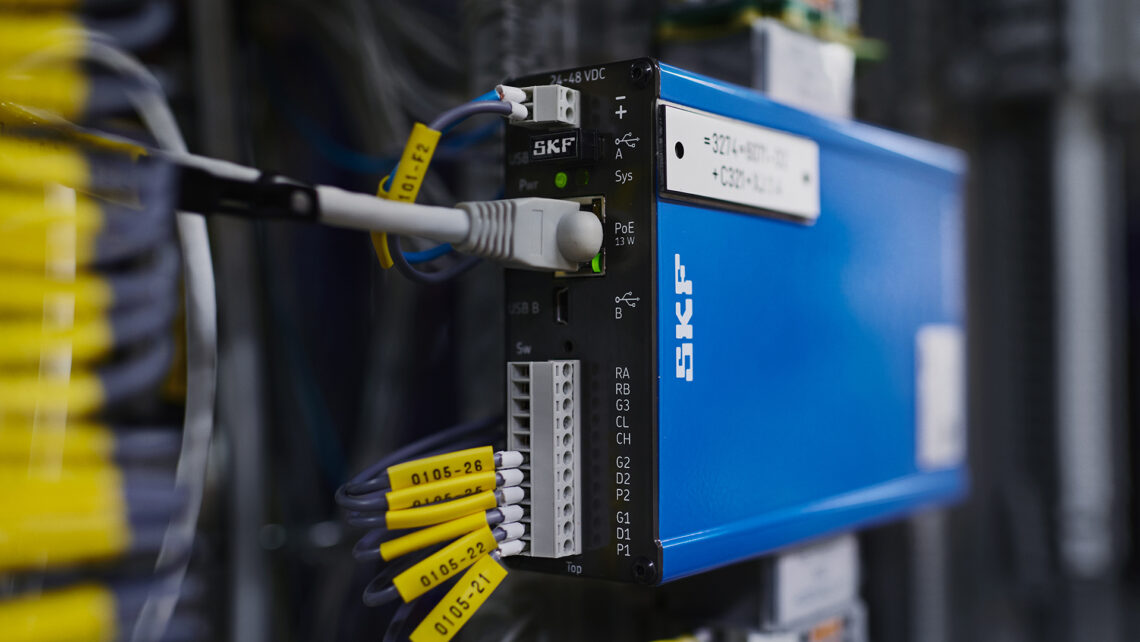
Schwere Lasten
Probleme an den Hauptrotorlagern sind dagegen wesentlich komplizierter. „Hierfür müssen wir die komplette Hauptwelle ausbauen, die rund 70 Tonnen wiegt“, erläutert Uyttersprot. „Um aber an dieses Bauteil heranzukommen, müssen die Rotoren und die Nabe, mit einem Gewicht von insgesamt 130 Tonnen, abmontiert werden.“ Für diese Arbeiten braucht man ganz spezielle Schwerlast-Hebezeuge. Ausgeführt werden sie mit einem Hubschiff, das mit einem Schwerlastkran und Stützbeinen ausgerüstet ist, die als zusätzliche Stütze auf den Meeresboden abgelassen werden. Abgenutzte oder beschädigte Rotorwellenbaugruppen werden zur Reparatur und Überholung an SKF geschickt.
Aufgrund der hohen Kosten und der Komplexität solcher Reparaturarbeiten an Hauptwellenlagern ist die Zuverlässigkeit dieser Komponenten für alle Windparkbetreiber von äußerster Wichtigkeit. Dieses Thema steht bei SKF und C-Power seit langem im Fokus. „Im Laufe der Jahre haben wir zahlreiche Veränderungen vorgenommen“, sagt Uyttersprot. „Wir haben das Schmierfett in diesen Lagern gewechselt, um die Schmierleistung zu verbessern, und sind inzwischen auf neue Lagereigenschaften umgestiegen, die eine längere Gebrauchsdauer gewährleisten.“
An einigen Turbinen führen SKF und C-power zurzeit eine mehrjährige Versuchsreihe mit einer neuartigen Zustandsüberwachungstechnologie durch. „Wir haben einige unserer Turbinen mit Hauptlagern ausgerüstet, in deren Wälzkörper Sensoren eingebaut sind“, erklärt Uyttersprot. „Damit können wir die Lasten im Inneren der Lager messen und beobachten, wie sie bei unterschiedlichen Betriebsbedingungen und in den jeweiligen Positionen in ihrem Umlauf schwanken.“ Die Datenerfassung an den sensorbestückten Lagern ist noch nicht abgeschlossen, aber Uyttersprot hofft, dass die Erkenntnisse aus der Versuchsreihe am Ende weitere Verbesserungen der Zuverlässigkeit von kritischen Komponenten ermöglichen werden.
In der Zwischenzeit erleichtern andere SKF Innovationen bereits die Arbeit der C-Power-Wartungsteams. Ein Beispiel dafür ist eine neue Spaltdichtung (geteilte Dichtung – split seal) für Hauptrotorlager. Die für den belgischen Pionier im Bereich der erneuerbaren Energie entwickelte Konstruktion ist nicht nur eine robustere Lösung, sondern sie verkürzt auch die Montagezeit.
Leistungsstarke Produktion
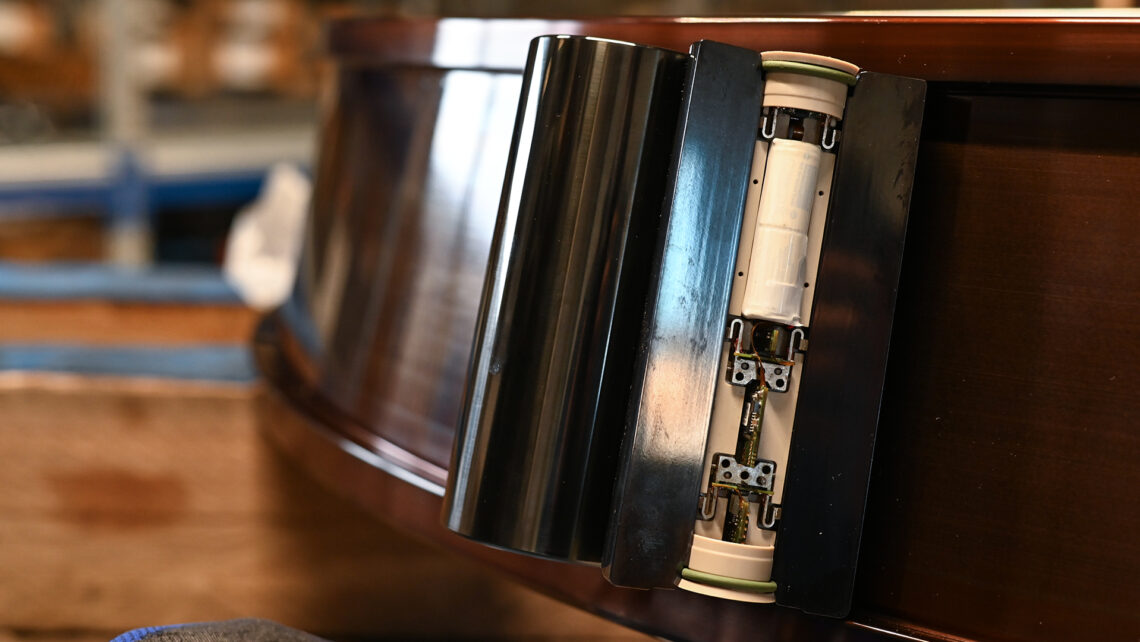