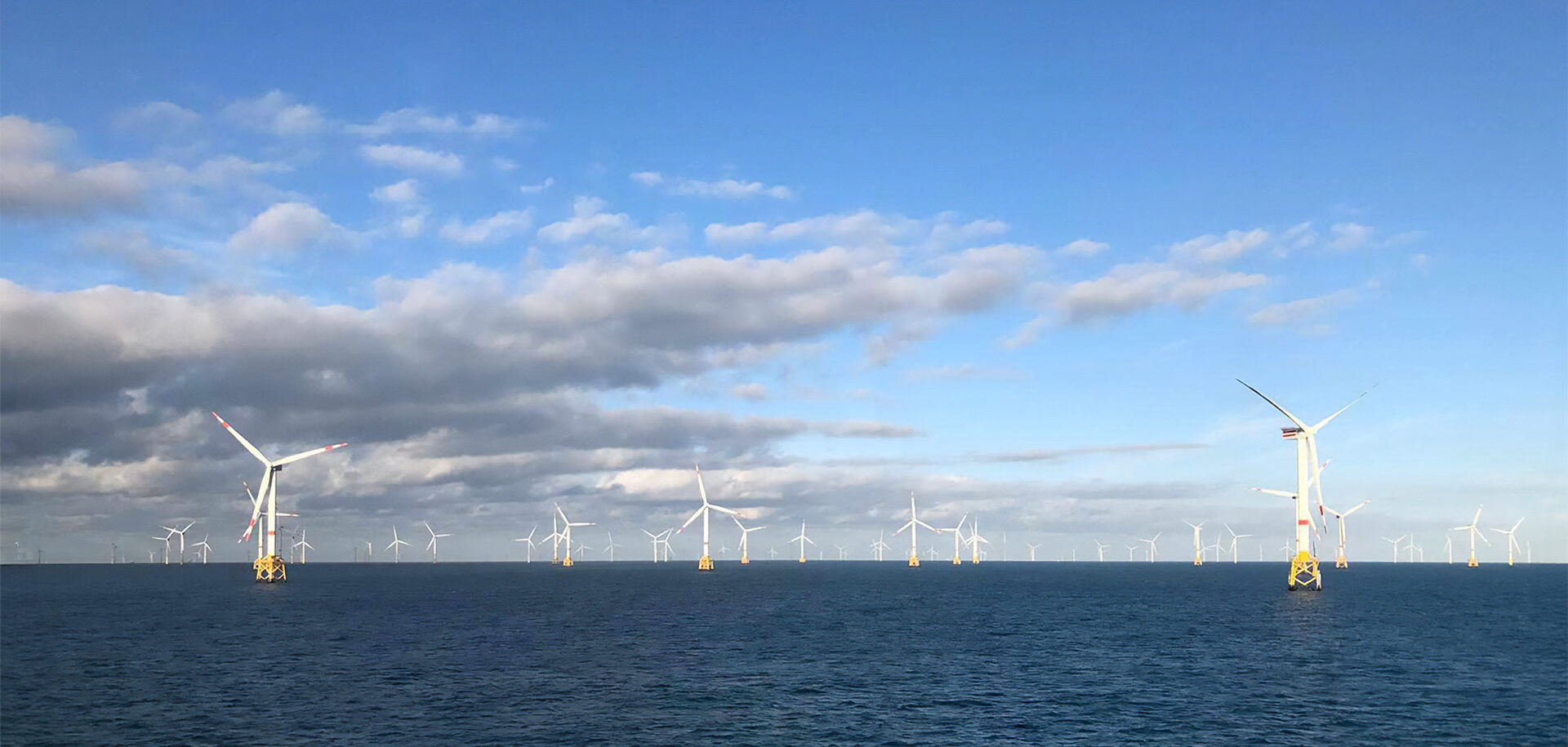
Parques eólicos añejos en plena forma gracias a la colaboración
Uno de los primeros parques eólicos marinos de Europa ha llegado a la mitad de su vida útil. Soluciones innovadoras de servicio y apoyo de SKF ayudan a mantener las turbinas en funcionamiento.
Cuando la fase inicial del parque eólico de C-Power, compuesta por seis turbinas, comenzó en 2009, se trataba del primer proyecto comercial de Bélgica para la generación de energía renovable en alta mar. Colocadas en dos cuadrículas, las turbinas están separadas por un canal para la conducción de energía eléctrica y un gasoducto. Aunque las turbinas de 5 y 6 MW del parque solo miden la mitad que las máquinas de mayor tamaño que funcionan actualmente, siguen siendo artilugios imponentes. Tres palas de 61,5 metros giran sobre un buje a una altura de unos 95 a 96 metros por encima de la superficie del mar, alzadas sobre una torre de acero de 68 metros de alto, montada, a su vez, sobre una base de 45 metros. Las primeras turbinas utilizaban enormes bases de hormigón que pesaban hasta 3000 toneladas. Hoy, la mayoría de las turbinas se asientan sobre una estructura reticulada más ligera de acero, sostenida por cuatro pilotes de dos metros de diámetro cada uno, hincados en el lecho marino.
En la punta de cada torre, una góndola de 320 toneladas aloja los rodamientos del rotor de la turbina, la caja de engranajes, el sistema de guiñada y el equipo de conversión de energía. En palabras de C-Power, sus turbinas, junto con la estación transformadora marina del parque, son como “55 fábricas a las que hay que cuidar y mantener”.
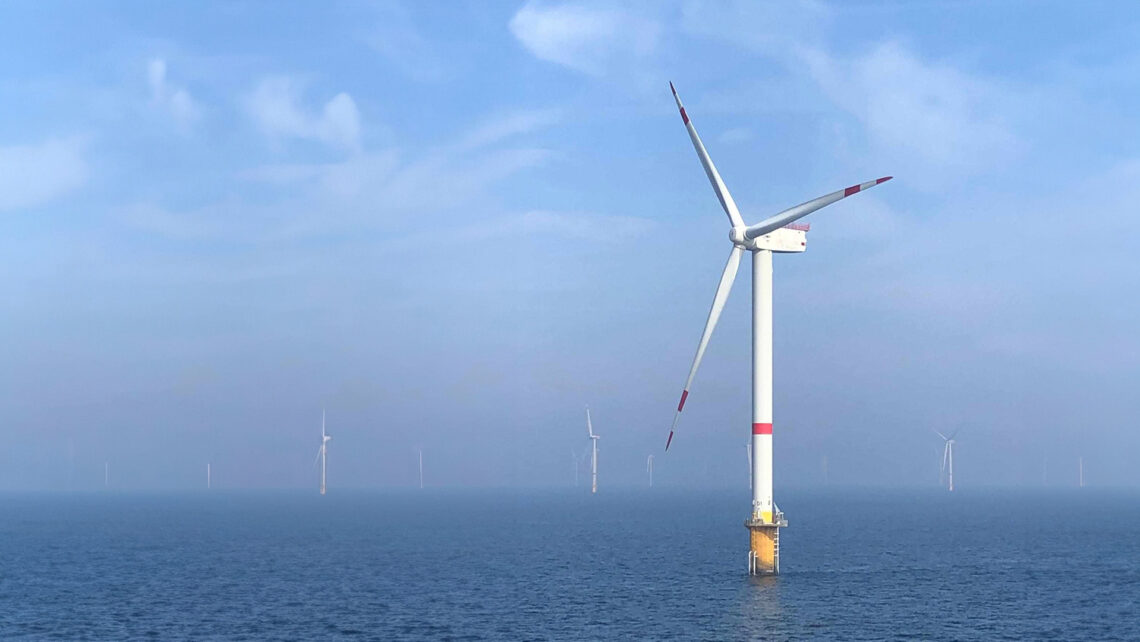
Un trabajo a tiempo completo
Las turbinas más antiguas de C-Power llevan ya 14 años funcionando en las difíciles condiciones del Mar del Norte. Es decir, han completado más de la mitad de su vida útil teórica, que es de 25 años. Y las más nuevas ya han cumplido 10 años.
Como cualquier persona que encare los desafíos de una edad avanzada, las turbinas necesitan cuidados y soporte adicionales para mantenerse en perfectas condiciones. Y, algo inusual para una instalación eólica marina, C-Power realiza todas sus operaciones y actividades de mantenimiento con personal propio.
Casi todas las mañanas del año, los equipos de mantenimiento viajan en barco desde Ostende para trabajar en las turbinas. Su régimen de mantenimiento se rige por un programa integral de tareas de mantenimiento preventivo de periodicidad anual y semestral. En promedio, cada turbina requiere 11 días de mantenimiento preventivo al año. Además, los equipos pueden tener que atender problemas imprevistos y realizar las reparaciones necesarias.
Los buques de servicio vuelven a casa cada tarde, pero C-Power sigue vigilando las instalaciones las 24 horas del día, los 7 días de la semana, desde una estación de monitoreo remoto en el puerto de Ostende. Si la meteorología no permite acceder a las turbinas por mar, cada turbina está equipada con una plataforma para helicópteros que permite el acceso para reparaciones urgentes.
Aunque C-Power se encarga de gestionar el mantenimiento por su cuenta, no lo hace sola. Desde hace años, cuenta con SKF para ayudarla a mejorar la confiabilidad de las turbinas y a desarrollar soluciones innovadoras para el sector energético marino. Equipos de ambas empresas participan en reuniones semanales para informar de los progresos de los proyectos en curso e identificar nuevas oportunidades de colaboración.
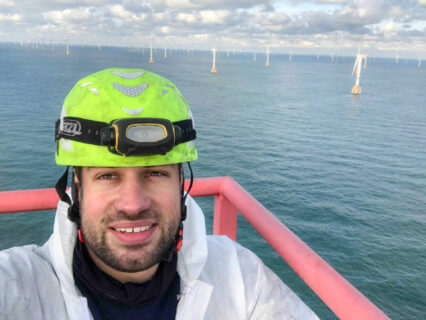
Utilizamos la tecnología de monitoreo de condición para saber qué está ocurriendo con nuestras turbinas
Bryan Uyttersprot, ingeniero de mantenimiento y de la sala de control de C-Power
Control remoto
Bryan Uyttersprot, ingeniero de mantenimiento y de la sala de control de C-Power, supervisa la sala de control del parque eólico de C-Power cada cinco semanas. El resto del tiempo, es responsable de una amplia gama de proyectos de reparación y mejora de la confiabilidad. “A veces, subo a los barcos y trabajo in situ con nuestros equipos de mantenimiento, sobre todo cuando estamos probando algo nuevo”, dice. “Pero la mayor parte de mi trabajo es de oficina, trabajando en proyectos a más largo plazo”.
Esos turnos de control son un ejemplo perfecto de la profunda relación entre SKF y C-Power. “Utilizamos la tecnología de monitoreo de condición para saber qué está ocurriendo con nuestras turbinas”, continúa Uyttersprot. “Los rodamientos de los generadores y las cajas de engranajes tienen instalados unos 14 sensores de vibración, y hay sensores adicionales en los rodamientos principales del eje del rotor”.
Los datos se recopilan desde esos sensores mediante dispositivos de monitoreo de máquinas Multilog IMX de SKF, y se transmiten a través de un enlace de datos seguro al Centro de Servicios de Diagnóstico Remoto (RDC) de SKF en Hamburgo, Alemania. En el RDC, especialistas de SKF en monitoreo de condición de energía eólica analizan los espectros de vibración, buscando los primeros indicios de problemas en componentes críticos.
“Trabajo estrechamente con los ingenieros en el RDC”, sostiene Uyttersprot. “Sus análisis pueden indicarnos si tenemos un problema, como un aro de rodamiento roto o daños en los elementos rodantes”. Basándose en los informes de SKF, Uyttersprot decidirá qué medidas son las más adecuadas para que la turbina vuelva a funcionar correctamente.
“Si tenemos un problema con un rodamiento del generador o de la caja de engranajes, sustituirlo es bastante sencillo”, afirma, “aunque tenemos que enviar un equipo especializado para terminar el trabajo”. Cada una de las góndolas de las turbinas eólicas cuenta con una grúa hidráulica que el equipo puede utilizar para mover los pesados componentes con seguridad.
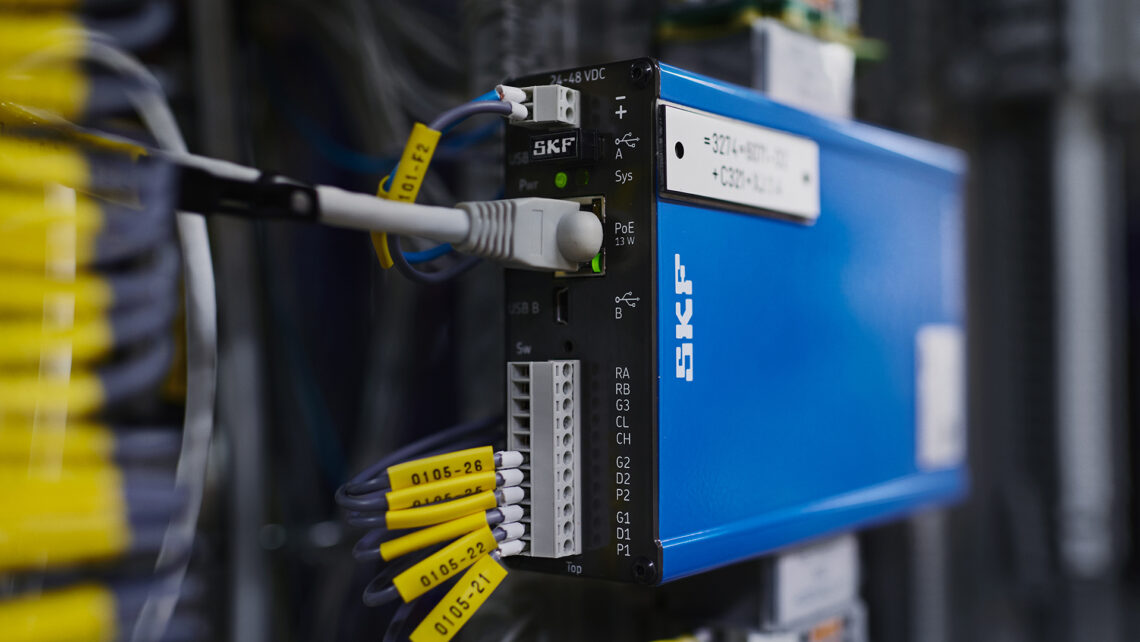
Trabajo pesado
Si surge un problema con los rodamientos principales del rotor, las reparaciones son mucho más complejas. “Obligan a sacar el eje principal entero, que pesa unas 70 toneladas”, explica Uyttersprot. “Y, para acceder a ese conjunto de componentes, tenemos que desarmar los rotores y el buje, que pesan 130 toneladas”. Estas tareas requieren máquinas altamente especializadas capaces de elevar cargas pesadas. Para ello, se utiliza un buque autoelevable equipado con una grúa pesada y patas extensibles que se clavan en el lecho marino para dar estabilidad. Los ejes de rotor gastados o dañados se trasladan a un centro de SKF para su reparación y revisión.
Conscientes del elevado costo y la gran complejidad de estas reparaciones, los operadores de parques eólicos quieren asegurar la confiabilidad de estos componentes. Tanto SKF como C-Power trabajan en el tema de la confiabilidad desde hace tiempo. “A lo largo de los años, hemos hecho muchos cambios”, afirma Uyttersprot. “Hemos cambiado la grasa que utilizamos en estos rodamientos para mejorar el rendimiento de la lubricación. Y, con el tiempo, hemos incorporado nuevas prestaciones a los rodamientos para alargar su vida útil”.
En algunas turbinas, SKF y C-Power están a mitad de camino de un ensayo plurianual de una innovadora tecnología de monitoreo de condición. “Hemos dotado algunas de nuestras turbinas de rodamientos principales que llevan sensores en el interior de los elementos rodantes”, explica Uyttersprot. “Eso nos permite medir las cargas internas de los rodamientos y ver cómo varían esas cargas en diferentes condiciones de funcionamiento y en diferentes puntos de su circunferencia”. Todavía se están recopilando datos de los rodamientos equipados con sensores, pero Uyttersprot confía en que permitan descubrir nuevos caminos para mejorar la confiabilidad de estos componentes críticos.
Mientras tanto, otras innovaciones de SKF ya están facilitando el trabajo diario de los equipos de mantenimiento de C-Power. Un ejemplo es un novedoso diseño de sello partido para los rodamientos principales del rotor. Desarrollado originalmente para la empresa belga pionera en energías renovables, el nuevo diseño no solo aporta más robustez al componente, sino también acorta los tiempos de ensamblaje.
Producción potente
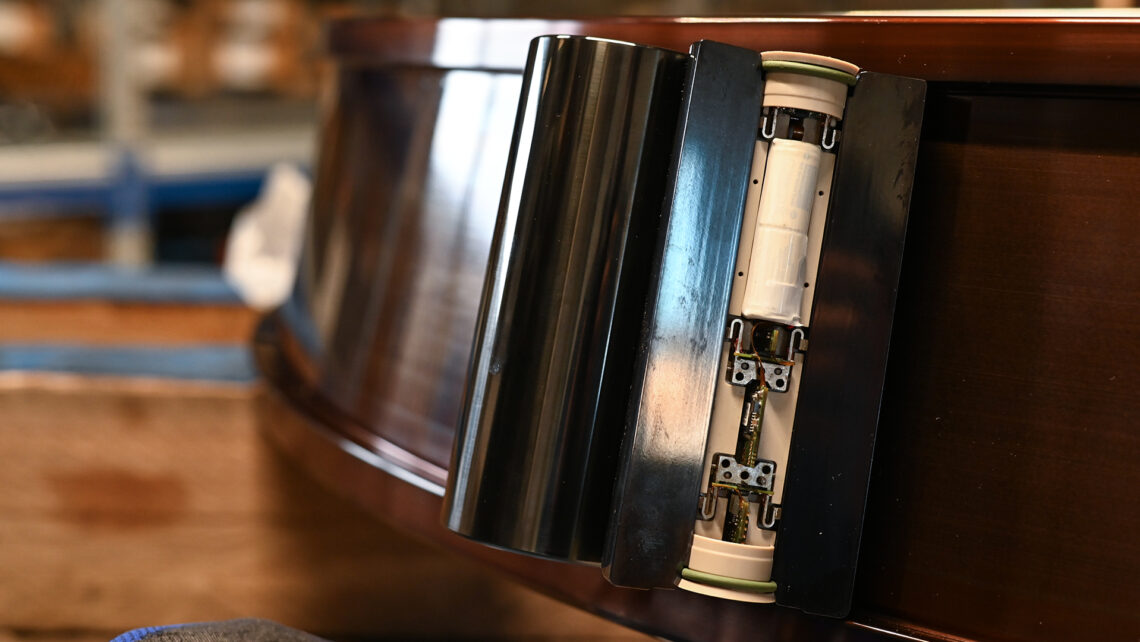