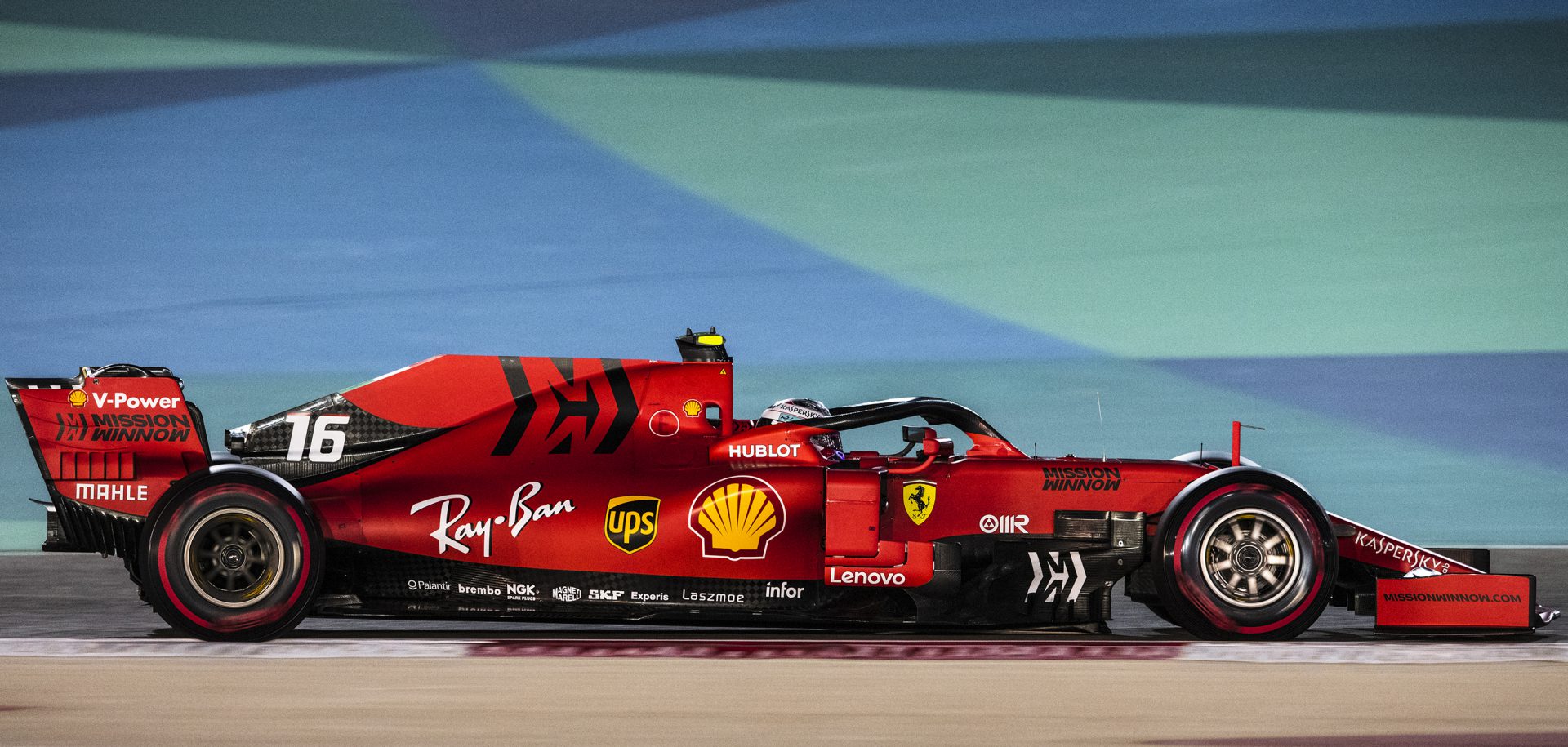
Vom Formel 1-Boliden ins E-Auto
Nur wenige Technologiezweige bieten ein derart anspruchsvolles „Testfeld“ wie der Rennsport. In diesem Highspeed-Sektor rast SKF schon seit fast 100 Jahren mit. Von den Erkenntnissen im Grenzbereich des technisch Machbaren profitieren auch Serienfahrzeuge.
Schon in den offenen Bugattis vom Typ 35 steckte SKF Technik: Mit ihren Achtzylinder-Motoren erreichten die nur 750 Kilogramm leichten Rennwagen bereits in den 1920er Jahren Spitzengeschwindigkeiten mehr als 200 Kilometern pro Stunde. Danach folgten über 2.000 Siege, mit denen der Typ 35 in Bugattis „goldenem Jahrzehnt“ den Grundstein für den sagenhaften Mythos dieser Automobilmarke legte.
Angesichts derartiger Erfolge verlässt sich heutzutage fast jeder Formel 1-Rennstall auf die Racing-Erfahrung von SKF: In den aktuellen Boliden der Scuderia Ferrari beispielsweise sind mehr als 150 extrem leistungsfähige SKF Komponenten verbaut. Dazu gehören u. a. spezielle Kugel-, Rollen- und Gleitlager für Radnaben, Getriebe, Kupplung, Motor, Turbo, Motor-Generator-Units und Aufhängungen. Viele dieser hochgezüchteten Teile fertigt der Konzern in seinem Schweinfurter Werk.
Auch außerhalb der Formel 1 sorgt das Unternehmen dafür, dass Motoren und Nockenwellen enorme Drehzahlen erreichen, Getriebe flüssig schalten und sich Räder reibungslos drehen: Von Formula Student- und Kart-Rennen über Truck-Wettbewerbe bis hin zu den nordamerikanischen NASCAR-Meisterschaften; im Grunde ist SKF auf jeder Piste zu finden. Hinzu kommen Kleinserien-Supersportwagen und natürlich Elektro-Flitzer, für die die Racing-Spezialisten des Unternehmen maßgeschneiderte Lösungen entwickeln.
Von der Rennstrecke auf die Straße
Viele der dabei gesammelten Erkenntnisse sind inzwischen in die Serienfertigung eingeflossen. Ein aktuelles Beispiel dafür sind Hybridlager, die sich bis dato insbesondere in den Highspeed-Anwendungen der Formel 1 etabliert hatten. Von solchen Lagern profitieren inzwischen immer mehr allradgetriebene E-Autos für die Straße, weil auch deren Elektromotoren mit sehr hohen Drehzahlen laufen: Diese erzielen bis zu 20.000 min-1.
Hinzu kommt, dass die Hybridlager (mit Ringen aus Stahl und Wälzkörpern aus Keramik) über einen hohen elektrischen Widerstand verfügen. Deshalb sind sie gegenüber Kriechströmen unempfindlich, wohingegen „konventionelle“ Stahl-Lager dadurch früher oder später zerstört würden. Abgesehen von ihren isolierenden Eigenschaften bieten die Keramikkugeln auch noch weitere Vorteile: Diese Wälzkörper sind etwa 60 Prozent leichter und dennoch robuster als Stahlkugeln. Sie laufen im Endeffekt kühler, sind unempfindlicher gegenüber Mangelschmierung und erreichen unter stark verschmutzten Betriebsbedingungen eine Verschleißfestigkeit, die bis zu neunmal so hoch ist wie diejenige vergleichbarer Stahl-Lager.
Aufgrund derartiger Vorzüge verlässt sich ein Premium-Anbieter von E-Fahrzeugen schon seit 2014 auf die Hybridlager von SKF – und hat seither festgestellt, dass diese Lager dank ihrer Unempfindlichkeit gegen Kriechströme, ihres geringeren Gewichts und ihrer höheren Härte auch für einen höheren Wirkungsgrad im Auto sorgen, was den Fahrzeugen letztlich zu einer größeren Reichweite verhilft.