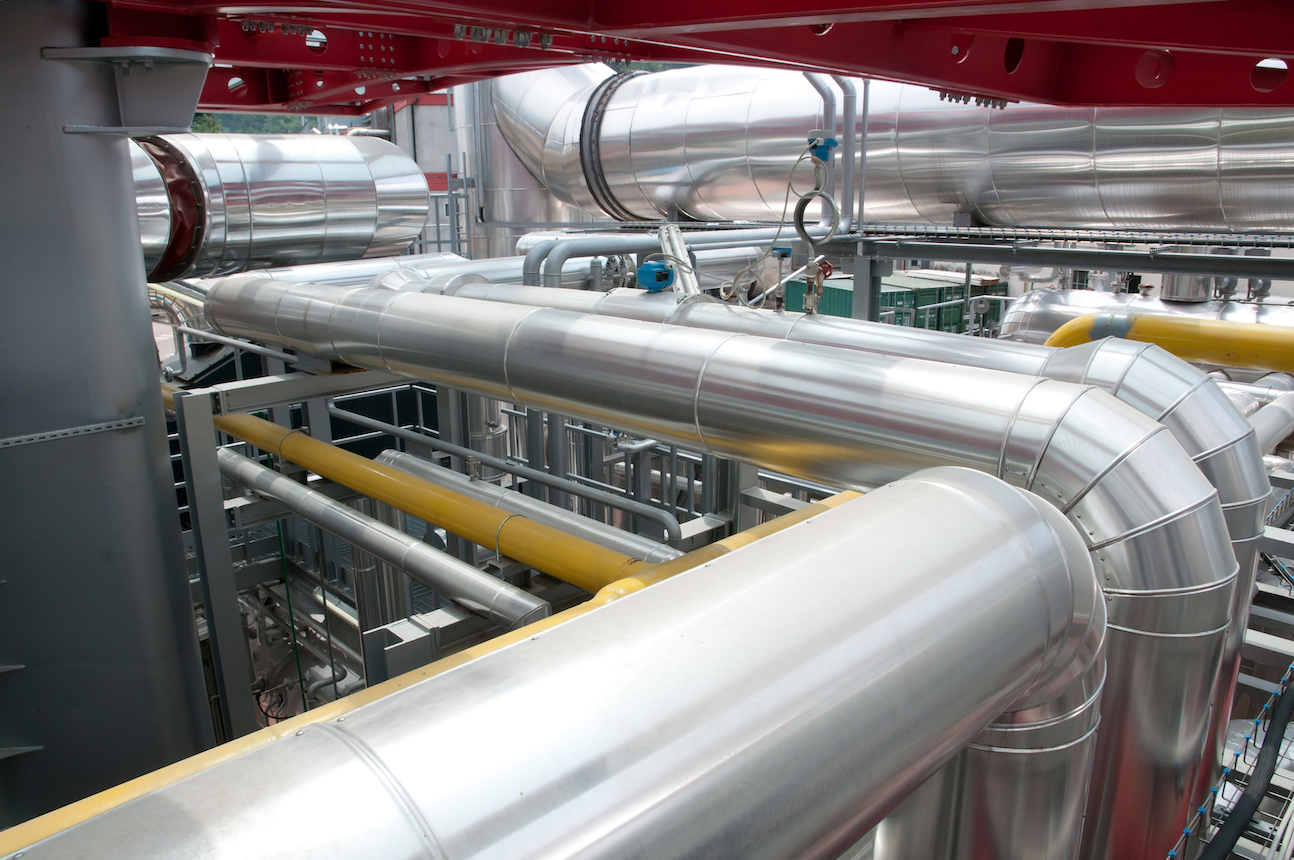
Aunar fuerzas
Con sede en Giessen, Alemania, STANLEY Engineered Fastening fabrica husillos electromecánicos para aplicar remaches autoperforantes en aluminio.
Datos
STANLEY ENGINEERED FASTENING
Sede: Giessen, cerca de Fráncfort
Empleados: 750 en Alemania, 5.000 en todo el mundo
Volumen total de negocio: 1.000 millones de euros
Productos: Sistemas de fijación y unión, principalmente para la industria automovilística, y también para la electrónica y otros sectores
www.stanleyengineeredfastening.com
Enlaces relacionados
Contacto de venta
Swen Wenig Torsten Krause
Desde que Audi lanzó el primer coche con una carrocería de aluminio (el A8, en 1994) la importancia de este metal para la industria de la automoción ha ido en aumento. Y ahora que los fabricantes tratan de hacer vehículos más respetuosos con el medioambiente y menos pesados, se ha convertido en un material de primer orden, puesto que permite reducir el consumo de combustible, las emisiones de dióxido de carbono y el peso de la carrocería.
Pero el aluminio también tiene inconvenientes. No es fácil de soldar, y hacerlo al acero resulta imposible. Aquí es donde entra en escena STANLEY Engineered Fastening.
A la empresa, filial del gigante estadounidense de las herramientas Stanley Black & Decker, todavía se la conoce en Europa por su antiguo nombre: Tucker. Su especialidad son los sistemas que permiten unir elementos. Se centra en la industria automovilística y su cartera de productos incluye, entre otros, sistemas para la soldadura de espárrajos, fijaciones de plástico, remaches ciegos o remaches autoperforantes.
Según Manfred Müller, presidente de Global Automotive, los remaches autoperforantes (RAP) son una buena manera de juntar dos planchas de aluminio o de unirlas a planchas de acero. “El remache perfora la superficie superior y se abre una vez atraviesa la segunda capa”, dice Müller. “El resultado es una unión tremendamente fuerte que ofrece más ventajas que el remache ciego: no hay que hacer un agujero, puede automatizarse y es totalmente impermeable a líquidos y gases”.
La primera incursión en este campo coincidió con la fabricación del Audi A8. Se le pidió a Tucker que adaptara su sistema de suministro de espárragos a la pistola soldadora para que funcionase también con remaches autoperforantes. “Fue entonces cuando vimos el potencial”, recuerda Müller.
Por entonces, los RAP se fijaban por medios hidráulicos, y Müller admite que era un método que Tucker no dominaba: “Siempre habíamos trabajado en el mundo de la soldadura y lo sabíamos todo sobre electricidad. Por eso, decidimos desarrollar un sistema electromecánico”. Su falta de experiencia inicial acabó siendo una bendición, ya que la solución electromecánica aportó ventajas considerables.
En colaboración con SKF, desarrollaron un husillo que empuja el remache de forma eficiente y muy controlada. Un motor eléctrico y una transmisión por engranaje accionan un husillo SKF de rodillos planetarios que aplica presión al remache.
“La presión y la velocidad se pueden definir con gran exactitud”, dice Müller. Swen Wenig, jefe de la unidad de ventas de SKF para aplicaciones de precisión en Alemania y Suiza, añade que se puede obtener una presión máxima incluso cuando la unidad está parada. “El 100% de la carga de presión se aplica en cada posición, independientemente de la velocidad del sistema de empuje”, dice. “También destaca por su eficiencia energética; sólo hay consumo cuando el motor está funcionando”.
Las primeras máquinas remachadoras se entregaron a principios de los 90 y, desde entonces, tanto STANLEY como SKF han perfeccionado el producto. “Nuestra área de I+D ha seguido trabajando para perfeccionar el husillo de rodillos planetarios”, dice Müller. Añade Wenig: “Uno de los grandes retos ha sido el de aumentar la rentabilidad de todo el sistema”.
También se han mejorado, de manera significativa, el sistema de alimentación de los remaches y el software, que controla la fuerza y la carrera. Las unidades se acoplan a los más de 250 robots encargados de aplicar unos 3.500 remaches por vehículo que hay en una cadena de montaje de carrocerías de aluminio. Cada husillo debe diseñarse con un fin específico, adaptándose al tamaño y la forma de las prensas de bastidor en C en las que se colocan las planchas, y adecuándose a los diferentes requisitos físicos. Incluso puede ser necesario ajustar el bastidor antes de iniciar el remachado. En ese caso, el husillo deberá levantarse para que la unidad alcance la superficie, si bien luego (a medida que se aplica cada remache) este movimiento se reducirá al mínimo para ahorrar tiempo y energía.
Los bastidores constituyen una parte muy importante del diseño. “Están fresados con un acero especial y deben soportar grandes cargas”, explica Burkhard Butz, jefe de planta. Para que funcione el sistema, las partes superior e inferior de los bastidores en C deben estar perfectamente alineadas, a pesar de que las cargas tienden a desalinearlas. “Pueden pesar hasta 600 kilos”, dice Carsten Hess, jefe de compras.
Las cargas en estas unidades de remachado pueden ser mayores en el futuro. “El aumento en el uso de acero de gran resistencia como solución para reducir el peso supondrá un reto importante”, dice Müller. “El acero, que es muy fino y resistente, siempre se usa como la capa superior que el remache debe perforar. Sin embargo, el husillo debe ser capaz de administrar la fuerza que tiene que aplicar para poder así controlar el remache. Éste debe ser lo suficientemente resistente como para perforar el acero, pero lo suficientemente dúctil como para abrirse en el aluminio”.
Husillos de rodillos planetarios SKF
Los husillos de rodillos planetarios de SKF permiten un control muy preciso de los movimientos lineales. Un husillo de rodillos planetarios está compuesto por un eje de husillo, rodillos planetarios y una tuerca. Estos componentes tienen una rosca helicoidal perfectamente acoplada. Cuando se gira la tuerca, se produce un movimiento lineal del eje de husillo sin juego axial. La forma de la rosca proporciona una superficie de contacto amplia y una capacidad elevada de carga. La enorme precisión del husillo de rodillos planetarios permite controlar a la perfección la presión y la velocidad del movimiento lineal.