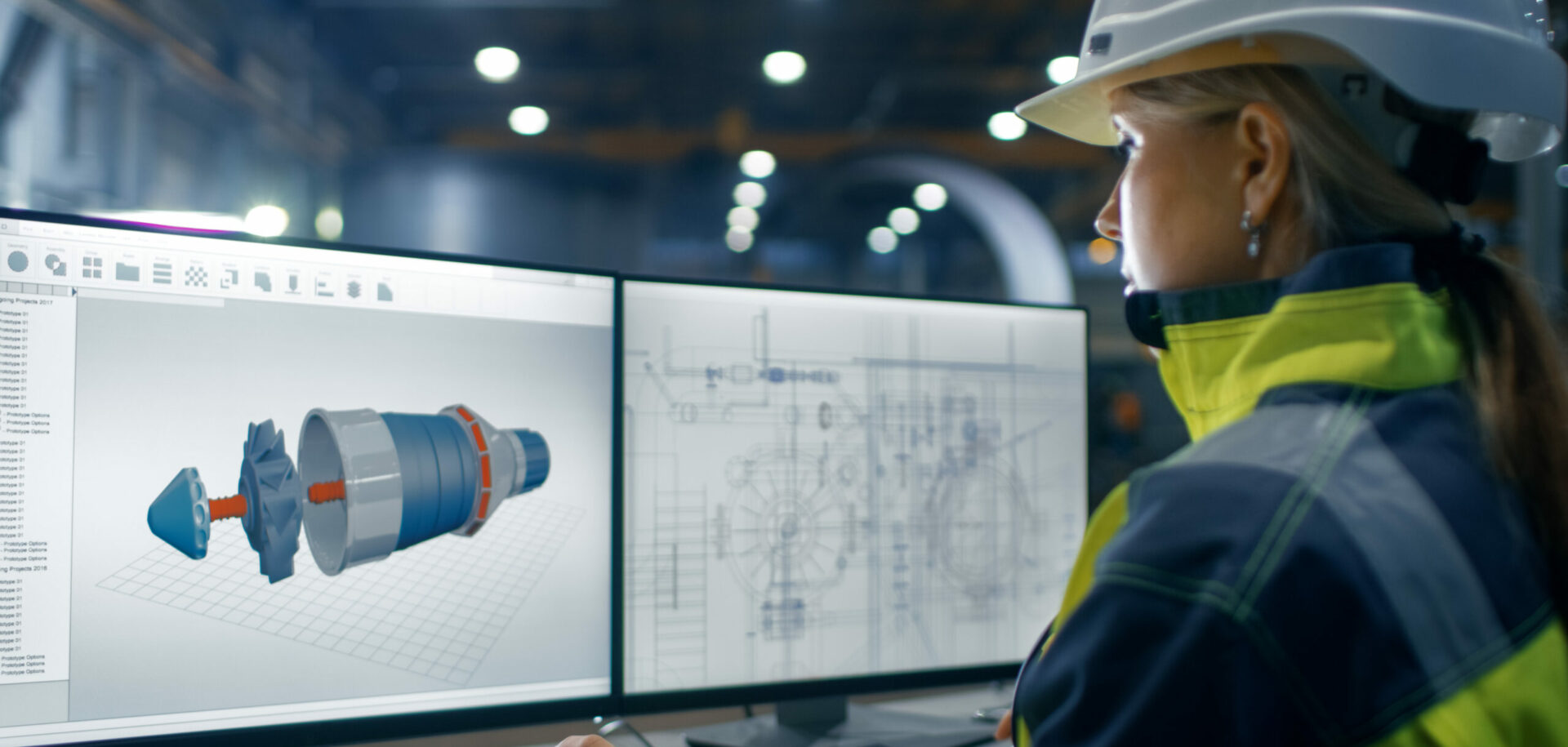
Beneficios de utilizar rodamientos revestidos de óxido negro en aplicaciones eólicas
El aumento constante del tamaño de las turbinas eólicas para incrementar la producción de energía impone mayores demandas a los trenes de potencia.
Resumen
Para hacer frente a los complejos requisitos operativos de la industria de turbinas eólicas, SKF está utilizando un proceso de tratamiento especial denominado “oxidación negra”. Este confiere a los componentes de los rodamientos una capa protectora dotada de resistencia química y resistencia a la corrosión, y que contribuye a prevenir daños en los rodamientos durante la crucial fase de rodaje.
Durante su vida útil, las turbinas eólicas están expuestas a grandes variaciones de temperatura, velocidad del viento y cargas [1]. Estas condiciones de funcionamiento, en combinación con la potencial influencia nociva de contaminantes sólidos y el ataque triboquímico de los componentes químicos del aceite y la contaminación de agua, pueden provocar daños en los rodamientos (fig. 1) [2], que acortarán considerablemente su vida útil.
Uno de los requisitos para evitar estas fallas es que los rodamientos tengan superficies de alto rendimiento que favorezcan el proceso de rodaje, además de ser resistentes a la corrosión e inertes ante reacciones nocivas de los componentes químicos agresivos del lubricante. Gracias a su larga colaboración con la industria de la energía eólica, SKF ha comprobado que la oxidación negra es una de las muchas soluciones que mejoran la confiabilidad operativa.
El proceso de oxidación negra
El óxido negro es un tratamiento de la superficie que se forma por una reacción química en la capa superficial del acero del rodamiento, y tiene lugar cuando las piezas se sumergen en una solución de sal alcalina acuosa a una temperatura de aproximadamente entre 130 y 150 °C. La reacción entre el hierro de la aleación férrica y los reactivos produce una capa de óxido en la capa exterior de los componentes del rodamiento, que es una combinación bien definida de FeO y Fe2O3, que forma Fe3O4. El resultado es una capa superficial negra de aproximadamente 1–2 μm de espesor. El proceso total consta de unas 15 etapas de inmersión diferentes, en muchas de las cuales es posible variar el contenido de productos químicos, la concentración, temperatura, tiempo de inmersión y comportamiento del fluido en los tanques [3].
Beneficios de la oxidación negra
Aquí vamos a limitarnos a resumir solo los efectos beneficiosos más relevantes de la oxidación negra para la industria eólica. Se describen brevemente en tres categorías y demuestran cómo este proceso puede contribuir a reducir los riesgos que conlleva cada mecanismo causante de fallas.
1. Menos riesgo de fallas prematuras
En algunos trenes de potencia de turbina eólica, los rodamientos de la multiplicadora pueden fallar prematuramente debido a grietas, desconchado o grietas irregulares de corrosión blanca por ataque ácido (WEC). Las WEC se refieren al aspecto de la microestructura alterada del acero al pulir y grabar una microsección. Pueden producirse fallas en varios puntos del diseño de las multiplicadoras de la turbina eólica, como los rodamientos planetarios, el eje intermedio y los rodamientos del eje de alta velocidad.
La presencia de fallas debido a las WEC ha sido ampliamente debatida en el sector de la industria eólica, y está siendo investigada separadamente por los fabricantes de turbinas eólicas y de multiplicadoras, por los proveedores de rodamientos y por universidades e institutos independientes. Muchas de las hipótesis actuales se concentran en aspectos relativos a la superficie, como la penetración de hidrógeno e interacción con inclusiones subsuperficiales, o fenómenos puramente de fatiga/tribomecánica relacionados con el funcionamiento de la superficie. Para obtener información más detallada sobre la causa raíz de una falla WEC, ver [4].
Según la investigación que se realiza actualmente y la información bibliográfica, distintos mecanismos pueden contribuir a reducir el riesgo de fallas WEC, como:
- reducción del ataque tribológico y químico [5] (“pasivación”)
- reducción de la difusión del hidrógeno en el acero del rodamiento [6] (“pasivación”)
- protección contra la corrosión [7]
- estabilización de la microestructura del camino de rodadura [8].
La oxidación negra puede contribuir a proteger los componentes del rodamiento de los mecanismos de fallas antes mencionados. A continuación, expondremos varios ensayos de laboratorio e investigaciones que revelan las ventajas de la oxidación negra.
1.1 Ataques triboquímicos de lubricantes y aditivos
Los aceites para engranajes se han desarrollado para optimizar el rendimiento de esos equipos. En la mayoría de los casos, se añaden aditivos antidesgaste e inhibidores de la corrosión para incrementar el rendimiento del engranaje. Lamentablemente, los componentes químicos de esos aceites no siempre favorecen el funcionamiento de los rodamientos. En los contactos de los dientes de los engranajes, el deslizamiento macroscópico es significativamente superior (relación entre deslizamiento y rodadura de hasta el 30%) al de los rodamientos (relación entre deslizamiento y rodadura de hasta el 4%, según el tipo de rodamiento). Por ello, la dinámica (formación y extracción) de capas de reacción en los engranajes es diferente de la de los rodamientos.
Cuando los rodamientos funcionan en condiciones de lubricación marginales (condiciones límite y combinadas), se producen reacciones entre los aditivos en el aceite del engranaje y la superficie de acero de los contactos rodantes. Probablemente, cuando se forma una capa de reacción, la energía química empleada, junto con la energía tribológica, modifican en el acero del rodamiento la microestructura cerca de la superficie [9]. El cambio de la microestructura cerca de la superficie provoca un cambio en sus propiedades mecánicas y, en consecuencia, en el rendimiento tribológico (fricción, desgaste y fatiga en la superficie). Si las reacciones no son favorables, se producen cambios significativos en la microestructura cerca de la superficie, seguidos de la iniciación de microgrietas.
Mediante ensayos con aceites para engranajes, Pasaribu y Lugt [10] han demostrado la correlación positiva entre el espesor de las capas de óxido y el rendimiento del rodamiento. Esto indica que la pasivación de las superficies del rodamiento retarda reacciones desfavorables entre los aceites para engranajes y las superficies de los rodamientos. Por consiguiente, capas de óxido de ~1–2 μm preparadas previamente, como una capa de óxido negro, reducen el riesgo de reacciones desfavorables entre los aceites para engranajes y las superficies de los rodamientos.
La ventaja del tratamiento de oxidación negra como medida preventiva contra la formación de grietas en las superficies puede determinarse sometiendo las superficies con oxidación negra a contactos tribológicos con lubricación límite. Un ejemplo de dicho ensayo es la bola en disco lubricada y desalineada. La bola y el disco están accionados independientemente, lo que permite controlar la relación entre deslizamiento y rodadura relevante en el funcionamiento del rodamiento. La fig. 2 muestra resultados de ensayos con aceite que contiene aditivos antidesgaste agresivos. La superficie del acero sin tratar se ve afectada por microgrietas. En cambio, la superficie con oxidación negra no muestra formación alguna de microgrietas.
1.2 Fragilización por hidrógeno
La oxidación negra, como tratamiento superficial de “pasivación”, puede reducir con eficacia la penetración de hidrógeno atómico y el ataque químico al acero de los rodamientos. Esta propiedad se evaluó en los resultados de ensayos en laboratorio de aro C y permeación de H [11].
Se diseñó especialmente un banco de pruebas de aros C para evaluar el agrietamiento por tensocorrosión inducido por el hidrógeno (hydrogen-induced stress corrosión cracking, HISCC) en contactos lubricados [12]. La fig. 3 muestra un aro interior de un rodamiento de rodillos cilíndricos con un segmento cortado. El aro se carga mediante un tornillo para generar en la superficie una tensión de tracción definida. La absorción de hidrógeno del entorno lubricante favorece la iniciación de grietas en la superficie por tensión de tracción. La vida útil del aro C, definida como el tiempo transcurrido hasta que el aro C se agrieta bajo una carga de tracción definida, refleja la resistencia contra el HISCC. El gráfico en la fig. 3 muestra que los aros C con oxidación negra tienen una vida útil más prolongada, en comparación con la probeta sin revestir.
La resistencia de la oxidación negra a la absorción de hidrógeno también puede evaluarse en un ensayo de permeación electroquímica de H, en el que se genera hidrógeno atómico mediante carga electroquímica. El hidrógeno penetra en la chapa de acero y se mide mediante oxidación electroquímica cuando se libera del otro lado de la chapa de acero. La penetración de hidrógeno a través de un revestimiento superficial puede evaluarse comparando el flujo (la corriente) de permeación de hidrógeno obtenido con el de la probeta sin revestir. La fig. 4 muestra que las chapas de acero con una superficie con oxidación negra emiten un flujo de permeación de H significativamente inferior al de una probeta sin revestir. Ello se debe, a diferencia de la difusión en acero grueso, a que el hidrógeno atómico debe ionizarse (como protón) para poder atravesar una capa de óxido. La fuerte interacción entre los átomos de hidrógeno ionizado y los aniones del óxido de hierro forma una capa de óxido negro que actúa como una barrera que retarda la permeación de H [13].
1.3 Daños de corrosión por humedad (corrosión por reposo)
Unos gradientes de temperatura elevados fomentan la condensación del agua del aire húmedo. Aun cuando el riesgo de contaminación de agua no se menciona frecuentemente de manera directa en aplicaciones eólicas, es ampliamente conocido que el agua disuelta podría reducir la funcionalidad de los aditivos antidesgaste [14] y que el agua libre fomenta la corrosión y la absorción de hidrógeno [15][16]. El riesgo de corrosión aumenta en las paradas durante los intervalos de mantenimiento de la turbina eólica o cuando no sopla el viento [7].
La microestructura del óxido negro tiene una cierta porosidad, lo cual puede incrementar la afinidad del lubricante o de los conservantes en la capa de revestimiento, y aumentar la resistencia a la corrosión por humedad o reposo. En un ensayo con rociado de sal en un armario [17], las probetas con oxidación negra mostraban una resistencia a la corrosión significativamente superior a las sin revestir (fig. 5).
2. Condiciones operativas severas con lubricación insuficiente, o daños en la superficie.
2.1 Desgaste adhesivo; daños por adherencia o deslizamiento
Si los rodamientos están sometidos a una carga excesivamente baja (inferior a la carga mínima requerida), ello puede conducir a una gran discrepancia entre la velocidad de rotación del aro interior y el conjunto de rodillos, lo cual, a su vez, comporta un elevado deslizamiento entre los elementos rodantes y el aro interior [18]. A veces, la probabilidad de deslizamiento puede ser muy elevada en aplicaciones exigentes como ejes a alta velocidad de multiplicadoras de turbinas eólicas, en condiciones de funcionamiento en vacío y en los cambios de zonas de carga. Por tanto, se corre un alto riesgo de daños por adherencia [19] [20].
En rodamientos de ejes de alta velocidad, los resultados de ensayos de funcionamiento en vacío de multiplicadoras manifiestan una mejora del efecto protector del revestimiento de óxido negro contra los daños por adherencia. La fig. 6 muestra los daños por adherencia que aparecen en las superficies del aro interior y el rodillo sin revestir después de 45 minutos en condiciones de funcionamiento en vacío, mientras que los aros con oxidación negra no manifiestan daños significativos después de 30 horas.
El mecanismo protector de las superficies con oxidación negra puede explicarse como una menor fricción después de la fase de rodaje, así como una mejor adhesión del lubricante a la superficie, en comparación con las superficies sin revestir.
2.2 Deformación superficial
La deformación superficial es una fatiga iniciada en la superficie a un nivel de aspereza, asociada con condiciones de lubricación deficientes, y que corresponde a tracciones superficiales (de fricción) elevadas [21]. Se presenta especialmente en los dientes de engranajes, pero a veces también en los rodamientos. Si el daño se produce en los rodamientos, la deformación superficial puede ser muy perjudicial para su funcionamiento.
Aunque no es necesariamente una forma de falla primaria en los rodamientos, puede facilitar o acelerar la aparición de otros tipos de fallas, como indentaciones por impurezas, el desconchado iniciado en la superficie y el agarrotamiento [22]. El riesgo de deformación superficial puede reducirse de diversas maneras, por ejemplo, disminuyendo la fricción en la superficie, redistribuyendo las tensiones cerca de ella de una manera favorable, o bien reduciendo las presiones de lubricación combinadas u optimizando el proceso de rodaje. Una forma de conseguir estos objetivos es utilizando revestimientos de protección, como oxidación negra.
A pesar de la gran labor teórica y experimental que se ha realizado sobre la deformación superficial en general (ver la bibliografía en [21]), hasta ahora la influencia de los revestimientos en la deformación superficial no se había estudiado lo suficientemente. Por consiguiente, se ha realizado una serie de experimentos con rodillos con oxidación negra [23] en un banco de pruebas de deformación superficial en condiciones de laboratorio [14] [21], que han abarcado el control de la relación entre deslizamiento y rotación, las condiciones de lubricación, la temperatura, la carga y la velocidad. La unidad de carga del banco de pruebas de deformación superficial se muestra esquemáticamente en la fig. 7 (arriba): un rodillo giratorio en contacto con tres discos, todo ello fabricado de acero de rodamientos templado. Consta de un pequeño rodillo (12 mm de diámetro) procedente de un rodamiento de rodillos a rótula y tres grandes piezas antagonistas que son aros interiores de rodamientos de rodillos cilíndricos. El tratamiento final de los rodillos y aros puede ser rectificado y/o pulido hasta el tipo de rugosidad deseado. El material de los rodillos y piezas antagonistas probados es acero de rodamientos ANSI-52100. Las condiciones de lubricación durante los ensayos variaron desde lubricación de capa límite hasta lubricación combinada. Después de los ensayos, se controló la deformación superficial de la superficie de los rodillos. Se compararon los resultados de rodillos sin revestir y con oxidación negra en condiciones idénticas.
Los resultados experimentales obtenidos con el banco de pruebas de deformación superficial revelan que la oxidación negra proporciona una cierta protección contra deformaciones en la superficie por toda la gama de las condiciones del ensayo [23], tal como se describen en la fig. 7.
Además, en superficies revestidas [23] se realizó un análisis paramétrico del modelo de deformación superficial [22], incluidos los efectos de fricción, y de rigidez y espesor del revestimiento. Se comprobó la existencia de un espesor de revestimiento óptimo que se correspondía con los mínimos daños de deformación de la superficie. Como muestran los resultados experimentales y teóricos, el tratamiento de óxido negro prolonga la gama de condiciones operativas seguras ante la deformación superficial, en comparación con las superficies de acero de rodamientos sin revestir.
3. Ensayos en rodamientos y experiencia práctica
Se ha realizado un ensayo de vida útil en rodamientos con oxidación negra expuestos a condiciones de lubricación severa combinadas. Se ha podido confirmar el efecto positivo de los rodamientos con oxidación negra, en comparación con los tipos sin revestir en cuanto a rodaje [24] y condiciones de lubricación con valores kappa bajos.
En este ensayo, se han suspendido todas las pruebas de rodamientos con oxidación negra. De hecho, los resultados señalan una estimación de vida L10 de 2 a 3 veces superior a la estimación de vida L10 de los rodamientos sin revestir.
Además de los resultados del ensayo de componentes y de los ensayos con rodamientos antedichos, la experiencia práctica ha demostrado los beneficios de la oxidación negra en la reducción del riesgo de fallas prematuras. Informes de los fabricantes de multiplicadoras y de turbinas eólicas confirman una disminución significativa en la proporción de fallas de rodamientos mediante el uso de rodamientos con oxidación negra en comparación con rodamientos sin revestir [25] [26].
Asimismo, se ha observado en [8] y [25] que un recalentamiento suave por debajo de la temperatura de revenido o transformación, puede contribuir a optimizar y reforzar la microestructura sin pérdidas de dureza y, en consecuencia, a prolongar la vida de fatiga del rodamiento. Siguiendo este concepto, la oxidación negra a una temperatura similar puede contribuir a crear efectos beneficiosos en la microestructura de la superficie exterior del acero, lo cual quedó reflejado por una reducción >0,1 grados en el valor de anchura a media altura (full width half maximum, FWHM o b/B) de los valores pico de XRD.
Conclusiones
Al combinar investigación en laboratorio, ensayos con rodamientos y experiencia práctica, se han demostrado varios efectos beneficiosos del óxido negro. Este tratamiento superficial ofrece una cierta protección contra los ataques triboquímicos, reduce la permeación de hidrógeno e incrementa la resistencia a los daños provocados por la humedad (como la corrosión por reposo). Además, las superficies de acero de rodamientos con oxidación negra mejoran el margen de seguridad cuando se examinan fallas de los tipos de desgaste adhesivo/daños por adherencia o deformación de la superficie. Los resultados positivos de la experiencia práctica confirman estas observaciones.
En resumen, el proceso de oxidación negra utilizado por SKF refuerza la protección contra daños de los componentes de los rodamientos. Los rodamientos tratados con oxidación negra, además de montarse en equipo original, pueden usarse como recambios de rodamientos convencionales como parte de las rutinas de mantenimiento de los parques eólicos. Esto significa que los beneficios de la oxidación negra pueden aplicarse a todos los tipos de rodamiento utilizados en sistemas clave de multiplicadoras de turbinas eólicas por toda la industria de la energía eólica. Para un rendimiento óptimo, SKF recomienda que estén tratados con oxidación negra el aro interior y exterior, así como los elementos rodantes.
Referencias
[1] J.Rosinski, D.Smurthwaite, Troubleshooting wind gearbox problems, Gearsolutions 2010
[2] K.Stadler, Tratamiento de oxidación negra, Evolution #4 2013
[3] DIN 50938, Black oxide treatment of ferrous material
[4] K.Stadler, A.Stubenrauch, Averías prematuras en los rodamientos de las multiplicadoras eólicas y grietas WEC, Antriebstechnisches Kolloquium Aachen, ATK 2013 y SKF Evolution #2 2013
[5] W.Holweger, Interaction of rolling bearing fatigue life with new material phenomenons, VDI Kongress “Antriebs-stränge in Windenergieanlagen” 2012
[6] H.Uyama, The mechanism of white structure flaking in rolling bearings, NREL workshop, Broomfield noviembre 2011
[7] I.Strandell, C.Fajiers, T.Lund, Corrosion – one root cause for premature bearing failures, 37th Leeds-Lyon Symposium on Tribology, 2010
[8] J.Gegner, L.Schlier, W.Nierlich, Evidence and analysis of thermal static strain aging in the deformed surface zone of finish-machined hardened steel, PowderDiffraction 24-2009 págs. 45-50
[9] M.Reichelt, T.E.Weirich, J.Meyer, T.Wolf, J.Loos, P.W.Gold, M. Fajfrowski, TEM and nanomechanical studies on tribological surface modifications formed on roller bearings under controlled lubrication conditions. J. Mater. Sci. 41, 4543-4553 (2006)
[10] H.R.Pasaribu, P.M.Lugt, The Composition of Reaction Layers on Rolling Bearings Lubricated with Gear Oils and Its Correlation with Rolling Bearing Performance, Tribology Transaction, Vol. 55, 3, 351-356, 2012
[11] ASTM G38, “Standard practice for making and using C-ring stress-corrosion test specimens” and ASTM G148, “Standard practice for evaluation of hydrogen uptake, permeation and transport in metals by an electrochemical technique”
[12] B.Han, B.X.Zhou, R.Pasaribu, C-ring Hydrogen Induced Stress Corrosion Cracking (HISCC) – Tests in Lubricating Liquid Media, EuroCorr 2011 Proceeding
[13] R-H.Song, S-I.Pyung, R.A.Oriani, The hydrogen permeation through passivating film on iron by modulation method, Electrochemica Acta Vol 36, No. 5/6, págs. 825-831, 1991
[14] V.Brizmer, R.Pasaribu, G.E.Morales, Micropitting Performance of Oil Additives in Lubricated Rolling Contacts, Tribology Transactions, Vol. 56, 5, págs. 739-748, 2013
[15] R.J.K.Wood, Tribology and corrosion aspects of wind turbines, Wind Energy – Challenges for Materials, Mechanics and Surface Science, IoP, Londres 2010
[16] D.A.Jones, Principles and Prevention of Corrosion – 2nd Ed., página 335, ISBN: 0-13-359993-0, 1996
[17] ASTM B117-09, Standard Practice for Operating Salt Spray (Fog) Apparatus
[18] M.Volkmuth, K.Stadler, R.Heemskerk, Slippage measurements in roller bearings, Antriebstechnisches Kolloquium ATK Aachen 2009
[19] R.Hambrecht, Anschmiererscheinungen in Wälzlagern bei Fettschmierung, PhD thesis, Erlangen 1999
[20] B.J.Scherb, J.Zech, A study on the smearing and slip behavior of radial cylindrical roller bearings, Schaeffler Group 2001
[21] G.E.Morales, K.Stadler, V.Brizmer, Understanding and preventing surface distress, Gear solutions 2012
[22] G.E.Morales-Espejel, V.Brizmer, Micropitting Modelling in Rolling-Sliding Contacts: Application to Rolling Bearings, Trib. Trans., 54, págs. 625-643, 2011
[23] V.Brizmer, A.Rychahivskyy, B.Han, Anti-Micropitting Performance of Black Oxide Coating, Word Tribology Congress, Turín 2013
[24] H.v.Lier, C.Hentschke, Untersuchungen zum Betriebsverhalten brünierter Wälzlager, VDI-Bericht Nr.2202, 2013
[25] J.Luyckx, Hammering Wear Impact Fatigue Hypothesis WEC/irWEA failure mode on roller bearings, NREL workshop, Broomfield noviembre 2011
[26] Comunicación interna de SKF a fabricantes líderes de la industria eólica