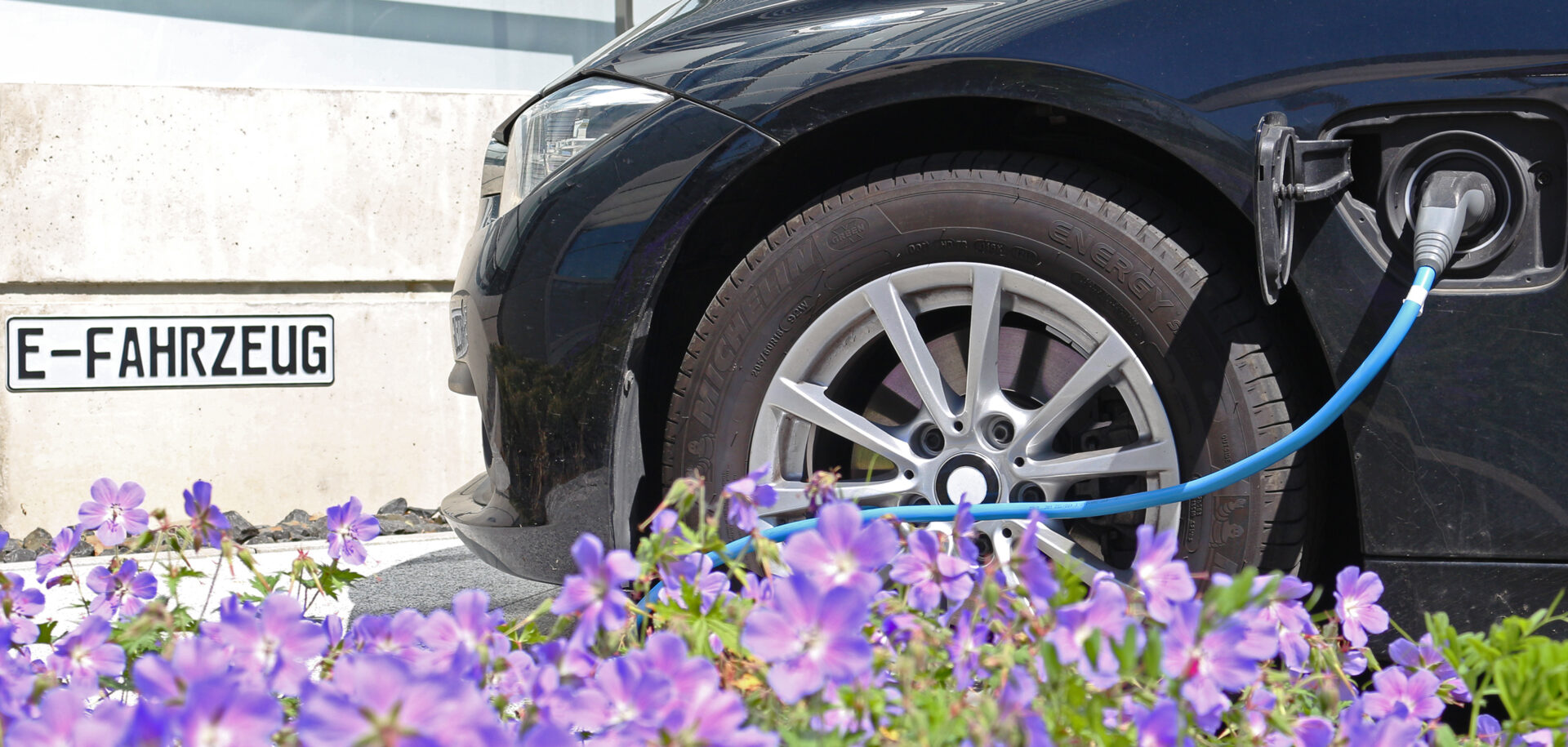
Schlüssel-Komponenten für Elektromobilität
Elektro- und Hybridfahrzeuge kommen immer mehr ins Rollen. Zwar dürften „herkömmliche“ Automobile den internationalen Markt noch eine Weile dominieren, doch werden immer schärfere Kohlendioxid- und Partikelemissions-Vorschriften zwangsläufig dazu führen, dass „alternative“ Antriebskonzepte an Bedeutung gewinnen. Dazu können innovative Lagertechnologien einen wichtigen Beitrag leisten.
Elektro- und Hybridfahrzeuge erfreuen sich weltweit wachsender Beliebtheit. Allerdings ist die Elektrifizierung des Antriebsstrangs alles andere als ein einfacher Job. Denn der Antriebsstrang eines Hybridfahrzeugs gestaltet sich weitaus komplexer als jede „konventionelle“ Lösung. Beispielsweise muss im Hybrid-Auto zwischen Elektro- und Kraftstoffmotor umgeschaltet werden, sofern nicht gerade beide gebraucht werden. Zu diesem Zweck existieren schon jetzt verschiedenste Lösungen, wobei die bis dato übliche Integration des Elektromotors in vorhandene Konfigurationen in den nächsten fünf bis zehn Jahren noch diverse Modifikation erfahren dürfte. Aus heutiger Sicht sind gut 30 alternative Antriebsstrang-Konfigurationen für Elektro- oder Hybridfahrzeuge denkbar.
Allen unterschiedlichen Varianten zum Trotz werden sämtliche Entwicklungs-Ingenieure danach streben, die jeweils größtmögliche Kompaktheit zu realisieren. Hinzu kommen allgemeingültige Kriterien wie „Robustheit“, „einfache Montage“ und insbesondere natürlich „Energieeffizienz“. So komplex die jeweiligen Konstruktionen im Endeffekt auch sein mögen – die Verwendung maßgeschneiderter Wälzlager wird wesentlich zum maximalen Wirkungsgrad der neuen Konzepte beitragen.
Energierückgewinnung
Eine vorteilhafte Komponente im Antriebsstrang eines Hybridfahrzeugs ist der gut integrierbare, riemengetriebene Starter-Generator (Belt Alternator Starter, BAS): Mit ihm lässt sich Bremsenergie zurückgewinnen. Diese kann wieder in den Motor eingeleitet werden. Mit diesem Ziel vor Augen unterstützte SKF neulich einen Tier 1-Lieferanten, der sein BAS-System in einem 48-V-Antriebsstrang optimieren wollte.
Für die neueste Version dieses Systems entwickelte SKF ein neues Rotorpositionslager, das sowohl mit Synchron- als auch Induktions-Fahrmotoren verwendet werden kann (wie sie in Elektro- und Hybridfahrzeugen zum Einsatz kommen). Das neue Lager lässt sich dank seiner Kompaktheit und seines geringen Gewichts problemlos in derartigen Antriebssträngen einsetzen. Außerdem ist es auf extreme Betriebsbedingungen ausgelegt: Es eignet sich für den dauerhaften Betrieb bei Temperaturen von bis zu 150 °C. Dabei widersteht es schweren Störmagnetfeldern sowie starken Vibrationen und wirkt nicht zuletzt Drehmomentwelligkeit und elektrischem Rauschen entgegen.
So trägt die extrem präzise arbeitende und leicht zu integrierende Lösung von SKF u. a. zu einem leiseren Lauf des Elektromotors bei, was nicht nur für ein angenehmeres Fahrerlebnis sorgt, sondern auch für eine höhere Effizienz.
Reibungsminimierung
Ein Schlüsselelement zur maximalen Effizienz ist naturgemäß ein Minimum an Reibung. Deren „Bekämpfung“ findet seit je her in jedem Teil des Fahrzeugs statt – von den Kolben bis hin zu den Reifen. In Elektro- und Hybridfahrzeugen müssen aber auch noch Reibungseffekte vermindert werden, die bspw. aus der größeren Leistungsdichte und den höheren Drehzahlen resultieren.
Auch hier kann SKF unterstützen: Wie ein Tier 1-Kooperationspartner neulich erfahren hat, ließ sich sein 48-V-BAS durch den Einsatz äußerst reibungsarmer eDrive-Rillenkugellager von SKF deutlich verbessern: Bei gleichen Abmessungen waren plötzlich höhere Drehzahlen, Lasten und Temperaturen möglich. Die speziell für den Einsatz in Elektro- und Hybrid-Antriebssträngen entwickelten SKF Lager zeichnen sich u. a. durch einen patentierten Polymerkäfig, eine optimierte Laufbahngeometrie und ein besonderes Schmierfett aus. Derartige Möglichkeiten hatte der anfragende Tier 1-Kunde zuvor gar nicht in Betracht gezogen. Dabei können diese Spezial-Lager – gemessen an „konventionellen“ Lösungen – die Reibung um bis zu 30 Prozent reduzieren.
Ein solcher Fortschritt fußt also nicht nur auf der ausgeklügelten Simulationssoftware des Lagerlieferanten: Obwohl die Computer-Modellierung von Komponenten in der Regel der entscheidende Ausgangspunkt ist, um sie für ihre spätere Anwendung zu spezifizieren, können „standardisierte“ Ausgangs-Annahmen zu fehlerhaften Rückschlüssen führen. Um solche irreführenden Schlussfolgerungen zu vermeiden, testet SKF die angestrebten Lager-Designs zum Teil auch auf speziellen Prüfständen. Deren Anforderungen gehen oft über die aktuellen Anforderungen des Marktes hinaus. Dadurch kann SKF den Kunden mehr „Sicherheitsreserven“ für die Zukunft bieten.
Isolierung
Nun sind neue Technologien ja oft Segen und Fluch zugleich. Ein gutes Beispiel hierfür sind elektrische Umrichter: Trotz all ihrer Vorteile – wie der verbesserten Energieeffizienz – führt ihr schnelles Umschalten auch zu unliebsamen Kriechströmen. Diese Kriechströme können die Lager beschädigen und somit auch deren Gebrauchsdauer senken.
An dieser Stelle sorgen Hybridlager für Abhilfe: Sie kombinieren Ringe aus Wälzlagerstahl mit einem Keramikwälzkörper. Dadurch lässt sich Kriechstrom isolieren; sodass die Komponenten samt Schmierstoff vor Beschädigungen durch Stromdurchgang geschützt werden. Außerdem halten die Hybridlager den hohen Drehzahlen elektrischer Antriebsstränge stand und sind gegenüber unzureichender Schmierung äußerst unempfindlich.
Blick nach vorn
Zweifelsohne werden Elektro- und Hybridfahrzeuge in Zukunft an Bedeutung gewinnen. Ergo suchen alle namhaften Automobilhersteller nach erfolgversprechenden Konzepten. Dabei spielt die Optimierung derzeitiger Konstruktionen eine entscheidende Rolle. Da sich Wälzlager in vielen Fällen massiv auf die Leistungsfähigkeit des Antriebsstrangs auswirken können, entwickelt SKF schon jetzt maßgeschneiderte Lösungen für die Elektromobilität von morgen.