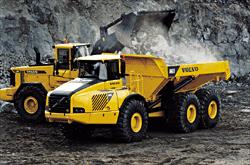
Erdbewegungen
Volvos knickgelenkter Dumper A40D transportiert Steine und Kies und ist mit seiner Nutzlast von 37 Tonnen ein Koloss, von dem allerdings ein minimaler Wartungsaufwand verlangt wirdErst wenn man die Stufen zu dem gelb-grauen Fahrerhaus des Volvo-Dumpers A40D hinaufklettert, begreift man seine gigantischen Abmessungen. Allein die Räder mit einem Gewicht von jeweils 900 Kilogramm sind größer als ein erwachsener Mann von durchschnittlicher Größe. Das Dach des Fahrerhauses befindet sich fast vier Meter über dem Boden. Die Nutzlast beträgt 37 Tonnen. Unter der Motorhaube verbirgt sich ein Sechszylinder-Motor mit Turbolader und einer Leistung von 420 PS.
Volvos knickgelenkter Dumper A40D transportiert Steine und Kies und ist mit seiner Nutzlast von 37 Tonnen ein Koloss, von dem allerdings ein minimaler Wartungsaufwand verlangt wirdErst wenn man die Stufen zu dem gelb-grauen Fahrerhaus des Volvo-Dumpers A40D hinaufklettert, begreift man seine gigantischen Abmessungen. Allein die Räder mit einem Gewicht von jeweils 900 Kilogramm sind größer als ein erwachsener Mann von durchschnittlicher Größe. Das Dach des Fahrerhauses befindet sich fast vier Meter über dem Boden. Die Nutzlast beträgt 37 Tonnen. Unter der Motorhaube verbirgt sich ein Sechszylinder-Motor mit Turbolader und einer Leistung von 420 PS.
Der speziell für extrem unwirtliches Gelände ausgelegte A40D-Dumper – oder Kipper – mit Knicklenkung ist das größte von fünf Dumper-Modellen, die von Volvo Articulated Haulers in Braås nahe der schwedischen Stadt Växjö gebaut werden. Die Fahrzeuge mit Nutzlasten von 20 bis 37 Tonnen werden hauptsächlich für Straßen-, Brücken- und Dammbauprojekte eingesetzt, um Steine, Kies, Sand und Erde in großen Mengen zu transportieren. Darüber hinaus werden sie in der Bergbauindustrie gebraucht.
Schwere Einsatzfälle
Ein Dumper mit Knicklenkung kann nicht nur dreimal höhere Nutzlasten befördern als ein herkömmlicher Kipper, er ist auch beweglicher und für schwere Einsatzfälle besser ausgerüstet. Volvos Dumper-Modelle haben eine Dreipunktaufhängung, so dass sich die Achsen unabhängig voneinander bewegen können. Eine Anhängekupplung, die beweglich gekoppelt werden kann, verbindet den vorderen mit dem hinteren Teil des Fahrzeugs und ermöglicht Seitenbewegungen von bis zu 180° sowie einen großen Spielraum an vertikalen Bewegungen. Das bedeutet, dass der Dumper praktisch überall durchkommt, ohne steckenzubleiben oder umzukippen.
Gösta Svensson, Leiter der Produktplanung und Transporttechnik bei Volvo Articulated Haulers, beschreibt schwere Dumper als die flexibelsten und kostengünstigsten Transporter für große Massen.
„Knickdumper können vieles, was LKW oder Starrkipper [ein anderer Typ von Transportfahrzeug] nicht können“, sagt er. So entdeckte zum Beispiel Indonesien kürzlich die Vorteile von Volvos Dumper-Modellen, nachdem die Kunden dort eingesehen hatten, dass nur diese Fahrzeuge in der Lage waren, schwere Lasten während der Regenzeit in unwirtlichem Gelände zu transportieren.
Volvo ist mit einem Anteil von über 50 Prozent des globalen Marktes in dieser Sparte Weltmarktführer. Von Volvo stammt auch der erste knickgelenkte Kipper aus den fünfziger Jahren. „Wir waren der erste Fahrzeughersteller, der ein Knicklenkungssystem auf den Markt brachte“, erinnert sich Svensson. „Unser erster Kipper hieß Moonrocket, und der erste seriengefertigte Transporter dieses Typs, den wir Gravel Charlie nannten, kam 1966 auf den Markt.“
Gesunde Umsätze
Danach hat Volvo noch fünf weitere Dumper-Generationen gebaut. Die neusten Modelle tragen die Bezeichnung A40D und A35D. Da der Markt für diese Nutzfahrzeuge kontinuierlich wächst, sieht Volvo ein gutes Potenzial für langfristige gesunde Absatzsteigerungen, denn immerhin exportiert der schwedische Fahrzeughersteller seine Dumper in 60 Länder. „Es gibt immer noch viele Länder, in denen das Dumper-Konzept nicht sehr bekannt ist. Dort verlässt man sich auf LKW und Kratzbagger“, erklärt der Produktspezialist Pär-Olof Gåård von Volvo Articulated Haulers.
Das Absatzvolumen an Dumpern hat sich in den letzten zehn Jahren weltweit verdoppelt. Dennoch ist dieser Fahrzeugtyp nach wie vor ein Nischenprodukt – angesichts des Preises von bis zu 400.000 US-Dollar (440.000 Euro) für das größte Modell vielleicht nicht so erstaunlich. Volvo verkauft im Schnitt rund 2.000 schwere Dumper pro Jahr.
Auf den ersten Blick unterscheiden sich die heutigen Modelle nicht so radikal von denen der „Gravel Charlie“-Ära. Sie sind immer noch gelb und bestehen aus einem Fahrerhaus und einem Anhänger, der über eine Achse und eine Antriebswelle mit dem vorderen Teil des Fahrzeugs verbunden ist. Leistung und Fähigkeiten sind jedoch nicht mit den früheren Modellen zu vergleichen.
Die Nutzlast hat sich in den vergangenen drei Jahrzehnten nahezu verdreifacht. Während die Kipper der sechziger Jahre eine Höchstgeschwindigkeit von 30 Stundenkilometer erzielten, schaffen die heutigen schweren Dumper-Modelle 50 Stundenkilometer und sind mit Automatikgetriebe und Federung ausgestattet. Sie verfügen zudem über fünf Bordcomputer, die Volvo als „eingebaute Intelligenz“ bezeichnet. Sie steuern Fahrzeugfunktionen wie etwa die Kraftstoffeinspritzung, den Gangwechsel und die Serviceintervalle.
Die neuen A35D- und A40D-Modelle haben auch ein leicht verändertes, abgerundetes Design, was der Tatsache zu verdanken ist, dass die Motorhaube nun aus einem als Telene bezeichneten neuen Kunststoff gefertigt wird. Dieser Werkstoff ist leicht formbar und so robust, dass man „mit einem Vorschlaghammer draufschlagen kann, ohne dass es Dellen gibt“, sagt Gåård.
Mit dem neuen Fahrerhaus-Konzept wollte Volvo das Sichtfeld des Fahrers verbessern. Sicherheit gehört zu den zentralen Werten des Unternehmens. Die ergonomische Gestaltung und Luftqualität des Fahrerhauses bieten dem Fahrer einen so hohen Komfort, dass er problemlos acht Stunden oder manchmal auch länger die Maschine bedienen kann. „Einen Motor mit 1.000 PS oder mehr zu haben, nutzt nichts, wenn sich der Fahrer nicht wohl fühlt“, erklärt Svensson. „Wenn es dem Fahrer gut geht, steigert das die Produktivität.“
Das ausgeprägte Umweltbewusstsein des Unternehmens wird bei einem Besuch im Werk von Braås deutlich. Überall stehen Recyclingbehälter herum – für alles von Metallabfällen bis zu Karton- und Kunststoffabfällen. Selbst die kleinsten Metallspäne werden sorgfältig aufgesammelt und rückgewonnen. Lackiert werden die Fahrzeuge vollautomatisch von gigantischen Robotern, so dass dem Personal das ansonsten giftige Milieu einer Lackierwerkstatt erspart bleibt.
Lackabfälle werden in einem Katalysator verbrannt, der so gut wie keine Schadstoffemissionen verursacht. Auch die Fabrik insgesamt hat sehr niedrige Emissionswerte, wie der Leiter der Fertigungstechnik Jörgen Sjöstrand bestätigt. Das Werk ist nach dem internationalen Umweltmanagementstandard ISO 14001 sowie nach dem Qualitätsstandard ISO 9000 zertifiziert. Nach Aussage von Volvo entsprechen die Fahrzeuge den europäischen und amerikanischen Normen für den Schadstoffausstoß von Geländefahrzeugen und in manchen Fällen schneiden sie sogar noch besser ab.
Für den Bau eines typischen knickgelenkten Dumpers benötigt man 200 Personen. Die Komponenten werden zum größten Teil in Schweden gefertigt – einige von anderen Volvo-Unternehmen und einige von externen Herstellern.
Geringer Wartungsaufwand
Sjöstrand ist offensichtlich stolz auf die neuste Dumper-Generation, die derzeit in Braås sowie in den beiden anderen Werken von Volvo Articulated Hauler in North Carolina und Brasilien vom Band läuft. Volvo hat mit der D-Serie einen großen Schritt nach vorn getan, meint er. Die Kunden verlangten längere Serviceintervalle, und dieser Forderung hat man Rechnung getragen.
Die D-Serie ist mit wartungsfreien Lagern (siehe Kasten nebenan) bestückt, die den Wartungsbedarf erheblich verringert haben. Tägliche Inspektionen sind nicht mehr erforderlich, da der Bordcomputer im Fahrerhaus den Bediener über einen eventuellen Servicebedarf informiert. Der bedeutendste Aspekt für den Kunden ist vielleicht die Tatsache, dass bei der D-Serie die Ausfallzeiten auf Grund von täglichen und wöchentlichen Inspektionen von 33 Stunden, wie es beim Vorgänger-Modell üblich war, auf sieben reduziert werden konnten.
„Wenn die wartungsbedingte Ausfallzeit eines solchen Fahrzeugs nur um eine Stunde verringert werden kann, senkt das nicht nur die Kosten des Kunden, sondern steigert auch seine Erträge und seine Produktivität“, sagt Svensson.
Greg McIvor
Wirtschaftsjournalist in Stockholm