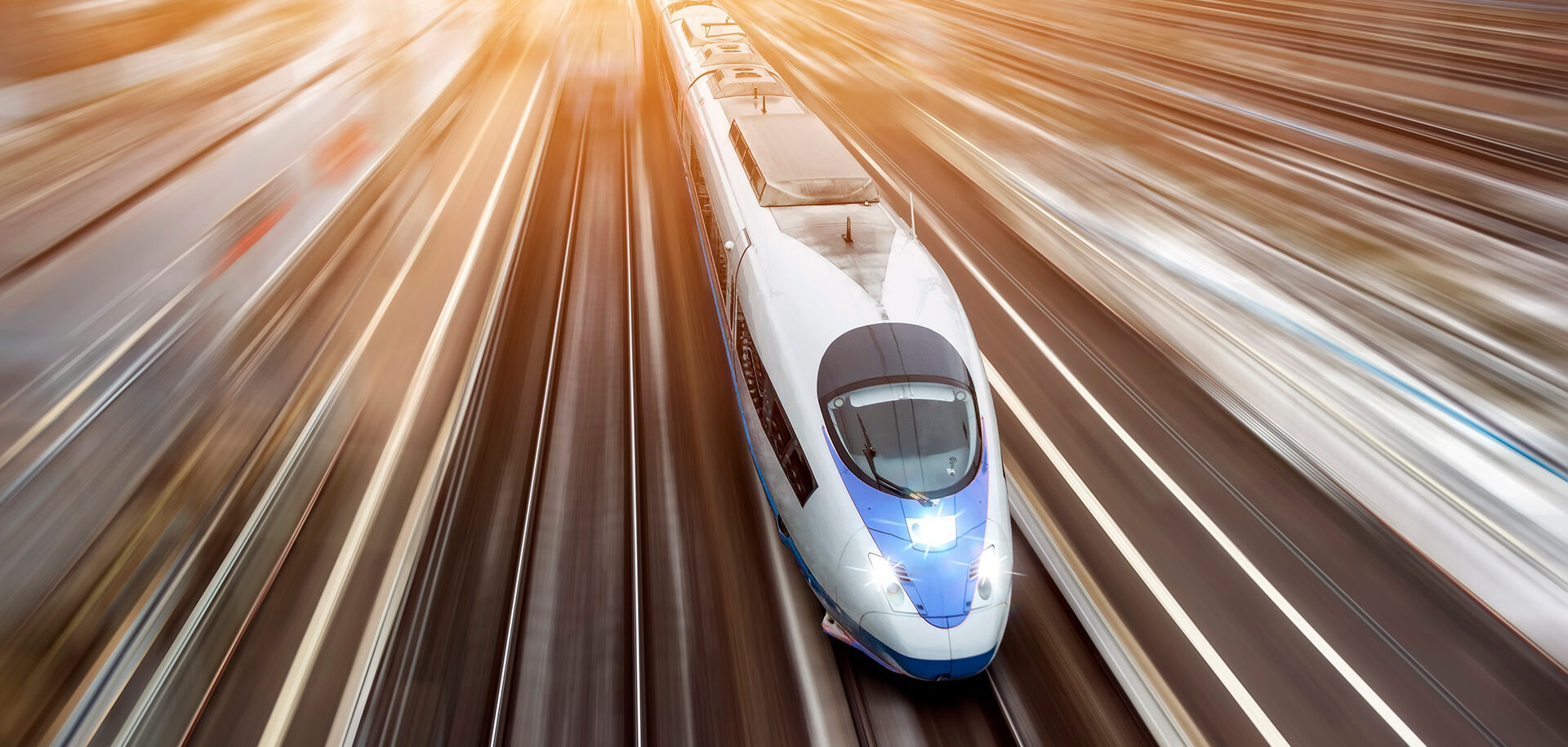
SKF Tribological Black Oxide(TBO)-Brünierung optimiert die Energieeffizienz von Radsatzlagern für Schienenfahrzeuge
Angesichts des weltweit wachsenden Schienenverkehrs, bei dem Energieverbrauch und CO2-Emissionen reduziert werden müssen, steht auch die Optimierung von Radsatzlagereinheiten an, um Leistungsverluste weiter zu verringern, ohne dass die Zuverlässigkeit darunter leidet. Bei einer der dabei untersuchten Lösungen geht es um die Auswahl des optimalen Oberflächenbearbeitungsverfahrens. Die Ergebnisse zeigen, dass die Tribological Black Oxide (TBO)-Brünierung von SKF das Lagerdrehmoment sowohl bei niedrigen als auch bei mittleren Drehzahlen erheblich reduzieren kann, was vor allem für Intercity-Züge wichtig ist.
Beschichtete Wälzlager
Es gibt viele Arten von Beschichtungen, die bei Wälzlagern zum Einsatz kommen können [2], aber nur wenige eignen sich für Lagerlaufbahnen [3]. Unter dem Oberbegriff „Konversionsbeschichtungen“ wird eine Gruppe von Beschichtungen zusammengefasst, bei der die eisenhaltigen Metalloberflächen durch geeignete elektrolytische oder nichtelektrolytische chemische Reaktionen in eine Beschichtung umgewandelt werden.
Bildung von Konversionsschichten durch Phosphatierung: Die Beschichtung ist das Ergebnis einer chemischen Reaktion, bei der das Eisen an der Oberfläche mit Mangan-, Zink- oder Zink-Calcium-Kationen und den Phosphatanionen in der Flüssigkeit reagiert. Bei Lageranwendungen haben Mangan- oder Zinkphosphate eine Dicke von 2-15 μm [2]. Anzumerken ist, dass die Phosphatierung saure Prozesse beinhaltet, die bei unsachgemäßer Durchführung sogenanntes Pitting hervorrufen können (hierdurch erhöht sich das Risiko einer unterhalb der Oberfläche beginnenden Ermüdung), was beim alkalischen Lageroxidationsverfahren (TBO-Brünierung) nicht der Fall ist. [4].
Bildung von Konversionsschichten durch Oxidation: Die Beschichtung ist das Ergebnis einer chemischen Reaktion zwischen dem Eisen der Stahloberfläche und den Reagenzien. Hierbei bildet sich eine schwarze, etwa 1 μm dicke Schicht, die aus einer Mischung aus FeO, Fe2O3 und Fe3O4 besteht. Die Norm DIN 50938 [5] und die entsprechende ISO 11408 [6] bilden die Grundlage für dieses Verfahren. Allerdings ist hier zu erwähnen, dass beide Normen schwerpunktmäßig den Korrosionsschutz behandeln und nicht darauf abzielen, Brünierschichten mit tribologischen Eigenschaften für Wälzlageranwendungen zu erzeugen. Die TBO-Brünierung von SKF wird nach diesen Normen hergestellt, aber mit optimierten Verfahren, um die tribologischen Eigenschaften der Beschichtung zu verbessern.
Morphologie und mechanische Eigenschaften von Beschichtungen
Bild 1 zeigt die Morphologie der drei untersuchten Konversionsschichten in der rasterelektronenmikroskopischen (REM-)Draufsicht. Die TBO-Brünierung (Bild 1a) zeigt Fehlstellen und Risse. Die Fehlstellenbildung ist auf die Art der Oxidumwandlung zurückzuführen, während die Risse mit dem Spannungsabbau an der Oberfläche zusammenhängen, da die Oxidschicht einen anderen Wärmeausdehnungskoeffizienten hat als das Trägermaterial aus Stahl. Die MnPh-Beschichtung (Bild 1b) weist ein polykristallines Gefüge mit prismatischen Kristallen von 5-10 µm auf. Die ZnCaPh-Beschichtung hat durch den Einsatz von Calcium während der Phosphatierung ein kompaktes Gefüge mit einer gleichmäßigen Kornverteilung (Bild 1c). In Tabelle 1 sind die mechanischen Eigenschaften der Beschichtungen aufgeführt.
Reziproke Gleittests
Zur Messung des Reibungskoeffizienten unter reinen Gleitbedingungen wurde ein firmeneigener Reibverschleißprüfstand (Bild 2) benutzt. Nach einer kurzen Einlaufzeit wiesen alle Beschichtungen eine konstante Reibung auf. Die Ergebnisse zeigen, dass der Reibungskoeffizient unter derartigen Reibverschleißbedingungen bei Konversionsbeschichtungen geringer ist, was vermutlich auf die leichtere Glättung der anfänglichen Rauheitsspitze zurückzuführen ist. Der niedrigste Reibungskoeffizient wird mit den TBO-brünierten Platten erzielt.
Roll-/Gleit-Tests
Das Reibungsverhalten unter Roll-/Gleitbedingungen wurde mit einem Prüfstand der Firma Wedeven Associates Machine (WAM) unter den für Zylinder- und Kegelrollenlager relevanten Bedingungen bewertet. Der WAM-Prüfstand wurde in zwei verschiedenen Konfigurationen verwendet, von denen die eine einen Lagerlaufbahnkontakt und die andere einen Rolle/Bord-Kontakt simulierte. Bei allen Tests wurde ein Mineralöl von 32 mm/s2 bei 40 °C ohne EP/AW-Zusätze verwendet, die Temperatur betrug 60 °C und der Schmierparameter λ = 0,3.
Bei den Kontaktbedingungen Laufbahn (Bild 3) und Bord (Bild 4) ist zu beobachten, dass die Reibung bei MnPh und ZnCaPh im Vergleich zur Stahlvariante vom Anfang bis zum Ende der Testdauer deutlich abnimmt (dies hängt mit dem Einlaufen der Konversionsschichten zusammen), während die TBO-Brünierung von Anfang an die geringste Reibung aufweist. Die Vorteile hinsichtlich der Reibung können mit der Rauheit im Inneren der Laufbahn nach den Tests verglichen werden (Tabelle 2), die bei der TBO-Scheibe sowohl in der Laufbahn- als auch in der Bord-Konfiguration deutlich geringer ist.
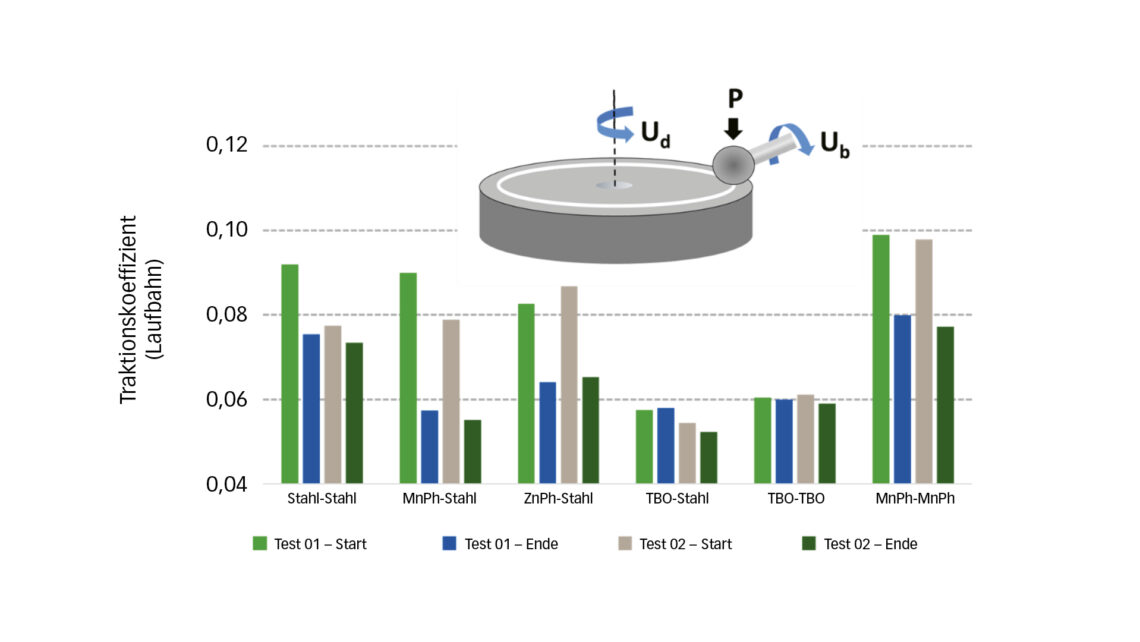

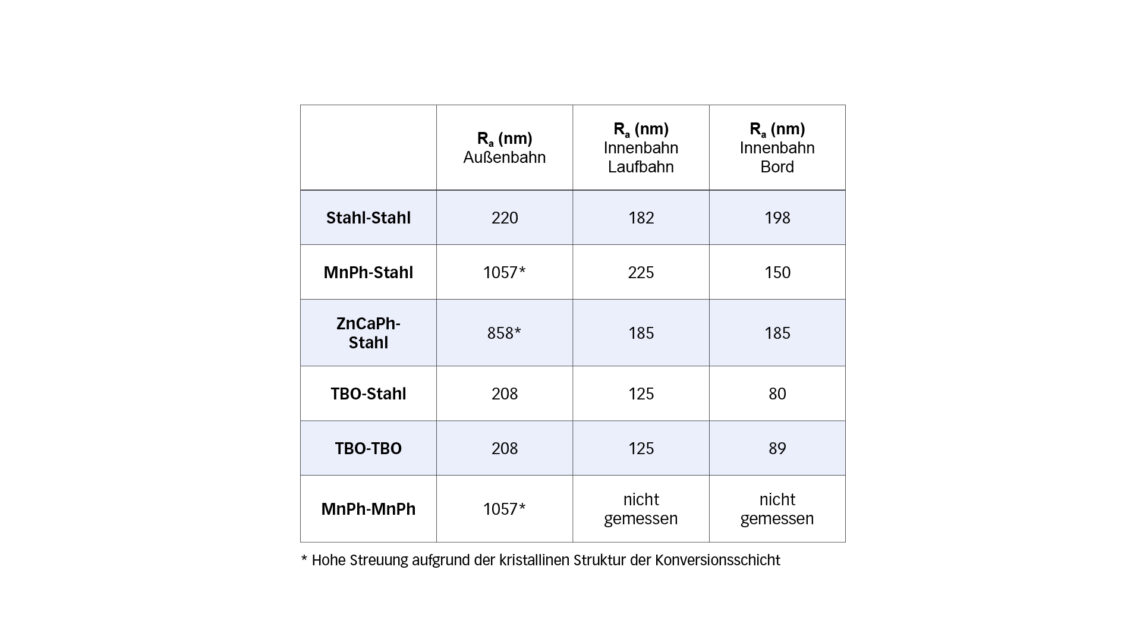
Reibungstests
Ein firmeneigener Prüfstand (Bild 5), der speziell für die Messung des Lager-Reibmoments unter verschiedenen Drehzahl- und Lastbedingungen entwickelt wurde, diente dazu, die verschiedenen Konversionsschichten unter Bedingungen miteinander zu vergleichen, die weitestgehend denen typischer Radsatzlagereinheiten von Intercity-Zügen entsprechen. Da es sich bei Radsatzlagereinheiten typischerweise um zweireihige Einheiten handelt, wurden die Tests mit einer doppelten Zylinderrollenlager-Anordnung (NU2207 ECP/C3 und NJ 2207 ECP/C3) durchgeführt. Um den Aus- und Wiedereinbau der Rollensätze zum Beschichten der Innen- und Außenringe zu erleichtern, wurden anstelle von Kegelrollenlagern Zylinderrollenlager gewählt. Die Rollensätze wurden mit den Originalringen versehen, damit die radiale Lagerluft C3 erhalten blieb. Vor der Prüfung wurde jedes Lager mit 2,50 g eines typischen Schmierfetts für Schienenfahrzeuganwendungen befüllt, um die gleiche anfängliche Fettverteilung zu gewährleisten.
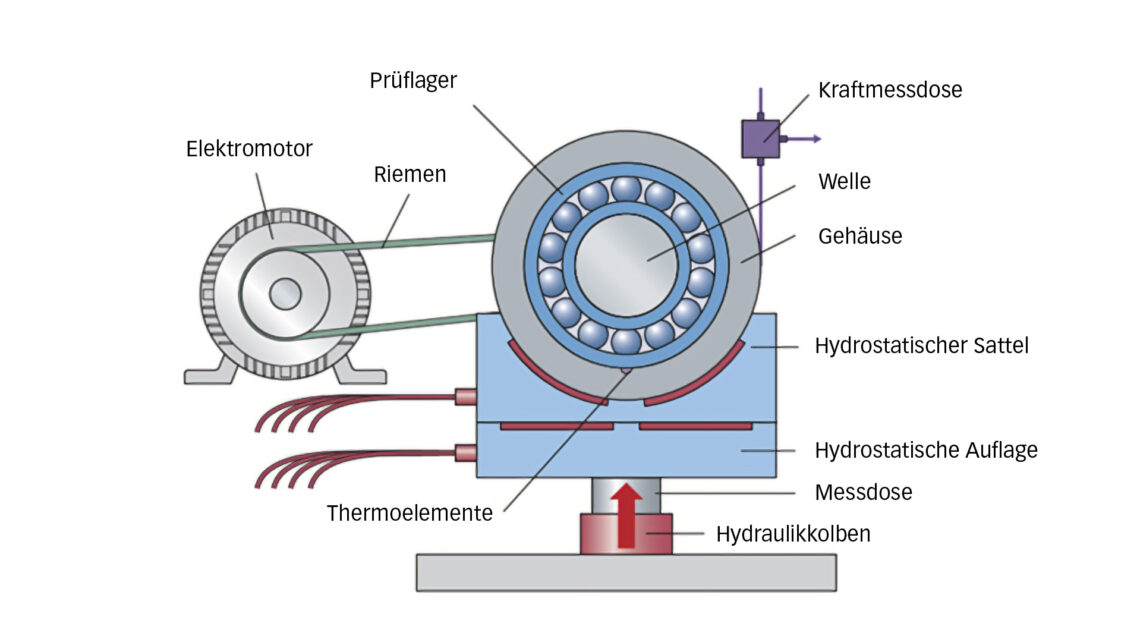
Die Radiallast wurde so eingestellt, dass der Kontaktdruck am Innenring 1,3 GPa und am Außenring 1 GPa betrug. Die Axiallast für die Drehzahlzyklen wurde so eingestellt, dass am Bordkontakt 200 MPa erzielt wurden. Der Drehzahlzyklus wurde so konzipiert, dass typische lineare Drehzahlen wie bei Intercity-Radsatzlagereinheiten erreicht und der Einfluss von Fettbewegungen auf das gemessene Drehmoment minimiert wurden. Der Axiallastzyklus wurde so ausgelegt, dass der Bordanteil zwar hervorgehoben wurde, jedoch unter dem maximal empfohlenen Axial-/Radiallastverhältnis blieb.
Nach einem 10-stündigen Einlauf wurde jeder Drehzahl- oder Axiallastschritt von einer Stunde in eine 30-minütige Drehung im Uhrzeigersinn und eine 30-minütige Drehung gegen den Uhrzeigersinn bei der vorgegebenen Drehzahl unterteilt, und das durchschnittliche Drehmoment wurde über die jeweils letzten 20 Minuten ermittelt. So konnte ein eventueller Messfehler des Kraftmessers korrigiert werden, wodurch sich eine geringe Standardabweichung ergab. Jeder Zyklus wurde nach dem Einlaufen mindestens sechsmal wiederholt, und jeder Test wurde an mindestens zwei Lagersätzen durchgeführt. Bei dieser Testreihe waren die Innen- und Außenringe entweder unbeschichtet oder mit TBO, MnPh- oder ZnCaPh-Beschichtungen versehen. Die Rollen waren nicht beschichtet.
In Bild 6 ist das durchschnittliche Drehmoment, das bei verschiedenen Drehzahlen auf der doppelten Zylinderrollenlager-Versuchsanordnung gemessen wurde, für die Tests mit unbeschichteten Stahlringen und mit den mit TBO, MnPh und ZnCaPh beschichteten Ringen dargestellt. Das durchschnittliche Drehmoment ist auf das bei den unbeschichteten Ringen gemessene Drehmoment bei 3100 min-1 und 250 N Axiallast normalisiert. Nach den Drehzahltests wurde die Laufbahn- und Bordrauheit der NJ2207-Innenringe interferometrisch gemessen (Tabelle 3). Die gemessene Rauheit wurde mit der durchschnittlichen Rauheit der neuen Innenringlaufbahn verglichen.
Bild 6 zeigt, dass die TBO-Ringe stets das niedrigste Drehmoment aufweisen, was sich mit den Feststellungen aus den Kugel-Scheibe-Versuchen deckt. Die Rauheitsmessungen lassen vermuten, dass das geringere Drehmoment auf das Einlaufen und die geglättete Oberflächentopographie der Innenringlaufbahn und des Bords zurückzuführen sein könnte (Tabelle 3). Dies könnte eine Erklärung dafür sein, warum die Vorteile der TBO-Brünierung bei höheren Drehzahlen, also wenn die Schichtdicke zwischen den Oberflächen größer ist, etwas geringer ausfallen.
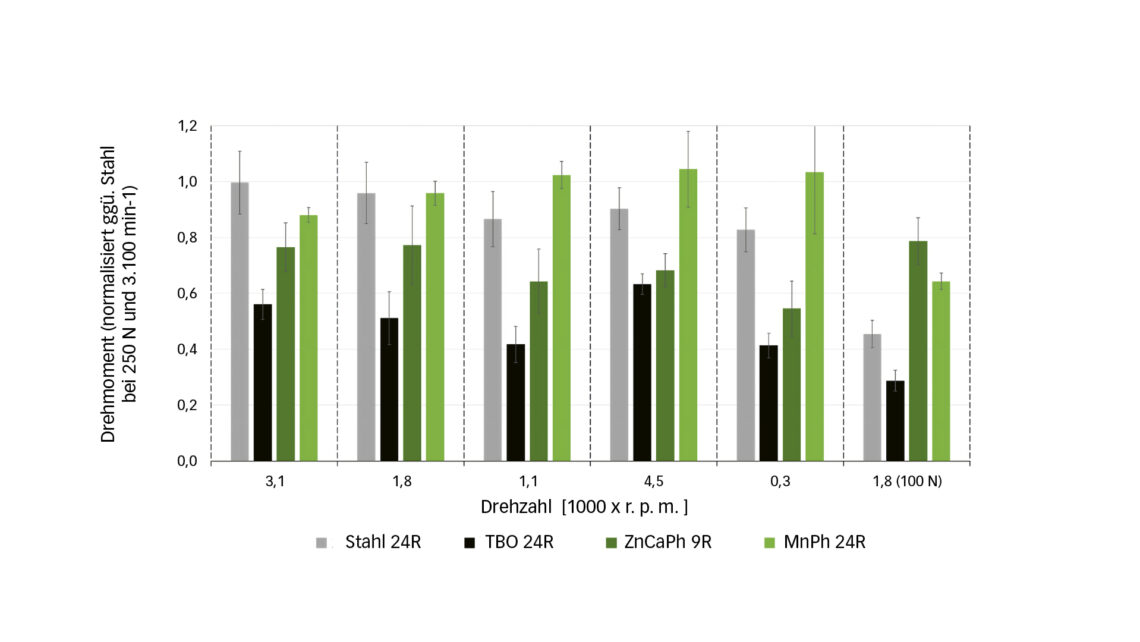
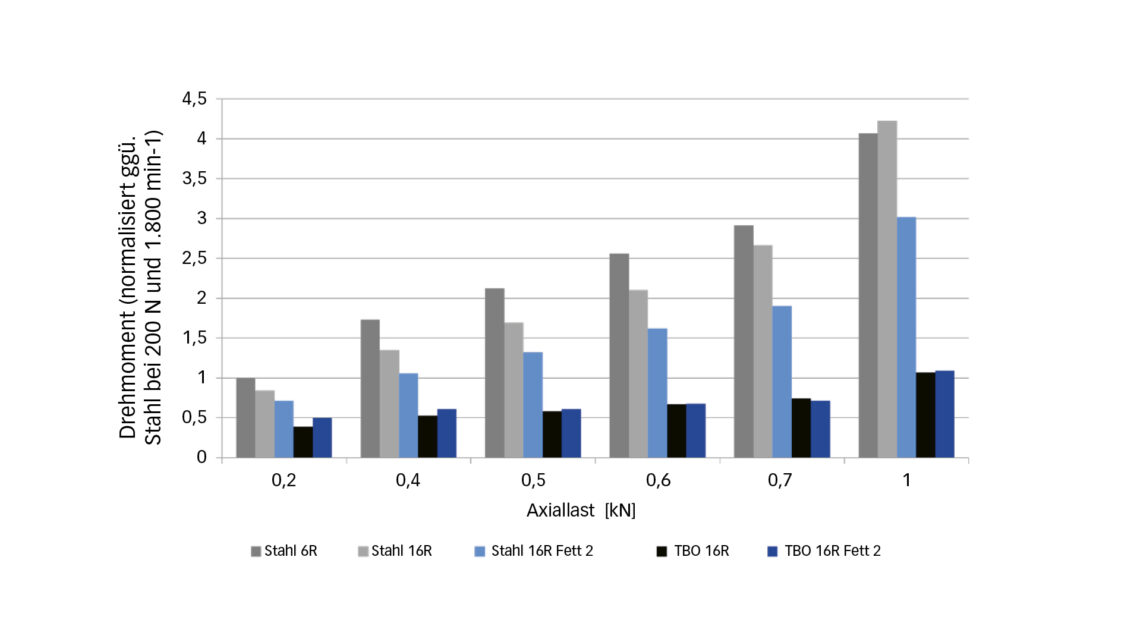
Fazit
Die reziproken Gleitversuche, die WAM-Roll-/Gleitversuche und die Lagerreibungstests zeigten, dass die TBO-Brünierung ein optimales Potenzial zur Reibungsreduzierung besitzt. Unter den gegebenen Prüfbedingungen verringert das TBO-Brünieren der Scheibe den Reibungskoeffizienten von 0,08 auf 0,06 in der Laufbahnanordnung (Bild 3) und von 0,09 auf 0,02 in der Bordkontaktanordnung (Bild 4), jeweils im Vergleich zu unbeschichteten Scheiben. Bei den Lagertests mit doppelter Zylinderrollen-Anordnung verringerte die TBO-Brünierung auf den Innen- und Außenringen das Lagerdrehmoment um bis zu 75 % (im Vergleich zu unbeschichteten Ringen), wenn eine fünffach höhere Axiallast aufgebracht wurde (und somit der Anteil des Bordkontakts erhöht wurde) (Bild 7). Es scheint, dass sich ein wesentlicher Teil der Vorteile der TBO-Brünierung zur Verringerung der Lagerreibung auf die Bordkontakte zurückführen lässt, wo die Kontaktdrücke das Einlaufen nicht erleichtern (im Vergleich zu den Laufbahnkontaktdrücken).
Die Ergebnisse bestätigen auch, dass die Vorteile, die durch das einfachere Einlaufen erzielt werden, auch mit einer gesteigerten Leistung hinsichtlich Oberflächenzerüttung und -verschleiß einhergehen, wenn die TBO-Brünierung auf der raueren Oberfläche aufgebracht wird [7]. Je nach Betriebsbedingungen kann die TBO-Brünierung auch nach längerer Zeit optisch schwarz erscheinen (Bild 8) und in den Kontaktbereichen der Wälzkörper heller und abgerieben erscheinen. Selbst wenn sie abgenutzt aussieht, bleibt eine dünne Schicht mit einem höheren Sauerstoffgehalt und einer geglätteten Oberfläche zurück. Hervorzuheben ist, dass die TBO-Brünierung außerhalb der Wälzkontaktbereiche weitere Vorteile mit sich bringt, wie beispielsweise einen leichten Korrosionsschutz, eine verbesserte Benetzbarkeit durch Schmierstoff, eine Wasserstoffbarriere usw. [2].
Es bedarf weiterer Entwicklungen, um die Lösung für Radsatzlager für Schienenfahrzeuge zu validieren, zu homologieren und industriell umzusetzen. Diese zusätzlichen Schritte werden von den Bahntechnik- und Entwicklungsteams unternommen, um den Kunden die energieeffizientesten und nachhaltigsten Lösungen anbieten zu können.
Kontakt: Esteban Broitman esteban.daniel.broitman@skf.com
References
- E. Broitman; A. Ruellan; R. Meeuwenoord; D. Nijboer; V. Brizmer, “Comparison of Various Conversion Layers for Improved Friction Performance of Railway Wheel-End Bearings.” Coatings 13 (2023) 1980
- „SKF Coatings Catalogue.“
- E. Broitman, “Coatings to Improve Bearing Performance.” Evolution (2022) 1-7.
- T. von Schleinitz, K. Nentwig, C. Bruckhaus and W. Kachler, „Brünierung: Die alte neue Hochleistungsschicht,“ Galvanotechnik, vol. 5, pp. 889-894, 2018.
- ”DIN 50938 – Black Oxide Coatings on Ferreous Metal Components – Requirements and test methods,” Deutsches Institut fur Normung e.V., Berlin, 2018.
- ”ISO 11408: Chemical conversion coatings – Black oxide coating on iron and steel – Specification and test methods,” International Organization for Standardization, Geneva, 1999.
- V. Brizmer; K. Stadler, M. van Drogen; B. Han; C. Matta; E. Piras, “The Tribological Performance of Black Oxide Coating in Rolling/Sliding Contacts.” Tribology Transactions 60 (2017) 557–574.