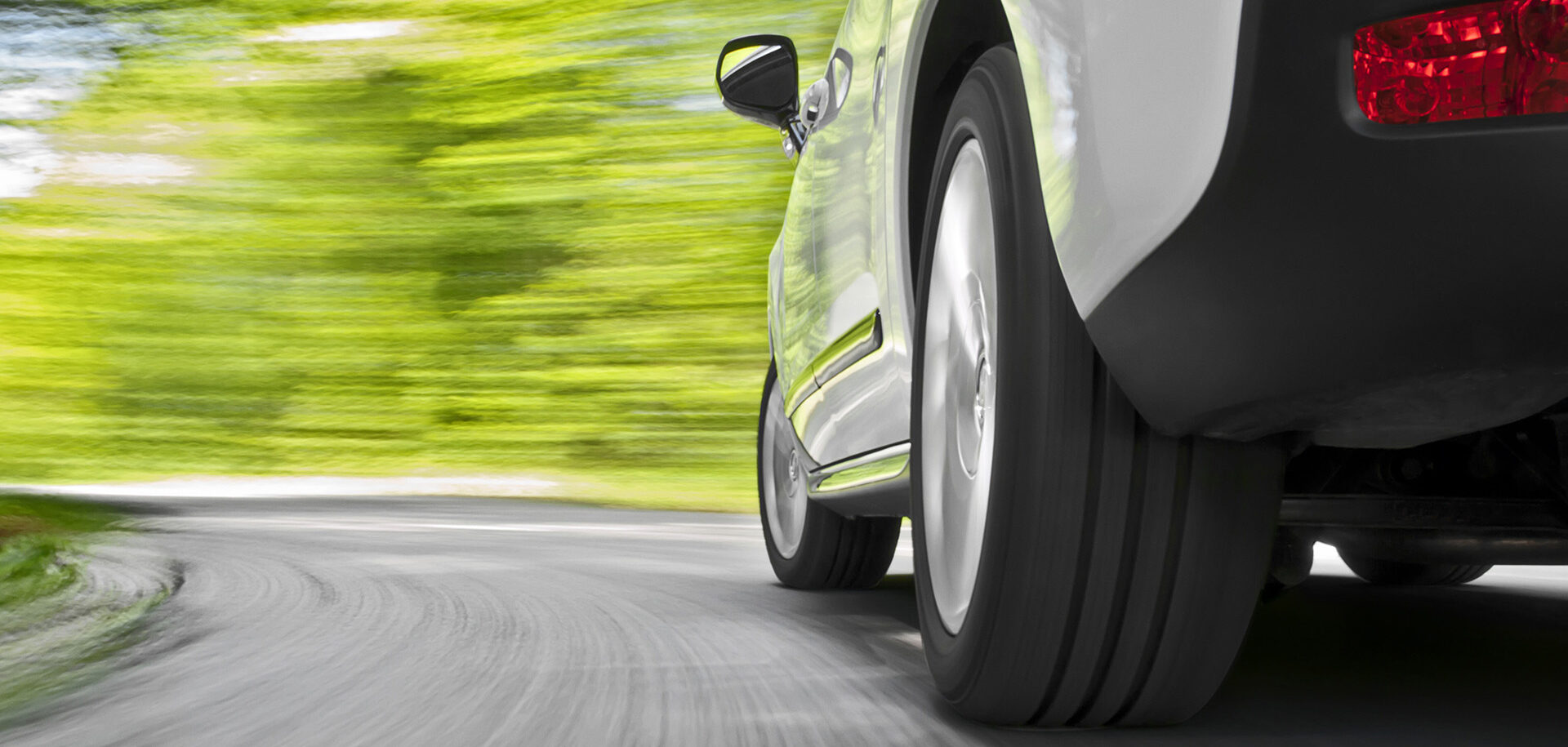
Leistungsfähige Dichtungen für mehr Nachhaltigkeit
Eine der Herausforderungen bei der Konstruktion von Dichtungen besteht darin, die Reibung so gering wie möglich zu halten und gleichzeitig sicherzustellen, dass der Schmierstoff in der Dichtung verbleibt und Verunreinigungen nicht eindringen können. Eine Reduzierung des Reibmoments mithilfe der SKF Virtual Seal Plattform trägt zur Senkung des Energieverbrauchs und der CO2-Emissionen bei.
Dichtungen tragen erheblich zur Reibung in rotierenden Maschinen bei – in einigen Anwendungen bis zu 60 % des gesamten Reibmoments. Seit einigen Jahren ist der Stromverbrauch in allen Anwendungen und Branchen weltweit rückläufig, und es wird erwartet, dass dieser globale Trend noch viele Jahre anhalten wird. Die Reduzierung des Reibmoments von Dichtungen ist daher eine der wichtigsten Kundenanforderungen, um die Systemeffizienz zu verbessern, den Energieverbrauch zu senken und die Kohlenstoffemissionen insgesamt zu verringern.
Die größte Herausforderung bei der Konstruktion einer optimalen Dichtung besteht darin, die Reibung so gering wie möglich zu halten und gleichzeitig sicherzustellen, dass der Schmierstoff in der Dichtung verbleibt und keine Verunreinigungen in das System gelangen. Aufgrund der strengeren CO2-Vorschriften wird zunehmend gefordert, die Reibung der vorgeschlagenen Dichtungslösung während des Betriebs weiter zu reduzieren.
Dieser Artikel behandelt hauptsächlich die Reibungsverluste des verwendeten Dichtungssystems, die indirekt in eine nachgelagerte Kategorie von Scope 3 des GHG Protocol (Greenhouse Gas Protocol) fallen, nämlich in die Unterkategorie „Verwendung gekaufter Produkte“.
Bei den meisten SKF Anwendungen entfällt der größte Anteil der gesamten CO2-Emissionen unserer Wälzlagerprodukte auf Reibungsverluste, die in eine nachgelagerte Kategorie von Scope 3 fallen, wie dieser Link zeigt.
Intelligente Kombination von Simulationsprogrammen
Für eine genaue Vorausberechnung des Reib- und Temperaturverhaltens von Dichtungen ist eine Kombination aus erweiterten Material-, Tribologie-, Schmier- und Wärmeableitungsmodellen erforderlich. Das SKF Seals Global Research and Innovation Team hat eine technisch anspruchsvolle Simulationsplattform – SKF Virtual Seal (SAMBA) – entwickelt, die den Abaqus FEA(Finite-Elemente-Analyse)-Solver mit den firmeneigenen analytischen Modellgleichungen von SKF Seals kombiniert und so die Vorausberechnung der Reibungswärmeerzeugung einer Dichtung und der thermischen Entwicklung des Systems ermöglicht (Bild 1).
SKF hat einen CO2-Emissionsrechner entwickelt, der in Verbindung mit den von SKF Virtual Seal berechneten Reibmoment- und Temperaturwerten zeigt, wie nachhaltigere Dichtungslösungen mit modernen Simulationsplattformen virtuell entstehen können.
SKF Virtual Seal – Ein komplexer multiphysikalischer Ansatz
Die transiente Temperaturentwicklung in einem Dichtungssystem stabilisiert sich, wenn ein Gleichgewicht zwischen der durch das Reibmoment der Dichtung erzeugten Wärmemenge und der an die Umgebung des Dichtungssystems abgegebenen Wärmemenge besteht. Daher ist es für eine realistische Vorausberechnung sehr wichtig, sowohl die Reibungswärmeerzeugung als auch die Wärmeableitung zu berücksichtigen. Bei der Vorausberechnung des Dichtungsreibmoments sind mehr als hundert Variablen voneinander abhängig, was die Vorausberechnungsmodellierung noch komplexer macht. Durch die Integration der SKF Virtual Seal Modellierungsgleichungen in ein FEA(Finite-Elemente-Analyse)-Paket können alle voneinander abhängigen Variablen in jedem Zeitschritt der Simulation konsolidiert werden.
Sowohl bei der Implementierung der erforderlichen komplexen Modelle als auch bei deren Interaktion mit dem FEA-Solver werden verschiedene nicht standardisierte numerische Verfahren eingesetzt, die über erweiterte Funktionen verfügen müssen. Um den Einsatz und die Nutzung der SKF Virtual Seal Plattform zu erleichtern und zu beschleunigen, wurde eine Benutzerschnittstelle entwickelt. Ihre Aufgabe ist es, dem Benutzer die einfache Eingabe von anwendungsspezifischen Parametern zu ermöglichen.
Nachdem alle Eingaben über die Benutzerschnittstelle erfolgt sind, modifiziert ein Python-Skript das Standard-FEA-Modell und verknüpft alle Parameter mit einer vorkompilierten Routine, in der die analytischen Gleichungen programmiert sind. Dadurch wird im Hintergrund automatisch die bidirektionale Kopplung zwischen dem FEA-Solver und den analytischen Gleichungen von SKF Virtual Seal erzeugt. Der nächste Schritt des Konstrukteurs besteht dann darin, wie gewohnt eine Simulation mit der FEA-Software durchzuführen, mit dem Unterschied, dass ein nun verbesserter semianalytischer Solver während der Simulation unbemerkt im Hintergrund läuft.
Experimentelle Validierung
Auf dem Weg zu nachhaltiger Leistung
Die von SKF Virtual Seal vorausberechnete Reibung kann mithilfe des SKF Nachhaltigkeitstools, dem CO2-Emissionsrechner, in einen CO2-Emissionswert umgerechnet werden, so dass ein virtuelles Verfahren zur Auswahl der am besten geeigneten Dichtung auf Basis eines konkreten Nachhaltigkeitskriteriums zur Verfügung steht. Anschließend werden die durch Reibungsverluste verursachten Emissionen auf der Grundlage der regionalen CO2-Emissionen pro kWh Energie für den ausgewählten geografischen Standort berechnet.
Der Nutzen eines solchen Tools besteht darin, dass es Prognosen liefert und einen weiteren Schritt auf dem Weg zur Schaffung eines Bewusstseins darstellt, das auf einem konkreten Verfahren zur Messung der Auswirkungen unserer Produkte beruht.
Von der Theorie zur Praxis
Um das Potenzial der virtuellen Vorausberechnung von CO2-Emissionen in frühen Entwicklungsphasen zu verdeutlichen, werden im Folgenden zwei Beispiele aus der Automobil- und Schienenfahrzeugindustrie näher betrachtet.
Radlagerdichtungen in der Automobilindustrie
In diesem ersten Beispiel ist ein Automobilhersteller auf der Suche nach einer neuen Kassettendichtung für eine SKF Radlagereinheit (HBU) mit geringerer Reibung. Ziel ist eine Reibungsreduzierung um 20 % gegenüber der Vorgängergeneration von HBU-Kassettendichtungen.
Die Simulationsergebnisse von SKF Virtual Seal zeigen, dass ein optimiertes Dichtungsfett die Reibung um 28 % verringern kann:
- 0,33 N.m bei der Lösung mit dem ursprünglichen Fett (Fett A)
- 0,24 N.m bei der Lösung mit dem neuen reibungsarmen Fett (Fett B)
Diese Lösung übertrifft sogar die vom Kunden gewünschte Reibungsreduzierung. Darüber hinaus bestätigen die Ergebnisse der Produktvalidierungstests die SKF Virtual Seal Berechnungen (siehe Bild 3).
Vom Reibmoment zum CO2-Ausstoß
Durch Eingabe der Reibmomentwerte in den SKF CO2-Emissionsrechner können die Auswirkungen der Leistungsverbesserungen unserer neuen HBU-Dichtungslösung auf die nachgelagerten Produktemissionen von Scope 3 bewertet werden. Das firmeneigene Nachhaltigkeitstool rechnet die Reibungsverluste der Dichtung in zu erwartende CO2-Emissionen um. Der daraus resultierende Vergleich zwischen der neu entwickelten HBU-Kassettendichtungslösung mit optimiertem Fett und der bestehenden Lösung für Pkw-Radlagerdichtungen ist in Bild 4 dargestellt.
Radsatzlager in der Schienenfahrzeugindustrie
Das zweite Praxisbeispiel betrifft ein neues Partnerschaftsprogramm zwischen einem Schienenfahrzeughersteller und SKF zur Entwicklung eines neuartigen Lagersystems für eine neue Generation von Regionalzügen in einer europäischen Großstadt. Ziel für die neue Radsatzlagereinheit (TBU) ist eine Reibungsreduzierung um 30 % gegenüber der Vorgängergeneration.
Wie im zuvor beschriebenen Beispiel aus der Automobilindustrie wurde die neue TBU-Dichtung mithilfe der SKF Virtual Seal Plattform optimiert und weist eine prognostizierte Reibungsreduzierung von 44 % auf:
- 0,77 N.m bei der ursprünglichen Lösung
- 0,43 N.m bei der optimierten Lösung.
Wie in Bild 5 dargestellt, stimmen die Ergebnisse der Produktvalidierungstests wiederum mit den SKF Virtual Seal Modellierungsberechnungen überein.
Vom Reibmoment zum CO2-Ausstoß
In ähnlicher Weise rechnet das firmeneigene Nachhaltigkeitstool die Reibungsverluste der TBU-Dichtung in zu erwartende CO2-Emissionen um. Der daraus resultierende Vergleich zwischen der neu entwickelten TBU-Dichtungslösung und der ursprünglichen Lösung ist in Bild 6 dargestellt.
Fazit
Die unbestreitbare Notwendigkeit, dass etwas gegen den Klimawandel unternommen werden muss, rückt das Thema Nachhaltigkeit immer mehr in den Fokus. Daher ist es sehr wichtig, mit allen Beteiligten entlang der ganzen Wertschöpfungskette wie Lieferanten, Herstellern und Kunden über die Umwelteinflüsse unserer Produkte zu sprechen und sie dafür zu sensibilisieren.
Ökologische Nachhaltigkeit, wie sie in Scope 3 des GHG Protocol (Greenhouse Gas Protocol) definiert ist, ist sehr weit gefasst. Die Beispiele in diesem Artikel veranschaulichen eine von vielen notwendigen Maßnahmen, die SKF ergreift, um die Umweltbelastung durch Produkte mit geringeren CO2-Emissionen zu reduzieren und gleichzeitig wettbewerbsfähig zu bleiben.
Teil dieser Bemühungen ist die Entwicklung von webbasierten Berechnungsprogrammen wie dem SKF Nachhaltigkeitstool CO2-Rechner und fortschrittlichen Modellierungsplattformen wie SKF Virtual Seal, um die Umweltauswirkungen von Produkten bereits in der frühen Konstruktions- und Produktauswahlphase und darüber hinaus bewerten zu können und so den Weg für umweltfreundlichere Verfahren zu bereiten.