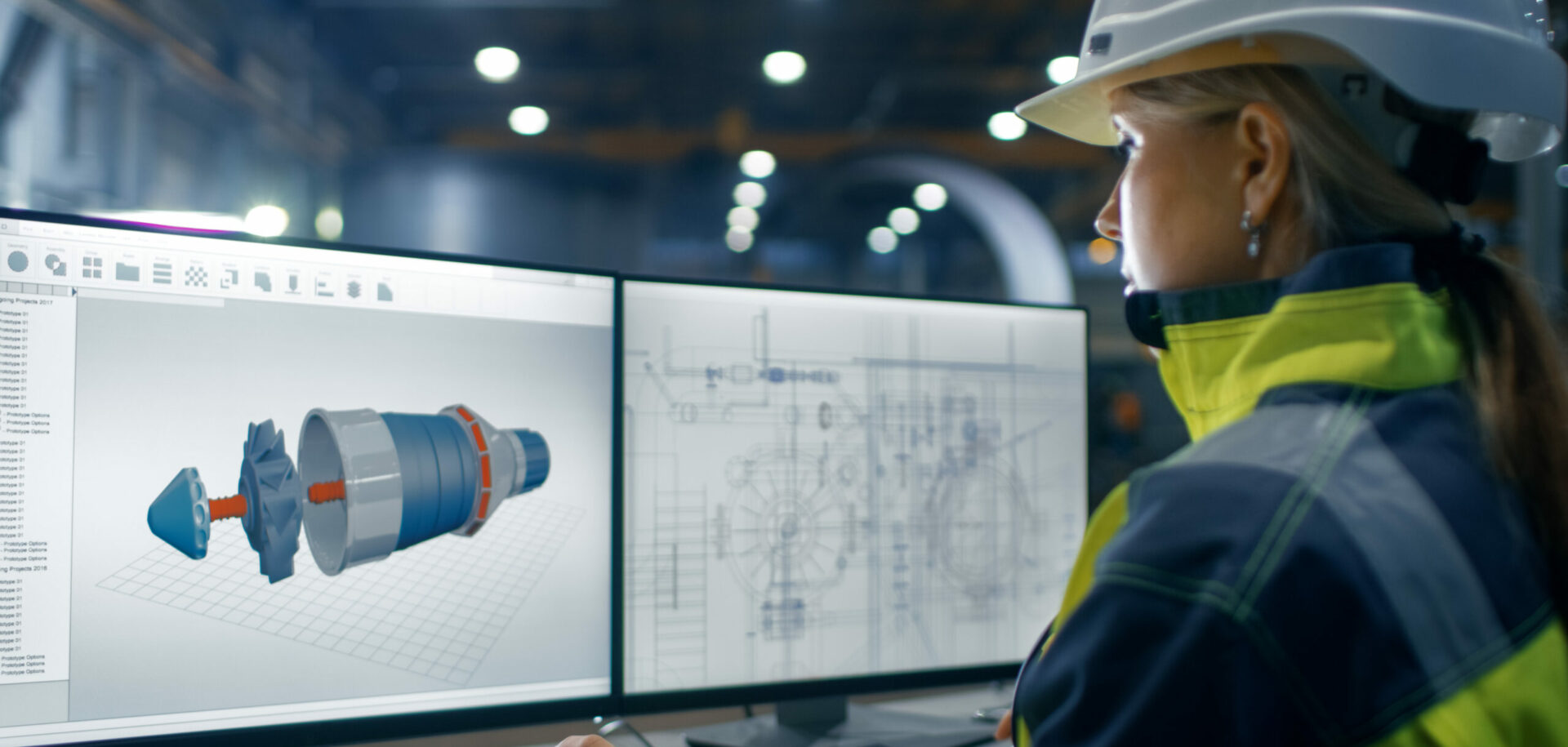
Vantaggi della black oxidation nei cuscinetti per le applicazioni eoliche
Le turbine eoliche, sempre più grandi per generare maggiori potenze, diventano più esigenti nei confronti degli organi di trasmissione.
Sintesi
Per soddisfare le rigorose esigenze dell’industria delle turbine eoliche, la SKF impiega uno specifico trattamento denominato “black oxidation”, che conferisce ai componenti dei cuscinetti uno strato protettivo, che resiste agli agenti chimici e alla corrosione e contribuisce a prevenire i guasti dei cuscinetti durante la fase critica del rodaggio.
In funzionamento le turbine eoliche sono soggette ad ampie variazioni di temperatura, carico e velocità del vento [1]. Tali condizioni di lavoro, a cui vanno aggiunte influenze potenzialmente pericolose, dovute a contaminazione da particelle solide e attacchi tribologico-chimici dovuti all’olio e alla contaminazione da acqua, possono danneggiare i cuscinetti riducendone sensibilmente la durata di esercizio (fig. 1) [2].
Per prevenire i danneggiamenti occorre migliorare le prestazioni delle superfici in modo che favoriscano il processo di rodaggio e resistano alla corrosione e ai lubrificanti aggressivi. Grazie alla lunga esperienza nel settore eolico, la SKF ha identificato nella black oxidation una delle diverse soluzioni per migliorare l’affidabilità operativa.
Il processo della black oxidation
La black oxidation è un rivestimento superficiale che si forma per effetto della reazione chimica sullo strato superficiale dell’acciaio e si ottiene immergendo il componente di un cuscinetto in una soluzione alcalina ad una temperatura tra i 130 e i 150 °C circa. La reazione tra il ferro della lega ferrosa e i reagenti produce sulla superficie esterna del componente uno strato di ossido, costituito da una miscela ben definita di FeO, Fe2O3 e di Fe3O4 risultante. Quello che si ottiene è uno strato di colore nero scuro dello spessore di circa 1–2 μm. Il processo prevede circa 15 immersioni, in molte delle quali è possibile variare il tenore delle sostanze chimiche, la loro concentrazione, la temperatura, i tempi di immersione e il movimento del fluido nel bagno [3].
Benefici della black oxidation
Di seguito elenchiamo solo i benefici del trattamento più importanti per l’industria eolica. Essi si possono suddividere in tre categorie, dimostrando la capacità della black oxidation di ridurre i rischi delle diverse tipologie di danneggiamento.
1. Riduzione del rischio di guasti prematuri
In alcune turbine eoliche, i cuscinetti dei rotismi possono guastarsi prematuramente a causa di cricche, sfaldature o white etching crack (WEC) irregolari. Con WEC intendiamo l’aspetto che assume la microstruttura alterata dell’acciaio quando ci sono strisciamenti ed è sottoposta ad attacco acido una micro-sezione del componente. I danneggiamenti si possono incontrare in molte posizioni di cuscinetti, in particolare in quelle dei satelliti, dell’albero intermedio e dell’albero veloce.
La presenza dei danneggiamenti evidenziati dalle WEC è oggetto di ampie discussioni nell’industria eolica ed è studiata indipendentemente sia dai costruttori delle turbine e da quelli dei moltiplicatori sia dai fornitori di cuscinetti, oltre che dalle università e da vari istituti di ricerca. Molte delle ipotesi si concentrano su fenomeni superficiali, quali la penetrazione di idrogeno e l’interazione con le inclusioni sotto-superficiali o sulla propagazione delle sollecitazioni tribologico-meccaniche conseguenti al lavoro compiuto dalle superfici. Per altre informazioni sulle ipotesi in merito alle cause delle cricche WEC, vedere [4].
Secondo le attuali indagini e sulle informazioni ricavabili dalla letteratura, diversi meccanismi possono contribuire a ridurre il rischio della formazione delle WEC:
- riduzione degli attacchi di tipo tribologico e chimico [5] (“passivazione”)
- riduzione della diffusione dell’idrogeno nell’acciaio dei cuscinetti [6] (“passivazione”)
- protezione contro la corrosione [7]
- stabilizzazione della microstruttura delle piste [8].
La black oxidation può contribuire a proteggere i componenti dei cuscinetti dai meccanismi di danneggiamento sopracitati. Di seguito, descriviamo i numerosi test e le indagini di laboratorio che rivelano i vantaggi del trattamento.
1.1 Attacchi tribologico-chimici da parte di lubrificanti e additivi
Gli oli per ingranaggi sono studiati per ottimizzare le prestazioni. In molti casi, a scopo di ulteriore miglioramento, si aggiungono additivi anti-usura e inibitori di corrosione. Sfortunatamente la chimica degli oli per ingranaggi non sempre favorisce il funzionamento dei cuscinetti volventi. Nei contatti tra i denti degli ingranaggi gli strisciamenti macroscopici sono molto più grandi che nei cuscinetti (rapporto strisciamento-rotolamento 30 %, anziché 4 %, a seconda del tipo di cuscinetto). Quindi la dinamica di reazione degli strati (formazione e asportazione) negli ingranaggi è diversa da quella nei cuscinetti.
Quando i cuscinetti operano in condizioni di lubrificazione marginale (limite e mista), si verificano reazioni tra le superfici in acciaio dei contatti volventi e gli additivi dell’olio per ingranaggi. L’energia chimica che si sviluppa durante la formazione di uno strato di reazione, unita all’energia di tipo tribologico, probabilmente modifica la microstruttura dell’acciaio prossima alla superficie [9]. Il cambiamento di microstruttura porta a modificare le proprietà meccaniche della superficie e di conseguenza il comportamento tribologico (attrito, usura e affaticamento superficiale). Se le reazioni sono sfavorevoli, si verifica un significativo cambiamento della struttura prossima alla superficie, seguita dall’innesco di microcricche in superficie.
Sottoponendo a test oli per ingranaggi, Pasaribu e Lugt [10] hanno dimostrato che esiste una correlazione positiva tra lo spessore di ossido e le prestazioni dei cuscinetti. Questo indica che la passivazione delle superfici dei cuscinetti ritarda le reazioni sfavorevoli tra gli oli e le superfici stesse. Quindi il predisporre strati di ossido, come il black oxide, di ~1–2 μm riduce il rischio di tali reazioni sfavorevoli.
Il vantaggio della black oxidation nel prevenire la formazione di cricche superficiali può essere verificato sottoponendo le superfici ossidate a test in condizione di lubrificazione limite. Un esempio di test è quello della sfera asimmetrica lubrificata su disco. Sfera e disco sono azionati in modo indipendente, per permettere il controllo del rapporto strisciamento-rotolamento, che è importante per il funzionamento dei cuscinetti. La fig. 2 mostra i risultati di test con olio contenente additivi aggressivi anti-usura. Le superfici in acciaio non trattate con black oxidation presentano microcricche superficiali, mentre quelle trattate non ne evidenziano.
1.2 Fragilità da idrogeno
Il trattamento di “passivazione” delle superfici dell’acciaio da cuscinetti con la black oxidation può ridurre efficacemente la penetrazione dell’idrogeno atomico e l’attacco chimico. Questa proprietà è stata verificata in laboratorio con i C-ring test e i test di permeazione di idrogeno [11].
Per valutare le cricche da idrogeno (Hydrogen-Induced Stress Corrosion Cracking, HISCC) nei contatti lubrificati, è stato realizzato uno speciale banco per il C-ring test [12]. La fig. 3 mostra l’anello interno di un cuscinetto a rulli cilindrici a cui è stato asportato un settore. L’anello è caricato da una vite per creare sulla superficie una sollecitazione di trazione predefinita. Le cricche con inizio superficiale sotto la sollecitazione di trazione sono favorite dall’assorbimento di idrogeno dal media di lubrificazione. Il tempo che intercorre prima che l’anello si rompa per effetto del carico (C-ring life) riflette la resistenza alle HISCC. Il grafico della fig. 3 mostra come gli anelli trattati con la black oxidation durino di più di quelli non trattati.
La resistenza della black oxidation all’assorbimento di idrogeno può anche essere valutata con un test di permeazione di idrogeno, in cui l’idrogeno atomico viene generato da cariche elettrochimiche. L’idrogeno che permea attraverso la piastra d’acciaio viene misurato dall’ossidazione elettrochimica che si libera dall’altra parte della piastra. L’idrogeno che passa attraverso un rivestimento superficiale può essere valutato confrontandone il flusso (la corrente) con quello che si ha con una superficie non rivestita. La fig. 4 mostra come le piastre trattate presentino un flusso di idrogeno notevolmente inferiore. Questo perché, contrariamente a quanto succede in un materiale massiccio, l’idrogeno atomico deve essere ionizzato per poter passare attraverso uno strato di ossido. La forte interazione tra gli atomi d’idrogeno ionizzato (come protone) e gli anioni dell’ossido di ferro crea uno strato ossidato che agisce da barriera in grado di rallentare la penetrazione dell’idrogeno [13].
1.3 Corrosione da umidità (corrosione da fermo)
Forti variazioni di temperatura favoriscono la condensazione dell’acqua presente nell’aria umida. Sebbene il rischio di contaminazione da acqua non sia citato molto spesso nelle applicazioni eoliche, è ben noto che l’acqua disciolta può ridurre la funzionalità degli additivi anti-usura [14] e che l’acqua libera favorisce la corrosione e l’assorbimento dell’idrogeno [15] [16]. Il rischio di corrosione è maggiore quando la turbina è ferma per manutenzione o per assenza di vento [7].
La microstruttura del black oxide presenta una certa porosità, che può aumentare l’interazione del lubrificante o delle sostanze protettive sullo strato di rivestimento e migliorare la resistenza all’umidità o alla corrosione da fermo. In una prova a nebbia salina [17], i campioni trattati hanno presentato una resistenza alla corrosione notevolmente superiore a quella offerta dai campioni non trattati (fig. 5).
2. Condizioni operative gravose con insufficiente lubrificazione o danneggiamento superficiale
2.1 Usura adesiva; smearing o danneggiamento da strisciamento
Quando i cuscinetti a rulli sono troppo poco caricati (al di sotto del carico minimo richiesto), può verificarsi una notevole differenza tra le velocità di rotazione dell’anello interno e del gruppo rulli, cosa che genera forti strisciamenti tra i corpi volventi e l’anello interno stesso [18]. Nelle applicazioni gravose come quelle degli alberi veloci dei moltiplicatori eolici, la presenza di rulli fermi e la variazione di posizione della zona sotto carico possono talvolta provocare forti strisciamenti, con conseguente rischio di usura adesiva [19] [20].
Test sui moltiplicatori eolici con funzionamento in idling hanno dimostrato che la black oxidation offre la migliore efficacia protettiva contro i fenomeni di smearing sui cuscinetti dell’albero veloce. La fig. 6 mostra il danneggiamento da smearing che compare sulle superfici non trattate dei rulli e dell’anello interno dopo 45 minuti di funzionamento in idling; sugli anelli trattati non compare alcun danneggiamento significativo dopo 30 ore.
Il meccanismo di protezione delle superfici trattate con black oxidation può essere spiegato sia da un minor attrito che si ha dopo il rodaggio sia dalla migliore adesione del lubrificante alle superfici.
2.2 Affaticamento superficiale
L’affaticamento superficiale (surface distress) è un fenomeno che inizia in superficie a livello delle asperità ed è associato a scarse condizioni di lubrificazione, a cui corrispondono elevati sforzi di trazione (per attrito) [21]. Esso si verifica specialmente sui denti degli ingranaggi, ma talvolta anche sui cuscinetti, sui quali può essere particolarmente dannoso.
Pur non essendo il principale modo di guastarsi dei cuscinetti volventi, l’affaticamento superficiale può facilitare o accelerare la comparsa di altri tipi di danneggiamento, quali impronte da detriti, erosioni con inizio superficiale e grippaggi [22]. Il rischio di affaticamento superficiale si può ridurre in vari modi, per esempio diminuendo l’attrito, redistribuendo le sollecitazioni prossime alla superficie in modo più favorevole o riducendo le pressioni causate dalla lubrificazione mista oppure ottimizzando il rodaggio. Per realizzare tale scenario si può ricorrere a rivestimenti protettivi, come la black oxidation.
Nonostante la grande quantità di lavori teorici e sperimentali sull’affaticamento superficiale in generale (ved. ad esempio [21]), finora l’influenza dei trattamenti non era stata ancora sufficientemente studiata. Si è quindi condotta una serie di esperimenti di laboratorio con rulli trattati [23] su un banco prova dell’affaticamento superficiale [14] [21], che consente il controllo del rapporto strisciamento-rotolamento, delle condizioni di lubrificazione, della temperatura, del carico e della velocità. Il banco è illustrato schematicamente in fig. 7 (in alto): un rullo rotante è in contatto con tre dischi: il primo è costituito da un rullo di 12 mm di diametro di un cuscinetto orientabile a rulli, mentre i secondi sono anelli interni di cuscinetti a rulli cilindrici. Rullo e anelli possono essere rettificati e/o lucidati per ottenere la rugosità desiderata. Il materiale di rullo e anelli è acciaio ANSI-52100 temprato per cuscinetti. Le condizioni di lubrificazione vengono variate da una lubrificazione limite a una mista. Dopo la prova si controlla la presenza di affaticamento superficiale sui rulli testati, mettendo a confronto quelli non trattati e quelli trattati con black oxidation, a parità di condizioni.
Il risultati degli esperimenti rivelano una buona efficacia contro l’affaticamento superficiale da parte della black oxidation nell’intera gamma delle condizioni di prova [23], come illustrato in fig. 7.
Inoltre, per le superfici trattate è stata eseguita un’analisi parametrica del modello dell’affaticamento superficiale [22] [23], includendo gli effetti dell’attrito e di rigidezza e spessore del rivestimento. Si è riscontrata l’esistenza di uno spessore di rivestimento ottimale in corrispondenza dell’affaticamento superficiale minimo. Come riscontrato nei risultati sia sperimentali sia teorici, la black oxidation amplia il numero di condizioni operative che non presentano affaticamento superficiale.
3. Test sui cuscinetti ed esperienze sul campo
È stata eseguita una prova di durata su cuscinetti operanti in condizioni gravose di lubrificazione mista. Essa ha confermato i positivi effetti della black oxidation rispetto all’assenza di trattamento, in presenza di rodaggio [24] e con valori bassi di kappa.
In questo caso tutti i test sui cuscinetti trattati sono stati interotti. Infatti i risultati puntano ad una stima della durata L10 che è 2–3 volte al di sopra di quella elativa ai cuscinetti non trattati.
Oltre ai risultati dei test di laboratorio, anche l’esperienza sul campo conferma i benefici ottenibili con la black oxidation nel ridurre il rischio di guasti prematuri. Informative da parte di costruttori di moltiplicatori e di turbine confermano i notevoli miglioramenti che si ottengono adottando la black oxidation sui cuscinetti [25] [26].
Si è inoltre osservato in [8] e [25] che un leggero riscaldamento al di sotto della temperatura di rinvenimento può contribuire a ottimizzare e rafforzare la microstruttura senza che ci siano diminuzioni di durezza, estendendo quindi la durata a fatica dei cuscinetti. Da questa esperienza si deduce che l’esecuzione della black oxidation ad una temperatura analoga può contribuire a produrre effetti benefici sulla microstruttura della superficie esterna dell’acciaio, cosa che si riflette con una riduzione superiore a 0,1 gradi del valore FWHM (Full Width Half Maximum value) o b/B dei picchi XRD.
Conclusioni
I molti benefici della black oxidation sono stati dimostrati confrontando indagini di laboratorio, test sui cuscinetti ed esperienze pratiche. Il trattamento offre una protezione contro gli attacchi tribologico-chimici, riduce la penetrazione dell’idrogeno e aumenta la resistenza contro i danni da umidità (quali la corrosione da fermo). Inoltre le superfici rivestite dell’acciaio per cuscinetti estendono il margine di sicurezza, se si considerano i problemi provocati dovuti dall’usura adesiva, dallo smearing o dall’affaticamento superficiale. Le esperienze positive sul campo confermano quanto sopra.
In sintesi il processo di black oxidation utilizzato dalla SKF offre una migliore protezione contro i danneggiamenti dei componenti dei cuscinetti. Con questo trattamento i cuscinetti, oltre che sul macchinario originale, possono essere impiegati come ricambio dei tipi tradizionali negli interventi di manutenzione delle centrali eoliche. Questo significa che i vantaggi della black oxidation possono essere applicati su tutti gli organi di trasmissione importanti delle turbine dell’industria eolica. Per ottenere il massimo dei vantaggi, la SKF consiglia di trattare con la black oxidation sia gli anelli interni ed esterni sia i corpi volventi.
Bibliografia
[1] J.Rosinski, D.Smurthwaite, Troubleshooting wind gearbox problems, Gearsolutions 2010
[2] K.Stadler, Riduzione costi nelle turbine eoliche grazie alla black oxidation, Evolution #4 2013
[3] DIN 50938, Black oxide treatment of ferrous material
[4] K.Stadler, A.Stubenrauch, Guasti prematuri nei riduttori industriali, Antriebstechnisches Kolloquium Aachen, ATK 2013 ed Evolution #2 2013
[5] W.Holweger, Interaction of rolling bearing fatigue life with new material phenomenons, VDI Kongress “Antriebs-stränge in Windenergieanlagen” 2012
[6] H.Uyama, The mechanism of white structure flaking in rolling bearings, NREL workshop, Broomfield November 2011
[7] I.Strandell, C.Fajiers, T.Lund, Corrosion – one root cause for premature bearing failures, 37th Leeds-Lyon Symposium on Tribology, 2010
[8] J.Gegner, L.Schlier, W.Nierlich, Evidence and analysis of thermal static strain aging in the deformed surface zone of finish-machined hardened steel, PowderDiffraction 24-2009 pp45-50
[9] M.Reichelt, T.E.Weirich, J.Meyer, T.Wolf, J.Loos, P.W.Gold, M. Fajfrowski, TEM and nanomechanical studies on tribological surface modifications formed on roller bearings under controlled lubrication conditions. J. Mater. Sci. 41, 4543-4553 (2006)
[10] H.R.Pasaribu, P.M.Lugt, The Composition of Reaction Layers on Rolling Bearings Lubricated with Gear Oils and Its Correlation with Rolling Bearing Performance, Tribology Transaction, Vol. 55, 3, 351-356, 2012
[11] ASTM G38, “Standard practice for making and using C-ring stress-corrosion test specimens” and ASTM G148, “Standard practice for evaluation of hydrogen uptake, permeation and transport in metals by an electro-chemical technique”
[12] B.Han, B.X.Zhou, R.Pasaribu, C-ring Hydrogen Induced Stress Corrosion Cracking (HISCC) – Tests in Lubricating Liquid Media, EuroCorr 2011 Proceeding
[13] R-H.Song, S-I.Pyung, R.A.Oriani, The hydrogen permeation through passivating film on iron by modulation method, Electrochemica Acta Vol 36, No. 5/6, pp. 825-831, 1991
[14] V.Brizmer, R.Pasaribu, G.E.Morales, Micropitting Performance of Oil Additives in Lubricated Rolling Contacts, Tribology Transactions, Vol. 56, 5, pp. 739-748, 2013
[15] R.J.K.Wood, Tribology and corrosion aspects of wind turbines, Wind Energy – Challenges for Materials, Mechanics and Surface Science, IoP, London 2010
[16] D.A.Jones, Principles and Prevention of Corrosion – 2nd Ed., Page 335, ISBN: 0-13-359993-0, 1996
[17] ASTM B117-09, Standard Practice for Operating Salt Spray (Fog) Apparatus
[18] M.Volkmuth, K.Stadler, R.Heemskerk, Slippage measurements in roller bearings, Antriebstechnisches Kolloquium ATK Aachen 2009
[19] R.Hambrecht, Anschmiererscheinungen in Wälzlagern bei Fettschmierung, PhD thesis, Erlangen 1999
[20] B.J.Scherb, J.Zech, A study on the smearing and slip behavior of radial cylindrical roller bearings, Schaeffler Group 2001
[21] G.E.Morales, K.Stadler, V.Brizmer, Understanding and preventing surface distress, Gear solutions 2012
[22] G.E.Morales-Espejel, V.Brizmer, Micropitting Modelling in Rolling-Sliding Contacts: Application to Rolling Bearings, Trib. Trans., 54, pp. 625-643, 2011
[23] V.Brizmer, A.Rychahivskyy, B.Han, Anti-Micropitting Performance of Black Oxide Coating, Word Tribology Congress, Turin 2013
[24] H.v.Lier, C.Hentschke, Untersuchungen zum Betriebsverhalten brünierter Wälzlager, VDI-Bericht Nr.2202, 2013
[25] J.Luyckx, Hammering Wear Impact Fatigue Hypothesis WEC/irWEA failure mode on roller bearings, NREL workshop, Broomfield November 2011
[26] SKF private communication to leading wind industry OEMs